Waterjet Technology Joins Digital Desktop Revolution
Waterjet Technology Joins Digital Desktop Revolution
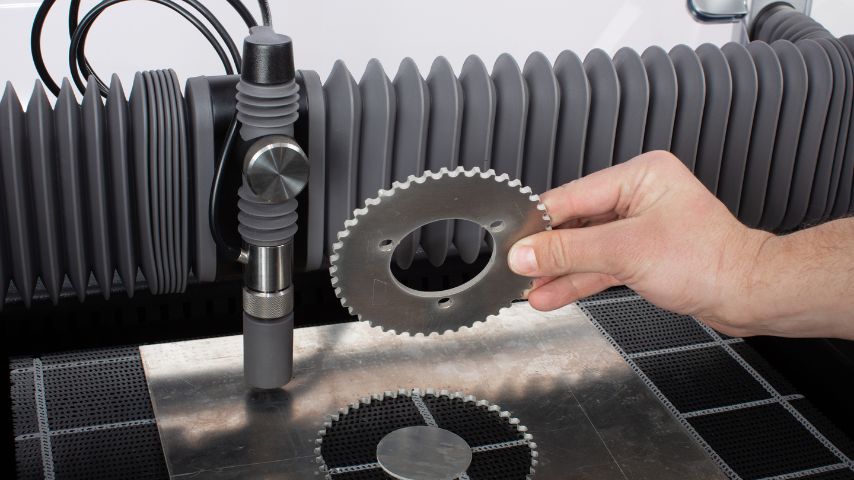
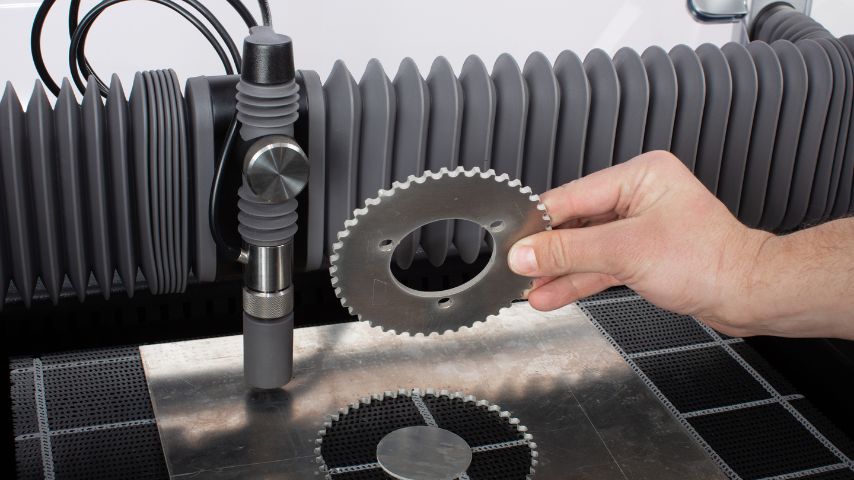
Wazer has taken an old technology—the waterjet—and elevated it to a cutting-edge desktop tool. Part of a mini digital revolution, these devices provide greater accessibility and innovation.
Waterjet technology has been around for decades. Most understand the tool used for the micro eroding of material as big, bulky, and extremely expensive. So the thought of a division of even a large organization being able to use the technology for visual inspection, quality control, and failure analysis was unheard of until today.
For Nisan Lerea, CEO of Wazer in Yonkers, N.Y., the technology is sound—allowing visual inspection without adding heat, corrosives, or other additives that may change the status of the piece or material being inspected. What needed to be introduced to this system was a way to bring it to the desktop as part of a digital toolbox, which allows engineers to improve products quickly and inexpensively.
Lerea, who started Wazer with three other mechanical engineers with Kickstarter funding, certainly sees a trend that Wazer can be a big part of—the digital desktop design movement. And accessible and affordable tools are part of an even larger trend—the “democratization of manufacturing,” he explained.
“Desktop digital processes are fueling innovation,” Lerea said. “When more people have more capabilities to make and improve, there's more that’s going to be made and improved. And the results are going to be innovative and not as expected,” he said.
The Wazer product—a desktop waterjet cutter priced at under $10,000—is the result of a senior project. While at the University of Pennsylvania, Lerea was crafting prototypes and didn't have an effective way to cut sheet metal. ”Our university machine shop didn't have a waterjet, so that was the original impetus to build this product,” he explained.
Become a Member: How to Join ASME
Founded in 2016, Wazer shipped its first unit two years later. Since that time, the startup has manufactured over 3,000 desktop water jet cutters for customers in over 60 countries. The flexible tool is used in a variety of industries for many applications, but one surprised even the Wazer team—quality control inspection and failure analysis.
“What makes waterjets unique for this application is the nature of the cutting process: it's a process, whereby individual, tiny particles of abrasive erode the target material away, chunk by chunk,” Lerea explained.
The benefit, he said, is that this specific way to remove material has the ability to get the job done without causing more damage to the target material being cut. “We are talking no heat, no stress, and no shearing,” Lerea explained. “These are all big issues that other cutting methods have. When you use blades, saws, or even lasers, you don't know if your inspection process is actually introducing new failures into your sample that weren't present beforehand.”
The size and price of the Wazer waterjet cutter are what make it possible to use this method for part inspections. Prior to the desktop version, a manufacturer may actually have one on the factory floor, but R&D and other departments would have to schedule time for their work and share the tool, or send the part out to a vendor.
More for You: Quiz: Water Under Pressure
Wazer customers often have robust R&D departments that require extensive onsite testing of components and products and failure testing for multiple product lines. “We are talking about companies that are working with processor units in everything from autonomous vehicles to gaming consoles,” Lerea explained.
Such work also includes derisking designs to find failure points before production begins and inspecting raw materials and components. “We learned the tool was being used to cut components in half to be able to inspect a cross section,” he said. “The standard industry process previously was a wet saw and chemicals, which generate heat and have accuracy issues.”
Lerea offered an example of such work with Trivium Packaging, which makes metal containers such as aluminum cans. “Sounds simple, right?” he said. But during every shift, an employee takes samples off the line and cuts them so that a cross-section can be inspected. ”The aluminum is super thin, and before the Wazer, the inspection process meant taking each sample, embedding it in epoxy, waiting for it to cure, and then using a band saw to cut it,” Lerea explained. “It was extremely tedious and an unusually manual process in what is otherwise a highly automated manufacturing operation.”
Failure analysis is another scenario where a quality team might cut through an entire component piece. For example, Nvidia's thermal engineering team cut an RTX 4090 Founders Edition cooler in half with a water jet. Malcolm Gutenburg from Nvidia explained on a popular YouTube video that the water jet allowed them to cut the card used for gaming, content creation, and production without damage. “This is the cleanest cross section of anything I have ever seen,” said the host of Gamers Nexus, Steve Burke, to Gutenburg while holding the component and exposing a spotless cross section of the vapor chamber, heat pipes, and evaporator.
Lerea explained that he has, for all intents and purposes, “reinvented the band saw.” The cutter is a practical “foundational tool” and one that becomes more useful as a desktop offering. He said that the movement makes tools, not only the waterjet cutter, more accessible since they are smaller, easier to use, and more affordable. “Our product is part of the trend in desktop digital manufacturing,” Lerea said, to be used next to desktop 3D printers, for example. The biggest challenge was bringing this precision product with hundreds of components to market and making it smaller and more affordable.
Lerea explained that the larger trend is the “manufacturing democratization.” Desktop digital tools are fueling innovation in large commercial enterprises, small startups, universities, and high schools, and even coops where people share resources. “When more people have more capabilities to make stuff, there's more things that are going to be made, and they're going to be innovative and different,” he said.
“Now every engineer, whether they are working in an R&D department of Boeing, a university lab, or a small startup, has access to tools and doesn't have to wait days, weeks, or months before they make interactions,” Lerea added.
Cathy Cecere is membership content program manager.
For Nisan Lerea, CEO of Wazer in Yonkers, N.Y., the technology is sound—allowing visual inspection without adding heat, corrosives, or other additives that may change the status of the piece or material being inspected. What needed to be introduced to this system was a way to bring it to the desktop as part of a digital toolbox, which allows engineers to improve products quickly and inexpensively.
Digital offering
Lerea, who started Wazer with three other mechanical engineers with Kickstarter funding, certainly sees a trend that Wazer can be a big part of—the digital desktop design movement. And accessible and affordable tools are part of an even larger trend—the “democratization of manufacturing,” he explained.
“Desktop digital processes are fueling innovation,” Lerea said. “When more people have more capabilities to make and improve, there's more that’s going to be made and improved. And the results are going to be innovative and not as expected,” he said.
The Wazer product—a desktop waterjet cutter priced at under $10,000—is the result of a senior project. While at the University of Pennsylvania, Lerea was crafting prototypes and didn't have an effective way to cut sheet metal. ”Our university machine shop didn't have a waterjet, so that was the original impetus to build this product,” he explained.
Become a Member: How to Join ASME
Founded in 2016, Wazer shipped its first unit two years later. Since that time, the startup has manufactured over 3,000 desktop water jet cutters for customers in over 60 countries. The flexible tool is used in a variety of industries for many applications, but one surprised even the Wazer team—quality control inspection and failure analysis.
“What makes waterjets unique for this application is the nature of the cutting process: it's a process, whereby individual, tiny particles of abrasive erode the target material away, chunk by chunk,” Lerea explained.
The benefit, he said, is that this specific way to remove material has the ability to get the job done without causing more damage to the target material being cut. “We are talking no heat, no stress, and no shearing,” Lerea explained. “These are all big issues that other cutting methods have. When you use blades, saws, or even lasers, you don't know if your inspection process is actually introducing new failures into your sample that weren't present beforehand.”
The size and price of the Wazer waterjet cutter are what make it possible to use this method for part inspections. Prior to the desktop version, a manufacturer may actually have one on the factory floor, but R&D and other departments would have to schedule time for their work and share the tool, or send the part out to a vendor.
More for You: Quiz: Water Under Pressure
Wazer customers often have robust R&D departments that require extensive onsite testing of components and products and failure testing for multiple product lines. “We are talking about companies that are working with processor units in everything from autonomous vehicles to gaming consoles,” Lerea explained.
Such work also includes derisking designs to find failure points before production begins and inspecting raw materials and components. “We learned the tool was being used to cut components in half to be able to inspect a cross section,” he said. “The standard industry process previously was a wet saw and chemicals, which generate heat and have accuracy issues.”
Lerea offered an example of such work with Trivium Packaging, which makes metal containers such as aluminum cans. “Sounds simple, right?” he said. But during every shift, an employee takes samples off the line and cuts them so that a cross-section can be inspected. ”The aluminum is super thin, and before the Wazer, the inspection process meant taking each sample, embedding it in epoxy, waiting for it to cure, and then using a band saw to cut it,” Lerea explained. “It was extremely tedious and an unusually manual process in what is otherwise a highly automated manufacturing operation.”
Failure analysis is another scenario where a quality team might cut through an entire component piece. For example, Nvidia's thermal engineering team cut an RTX 4090 Founders Edition cooler in half with a water jet. Malcolm Gutenburg from Nvidia explained on a popular YouTube video that the water jet allowed them to cut the card used for gaming, content creation, and production without damage. “This is the cleanest cross section of anything I have ever seen,” said the host of Gamers Nexus, Steve Burke, to Gutenburg while holding the component and exposing a spotless cross section of the vapor chamber, heat pipes, and evaporator.
A revolution
Lerea explained that he has, for all intents and purposes, “reinvented the band saw.” The cutter is a practical “foundational tool” and one that becomes more useful as a desktop offering. He said that the movement makes tools, not only the waterjet cutter, more accessible since they are smaller, easier to use, and more affordable. “Our product is part of the trend in desktop digital manufacturing,” Lerea said, to be used next to desktop 3D printers, for example. The biggest challenge was bringing this precision product with hundreds of components to market and making it smaller and more affordable.
Lerea explained that the larger trend is the “manufacturing democratization.” Desktop digital tools are fueling innovation in large commercial enterprises, small startups, universities, and high schools, and even coops where people share resources. “When more people have more capabilities to make stuff, there's more things that are going to be made, and they're going to be innovative and different,” he said.
“Now every engineer, whether they are working in an R&D department of Boeing, a university lab, or a small startup, has access to tools and doesn't have to wait days, weeks, or months before they make interactions,” Lerea added.
Cathy Cecere is membership content program manager.