3D Printing Meets High Performance in Czinger Hypercars
3D Printing Meets High Performance in Czinger Hypercars
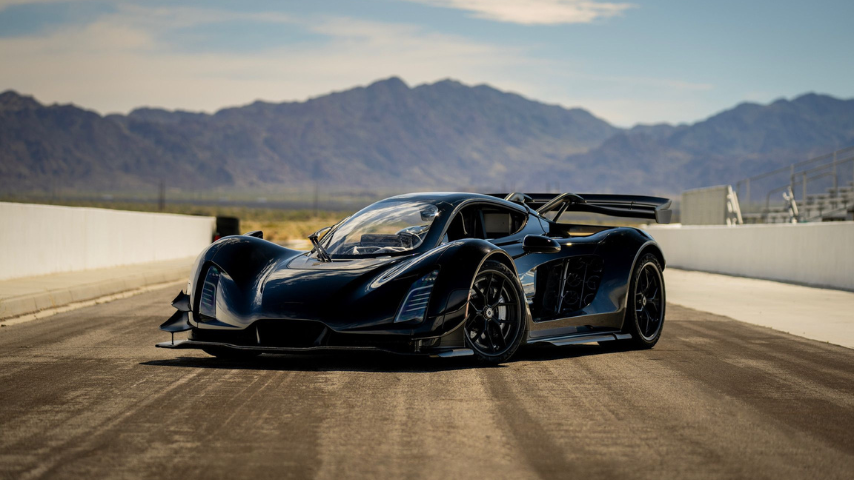
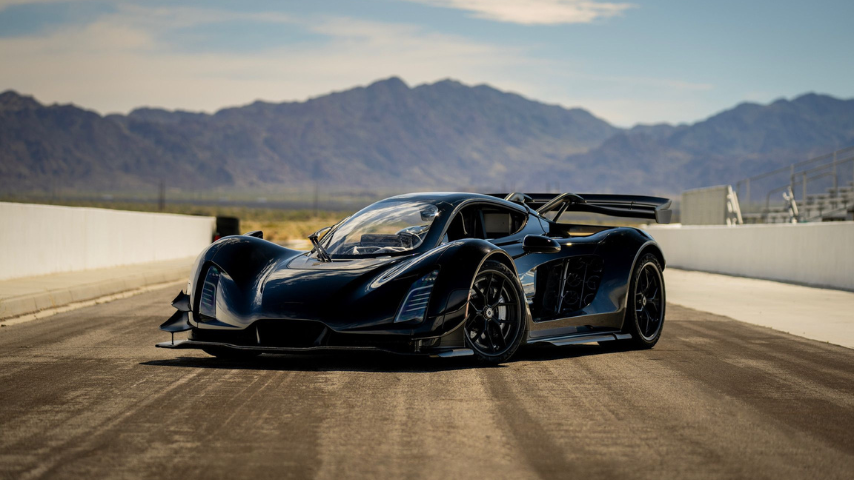
Inspired by the SR‑71 Blackbird reconnaissance aircraft, the Czinger 21C Blackbird Edition shares the vision of Kelly Johnson and the Skunk Works team for record‑breaking speed.
What do you get when combining additive manufacturing with a relentless need for speed? A hypercar engineered with precision, utilizing rapid prototyping and 3D printing to create a lightweight yet incredibly strong structure.
One of the fastest cars in the world, the Czinger 21C pushes the boundaries of performance, featuring a hybrid powertrain that blends a twin-turbo V8 with an electric motor. The fusion of cutting-edge technology and engineering excellence makes the 21C not just a hypercar, but a contemporary engineering marvel.
While Czinger has become known for their additive manufacturing, the initial goal was to go beyond the constraints of traditional tooling, according to Chief Engineer at Czinger, Ewan Baldry.
“Our parent company, Divergent, is the technology company,” Baldry explained. “It's been in existence for eight to 10 years now, and originally set out on the mission of developing this toolless manufacturing methodology for primary vehicle structures.”
Kevin Czinger, Founder and Executive Chairman of both companies, started Divergent Technologies after recognizing the limitations of traditional automotive production. He went on to establish Czinger Vehicles in 2019 with his son Lukas Czinger, Founder, President, and CEO of the Los Angeles based family businesses.
Baldry emphasized the advantage of being completely design-agnostic when it comes to manufacturing. “We print quite large structures that we assemble in a robot cell that has no tooling. And the beauty of all of that is you end up with a completely design-agnostic manufacturing facility that can make one thing one day, something else the next, without any kind of breakdown of the infrastructure,” he said.
Czinger bypasses some of the conventional manufacturing constraints, such as draft angle requirements, minimum wall thickness, and tool access requirements in casting or machining. One of the key advantages of this approach is topology optimization, a computational design process that determines the ideal distribution of material within a component based on real-world stress and load conditions.
“When you're printing things, you have significantly more freedom in the geometries that you design,” Baldry shared. “And that's enabled us actually to really embrace and develop and push the process of topology optimization.” Baldry added that a serious limitation in the past was certain geometries wouldn't have been manufacturable through conventional methods and practices. But without the constraints of traditional manufacturing, Czinger engineers can explore novel geometries and lightweight structures.
The process can result in organic, skeleton-like shapes that make up Czinger's components and sub-assemblies. “It ends up looking cool and exciting, which is great for a hypercar program where one of the attributes of a vehicle like ours is to make them visually interesting,” Baldry added.
Another major innovation is Czinger’s robotic assembly process, which eliminates the need for fixturing. Instead of relying on traditional tooling to hold components in place during assembly, robots use precisely controlled adhesives and laser-tracked positioning to bond parts together. “At the end of the process, there's a robot holding this ginormous printed structure,” Baldry said.
Key 3D-Printed Components in the Czinger 21C
Rear Subframe
Largest individual component, printed in sections for efficient material use. Resulting shapes are then laser-metal 3D printed and assembled in an automated, fixtureless robotic cell using high-performance adhesives developed in-house. A reflection of natural structures, the subframe's artistic design is commonly compared to a metal skeleton.
Gearbox Case
Automated seven‑speed semi‑sequential gearbox. Considered to be the first topology-optimized, additively manufactured production gearbox case to move beyond prototype. The unique printing process and proprietary aluminum alloy results in significant mass savings and structural performance.
BrakeNode
A single integrated structure combining the brake caliper and knuckle, reducing weight and improving performance. By consolidating functions, the BrakeNode lowers part count, simplifies assembly, and improves rigidity. Serves as a conduit for brake fluid.
Baldry highlighted the ability to iterate as a key advantage in Czinger's manufacturing. “We've not had to wait for the tooling to be manufactured. We make the first iteration, test it, find any issues that might exist, and make immediate improvements,” he said. “We can also accelerate our validation loop by making a one-off, instrumenting it and collecting data from real-use of that component in the field, then feed it back into the optimizer instantly.”
Bumps in the Road
Reaching this point was not without its challenges. Early concerns (now a distant memory, according to Baldry) included porosity in printed materials and variability in mechanical properties based on print orientation. Through continued development, Divergent refined its processes to ensure consistent material properties and reliable part performance.
Baldry recalled a major decision point when the company was developing its gearbox case. “We kind of committed to it before we had the ability to actually manufacture it,” he explained. “I remember sitting down with Kevin and Lukas Czinger at a key point in time and saying, hey guys, you know, we're kind of at this fork in the roads. Either we commit and cast the gearbox, which would have been the easy, conventional option, or we take this other route.”
Knowing that new printers were coming and the needed materials were going to be available, the team agreed to set off down that route. It was a decision that paid off, resulting in “the first 3D-printed, additively manufactured production gearbox case specifically designed for additive,” Baldry said. Over multiple iterations, Czinger refined its gearbox case design, integrating heat exchanger elements directly into the structure.
“If we push too far with an experimental design, we can always take a step back,” Baldry said. “We’re not locked into a mold or a tooling setup—we just reload an earlier version and print it again. That’s a huge shift in how we think about engineering.”
Full Speed Ahead for the Future
While Czinger’s technology is currently applied to a low-volume hypercar, its broader implications for the automotive industry are significant. Several major manufacturers, including McLaren and Bugatti, have already begun working with Divergent to explore the potential of 3D-printed structural components in their vehicles.“How can you make things faster and improve before you get to the printer?” Baldry asked. “How can you make the printing faster? How can you make the post-processing faster as well and the assembly of structures too?”
“The thing that excites us here, as design engineers within Czinger itself is just starting to spread that technology further outside of the primary structures,” he said, with next steps being the integration of cooling, electrical, and fluid networks directly into structural components. By embedding additional functions within structural elements, the aim is to further optimize packaging, reduce part counts, and improve overall vehicle efficiency.
Divergent and Czinger are also focused on scaling production and reducing costs, making additive manufacturing viable for higher-volume vehicle production. As the technology matures, there is potential for on-demand part printing, where components are produced as needed rather than stored in large inventories.
Reflecting on the progress made over the last six years, Baldry is optimistic about what’s ahead. “I really do believe that this will be the way things are made in future. In terms of efficient use of materials and energy, with the ability to recycle these materials as well and put them back into the manufacturing chain. It all seems to me to be there for the taking.”
Sarah Alburakeh is a strategic content editor.
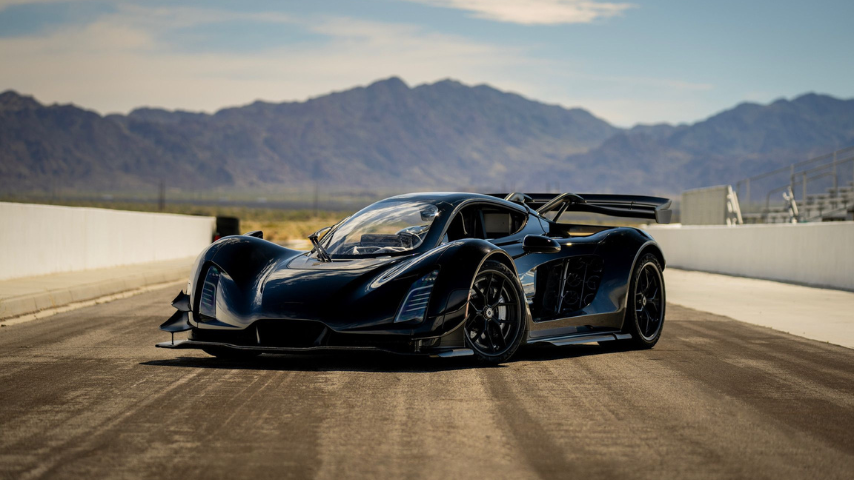
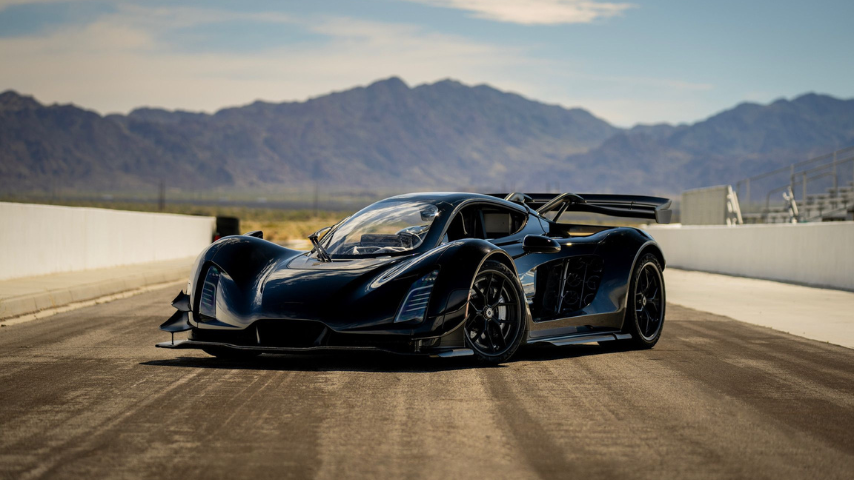