5 Agricultural Robots Bringing Food to the Table
5 Agricultural Robots Bringing Food to the Table
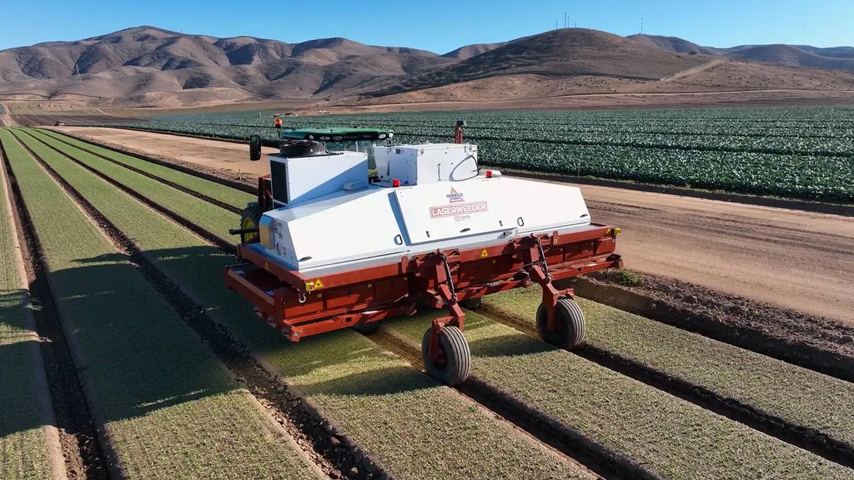
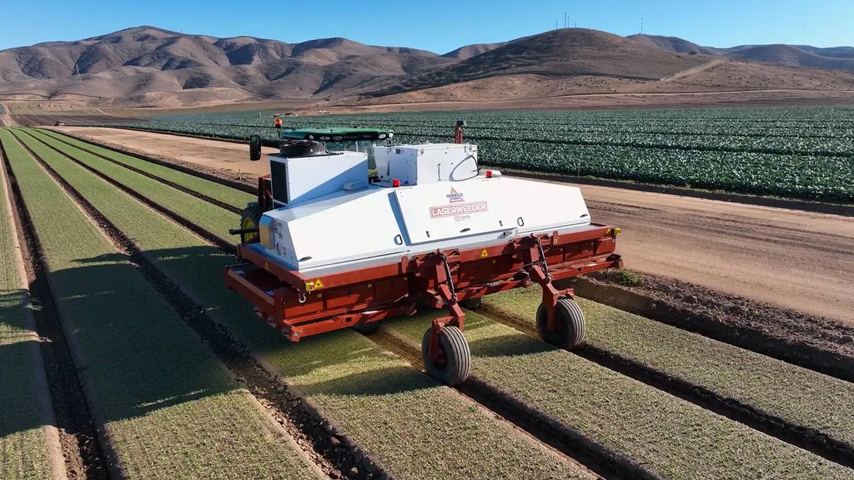
Laserweeder is just one of a range of agricultural robots now working farmland.
Agriculture continues to move further into automation. The trend began with self-driving tractors fitted with software and sensors to keep equipment moving throughout the day and into the night. It has expanded to include a range of robots, fitted with more sensors, software, lasers, and specialized grippers to harvest crops, weed the fields, and kill pests. Here are five new agricultural robots plying the nation’s farms.
Farming is, of course, about the cultivation of life, but it also requires the destruction of life. Weeding the land is one of the more toilsome and aggravating tasks that face farmers—and gardeners, for that matter. Now there are a handful of robots that can take on that burden, including Carbon Robotics’ Laserweeder. Inside this flora killer are lights and a dozen high-res cameras that scan the crop rows as it passes over them.
Become a Member: How to Join ASME
An AI system determines, in milliseconds, which plants are wanted, and which are to be weeded. Then its 150 carbon-dioxide lasers fire once ever 50 milliseconds at the offending growth, removing the weeds as potential nutrient thieves in an instant. It can mow through 200,000 weeds an hour, destroying 99 percent of them. With that kind of efficiency, the Laserweeder is good for the earth and the farmer, as it slashes the need for herbicides.
Who hasn’t bought a box of strawberries only to find that some of them are bruised, others moldy, and still others perfectly ready for popping into the mouth hole? That wild variability in quality and ripeness may soon be a thing of the past, thanks to the Harvest CROO. From the outside, the harvester looks like the tour bus for an electronica band.
But, as it cruises over rows of berries, a vision system inside the box scans each fruit and determines, in milliseconds, which are ripe for the picking. Then one of the 16 robots in the harvester gathers the berries with very gentle grippers. Lidar units on the outside of big box help steer it carefully down each row and keep it from trampling crops and any people that might be in the way.
Some fruiting plants have male and female flowers and pollen from the male has to be brought—by insect or toothbrush—to the female to produce a fruit. That’s the system of cucumbers and squash, for instance. Others, like the tomato and the blueberry, have both male and female organs built into the same flower. All they need is a little vibration and the deed is done. Usually bumble bees are the key pollinators, but their populations are decreasing. Humans can handle the task, but it’s labor intensive, as each flower needs to be individually twiddled. But now Polly the pollinating robot can take over.
Listen to Our Podcast: Beyond Precision Agriculture
Created by the Israeli company Arugga, this little robot slides between rows scanning plants as it goes. It’s AI recognizes not only flowers, but which ones are ready for pollination. Then it fires a puff of air, shaking the flower and beginning the fertilization process that will eventually lead to fruiting. The robot can work in temperatures and lighting that bumblebees don’t like, so it outperforms both humans and bees at the job.
Smaller farms are not likely to afford a different robot for hoeing, planting, weeding, and harvesting. For them, France’s Naio Technologies has created Oz. Coming in at a mere 330 pounds and 33 inches tall, this fully electric robot is guided by RTK GPS, making it accurate to within a centimeter.
It’s essentially a tiny fully autonomous tractor capable of weeding and seeding, furrowing, hoeing, and hauling—eight hours at a time. There are right now some 220 Oz bots in 48 countries that have done 36,000 hours of work. With a price tag around $30,000, commercial gardeners can afford to put it to use as well.
Before anyone or any machine begins to cultivate a piece of land, that land must be cleared of rocks. They block growth and can damage equipment. Removing them has always been a labor-intensive affair, but now TerraClear has created a digital tool and a physical tool to better clear the land.
First, a drone uses neural-network-produced software to identify the size and location of every rock sitting in the dirt, producing a rock map of the field. The robotic Rock Picker then uses three belted fingers to pick the rocks from the soil and deposit them in a scoop. TerraClear now is working to make that whole process completely autonomous.
Michael Abrams is a technology writer in Westfield, N.J.
Farming is, of course, about the cultivation of life, but it also requires the destruction of life. Weeding the land is one of the more toilsome and aggravating tasks that face farmers—and gardeners, for that matter. Now there are a handful of robots that can take on that burden, including Carbon Robotics’ Laserweeder. Inside this flora killer are lights and a dozen high-res cameras that scan the crop rows as it passes over them.
Become a Member: How to Join ASME
An AI system determines, in milliseconds, which plants are wanted, and which are to be weeded. Then its 150 carbon-dioxide lasers fire once ever 50 milliseconds at the offending growth, removing the weeds as potential nutrient thieves in an instant. It can mow through 200,000 weeds an hour, destroying 99 percent of them. With that kind of efficiency, the Laserweeder is good for the earth and the farmer, as it slashes the need for herbicides.
Who hasn’t bought a box of strawberries only to find that some of them are bruised, others moldy, and still others perfectly ready for popping into the mouth hole? That wild variability in quality and ripeness may soon be a thing of the past, thanks to the Harvest CROO. From the outside, the harvester looks like the tour bus for an electronica band.
But, as it cruises over rows of berries, a vision system inside the box scans each fruit and determines, in milliseconds, which are ripe for the picking. Then one of the 16 robots in the harvester gathers the berries with very gentle grippers. Lidar units on the outside of big box help steer it carefully down each row and keep it from trampling crops and any people that might be in the way.
Some fruiting plants have male and female flowers and pollen from the male has to be brought—by insect or toothbrush—to the female to produce a fruit. That’s the system of cucumbers and squash, for instance. Others, like the tomato and the blueberry, have both male and female organs built into the same flower. All they need is a little vibration and the deed is done. Usually bumble bees are the key pollinators, but their populations are decreasing. Humans can handle the task, but it’s labor intensive, as each flower needs to be individually twiddled. But now Polly the pollinating robot can take over.
Listen to Our Podcast: Beyond Precision Agriculture
Created by the Israeli company Arugga, this little robot slides between rows scanning plants as it goes. It’s AI recognizes not only flowers, but which ones are ready for pollination. Then it fires a puff of air, shaking the flower and beginning the fertilization process that will eventually lead to fruiting. The robot can work in temperatures and lighting that bumblebees don’t like, so it outperforms both humans and bees at the job.
Smaller farms are not likely to afford a different robot for hoeing, planting, weeding, and harvesting. For them, France’s Naio Technologies has created Oz. Coming in at a mere 330 pounds and 33 inches tall, this fully electric robot is guided by RTK GPS, making it accurate to within a centimeter.
It’s essentially a tiny fully autonomous tractor capable of weeding and seeding, furrowing, hoeing, and hauling—eight hours at a time. There are right now some 220 Oz bots in 48 countries that have done 36,000 hours of work. With a price tag around $30,000, commercial gardeners can afford to put it to use as well.
Before anyone or any machine begins to cultivate a piece of land, that land must be cleared of rocks. They block growth and can damage equipment. Removing them has always been a labor-intensive affair, but now TerraClear has created a digital tool and a physical tool to better clear the land.
First, a drone uses neural-network-produced software to identify the size and location of every rock sitting in the dirt, producing a rock map of the field. The robotic Rock Picker then uses three belted fingers to pick the rocks from the soil and deposit them in a scoop. TerraClear now is working to make that whole process completely autonomous.
Michael Abrams is a technology writer in Westfield, N.J.
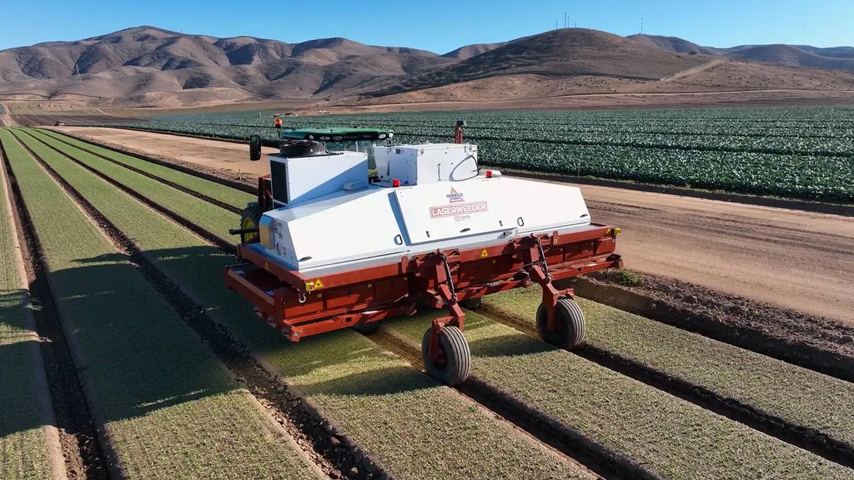
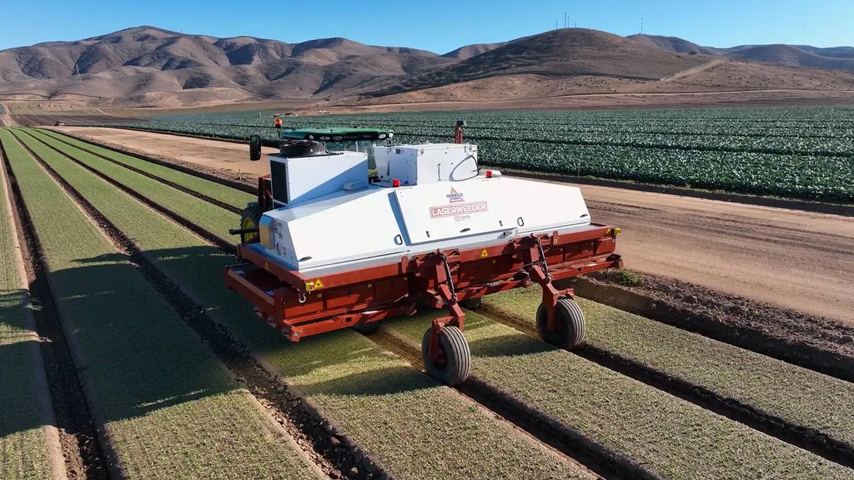