Augmented Reality Is Transforming Mine Safety
Augmented Reality Is Transforming Mine Safety
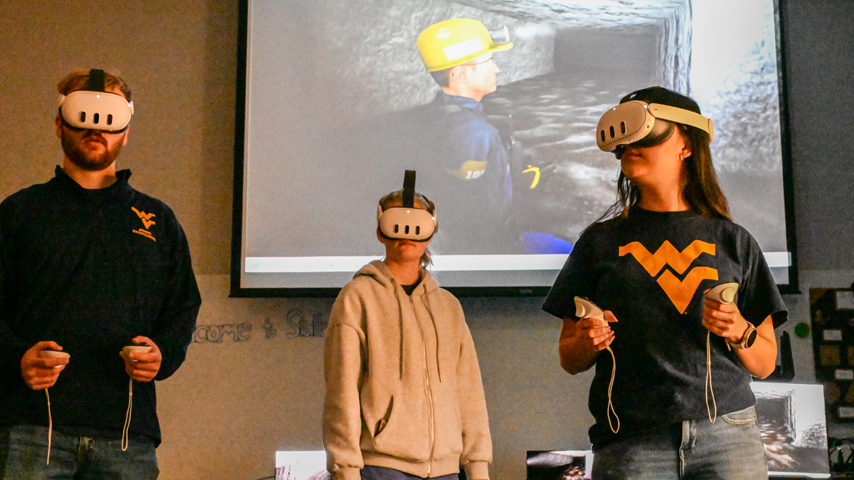
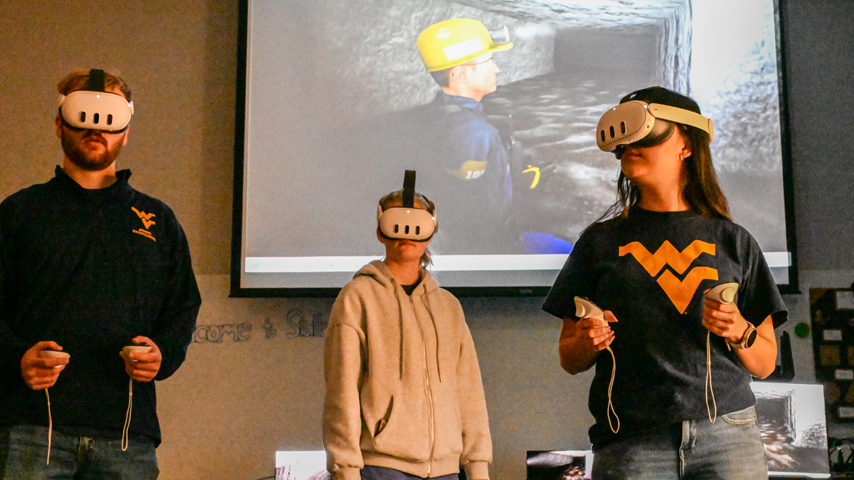
Specially designed AR training modules aim to improve safety outcomes in dangerous mining.
Augmented reality (AR) training modules are helping to improve visibility awareness around large mining equipment. Researchers at West Virginia University (WVU) have started developing these modules mainly focused on haulage machinery used to transport materials or other equipment within a mine.
Using data from the National Institute for Occupational Safety and Health (NIOSH) called blind area diagrams, the team is creating modules that will project digital images through an AR headset in real world settings. This immersive approach will allow operators to engage in immersive, hands-on learning, identify blind spots, recognize risk situations, and practice avoidance strategies safely.
“Imagine wearing an AR headset in a university parking lot, projecting a holographic haul truck, or at a mine site, anchoring it to a real haul truck. By fixing the projection in place, we can overlay critical information,” explained Amy McBrayer, teaching assistant professor at the University of West Virginia’s Department of Mining Engineering. “As you walk around the truck, the headset delivers real-time feedback, highlighting blind spots and other key data to improve situational awareness and safety.”
More for You: Bringing Augmented Reality to Engineering Classes
With support from the US Department of Labor Brookwood-Sago Mine Safety Grants Program, the team worked to complete the initial modules within the first grant year, emphasizing ground personnel’s understanding of drivers’ blind spots while also providing drivers a critical ground-level perspective.
“This training isn’t just for drivers. It’s also crucial for mine surveyors, engineers, and anyone working around heavy equipment. By showing blind spots and operational limits, we can boost safety awareness for everyone, no matter what role they play,” McBrayer explained.
AR development
Powered haulage poses a major safety concern for the mining industry as the leading cause of fatalities in all mines. “We’re focusing on new employees, especially those with less than a year of experience, since that's when safety challenges are highest,” McBrayer said.
Developing an effective AR training program for a diverse mining workforce requires an iterative approach. Pilot testing with experienced and new workers will gather feedback on usability and effectiveness. This input will guide module refinements, shaping interface adjustments, complexity levels, and varied learning methods. As the program expands, ongoing testing and refinement ensure relevance, with performance monitoring and structured feedback to suit industry needs.
“We know some operators may hesitate to embrace AR training. The mining workforce includes workers with varying levels of acceptance of technology, both those new to the industry and experienced pros who’ve been in the industry for years,” McBrayer explained. “The challenge is making the technology work for both—building on the expertise of seasoned operators while keeping training clear and approachable for newcomers and students. We want it to be in-depth without feeling overwhelming.”
A combination of factors led to the steady decline in mining-related fatalities in the 20th century. Agencies like the Mine Safety and Health Administration (MSHA) enforced stricter regulations, technological advancements improved equipment and monitoring systems, and enhanced worker training strengthened safety practices. Despite these improvements, accidents still occurred. The mining industry focused technologies and training methodologies to reduce miner risk and increase awareness. More education and further safety measures remained necessary to continue reducing risks.
Beyond the AR modules, the research team planned to develop interactive quizzes, follow-up questionnaires, and data analytics for performance tracking, addressing both technical and statutory training needs.
West Virginia mines
The US Energy Information Administration’s Annual Coal Report 2023 highlighted West Virginia as the state with the most coal mines, over half of which are surface mines. The nationwide decline in coal-fired power plants forced mining companies to shift focus toward extracting critical minerals needed for renewable energy and electric vehicles. Across the United States, companies invested in automation and sustainable mining practices to stay competitive and environmentally responsible.
Surface mining in West Virginia, shaped by its mountainous terrain, required the mitigation of substantial safety hazards, including risks from heavy machinery collisions, blind spots, highwall failures, rock falls, and exposure to dust and noise. Researchers and industry professionals continue to employ advanced techniques to mitigate and reduce miner exposure. Mine sizes vary, with large-scale operations deploying numerous haul trucks daily, adjusting fleet sizes based on production demands.
Discover the Benefits of ASME Membership
Further development of augmented reality (AR) training modules could expand into underground mines, adapting surface mine training to address key environmental differences. Confined space training would emphasize navigation, spatial awareness, and emergency egress while low-light conditions require specialized AR displays. Beyond haul truck operations, AR could enhance emergency response and navigation. And tailoring AR training to the unique challenges of underground mining would improve safety and efficiency.
WVU’s development of AR training modules, grounded in NIOSH data, mark a crucial step toward addressing the persistent safety challenges in mining. By delivering immersive, hands-on experiences that highlight blind spots and operational hazards, this training bridges the knowledge gap between aging and incoming workforces, reducing risks and improving safety outcomes.
Nicole Imeson is an engineer and writer in Calgary, Alberta.