Autonomous Freight Takes to the Rail, Road, Sea, and Air
Autonomous Freight Takes to the Rail, Road, Sea, and Air
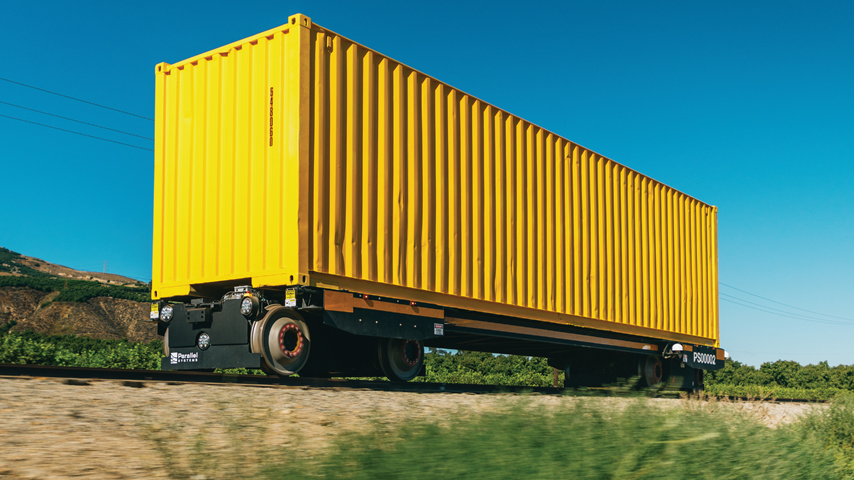
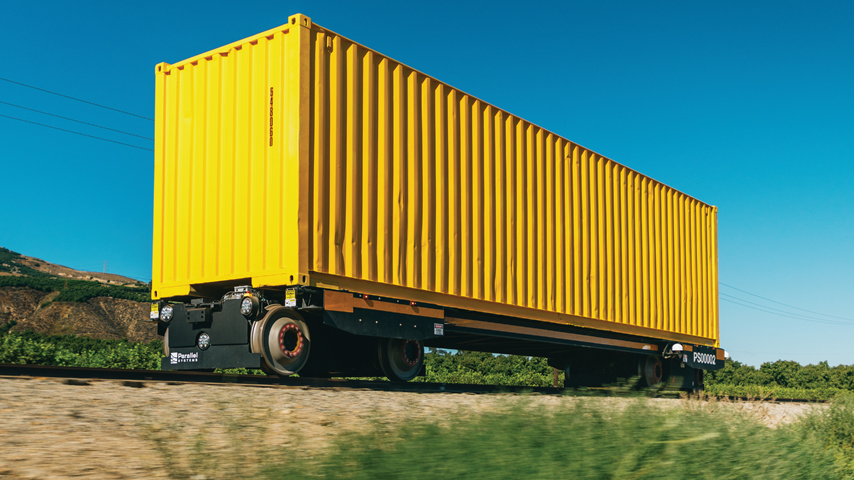
Startups are looking to develop self-driving cargo delivery vehicles that can improve delivery times, cut emissions, and mitigate skilled-worker shortages.
Autonomous vehicles are here—to a degree. Driverless cars are already shuttling busy professionals to work and elsewhere, so they can sit back and read a magazine or do something else productive along the way. Robotaxis and air taxis appear to be close behind too.
A parallel trend is now on the rise, bringing autonomy to freight transportation. Engineers are launching companies that utilize driverless trucks, trains, boats, and drones to ship and deliver goods.
While these modes of autonomous transit may not be as sexy as an air taxi, they are already improving supply chains.
“We’re driving 24/7 for freight customers today and we drive for large carriers across the United States,” said Andreas Wendel, chief technology officer at Kodiak Robotics, a Mountain View, Calif., company that outfits autonomous tractor-trailers.
A serendipitous amalgamation of technological advancements in recent years has helped with the rise of autonomous cargo vehicles. Some experts even claim autonomous technologies can already surpass a human driver’s capabilities, though studies have not yet proven this conclusively. These vehicles use cameras, LiDAR, and radar to perceive the outside environment and various other types of sensors to monitor engines, motors, and other moving parts. Robotics, computer vision, artificial intelligence (AI), machine learning, and advanced software then help process all that data.
Past technological shortcomings of features such as LiDAR translated into limited capabilities during inclement weather, which previously limited the implementation of such systems. However, with the advent of deep learning techniques, autonomous vehicles can now effectively identify outdoor weather conditions and make appropriate decisions to easily adapt to new conditions and environments.
The Latest Breakthroughs: R&D Pulse Highlights Engineering Research
But the fundamental mechanical technology behind autonomous cars and trucks has remained the same for years. For steering, servomotors on the steering column use signals received from electronic devices to make movements and corrections to control the vehicle as it motors down the road or maneuvers in a parking lot. At the same time, pneumatic valves and cylinders actuate the brakes as necessary, also using signals from a controller.
Autonomous cargo vehicles offer several benefits. They are particularly good at long hauls across continents and oceans. These are typically “long and dull routes” that are quite dangerous for human drivers, Wendel added. Last year, trucking companies in the United States suffered a record deficit of 80,000 drivers, according to the American Trucking Associations. Despite this, there is an immense need for drivers and operators to move freight across these routes—and since few people want to take on those duties, autonomous vehicles can fill this gap.
“For a typical trip, the product will have a human driving on the beginning and the end, and a long stretch of autonomy in between,” Wendel explained. “Humans want to be local drivers. It helps us to have humans in the loop at the beginning and end.” Faster deliveries can also result from this arrangement.
There’s an environmental consideration, too. Autonomous vehicles could reduce a fleet’s carbon footprint. “We see more than 10 percent fuel savings already,” he said.
Electric and hydrogen vehicles are on the horizon as well. “Our technology works with all of those future technologies, so there’s huge potential to further improve emissions,” Wendel added.
Although driverless technology’s market readiness has been up to some debate in recent years, implementation has most certainly been slower since regulations have not kept the same pace. Experts say the technology is 85 to 90 percent of the way to being fully market-ready and that it could take years, or even decades, to get over the final hump. Not surprisingly, states are at various stages of evaluating the technology and passing laws concerning its implementation.
“At the moment, we have a safety driver in the vehicle—a person monitoring everything. The next step is to be driverless,” Wendel said.
But when it comes to electrified rail systems, although there are some systems that have made that conversion, such as “an airport people mover, an underground transit system, and commuter rail systems, people really haven’t done this for freight,” said Tim Luchini, CEO and co-founder of Intramotev, a rail company based in St. Louis. That is beginning to change and a new breed of railroad companies is emerging as a result.
Shipping companies currently gain economy of scale with long trains traveling great distances—Chicago to Los Angeles, for example. The locomotives do all the work pulling and pushing the cars along for the ride.
However, these newer rail companies are opting for much shorter trains, Luchini said.
“We can enable trains of one or two cars, or five to 10 cars at a time with the same unit economics as a three-mile-long train,” he explained. “We can do that because we shrank the power system.” Every car has a motor that can pull itself and its fellow cars as needed when linked together.
Intramotev currently offers two products. One is the TugVolt, which is a rail car that can be run remotely or autonomously, depending on the operating perspective. TugVolt can also decouple to independently service first and last mile legs. The second is ReVolt, which uses a regenerative braking technology that captures energy to help power the locomotive.
“Sensors are mounted around the periphery of the vehicle. Things like cameras and radars, sensing and detecting the environment the car is going to live in. Then you’ll have things like the real-time operating system running on the rail car,” Luchini explained. “You also have other things like video processing units and other computers that help manage all that data.”
More About Autonomous Roadways: Collective Perception Allows Vehicles to See More
A mechanical engineer by training, Luchini did his undergraduate work at the University of South Dakota and got his doctorate at Michigan State in jet engines. He went to work in the defense industry on unmanned systems like cruise missiles and fighter jet platforms, then became a manager at Boeing on flying cars and package delivery drones. He collaborated with his friend Alex Piper, who was studying logistics at the University of Southern California, to found Intramotev.
The concept of an autonomous train may sound simple, as the vehicle is constrained by rails and only goes forward or backward. But when traveling a long distance, the train eventually must turn, which involves shifting to different tracks. That must still be done via switches, some of which are electrified and controlled remotely, depending on location.
Over in Los Angeles, Parallel Systems is building automated, battery-electric, freight rail vehicles and the tools to integrate this service into railroad operations.
“We coexist with and complement existing freight rail service,” explained Matt Soule, the company’s co-founder and CEO. “Our technology will allow railroads to expand to provide service on rail corridors less than 1,000 feet.”
Soule, who is an electrical engineer, launched Parallel Systems after working in the aerospace industry for 20 years.
“I left SpaceX after being there for 13 years,” he said. “I started getting interested in climate tech, ways to decarbonize. I was going to get into transportation, particularly the rail industry. I was enamored with the untapped potential of rail, starting with the energy efficiency.”
Parallel Systems’ solution, now in its second generation, ensures every rail car can move on its own, each equipped with a battery, motor, sensor suite, communications, and charger. These trains also have regenerative braking technology.
For You: Drones Deliver in the Maritime Environment
“We have pre-controllers, inverters for the motor, computers for perception, and radios,” Soule said. “It looks like an EV on steel wheels.”
Parallel is also collaborating with the National Renewable Energy Laboratory—its Advanced Locomotive Technology and Rail Infrastructure Optimization System, or ALTRIOS, software will help quantify how Parallel’s vehicles reduce energy consumption and emissions compared to existing locomotives. The hope is that this partnership will help kick start further decarbonization across the rails.
One such technology paving the way is Orca AI’s SeaPod. This AI-based maritime navigation assistant acts as a fully automated watchkeeper. It gathers information from multiple sources and sensors, including thermal cameras and navigation sensors. This integration compensates for the limitations of specific sensors, such as day cameras in poor visibility or radar noise in congested waters.
The story of Orca AI began 15 years ago, when co-founders Yarden Gross and Dor Raviv met. These two naval technology experts began discussing the impacts that autonomy, AI, and computer vision were having on the maritime industry.
Fast forward to 2018, when they founded Orca AI to lay the foundation for global adoption of smart, autonomous ships. The company combines sensors with existing onboard systems to improve safety and navigation capabilities of ships on crowded waterways.
Headquartered in Israel, Orca AI looks to bridge sea-bound ships to the shore to ensure shipping companies keep their cargo safe and efficient, all while providing the technology to bring autonomous cargo ships to reality.
The world’s first autonomous commercial cargo ship, a 750-gross-ton vessel, recently completed a test run using SeaPod. It successfully navigated a nearly 500-mile voyage through the congested waters of Tokyo Bay without human intervention for 99 percent of the trip.
Meanwhile, Dronamics—a company based in Sophia, Bulgaria—is trying to create an industry that uses breakthroughs in aviation, software, and robotics to revolutionize air cargo transport. The company’s leadership has a dream of enabling same-day delivery for everyone, everywhere, with a “cargo drone airline.” This would make air freight more efficient, affordable, and accessible.
Our Interview: Andreas Wendel on Self-Driving Trucks
Dronamics’ drone, the Black Swan, can carry the same load as a small cargo van—up to 770 pounds—to a distance of up to 2,500 kilometers. With a wingspan of 52 feet, the 14-foot-tall gasoline-powered drone can reach speeds up to 125 miles per hour and an altitude of 20,000 feet.
The company’s co-owner and chief technology officer Konstantin Rangelov said the firm may develop larger models as well that would have the same efficiencies as the Black Swan. Dronamics currently provides delivery services for couriers such as FedEx, UPS, and DHL.
“We don’t want to put up fancy new buildings,” Rangelov said. “There are over 50,000 airports and airfields in the world currently, and that’s plenty to use without building new ones.”
Rangelov was studying aerospace engineering in the Netherlands at the same time his brother Svilen was studying economics in the United States. After graduating, Rangelov began working with a drone to transport goods between cities, while his brother began developing a drone delivery system in 2014. Together, they created a system that used larger drones for bigger payloads.
More from the Magazine: Begun, the Drone Wars Have
Although the company’s drones can be autonomously or remotely piloted, regulations currently only allow remotely piloted flights. An autonomous flight would require filing a flight plan, Rangelov noted. The drones operate in controlled shared airspace regulated by the local civil aviation authority, the European Aviation Safety Agency in Europe and the Federal Aviation Administration in the United States.
“We have a ground control station at a given airport, and we have two pilots controlling it as if they were in the cockpit of an airplane,” he said. “When regulations catch up in the next couple of years, we’ll switch to autonomous flights. We’ll have one pilot responsible for up to 12 aircraft.”
One advantage is that filling the Black Swan with 800 pounds of cargo takes far less time than loading a plane with several tons, Rangelov added. “With a normal delivery service, you have to take a part to a warehouse, where it gets sorted to go on a big airplane, then the plane goes to another airfield and warehouse,” he said. “You basically cut out the middleman and shorten the distance between supplier and client.”
As this momentum continues to build in realizing autonomous freight transportation systems across all modes, these solutions will likely soon be visible by land, sea, and sky.
Tom Gibson, P.E. is a freelance writer based in Sugar Grove, Va. He is a consulting mechanical engineer specializing in machine design, sustainability, and recycling.
A parallel trend is now on the rise, bringing autonomy to freight transportation. Engineers are launching companies that utilize driverless trucks, trains, boats, and drones to ship and deliver goods.
While these modes of autonomous transit may not be as sexy as an air taxi, they are already improving supply chains.
“We’re driving 24/7 for freight customers today and we drive for large carriers across the United States,” said Andreas Wendel, chief technology officer at Kodiak Robotics, a Mountain View, Calif., company that outfits autonomous tractor-trailers.
A serendipitous amalgamation of technological advancements in recent years has helped with the rise of autonomous cargo vehicles. Some experts even claim autonomous technologies can already surpass a human driver’s capabilities, though studies have not yet proven this conclusively. These vehicles use cameras, LiDAR, and radar to perceive the outside environment and various other types of sensors to monitor engines, motors, and other moving parts. Robotics, computer vision, artificial intelligence (AI), machine learning, and advanced software then help process all that data.
Past technological shortcomings of features such as LiDAR translated into limited capabilities during inclement weather, which previously limited the implementation of such systems. However, with the advent of deep learning techniques, autonomous vehicles can now effectively identify outdoor weather conditions and make appropriate decisions to easily adapt to new conditions and environments.
The Latest Breakthroughs: R&D Pulse Highlights Engineering Research
But the fundamental mechanical technology behind autonomous cars and trucks has remained the same for years. For steering, servomotors on the steering column use signals received from electronic devices to make movements and corrections to control the vehicle as it motors down the road or maneuvers in a parking lot. At the same time, pneumatic valves and cylinders actuate the brakes as necessary, also using signals from a controller.
Autonomous cargo vehicles offer several benefits. They are particularly good at long hauls across continents and oceans. These are typically “long and dull routes” that are quite dangerous for human drivers, Wendel added. Last year, trucking companies in the United States suffered a record deficit of 80,000 drivers, according to the American Trucking Associations. Despite this, there is an immense need for drivers and operators to move freight across these routes—and since few people want to take on those duties, autonomous vehicles can fill this gap.
“For a typical trip, the product will have a human driving on the beginning and the end, and a long stretch of autonomy in between,” Wendel explained. “Humans want to be local drivers. It helps us to have humans in the loop at the beginning and end.” Faster deliveries can also result from this arrangement.
There’s an environmental consideration, too. Autonomous vehicles could reduce a fleet’s carbon footprint. “We see more than 10 percent fuel savings already,” he said.
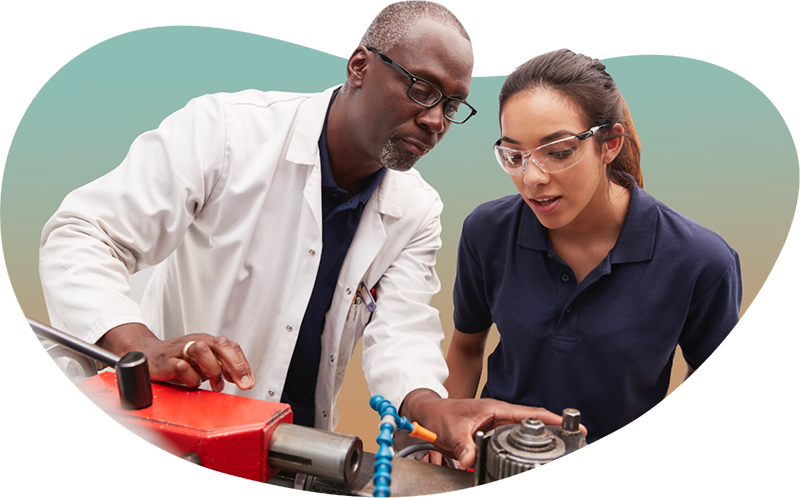
You Belong Here
ASME Membership provides you an instant community of engineers, opportunities to stay on top of industry trends, and a host of other valuable benefits.
Electric and hydrogen vehicles are on the horizon as well. “Our technology works with all of those future technologies, so there’s huge potential to further improve emissions,” Wendel added.
Although driverless technology’s market readiness has been up to some debate in recent years, implementation has most certainly been slower since regulations have not kept the same pace. Experts say the technology is 85 to 90 percent of the way to being fully market-ready and that it could take years, or even decades, to get over the final hump. Not surprisingly, states are at various stages of evaluating the technology and passing laws concerning its implementation.
“At the moment, we have a safety driver in the vehicle—a person monitoring everything. The next step is to be driverless,” Wendel said.
On the tracks
Diesel-electric locomotives first appeared in the 1920s as a replacement for steam-driven trains. Most freight trains in the United States still utilize this technology, which deploys an electric motor that runs off a diesel generator.But when it comes to electrified rail systems, although there are some systems that have made that conversion, such as “an airport people mover, an underground transit system, and commuter rail systems, people really haven’t done this for freight,” said Tim Luchini, CEO and co-founder of Intramotev, a rail company based in St. Louis. That is beginning to change and a new breed of railroad companies is emerging as a result.
Shipping companies currently gain economy of scale with long trains traveling great distances—Chicago to Los Angeles, for example. The locomotives do all the work pulling and pushing the cars along for the ride.
However, these newer rail companies are opting for much shorter trains, Luchini said.
“We can enable trains of one or two cars, or five to 10 cars at a time with the same unit economics as a three-mile-long train,” he explained. “We can do that because we shrank the power system.” Every car has a motor that can pull itself and its fellow cars as needed when linked together.
Intramotev currently offers two products. One is the TugVolt, which is a rail car that can be run remotely or autonomously, depending on the operating perspective. TugVolt can also decouple to independently service first and last mile legs. The second is ReVolt, which uses a regenerative braking technology that captures energy to help power the locomotive.
“Sensors are mounted around the periphery of the vehicle. Things like cameras and radars, sensing and detecting the environment the car is going to live in. Then you’ll have things like the real-time operating system running on the rail car,” Luchini explained. “You also have other things like video processing units and other computers that help manage all that data.”
More About Autonomous Roadways: Collective Perception Allows Vehicles to See More
A mechanical engineer by training, Luchini did his undergraduate work at the University of South Dakota and got his doctorate at Michigan State in jet engines. He went to work in the defense industry on unmanned systems like cruise missiles and fighter jet platforms, then became a manager at Boeing on flying cars and package delivery drones. He collaborated with his friend Alex Piper, who was studying logistics at the University of Southern California, to found Intramotev.
The concept of an autonomous train may sound simple, as the vehicle is constrained by rails and only goes forward or backward. But when traveling a long distance, the train eventually must turn, which involves shifting to different tracks. That must still be done via switches, some of which are electrified and controlled remotely, depending on location.
Over in Los Angeles, Parallel Systems is building automated, battery-electric, freight rail vehicles and the tools to integrate this service into railroad operations.
“We coexist with and complement existing freight rail service,” explained Matt Soule, the company’s co-founder and CEO. “Our technology will allow railroads to expand to provide service on rail corridors less than 1,000 feet.”
Soule, who is an electrical engineer, launched Parallel Systems after working in the aerospace industry for 20 years.
“I left SpaceX after being there for 13 years,” he said. “I started getting interested in climate tech, ways to decarbonize. I was going to get into transportation, particularly the rail industry. I was enamored with the untapped potential of rail, starting with the energy efficiency.”
Parallel Systems’ solution, now in its second generation, ensures every rail car can move on its own, each equipped with a battery, motor, sensor suite, communications, and charger. These trains also have regenerative braking technology.
For You: Drones Deliver in the Maritime Environment
“We have pre-controllers, inverters for the motor, computers for perception, and radios,” Soule said. “It looks like an EV on steel wheels.”
Parallel is also collaborating with the National Renewable Energy Laboratory—its Advanced Locomotive Technology and Rail Infrastructure Optimization System, or ALTRIOS, software will help quantify how Parallel’s vehicles reduce energy consumption and emissions compared to existing locomotives. The hope is that this partnership will help kick start further decarbonization across the rails.
By sea and air
Autonomy is progressing in the maritime industry as well. Some seafaring ships are already controlled remotely or fully autonomous.One such technology paving the way is Orca AI’s SeaPod. This AI-based maritime navigation assistant acts as a fully automated watchkeeper. It gathers information from multiple sources and sensors, including thermal cameras and navigation sensors. This integration compensates for the limitations of specific sensors, such as day cameras in poor visibility or radar noise in congested waters.
The story of Orca AI began 15 years ago, when co-founders Yarden Gross and Dor Raviv met. These two naval technology experts began discussing the impacts that autonomy, AI, and computer vision were having on the maritime industry.
Fast forward to 2018, when they founded Orca AI to lay the foundation for global adoption of smart, autonomous ships. The company combines sensors with existing onboard systems to improve safety and navigation capabilities of ships on crowded waterways.
Headquartered in Israel, Orca AI looks to bridge sea-bound ships to the shore to ensure shipping companies keep their cargo safe and efficient, all while providing the technology to bring autonomous cargo ships to reality.
The world’s first autonomous commercial cargo ship, a 750-gross-ton vessel, recently completed a test run using SeaPod. It successfully navigated a nearly 500-mile voyage through the congested waters of Tokyo Bay without human intervention for 99 percent of the trip.
Meanwhile, Dronamics—a company based in Sophia, Bulgaria—is trying to create an industry that uses breakthroughs in aviation, software, and robotics to revolutionize air cargo transport. The company’s leadership has a dream of enabling same-day delivery for everyone, everywhere, with a “cargo drone airline.” This would make air freight more efficient, affordable, and accessible.
Our Interview: Andreas Wendel on Self-Driving Trucks
Dronamics’ drone, the Black Swan, can carry the same load as a small cargo van—up to 770 pounds—to a distance of up to 2,500 kilometers. With a wingspan of 52 feet, the 14-foot-tall gasoline-powered drone can reach speeds up to 125 miles per hour and an altitude of 20,000 feet.
The company’s co-owner and chief technology officer Konstantin Rangelov said the firm may develop larger models as well that would have the same efficiencies as the Black Swan. Dronamics currently provides delivery services for couriers such as FedEx, UPS, and DHL.
Minimal infrastructure
The firm’s droneports require minimal infrastructure and can be installed at unused airfields, airports, seaports, logistic centers, and factory lots.“We don’t want to put up fancy new buildings,” Rangelov said. “There are over 50,000 airports and airfields in the world currently, and that’s plenty to use without building new ones.”
Rangelov was studying aerospace engineering in the Netherlands at the same time his brother Svilen was studying economics in the United States. After graduating, Rangelov began working with a drone to transport goods between cities, while his brother began developing a drone delivery system in 2014. Together, they created a system that used larger drones for bigger payloads.
More from the Magazine: Begun, the Drone Wars Have
Although the company’s drones can be autonomously or remotely piloted, regulations currently only allow remotely piloted flights. An autonomous flight would require filing a flight plan, Rangelov noted. The drones operate in controlled shared airspace regulated by the local civil aviation authority, the European Aviation Safety Agency in Europe and the Federal Aviation Administration in the United States.
“We have a ground control station at a given airport, and we have two pilots controlling it as if they were in the cockpit of an airplane,” he said. “When regulations catch up in the next couple of years, we’ll switch to autonomous flights. We’ll have one pilot responsible for up to 12 aircraft.”
One advantage is that filling the Black Swan with 800 pounds of cargo takes far less time than loading a plane with several tons, Rangelov added. “With a normal delivery service, you have to take a part to a warehouse, where it gets sorted to go on a big airplane, then the plane goes to another airfield and warehouse,” he said. “You basically cut out the middleman and shorten the distance between supplier and client.”
As this momentum continues to build in realizing autonomous freight transportation systems across all modes, these solutions will likely soon be visible by land, sea, and sky.
Tom Gibson, P.E. is a freelance writer based in Sugar Grove, Va. He is a consulting mechanical engineer specializing in machine design, sustainability, and recycling.
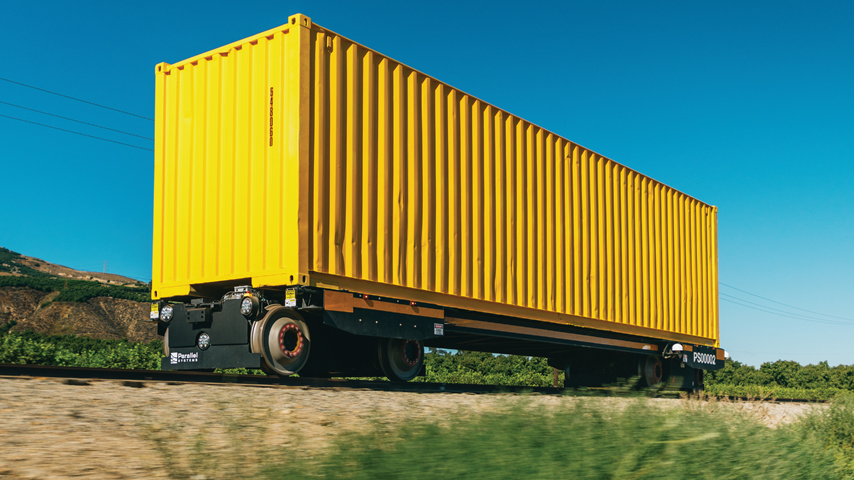
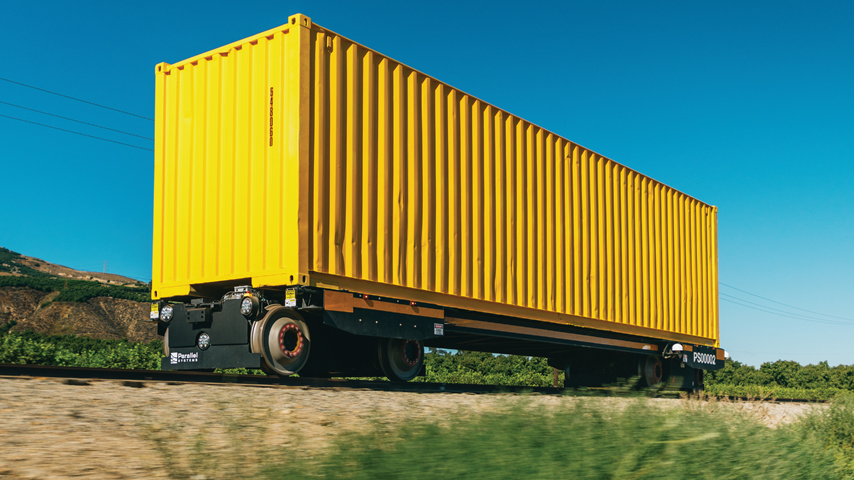