Blog: The Critters Have It
Blog: The Critters Have It
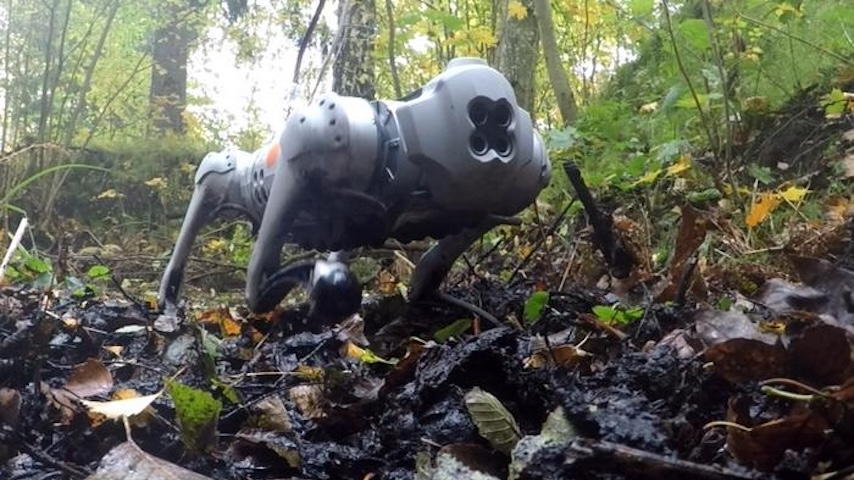
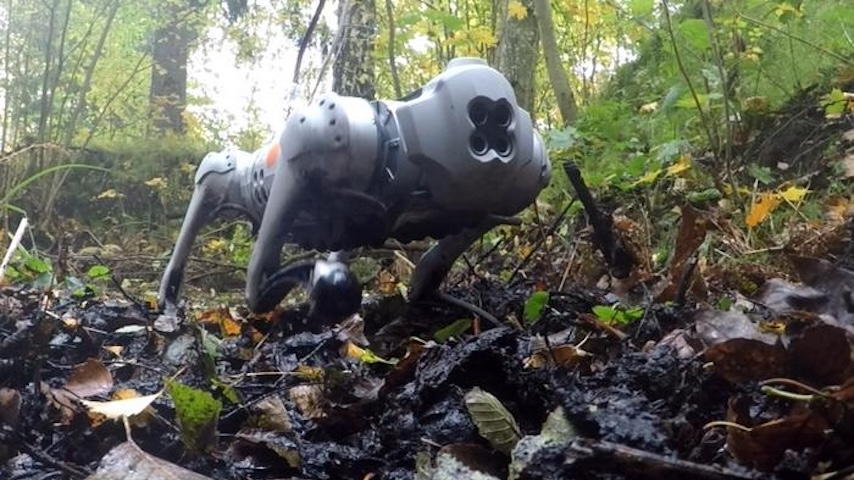
Engineers have long built upon nature's blueprints—some recent inventions range from a robot that soothes to better drone wings.
It’s hard to beat nature’s design, but engineers have long looked to creature power as a starting point in developing new ways to accomplish tasks. Although animal-bots of various kinds are nothing new and are constantly under development, there were a few standouts over the past several months that are worth a look.
Robotic dogs have long been the staple of university engineering programs, but it’s certainly not just dogs that are inspiring engineers. Take for instance, the humble moose.
A moose’s split hooves allow them to easily traverse any terrain, as they expand and contract to grow or shrink the hoof’s contact with the ground (kind of like a suction cup), so roboticists at the Tallinn University of Technology have developed feet modeled after split hooves to allow legged robots to better navigate slippery surfaces.
These silicon feet replicate that expansion and contraction effect, successfully reducing the amount a legged robot sinks and cutting its energy consumption by up to 70 percent, as detailed in “Robotic feet modeled after ungulates improve locomotion on soft wet grounds.”
Another four-legged source of inspiration lies a little closer to home. If you own a cat, chances are you’ve received some affectionate head bumps at some point. Otherwise known as bunting, this behavior has proven to have a healing effect on people, which is something researchers at the University of Tsukuba were looking to replicate in robot form.
Try This Quiz: A Few Notes on Biomimicry
The Tsukuba team created a robot capable of mimicking the bunting action thanks to a flexible neck that’s able to change its rigidity throughout the movement. It was made using a 3D printer and acrylate-styrene-acrylonitrile filaments, while the neck gets its movability thanks to a wire-driven continuum mechanism equipped with two motors.
These findings were detailed in a study published in December, “Development of a Robotic Device that Performs Head Bunting to Relieve User Tension.”
After developing the robot, the team tested it on 22 students and found that their bunting bot significantly reduced tension across all its settings, which they hope will help in the development of more robots that promote healing and stress relief.
Over in Switzerland, researchers at the École Polytechnique Fédérale de Lausanne (EPFL) are taking inspiration from bats to create flexible wings that improve both lift and flight performance in drones, as detailed in “Highly deformable flapping membrane wings suppress the leading edge vortex in hover to perform better,” published in January.
Bats’ flexible membrane wings can be more efficient than those of other winged creatures—some species have been shown to expend about 40 percent less energy than a similarly sized moth, the researchers indicated.
Discover the Benefits of ASME Membership
The EPFL team used an experimental platform with a highly deformable membrane made from a silicone-based polymer, mounted to a rigid frame with edges that rotate around their axes to create flexible wings. Instead of creating a vortex, air moves more smoothly around these wings, generating more lift and efficiency than similarly sized rigid wings would.
“We know that bats hover and that they have deformable membrane wings. How the wing deformation affects the hovering performance is an important question, but doing experiments on live animals is not trivial,” explained former EPFL Ph.D. student Alexander Gehrke, who is now a researcher at Brown University. “By using a simplified bio-inspired experiment, we can learn about nature’s fliers and how to build more efficient aerial vehicles.”
In addition to improving drone flight, these findings could one day help upgrade existing energy technologies such as wind turbines or tidal harvesters.
But moving away from the air and down into the water, another team of engineers has drawn from the shape and movement of manta rays to build a speedy swimming soft robot.
Researchers at North Carolina State University designed their robot’s fins to mimic those of a manta ray, which remain stable when opened and are attached to a flexible, silicone body that can be filled with compressed air—which is what powers the bot. Filling that air chamber forces the fins to bend in a down stroke motion much like a manta ray makes when swimming, so when air is then let out, the fins return to their open stable alignment.
More for You: Why Animals Are Still Faster Than Robots
Studying the manta rays’ fluid dynamics also played a key role in designing the robot’s vertical movement. Their work is discussed in “Spontaneous Snapping-Induced Jet Flows for Fast, Maneuverable Surface and Underwater Soft Flapping Swimmer,” published in December.
“Two years ago, we demonstrated an aquatic soft robot that was able to reach average speeds of 3.74 body lengths per second,” shared Jie Yin, corresponding author and associate professor of mechanical and aerospace engineering at NCSU. “We have improved on that design. Our new soft robot is more energy efficient and reaches a speed of 6.8 body lengths per second. In addition, the previous model could only swim on the surface of the water. Our new robot is capable of swimming up and down throughout the water column.”
This new system gives the team better control of the bot’s movement in water and could open the door to faster and nimbler aquabots in the future.
As inspiring as it is to see how animals help solve engineering conundrums, it’s also exciting to see how engineers can reciprocate for those furry friends who need a bit of mechanical assistance—something I’m particularly interested in as the owner of a corgi who’s been through multiple orthopedic surgeries and is partly bionic at this point.
As part of a senior mechanical engineering course about design methodologies at the University of Texas at Austin’s Cockrell School of Engineering, assistant professor Maryam Tilton worked with Austin Pets Alive (APA), a local animal shelter that helps the most vulnerable of pups, tasking students with designing wheelchairs for dogs with health issues.
This opportunity not only helped the animals, but also helped students visualize the real-world application of the skills they’re learning. A class of 70 students built 10 custom wheelchairs, focusing on the unique needs of each dog.
Students have remained in touch with the rescue and plan to pitch in should any parts of those wheelchairs need repair in the future.
Although I’ll still be interested to see the next robotic dog come down the line, with so many other creatures out there to inspire tomorrow’s engineers, many more fascinating creations lie ahead.
Louise Poirier is senior editor.