Breaking Barriers with High-Velocity Cold Bonding
Breaking Barriers with High-Velocity Cold Bonding
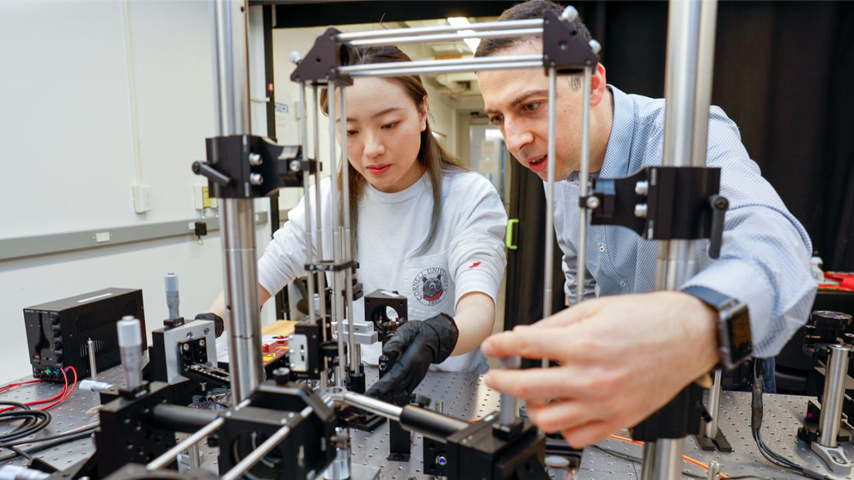
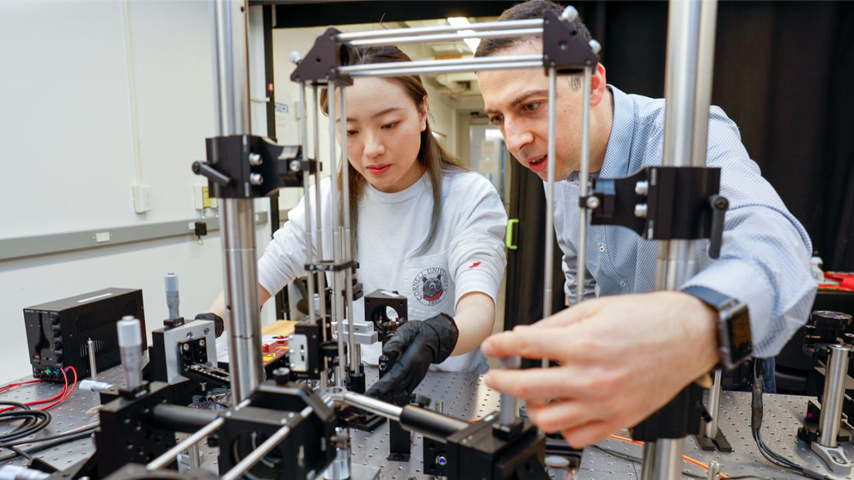
High-speed metallic collisions can form strong, durable atomic bonds, which could unlock ways to enhance 3D printing and other manufacturing techniques.
Cornell University researchers have cracked the code on high-velocity cold bonding by uncovering how surface oxide layer disruptions and metallic particle adhesion drive the process. This development could potentially improve a variety of manufacturing methods.
The team set out to measure the actual strength properties of cold spray bonding to clarify how these coatings or buildups function in structural applications. Previous evaluations and understanding relied on microstructure analysis, but this study, “Strength gradient in impact-induced metallic bonding,” marked the first direct measurement of bond strength of an isolated spray particle, including the strength gradient across individual particles.
“We isolated the individual impact bonding process, measured local interface strengths, and identified the origins of the strengths, providing insight into how particles accumulate and bond,” explained Qi Tang, a Ph.D. candidate at Cornell and first author of the study.
When a high velocity particle strikes the receiving surface, it disrupts the oxide layer coating, generating oxide particulates or debris in a ripple effect from the impact’s epicenter. Oxide layers block a continuous metallic bond between the spray particle and surface, preventing the overall particle bond. However, where the oxide layer broke, the close contact of exposed metal formed stronger bonds. This interaction created a strength gradient, with the weakest point in the center due to the nearly intact oxide layer and a stronger ring where disturbance exposed the metal, tapering off as impact-inducted pressure decreased.
Check This Out: Soft Magnetized Powders for 3D Printing Offer Boost for Electric Motors
The researchers evaporated the metallic chromium layer in the launch pad of a high-powered laser. This process expanded the polyurea film, propelling particles at high speeds toward the receiving surface and mimicking high-velocity cold spray techniques. A high-resolution camera captured and recorded the particle’s shape, size, and speed. In situ micro-tensile testing measured bond strength at various points along the bonded particle, while transmission electron microscopy (TEM) revealed bonded metallic interfaces and oxide layer disruptions. These observations clarified how the particle fractured the oxide layer to expose the underlying metal and how that assisted the bond strength.
“My first specimen came from the impact crater’s center. Then I analyzed one closer to the edge,” Tang explained. “For the first time, we measured bond strength varying across the particle. The bond evolves across the entire surface.”
A welding alternative
Cold bonding employs high-velocity cold sprays to attach one metal to another through kinetic impact, avoiding high temperature. The technique deposits thousands of particles simultaneously, but researchers remain uncertain about how velocity, size, and impact influences behavior. As an alternative to welding, cold bonding offered a safer option to repair metal surfaces in situations where welding or high temperatures present a safety hazard.
Past research examined cold spray processes, including critical velocity (the minimum velocity needed for bonding), temperature, and properties of the materials.
“The focus always stayed on the process. You accelerate tiny metallic particles to supersonic speeds—upon impact, they bond. Our goal shifted from studying the processing science, which we’ve done for decades, to understanding the resulting mechanical properties,” explained Mostafa Hassani, assistant professor at Cornell’s Sibley School of Mechanical and Aerospace Engineering.
The team created a predictive model, using aluminum as a baseline, to calculate impact-induced bond strength. This model focused on two primary mechanisms: surface exposure and bonding pressure. Surface exposure, defined as the ratio of exposed area between the disturbed oxide layer to total surface area, directly influenced bond potential, with greater exposure yielding a more active bonding process. Bonding pressure evaluated the effective force on the contact surface, considering flow stress and fracture process during bonding.
Discover the Benefits of ASME Membership
The research team discovered that particle size played a smaller role in bond strength than velocity. Higher velocities disrupted the oxide layer more effectively, exposing more surface metal and increasing bond strength. When the particle size was increased, the strength gradient spread over the larger area at relatively the same rate as smaller particles.
Moving forward, the team intends to isolate particle size, velocity, and temperature to study their effects on bond strength. By maintaining consistent parameters, they can compare each bond to previous results. With the framework established, the team will adjust and isolate specific parameters, measuring resulting bond strengths, to better understand how each variable impacts the overall bonding process.
A better bond—or not
Researchers have applied their findings to not only improve adhesion between two metals during high-velocity cold bonding, but also to mitigate unwanted surface adhesion. For example, space dust traveling at high speed can disrupt the oxide layer spacecraft develop on earth. Understanding particle adhesion helps rocket developers design spacecraft surfaces that resist oxide layer disruptions and prevent or mitigate exposed surface metal.
By shifting the focus from process mechanics to the properties of the resulting bonds, the team has provided critical insights into how velocity, surface exposure, and oxide layer disruptions affect bond strength.
Using techniques such as laser-driven launching of particles, high-resolution imaging, micromechanical testing, and transmission electron microscopy, the researchers established a predictive model to calculate bond strength based on surface exposure and bonding pressure. With this foundation, the Cornell team can continue optimizing cold bonding techniques, unlocking new possibilities for safer, more effective additive manufacturing, metal repair, and coating applications. These findings not only enhance cold bonding applications but also offer practical solutions for industries, such as aerospace, where surface coatings encounter extreme conditions.
Nicole Imeson is an engineer and writer in Calgary, Alta.
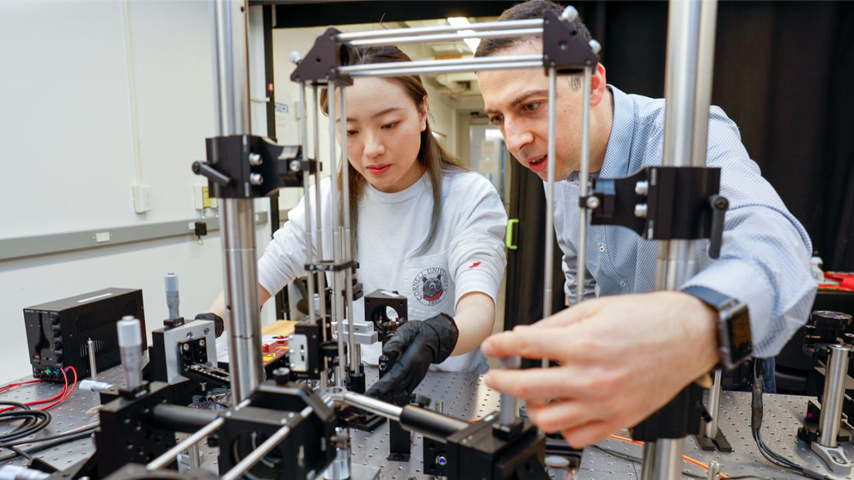
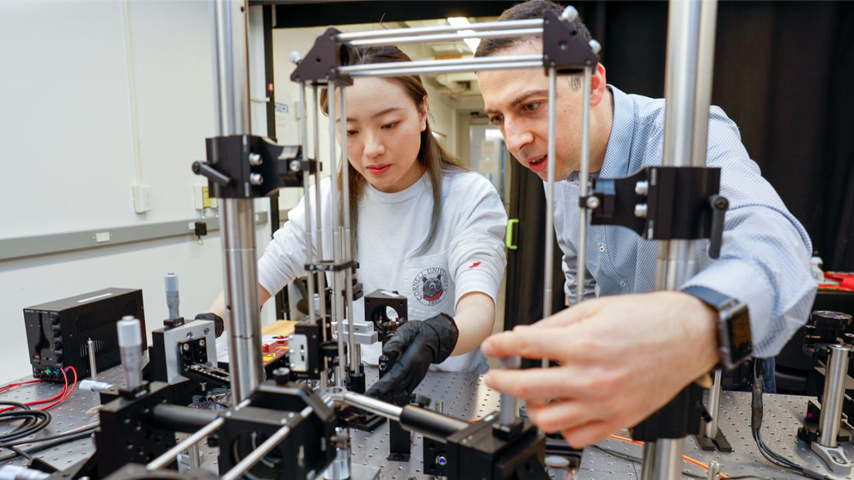