Gold Medal Engineering at the Olympics
Gold Medal Engineering at the Olympics
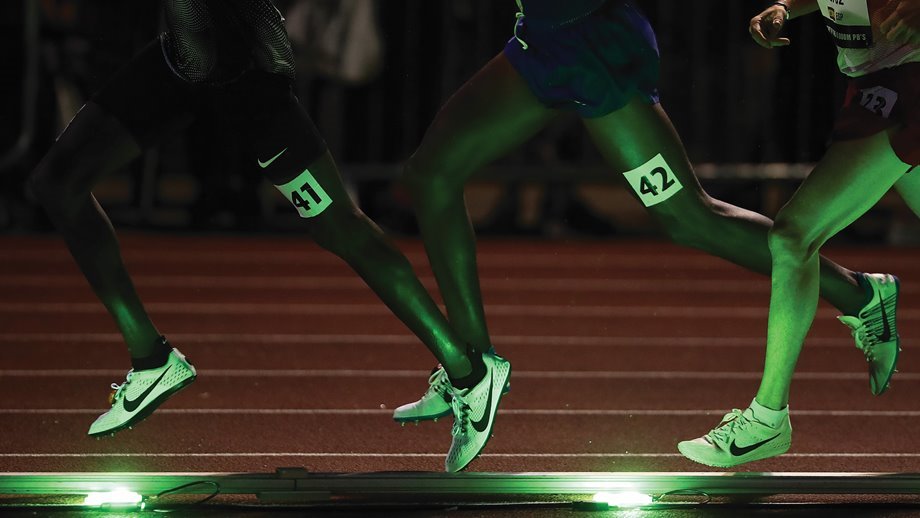
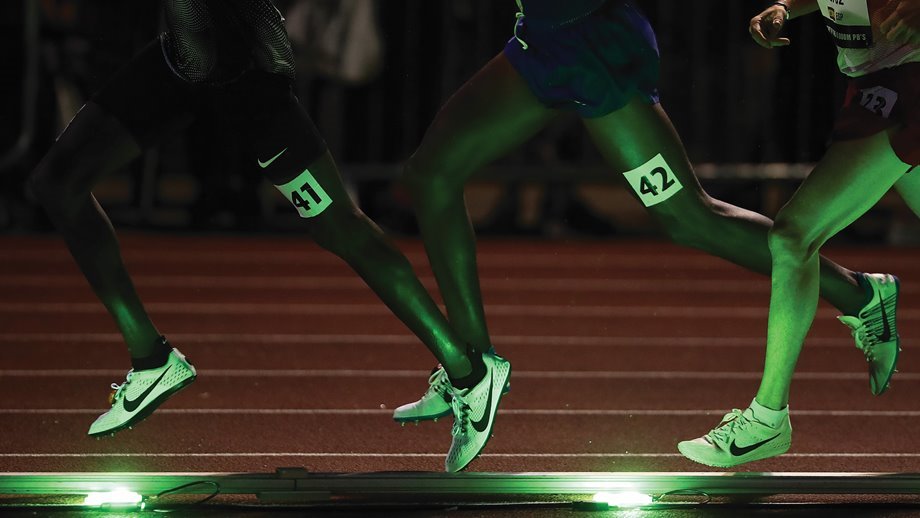
It takes more than extreme training to push the human body to its limits. 3D printing, CFD, engineered precision, and flashing lights are helping today’s Olympic athletes break new records.
There’s an old movie trope about the sharpshooter who can not only hit the bullseye every time but can put one bullet in the hole made by the previous shot. In fiction, that demonstrates the uncanny accuracy of the sharpshooter. At the Olympics, that might not even get you onto the medals podium.
The Olympic air rifle competition turns shooters armed with high tech pellet guns on a target about the width of a hand some 10 meters distant. In the center of the target is a dot 0.5 mm across—not much bigger than the period at the end of this sentence, and the goal is to hit that dot while standing without the benefit of a telescope site. This summer in Paris, the Olympic champion in air rifle will likely hit the dot, known as the 10 ring, repeatedly.
The Olympics are concerned with human achievement, pushing athletes to go faster, higher, and stronger. People have been running, throwing, jumping, and wrestling for Olympic glory since the Greeks started hosting them in the 700s B.C. And they’ve been rowing, shooting, fencing, and cycling since the birth of the modern Olympics in 1896. In all that time, however, athletes continue to set new records, surpassing what was considered the ultimate human potential just a few years prior.
Some of that, no doubt, is due to better training, better understanding of nutrition, and, who knows, maybe a little evolution. But there’s another force helping human bodies reach their max potential, and that’s technology. Rowers benefit from lighter boats, cyclists ride bespoke bikes, and the shooters placing pellets on top of pellets are handling more accurate rifles. Even the most stripped-down event of them all—running—features athletes trained with an engineered pacer to gain their serious advantage.
Behind the scenes engineering is pushing athletes further than they’ve ever gone.
While racing bikes can be tailored for the individual athlete, doing so is a long and expensive affair. Unless you use 3D printing.
Toot Engineering, a sports equipment manufacturer in Montichiari, Italy, has turned to additive manufacturing to develop bicycles fitted to the specific needs of specific riders. The resulting bike has an architecture that wouldn’t be possible otherwise.
The company’s bespoke bikes have caught the attention of the racing world, and its X23 model is slated to be raced by the Argentinian team in the 2024 Olympics in Paris.
“From a mechanical engineering point of view, it’s an area where you design something, you produce something, and the day after it’s in the field. There is no industry where the loop is so close—it’s incredible,” said Ferdinando Auricchio, a professor of solids and structural mechanics at the University of Pavia and one of the engineers who helped build the X23. “The bicycle is a funny area, because if you look at the bicycle, you look at something that seems extremely simple—and mechanically it is simple. But it’s also a high-end application. You need to be at the border of performance and technology.”
You May Like This: 3D Printing Saved the Life of Horse
The parts of the X23 are printed separately, out of a variety of materials, and then welded and assembled. The frame is made of Scalmalloy, an alloy of scandium, aluminum, and magnesium, while other parts are titanium or steel. The bike would be lighter, to be sure, if it were made of carbon fiber, but the extra weight won’t mean much on the hill-free Olympic track.
“You can, for example, sacrifice up a small part of the weight, but then you can enhance the stiffness, which is more important in this kind of race,” said Gianluca Alaimo, a mechanical engineer at the University of Pavia, who also worked on the bike.
The extra weight is more than made up for by the ability to print cheaply and repeatedly, fine-tuning the shape by millimeters, and measuring vibrations and deformations with each round.
Research Insights for ASME Members: R&D Pulse
“We can print quickly with steel,” Auricchio said. “And we’ve proven that with steel we’re getting much better behavior than other more advanced material. If you give me a machine with a better material, I can do even better.”
The X23 takes advantage of additive manufacturing throughout its structure. Its funky, super-narrow steel handlebars, for instance, are an architecture not easily made with other technologies. After repeated iterations, the Toot team was able to reduce the weight by 25 percent while keeping the same stiffness. More importantly, the handlebars are made to fit the posture, grip, and weight of the racer who will be using them.
To do that, a first prototype is done in plastic, meant only for the bicyclist to try out and offer feedback. Then, once it has been produced in metal, the bike and rider are put in a wind tunnel, and the resultant data is used to further tweak the design, after which it is printed out and tested all over again, a process that takes about 24 hours.
“Let’s say that he tries it out on the field, then gives us feedback. We do new simulations, we 3D print it in metal, and we give it to him. He tells us whether it’s OK or if we should do it a different way,” Auricchio said. “It’s an iterative process.”
Future handlebars might be altered and printed to fit the needs not only of specific racers but of specific courses—a design that might work for a track with only left turns would be different than one for a twisty course.
The X23 had its debut at the UCI Track World Championships in August 2023, and now 16 parts have been approved for use in the 2024 Olympics.
“We’re having fun, and we’re learning a lot,” Auricchio said. “And, you know, they are winning.”
That all changed with the advent of competitive air rifle shooting. The air rifles featured in these competitions are not the Daisy BB gun from childhood, but precision machines designed for accuracy.
“The barrel and action are automatically unlocked at the moment the trigger is released so that they can perform a longitudinal movement relative to the stock,” explained Volker Müller, head of technical distribution at Feinwerkbau, one of the leading air rifle manufacturers. This “compensating movement” makes the action and barrel move to the rear just as an air-forcing piston moves forward. Because the rifle’s center of gravity remains virtually unchanged, the shooter feels next to nil in terms of reaction forces.
The Feinwerkbau air rifle was sold for the first time in 1961. With this advanced rifle in their hands, shooters broke almost every existing record. While manufacturers of air rifles honed their skills, the technology leapt to another level after the sport’s Olympic debut in 1984. The air rifle has evolved several times over since then, becoming a thing of—in the right hands—astonishing accuracy.
Early air rifles were side-cocked and spring operated. That mechanism was soon replaced with pumps, like those seen on BB guns, and it was with such a rifle that Pat Spurgin won the gold for the U.S. in 1984. Eventually the pump was replaced by little CO2 canisters, which gave way to cylinders of air filled from a tank. This allowed for much faster shooting.
But the biggest leap forward had less to do with how the air was compressed than with how the recoil was dampened. In the 1980s Feinwerkbau added a tiny pen-sized chamber to the side of the rifle. Inside it is a little piston that goes backward as the pellet goes forward, cancelling the forces with near perfection. “You don’t feel the ping when the shot goes off,” said Peter Durben, a chemical engineer who was an Olympic air-rifle shooter in the 1980s and 90s and is now the national rifle coach for the U.S. national team. “Sometimes, when you’re in the zone, it shoots and you don’t even know if it went off because you don’t feel it.”
As the guns got better and better, the shooting got better and better, and the scores got better and better—which became a problem. Too many shooters were scoring the same near-perfect scores. To adjust for the new accuracy, the scoring now uses a decimal system where the bullseye—a mere half-millimeter hole—is worth 10.9. Today’s Olympic athletes are now shooting repeatedly into the same hole while standing without any kind of telescopic sight.
In recent years Feinwerkbau has worked with the world’s top shooters to create their 900 series. It offers more fine tuning of the absorber so athletes can better adjust for their personal needs, as well as a revamped trigger with a more optimized force distribution. (It’s also quieter.) The 900 series hit the market in 2023 and will likely bring an even greater precision to the Olympics.
In a race like an Olympics final, there’s no room for a pacer—everyone is running for the gold. And pacers aren’t available for day-to-day training.
“Ten years ago, there was a coach with a whistle, and he said, ‘Okay, when I blow the whistle, you have to speed up a little bit; when I blow it again, you have to slow down,’” said Bram Som, a Dutch middle-distance runner who competed in the 2000 and 2004 Olympics. Som is the founder of the company Wavelight, based in Nijmegen, Netherlands. “And now the whistle has switched to lights.”
More by This Author: How the Running of the Bulls May Aid Evacuations
Wavelight intends to take the guess work out of when a runner should speed up or slow down. In essence, the system is just a strip of lights—400 LEDs spaced a meter apart— installed along the inner edge of a track that can be programmed to go as fast or as slow as a coach or runner wants.
For training purposes, the speed can change throughout the course of a run.
Som said his team needed to optimize the system before it was ready to deploy on outdoor tracks. “Water is our biggest competitor,” Som said. Their first product had 400 connectors, each one an opportunity for moisture to wreak havoc. Now, there are only 15.
Another challenge was getting the lights to go off in perfect timing with the starting gun. “The first year we were starting the system manually,” Som said. Now the lights are triggered by a signal that comes straight from the gun’s trigger.
Career Development Courses from ASME
That means the system can be used in competitions to augment the experience of racing—and watching—events. Approved by the Diamond League, the international professional track and field series, the lights lined the track at a June 2023 meet at Stade Sébastien Charléty in Paris. For each race, a lighted patch circled the track at a pace equivalent to the world record in that event. Giving athletes a visual guide to target worked: Three world records were broken at that one meet. As of now Wavelight has been used by runners to break 12 world records.
“We pitched this as a tool for the spectators, to create a connection between the spectators and the athletes and to get more excitement in the stadium,” Som said. The crowd can watch how runners are faring compared to a standing record that is moving with the runners on the lights. And, when runners are on the track alone to see if they can best a competitor’s previous run, the audience—and the athletes—can see just how close or far they are from doing that.
Wavelights have been installed on some 20-odd tracks so far. Som hopes that eventually one in 10 of the world’s 1,000 or so tracks will be Wavelight equipped. Then maybe he can turn his attentions to creating a version of the Wavelight for bicycling, swimming, skating, and marathons.
But first he has to sell the system to perhaps the biggest player. Though many an Olympic runner is already training with a Wavelight system, it’s not yet clear whether Wavelight will be lighting up the Olympic track at Stade de France.
“We don’t have an agreement yet,” Som said. “We’re still negotiating.”
Seruga had already licensed a plastic design created by American Ted Van Dusen of Composite Engineering. At that time, Olympic boats had a set width. But Seruga knew what might be obvious to every engineer: Long thin things tend to be the fastest in water, or anywhere.
“I gave the order for the Institute of Sports in Poland to measure the hips of all the national teams,” he said. He was hoping to answer one simple question: “How narrow can I make them to satisfy a place for the body but minimize the width to make it an arrow.”
Subsequently Plastex introduced its long skinny plastic boat at the 1997 Canoeing World Championships in Canada. “One year later there was not another wood boat. Only plastics.” The International Canoe Federation changed its rules and since then, narrow boats have been the norm.
But Plastex’s innovations were far from over. Where Seruga had originally created his designs using his intuition, experience, and hands, he was soon using CFD and CNC machines to create more perfect boats. The result was a fine tuning of its existing fleet as well as the creation of an entirely new shape.
Prior to their computer modeling, Seruga and other boat designers had assumed that some 75 to 80 percent of total drag was from friction.
“We tried to make geometries with the lowest water surface possible—but we were at the end of possibilities—you need space for the athlete and the boat length is restricted,” he said. “After several CFD analyses we found out that to reduce the total drag we have to take into account the pressure.” The result is a flatter, more trapezoidal shape with a transom stern.
Now, though, Seruga believes there is once again little chance of finding ways to drastically improve Olympic boats if the rules don’t change again.
“A huge revolution in boat design is almost impossible—you cannot be narrower, you cannot be longer, the surface must be glossy and clean,” he said. “We are almost at the end of possibilities to create better kayaks and canoes according to the rules for boat construction.”
Michael Abrams is a technology writer in Westfield, N.J.
The Olympic air rifle competition turns shooters armed with high tech pellet guns on a target about the width of a hand some 10 meters distant. In the center of the target is a dot 0.5 mm across—not much bigger than the period at the end of this sentence, and the goal is to hit that dot while standing without the benefit of a telescope site. This summer in Paris, the Olympic champion in air rifle will likely hit the dot, known as the 10 ring, repeatedly.
The Olympics are concerned with human achievement, pushing athletes to go faster, higher, and stronger. People have been running, throwing, jumping, and wrestling for Olympic glory since the Greeks started hosting them in the 700s B.C. And they’ve been rowing, shooting, fencing, and cycling since the birth of the modern Olympics in 1896. In all that time, however, athletes continue to set new records, surpassing what was considered the ultimate human potential just a few years prior.
Some of that, no doubt, is due to better training, better understanding of nutrition, and, who knows, maybe a little evolution. But there’s another force helping human bodies reach their max potential, and that’s technology. Rowers benefit from lighter boats, cyclists ride bespoke bikes, and the shooters placing pellets on top of pellets are handling more accurate rifles. Even the most stripped-down event of them all—running—features athletes trained with an engineered pacer to gain their serious advantage.
Behind the scenes engineering is pushing athletes further than they’ve ever gone.
Bicycle, bespoke
One look at an expensive racing bike at the cycling store might lead you to believe there is little more that can be done to provide Olympic cyclists with a technological edge. Most vehicles designed and engineered for speed have extremely aerodynamic shapes to minimize air resistance. No matter how much streamlining you do to a racing bicycle, there will still be a not-very-aerodynamic rider sitting on top. Not only do these non-rigid forms catch air, but no two riders are alike.While racing bikes can be tailored for the individual athlete, doing so is a long and expensive affair. Unless you use 3D printing.
Toot Engineering, a sports equipment manufacturer in Montichiari, Italy, has turned to additive manufacturing to develop bicycles fitted to the specific needs of specific riders. The resulting bike has an architecture that wouldn’t be possible otherwise.
The company’s bespoke bikes have caught the attention of the racing world, and its X23 model is slated to be raced by the Argentinian team in the 2024 Olympics in Paris.
“From a mechanical engineering point of view, it’s an area where you design something, you produce something, and the day after it’s in the field. There is no industry where the loop is so close—it’s incredible,” said Ferdinando Auricchio, a professor of solids and structural mechanics at the University of Pavia and one of the engineers who helped build the X23. “The bicycle is a funny area, because if you look at the bicycle, you look at something that seems extremely simple—and mechanically it is simple. But it’s also a high-end application. You need to be at the border of performance and technology.”
You May Like This: 3D Printing Saved the Life of Horse
The parts of the X23 are printed separately, out of a variety of materials, and then welded and assembled. The frame is made of Scalmalloy, an alloy of scandium, aluminum, and magnesium, while other parts are titanium or steel. The bike would be lighter, to be sure, if it were made of carbon fiber, but the extra weight won’t mean much on the hill-free Olympic track.
“You can, for example, sacrifice up a small part of the weight, but then you can enhance the stiffness, which is more important in this kind of race,” said Gianluca Alaimo, a mechanical engineer at the University of Pavia, who also worked on the bike.
The extra weight is more than made up for by the ability to print cheaply and repeatedly, fine-tuning the shape by millimeters, and measuring vibrations and deformations with each round.
Research Insights for ASME Members: R&D Pulse
“We can print quickly with steel,” Auricchio said. “And we’ve proven that with steel we’re getting much better behavior than other more advanced material. If you give me a machine with a better material, I can do even better.”
The X23 takes advantage of additive manufacturing throughout its structure. Its funky, super-narrow steel handlebars, for instance, are an architecture not easily made with other technologies. After repeated iterations, the Toot team was able to reduce the weight by 25 percent while keeping the same stiffness. More importantly, the handlebars are made to fit the posture, grip, and weight of the racer who will be using them.
To do that, a first prototype is done in plastic, meant only for the bicyclist to try out and offer feedback. Then, once it has been produced in metal, the bike and rider are put in a wind tunnel, and the resultant data is used to further tweak the design, after which it is printed out and tested all over again, a process that takes about 24 hours.
“Let’s say that he tries it out on the field, then gives us feedback. We do new simulations, we 3D print it in metal, and we give it to him. He tells us whether it’s OK or if we should do it a different way,” Auricchio said. “It’s an iterative process.”
Future handlebars might be altered and printed to fit the needs not only of specific racers but of specific courses—a design that might work for a track with only left turns would be different than one for a twisty course.
The X23 had its debut at the UCI Track World Championships in August 2023, and now 16 parts have been approved for use in the 2024 Olympics.
“We’re having fun, and we’re learning a lot,” Auricchio said. “And, you know, they are winning.”
Shooting sharp
Marksmanship has been a feature of the Olympics since its rebirth at the end of the 19th century. However impressive those early shooters, recoil on their rifles limited their accuracy.That all changed with the advent of competitive air rifle shooting. The air rifles featured in these competitions are not the Daisy BB gun from childhood, but precision machines designed for accuracy.
“The barrel and action are automatically unlocked at the moment the trigger is released so that they can perform a longitudinal movement relative to the stock,” explained Volker Müller, head of technical distribution at Feinwerkbau, one of the leading air rifle manufacturers. This “compensating movement” makes the action and barrel move to the rear just as an air-forcing piston moves forward. Because the rifle’s center of gravity remains virtually unchanged, the shooter feels next to nil in terms of reaction forces.
The Feinwerkbau air rifle was sold for the first time in 1961. With this advanced rifle in their hands, shooters broke almost every existing record. While manufacturers of air rifles honed their skills, the technology leapt to another level after the sport’s Olympic debut in 1984. The air rifle has evolved several times over since then, becoming a thing of—in the right hands—astonishing accuracy.
Early air rifles were side-cocked and spring operated. That mechanism was soon replaced with pumps, like those seen on BB guns, and it was with such a rifle that Pat Spurgin won the gold for the U.S. in 1984. Eventually the pump was replaced by little CO2 canisters, which gave way to cylinders of air filled from a tank. This allowed for much faster shooting.
But the biggest leap forward had less to do with how the air was compressed than with how the recoil was dampened. In the 1980s Feinwerkbau added a tiny pen-sized chamber to the side of the rifle. Inside it is a little piston that goes backward as the pellet goes forward, cancelling the forces with near perfection. “You don’t feel the ping when the shot goes off,” said Peter Durben, a chemical engineer who was an Olympic air-rifle shooter in the 1980s and 90s and is now the national rifle coach for the U.S. national team. “Sometimes, when you’re in the zone, it shoots and you don’t even know if it went off because you don’t feel it.”
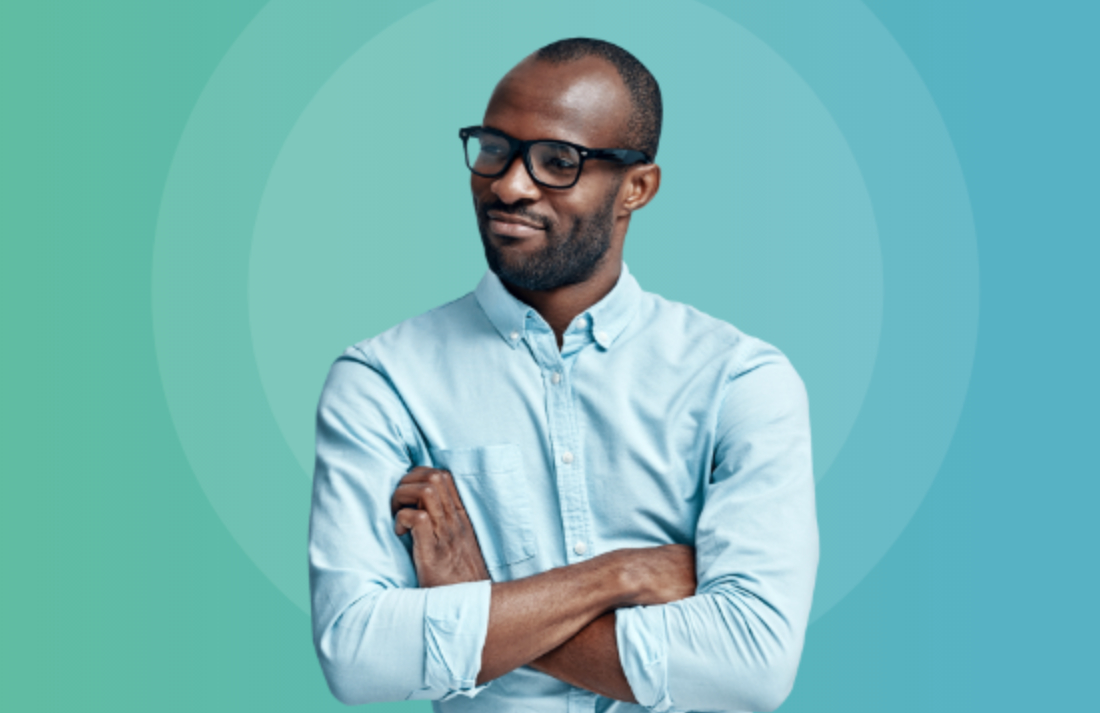
Discover the Benefits
Whether you’re an experienced professional or just starting your career, ASME’s membership community, resources and tools can help you with your lifelong journey.
In recent years Feinwerkbau has worked with the world’s top shooters to create their 900 series. It offers more fine tuning of the absorber so athletes can better adjust for their personal needs, as well as a revamped trigger with a more optimized force distribution. (It’s also quieter.) The 900 series hit the market in 2023 and will likely bring an even greater precision to the Olympics.
Set the pace
For top-flight middle-distance runners, the key to success isn’t running flat out for 1,500 meters. Instead, there is a pace for the first part of the race that’s fast but sustainable, leaving enough energy for a push toward the finish line. Some race organizers employ runners who act as pacers to run the optimal speed before veering off to allow the stars a clear shot at a record.In a race like an Olympics final, there’s no room for a pacer—everyone is running for the gold. And pacers aren’t available for day-to-day training.
“Ten years ago, there was a coach with a whistle, and he said, ‘Okay, when I blow the whistle, you have to speed up a little bit; when I blow it again, you have to slow down,’” said Bram Som, a Dutch middle-distance runner who competed in the 2000 and 2004 Olympics. Som is the founder of the company Wavelight, based in Nijmegen, Netherlands. “And now the whistle has switched to lights.”
More by This Author: How the Running of the Bulls May Aid Evacuations
Wavelight intends to take the guess work out of when a runner should speed up or slow down. In essence, the system is just a strip of lights—400 LEDs spaced a meter apart— installed along the inner edge of a track that can be programmed to go as fast or as slow as a coach or runner wants.
For training purposes, the speed can change throughout the course of a run.
Som said his team needed to optimize the system before it was ready to deploy on outdoor tracks. “Water is our biggest competitor,” Som said. Their first product had 400 connectors, each one an opportunity for moisture to wreak havoc. Now, there are only 15.
Another challenge was getting the lights to go off in perfect timing with the starting gun. “The first year we were starting the system manually,” Som said. Now the lights are triggered by a signal that comes straight from the gun’s trigger.
Career Development Courses from ASME
That means the system can be used in competitions to augment the experience of racing—and watching—events. Approved by the Diamond League, the international professional track and field series, the lights lined the track at a June 2023 meet at Stade Sébastien Charléty in Paris. For each race, a lighted patch circled the track at a pace equivalent to the world record in that event. Giving athletes a visual guide to target worked: Three world records were broken at that one meet. As of now Wavelight has been used by runners to break 12 world records.
“We pitched this as a tool for the spectators, to create a connection between the spectators and the athletes and to get more excitement in the stadium,” Som said. The crowd can watch how runners are faring compared to a standing record that is moving with the runners on the lights. And, when runners are on the track alone to see if they can best a competitor’s previous run, the audience—and the athletes—can see just how close or far they are from doing that.
Wavelights have been installed on some 20-odd tracks so far. Som hopes that eventually one in 10 of the world’s 1,000 or so tracks will be Wavelight equipped. Then maybe he can turn his attentions to creating a version of the Wavelight for bicycling, swimming, skating, and marathons.
But first he has to sell the system to perhaps the biggest player. Though many an Olympic runner is already training with a Wavelight system, it’s not yet clear whether Wavelight will be lighting up the Olympic track at Stade de France.
“We don’t have an agreement yet,” Som said. “We’re still negotiating.”
Canoe like an arrow
Canoeing has been an Olympic sport since 1936, and for more than 60 years, the material of choice for constructing these competition canoes was wood. It wasn’t until the 1990s that Richard Seruga, a slalom canoe paddler who competed for Poland in the 1972 Olympics in Munich, changed all that with his company Plastex.Seruga had already licensed a plastic design created by American Ted Van Dusen of Composite Engineering. At that time, Olympic boats had a set width. But Seruga knew what might be obvious to every engineer: Long thin things tend to be the fastest in water, or anywhere.
“I gave the order for the Institute of Sports in Poland to measure the hips of all the national teams,” he said. He was hoping to answer one simple question: “How narrow can I make them to satisfy a place for the body but minimize the width to make it an arrow.”
Subsequently Plastex introduced its long skinny plastic boat at the 1997 Canoeing World Championships in Canada. “One year later there was not another wood boat. Only plastics.” The International Canoe Federation changed its rules and since then, narrow boats have been the norm.
But Plastex’s innovations were far from over. Where Seruga had originally created his designs using his intuition, experience, and hands, he was soon using CFD and CNC machines to create more perfect boats. The result was a fine tuning of its existing fleet as well as the creation of an entirely new shape.
Prior to their computer modeling, Seruga and other boat designers had assumed that some 75 to 80 percent of total drag was from friction.
“We tried to make geometries with the lowest water surface possible—but we were at the end of possibilities—you need space for the athlete and the boat length is restricted,” he said. “After several CFD analyses we found out that to reduce the total drag we have to take into account the pressure.” The result is a flatter, more trapezoidal shape with a transom stern.
Now, though, Seruga believes there is once again little chance of finding ways to drastically improve Olympic boats if the rules don’t change again.
“A huge revolution in boat design is almost impossible—you cannot be narrower, you cannot be longer, the surface must be glossy and clean,” he said. “We are almost at the end of possibilities to create better kayaks and canoes according to the rules for boat construction.”
Michael Abrams is a technology writer in Westfield, N.J.