Graphene Additive to Cut Concrete Emissions
Graphene Additive to Cut Concrete Emissions
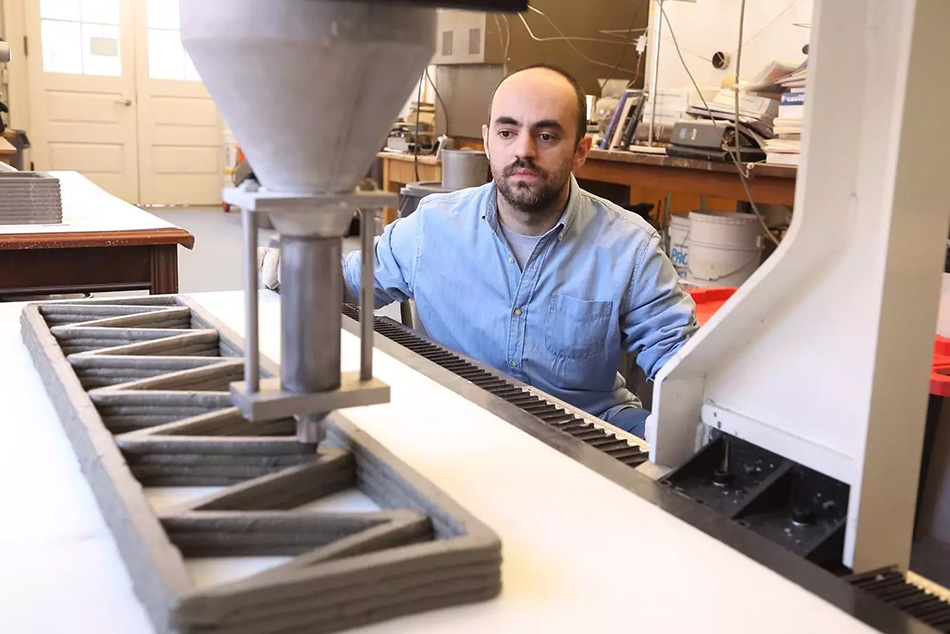
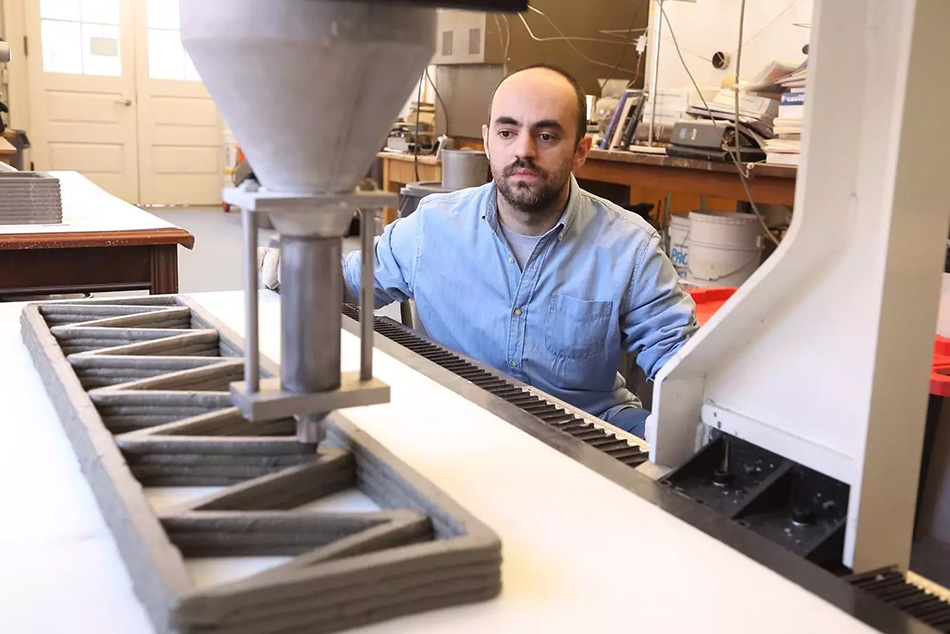
Swapping cement for a mixture of calcined clay and a 3D-printed graphene additive has unlocked a greener concrete option.
As part of an effort to cut concrete’s carbon and greenhouse gas emissions, while preserving the material’s mechanical properties and durability, University of Virginia researchers are exploring how graphene can be used as a 3D-printed concrete additive.
According to the World Economic Forum, cement manufacturing worldwide generated 1.6 billion metric tons of carbon dioxide (CO2) in 2022, representing about 8 percent of total global CO2 emissions. With cement being a vital component to make concrete and global concrete production expected to grow from 14 billion cubic meters in 2024 to 20 billion cubic meters by 2050, the amount of CO2 generated by the sector could reach as high as 3.8 billion tons per year, the WEF concluded.
Concrete combines cement, water, aggregate (sand, crushed stone, gravel), and additives to influence curing time, strength, and color. Recipes varied based on application—larger aggregates increase strength but create rough finishes and perform poorly in concrete printers. With 3D-printed concrete, producers rely on fine aggregates such as sand. This shift requires additional cement, which acts as the binder—similar to eggs in baking—to maintain strength.
“Printable concretes typically use more binder, primarily cement, compared to regular concrete. These mixtures usually exclude coarse aggregate, relying instead on fine aggregate, cement, and water. This composition increases binder content, with cement serving as the main contributor to concrete’s CO2 emissions. Finding ways to reduce cement use in printable concrete would significantly benefit sustainability,” explained Osman Ozbulut, professor in the Department of Civil and Environmental Engineering at the University of Virginia.
Calcined clay
Manufacturers can replace a portion of cement with calcined clay, or metakaolin, as a supplementary cementitious material (SCM). They produce it by heating kaolinite, a soft, white clay naturally found in kaolin (China clay). Unlike cement, calcined clay required heating to only 650 °C to 750 °C (1,202 °F to 1,382 °F), rather than 1,400 °C (2,552 °F) for limestone, reducing its climate impact.
“Using calcined clay or other SCMs typically reduced the compressive strength, especially at early ages. We explored adding graphene to recover this strength loss and to create a more sustainable printable concrete with strong mechanical performance,” Ozbulut explained.
Similar Reading: Leading Hard-to-Decarbonize Industries to Zero Emissions
The UVA team used a traditional concrete recipe that contained a low-carbon alternative called Portland limestone cement, but replaced 30 percent of the cement with calcined clay and added small amounts of graphene, explained Zhangfan Jiang, post-doctoral researcher in the Department of Civil and Environmental Engineering at UVA.
Researchers compared the calcined clay concrete with and without graphene, finding a 20-30 percent strength increase in the graphene-enhanced version.
Graphene filled voids and created a denser microstructure that strengthened the concrete. It also acted as a nucleation site, accelerating cement hydration and further improving mechanical performance.
“We added very small amounts of graphene to serve as a filler and produce a more compact microstructure, known as the filler effect, enhancing mechanical performance,” Ozbulut explained. “Graphene also served as a nucleation site for cement hydration, increasing hydrated products and boosting mechanical properties.”
Graphene production
Researchers extracted graphene using a liquid phase exfoliation technique, combining powdered graphite with a solvent. They applied energy through ultrasonication or high shear mixing to separate graphene into nanosheets, then used a centrifuge to isolate the graphene from the solution. This scalable, cost-effective process allowed unused graphite to undergo recycling and reuse while producing high-quality graphene.
Using biodegradable, non-toxic solvents to produce graphene supports sustainability, though ultrasonication or high shear mixing required significant energy and processing time, often lasting several hours.
Discover the Benefits of ASME Membership
“Compared to cement, graphene’s global warming potential and energy demand run high. However, only a small amount of graphene achieves similar stress levels,” explained Jiang. The graphene concrete mix incorporated just 0.05 percent of graphene by cement weight, delivering a 23 percent boost in compressive strength and a 31 percent reduction in environmental impacts.
Cement production
Another factor contributing to cement’s carbon footprint is the mining process to extract limestone, clay, and sand from quarries, followed by the process of crushing and blending the materials, then heating them in rotating kilns to 1,400 °C (2,552 °F). After cooling, that mixture is ground into a fine powder. Kiln fuels generate about 40 percent of cement-related emissions, while the chemical process of heating limestone releases the remaining 60 percent. Heated limestone produces calcium oxide and emits CO2 as a byproduct. While capturing waste heat or using alternative fuels reduced heat-related emissions, process emissions required carbon capture initiatives.
More for You: Next Gen Concrete Warms from Within
Previous efforts to cut concrete’s carbon footprint by reducing cement content weakened concrete’s mechanical properties, including compressive strength, tensile strength, thermal expansion, and curing shrinkage. To offset this, producers often added SCMs like fly ash, a coal byproduct, or slag, a byproduct of metal refining. Fly ash influenced workability and finish, therefore rarely surpassed 35 percent of cement content. Slag, which is finer than cement, created a less durable finish and rarely replaced more than 50 percent of the cement content.
The graphene-enhanced calcined clay 3D-printed concrete is showing potential in housing construction, a common application for 3D printing. The calcined clay also improved durability in chloride-rich marine environments by binding chloride ions at the concrete’s surface, reducing structural deterioration, and protecting against chloride damage, compared to non-calcined clay structures.
Replacing cement with calcined clay and adding minimal graphene offers a sustainable, energy-efficient solution for construction, particularly in marine environments, without sacrificing performance.
Nicole Imeson is an engineer and writer in Calgary, Alberta.
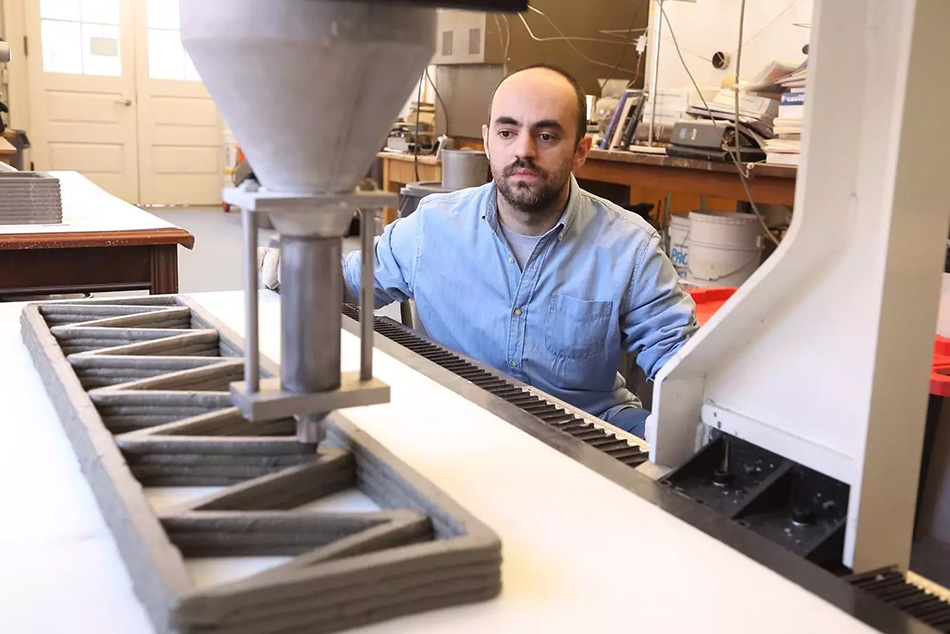
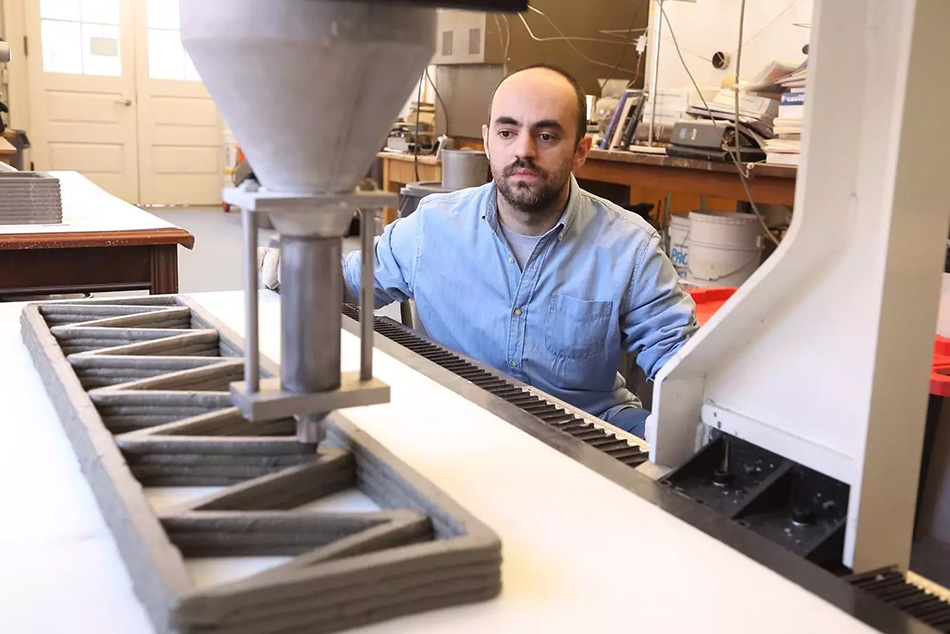