ORNL, VW Succeed in First 270-kW Wireless Power Transfer to EV
ORNL, VW Succeed in First 270-kW Wireless Power Transfer to EV
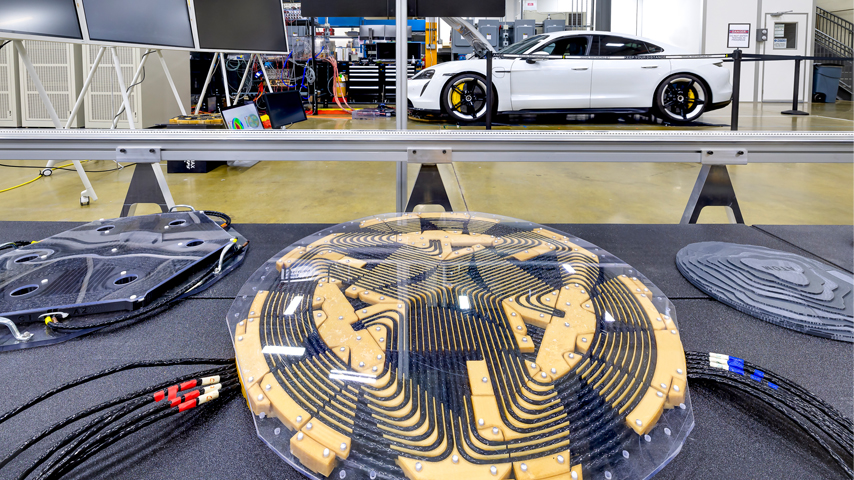
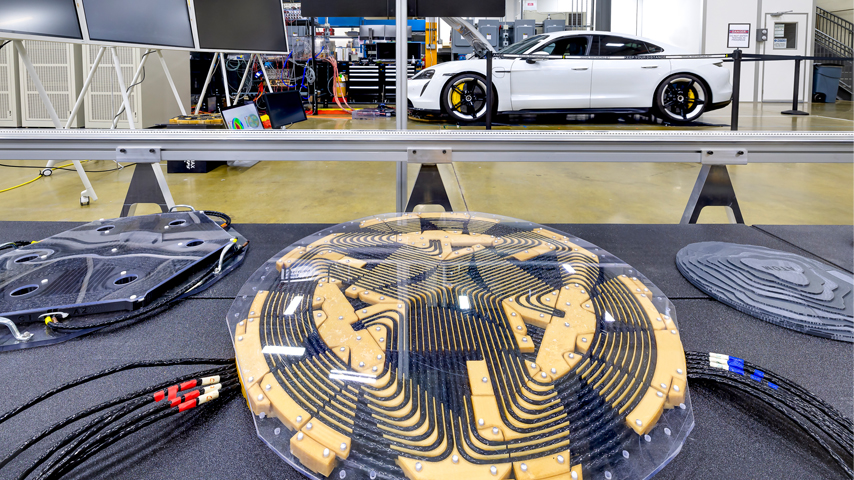
A new polyphase wireless charger for electric vehicles is as efficient as today’s plug-in variety.
Where the advent of the wireless charging of small consumer electronics merely saves us from the inconvenience of having to plug them in, the wireless charging of electric vehicles is a near essential technology for their full integration, and the eventual predominance of self-driving cars.
“When vehicles are so smart that they can do self-driving, self-parking, and can make route planning decisions to save time and fuel, are you going to have to hire someone to plug it in and unplug it?” asked Omer Onar, leader of the Vehicle Power Electronics group at Oak Ridge National Laboratory (ORNL). “In order to fully automate the charging process, you need to have wireless charging.”
To that end, Onar and his colleagues, in collaboration with Volkswagen Group of America, have created a 270-kilowatt wireless power transfer system that has successfully charged a Porsche Taycan.
The breakthrough was a refinement of—and a jump in power from—a similar 120-kilowatt demonstration system they developed for the DOE in 2018. The receiver coil on that version weighed a bit more than 114 pounds, was two inches thick, and more than two-and-a-half feet wide. Because the size and heft of that prototype would be a deal killer for car manufacturers doing everything to keep their vehicles light, the DOE asked Onar and his team to come up with something smaller, sleeker, and more powerful.
You Might Also Like: Wireless Charging for Public Transportation
The coils of existing wireless charging systems pulse power, from zero to peak, across an air gap between the transmitter and the receiver. That means they have a “very low space time utilization of the magnetic field,” Onar said. In other words, they’re limited in power rating, which makes charging a slow process.
To overcome this, the ORNL researchers turned to a coil geometry that energizes three phases to generate rotating magnetic fields. The coils are designed to have three sections, shifting every 120 degrees. Each phase carries about a third of the power. “So, when you sum up those powers at any time from the three phases, you always have constant power transfers delivered from primary to secondary,” Onar explained.
The polyphase geometry also reduced magnetic field emissions. With a single circular coil, the magnetic field lives at the outer edge. With the 120-degree design, it sits at the center, so the system requires no shielding to remain compliant with international guidelines for electromagnetic field emission limits.
Discover the Benefits of ASME Membership
The new charger is not the first attempt to use three phases for power transmission. However, previous versions used three separate coils. When arranged near each other, they had cross-couplings that caused cancelations and ultimately had to be placed too far apart to be practical.
“In our approach, we don’t have that problem,” said Onar. “As long as the spatial angles between phase windings are 90 degrees or larger, they create negative mutual inductance. So instead of canceling, phases will support each other.”
The result is a coil that can charge a car’s battery to 50 percent in 10 minutes. After that, the power has to be turned down, so things charge a bit slower. “You may spend another five minutes or so to push another 20-kilowatt hours or so,” said Onar. “So, in more or less 15 minutes, you can reach a 75 or 80 percent state of charge.” That’s enough to drive two or three hours on the interstate.
There’s an air gap of 4.75 centimeters between the transmitter and receiver coils of the charger—a typical ground clearance in light-duty passenger vehicles. Despite this seemingly large leap, the system is 95 percent efficient—in the same ballpark as the plug-in chargers used today.
Those cabled gas-station-like chargers have to switch first from AC to DC and then, to comply with the national electric code and UL safety standards, the chargers have to be isolated from the grid, which requires high-frequency isolation transformers. All of this knocks the efficiency down to 95 percent.
The two sides of the polyphase wireless chargers, already separated by air, don’t need further isolation from the grid and don’t need the transformers, so they’re only marginally less efficient than plug-in chargers.
Infographic: Charging Technologies for Electric Vehicles
As the percentage of electric vehicles on the road goes up, wireless chargers will make a lot more sense. For half a megawatt plug-in charger to work, the wire sizes have to be massive. To be able to maneuver them to plug in a car may require smaller connectors, which will have to be liquid cooled—a leak from which would be dangerous. Wireless charging doesn’t require any of that.
With the success of their recent demonstrations, the charger is ready to be moved out of the realm of handcrafted prototypes and into mass manufacturing. And there’s not much standing in the way of that happening quickly, according to Onar.
“I don’t see any downsides,” he said. “I think we will get there pretty soon—in just a few years.”
Michael Abrams is a technology writer in Westfield, N.J.
“When vehicles are so smart that they can do self-driving, self-parking, and can make route planning decisions to save time and fuel, are you going to have to hire someone to plug it in and unplug it?” asked Omer Onar, leader of the Vehicle Power Electronics group at Oak Ridge National Laboratory (ORNL). “In order to fully automate the charging process, you need to have wireless charging.”
To that end, Onar and his colleagues, in collaboration with Volkswagen Group of America, have created a 270-kilowatt wireless power transfer system that has successfully charged a Porsche Taycan.
The breakthrough was a refinement of—and a jump in power from—a similar 120-kilowatt demonstration system they developed for the DOE in 2018. The receiver coil on that version weighed a bit more than 114 pounds, was two inches thick, and more than two-and-a-half feet wide. Because the size and heft of that prototype would be a deal killer for car manufacturers doing everything to keep their vehicles light, the DOE asked Onar and his team to come up with something smaller, sleeker, and more powerful.
You Might Also Like: Wireless Charging for Public Transportation
The coils of existing wireless charging systems pulse power, from zero to peak, across an air gap between the transmitter and the receiver. That means they have a “very low space time utilization of the magnetic field,” Onar said. In other words, they’re limited in power rating, which makes charging a slow process.
To overcome this, the ORNL researchers turned to a coil geometry that energizes three phases to generate rotating magnetic fields. The coils are designed to have three sections, shifting every 120 degrees. Each phase carries about a third of the power. “So, when you sum up those powers at any time from the three phases, you always have constant power transfers delivered from primary to secondary,” Onar explained.
The polyphase geometry also reduced magnetic field emissions. With a single circular coil, the magnetic field lives at the outer edge. With the 120-degree design, it sits at the center, so the system requires no shielding to remain compliant with international guidelines for electromagnetic field emission limits.
Discover the Benefits of ASME Membership
The new charger is not the first attempt to use three phases for power transmission. However, previous versions used three separate coils. When arranged near each other, they had cross-couplings that caused cancelations and ultimately had to be placed too far apart to be practical.
“In our approach, we don’t have that problem,” said Onar. “As long as the spatial angles between phase windings are 90 degrees or larger, they create negative mutual inductance. So instead of canceling, phases will support each other.”
The result is a coil that can charge a car’s battery to 50 percent in 10 minutes. After that, the power has to be turned down, so things charge a bit slower. “You may spend another five minutes or so to push another 20-kilowatt hours or so,” said Onar. “So, in more or less 15 minutes, you can reach a 75 or 80 percent state of charge.” That’s enough to drive two or three hours on the interstate.
There’s an air gap of 4.75 centimeters between the transmitter and receiver coils of the charger—a typical ground clearance in light-duty passenger vehicles. Despite this seemingly large leap, the system is 95 percent efficient—in the same ballpark as the plug-in chargers used today.
Those cabled gas-station-like chargers have to switch first from AC to DC and then, to comply with the national electric code and UL safety standards, the chargers have to be isolated from the grid, which requires high-frequency isolation transformers. All of this knocks the efficiency down to 95 percent.
The two sides of the polyphase wireless chargers, already separated by air, don’t need further isolation from the grid and don’t need the transformers, so they’re only marginally less efficient than plug-in chargers.
Infographic: Charging Technologies for Electric Vehicles
As the percentage of electric vehicles on the road goes up, wireless chargers will make a lot more sense. For half a megawatt plug-in charger to work, the wire sizes have to be massive. To be able to maneuver them to plug in a car may require smaller connectors, which will have to be liquid cooled—a leak from which would be dangerous. Wireless charging doesn’t require any of that.
With the success of their recent demonstrations, the charger is ready to be moved out of the realm of handcrafted prototypes and into mass manufacturing. And there’s not much standing in the way of that happening quickly, according to Onar.
“I don’t see any downsides,” he said. “I think we will get there pretty soon—in just a few years.”
Michael Abrams is a technology writer in Westfield, N.J.
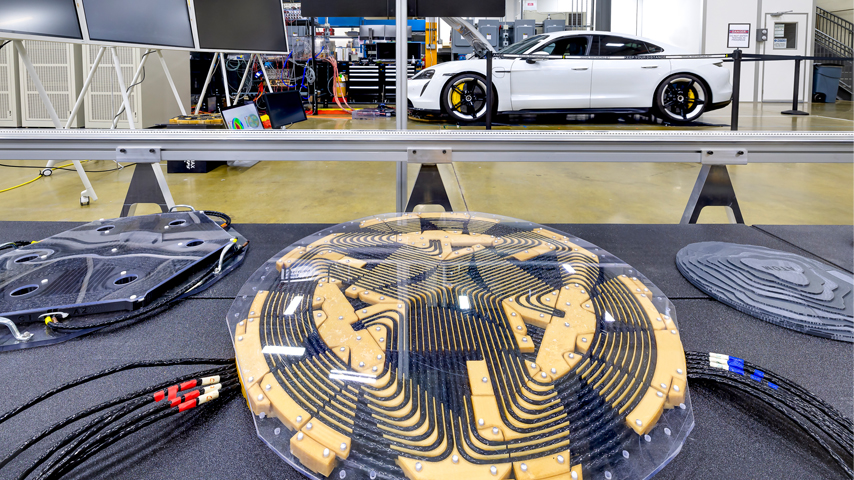
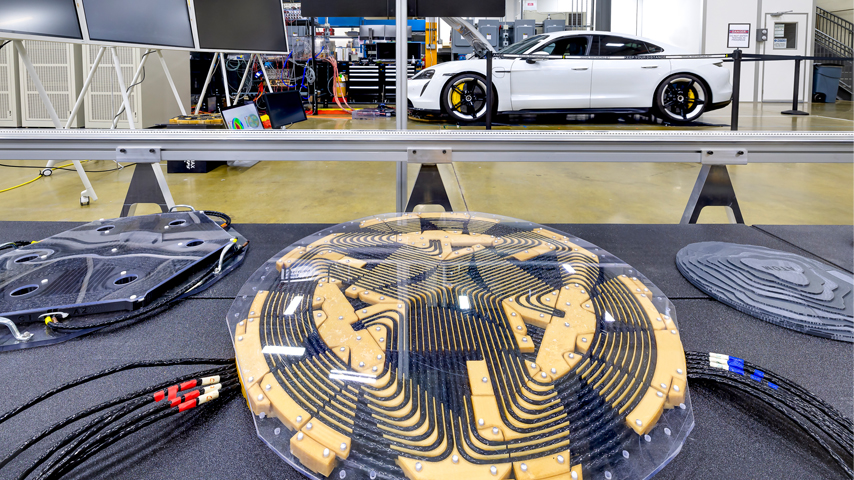