Oxidation Study May Lead to Advanced Alloys
Oxidation Study May Lead to Advanced Alloys
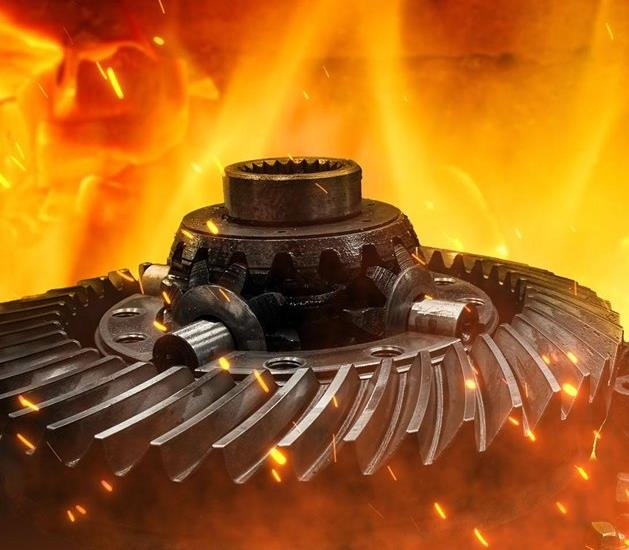
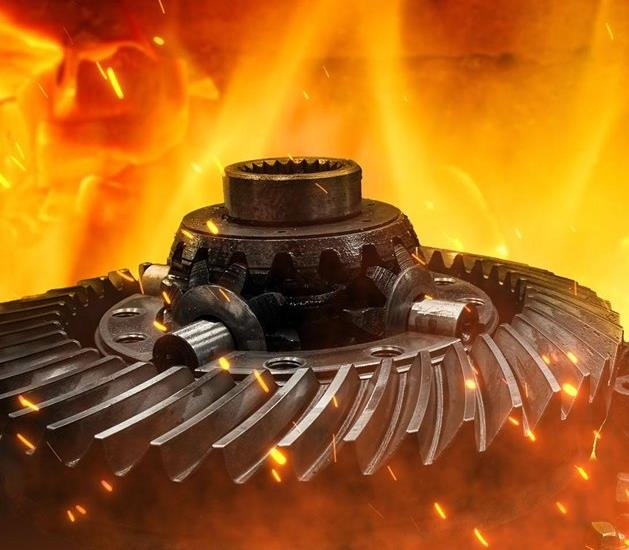
The hope is that a tool developed by researchers may provide the ability for rapid design and testing cycles for oxidation-resistant complex metal alloys.
Alloys such as bronze and electrum date to antiquity. Metallurgists added a small amount of one element to a larger amount of another to improve strength, ductility, or other characteristics. For instance, copper became harder and stronger with the addition of small amounts of tin and other metals, which is why bronze was such a prized material to the ancient Greeks.
“If you add three, four or five elements together, it complicates the microstructure and creates new phases because there are a greater number of interactions between them. But in some cases, researchers found that it was still a very simple looking microstructure,” explained Bharat Gwalani, Assistant Professor of Materials Science and Engineering at North Carolina State University (NCSU) in Raleigh.
The term high entropy alloys—a combination of five or more elements in a metallic composition—emerged from this concept, as the atomic disorder acted to stabilize the structure. Researchers also called them multi-principal-element alloys, and when equal parts of each element combined, they referred to them as equiatomic alloys.
But researchers had limited knowledge about how the material oxidized, which elements contributed to oxidation, and which remained stable under various atmospheric conditions. In a recent study published in Nature Communications, researchers at NCSU and the Department of Energy’s Pacific Northwest National Laboratory (PNNL) sought to answer how materials could be engineered to mitigate oxidation in more extreme environments.
“This study is meant to understand what is fundamentally happening in the very early stages of metal oxidation”, explained Bharat Gwalani, Assistant Professor of Materials Science and Engineering at NCSU.
From their results, the team creates a tool to enable researchers to predict how such high-entropy alloys will behave under high-temperature oxidative environments. The hope is that this tool may provide the ability for rapid design and testing cycles for oxidation-resistant complex metal alloys.
Oxidation on a metallic surface involves a chemical reaction between the metal and oxygen from the environment, forming an oxide layer on the surface of the metal. During this process, the metal loses electrons to the oxygen atoms, creating metal oxides—the reaction of iron and oxygen produces iron oxide, commonly known as rust.
The oxide layer either forms a stable, protective layer preventing further oxidation, as aluminum and chromium, or produces ongoing corrosion and the formation of oxide scales.
Changes in temperature, moisture content, and pressure helps speed up the reaction rates.
“When you take a material to higher temperatures, the oxide scales should remain stable and break or grow. They grow because the oxide reaction is energetically favorable, but we have to prevent it,” Gwalani said.
The research team began with a five-element equiatomic alloy composed of cobalt, chromium, iron, nickel, and manganese. After oxidizing the material for one hour at 400 °C, they discovered multiple stages of oxidation within that short timeframe.
To understand each phase individually and how the oxidation progressed, they used in-situ atom probe tomography to analyze each layer. They prepared a sharp needle specimen and field evaporated it into an analysis chamber to detect the elements in the sample. By analyzing samples at 2 minutes, 5 minutes, 30 minutes, 60 minutes, and 120 minutes they captured early stages of oxidation and identified the different layers formed by each element within the alloy.
They found that the fast-oxidizing element chromium controlled early oxidation, stabilizing to create the inner oxide layer, while the slower-oxidizing elements manganese, iron, and cobalt diffused outward and dominated the outer layer. Nickel maintained crystalline stability of the base alloy, forming a layer beneath the oxidation.
Martin Thuro and Andrew Martin at North Carolina State University’s Department of Materials Science and Engineering developed the preferential interactivity parameter (PIP), which PNNL and NCSU researchers applied to evaluate cohesive energy density, electronegativity, and atomic radius. While Ellingham focuses on fundamental equilibrium using Gibbs free energy as a single parameter, PIP utilizes multiple parameters to realistically assess elements' oxidation tendencies in diverse environments.
With limited research on oxidation in complex alloys, researchers input elements and parameters into the PIP chart. This provided outputs and expectations for in-situ atom probe tomography. Subsequently, they compared in-situ atom probe tomography results to PIP outputs and identified a correlation between the two.
The research team's next step involved developing gradient alloys, which comprised a single assembly with varying concentrations of an element from one end of the structure to the other. This approach enabled the team to assess the formation of oxide scales at different element concentrations within a single build, eliminating the need to construct multiple alloys with varying concentrations.
Researchers aim to provide “a new template to design microstructures that can fill in the gaps between room temperature to high temperature properties and between cheaper to expensive material to create cheaper and stronger materials for higher temperature applications,” Gwalani said.
Research on equiatomic alloys at PNNL and NCSU uncovered new insights into the oxidation behavior of high entropy alloys. The research team's promising findings pave the way for further studies on gradient alloys, potentially enhancing the understanding and engineering of oxidation-resistant materials.
Nicole Imeson is a technology writer in Calgary, Alta.
“If you add three, four or five elements together, it complicates the microstructure and creates new phases because there are a greater number of interactions between them. But in some cases, researchers found that it was still a very simple looking microstructure,” explained Bharat Gwalani, Assistant Professor of Materials Science and Engineering at North Carolina State University (NCSU) in Raleigh.
The term high entropy alloys—a combination of five or more elements in a metallic composition—emerged from this concept, as the atomic disorder acted to stabilize the structure. Researchers also called them multi-principal-element alloys, and when equal parts of each element combined, they referred to them as equiatomic alloys.
But researchers had limited knowledge about how the material oxidized, which elements contributed to oxidation, and which remained stable under various atmospheric conditions. In a recent study published in Nature Communications, researchers at NCSU and the Department of Energy’s Pacific Northwest National Laboratory (PNNL) sought to answer how materials could be engineered to mitigate oxidation in more extreme environments.
“This study is meant to understand what is fundamentally happening in the very early stages of metal oxidation”, explained Bharat Gwalani, Assistant Professor of Materials Science and Engineering at NCSU.
From their results, the team creates a tool to enable researchers to predict how such high-entropy alloys will behave under high-temperature oxidative environments. The hope is that this tool may provide the ability for rapid design and testing cycles for oxidation-resistant complex metal alloys.
Oxidation on a metallic surface involves a chemical reaction between the metal and oxygen from the environment, forming an oxide layer on the surface of the metal. During this process, the metal loses electrons to the oxygen atoms, creating metal oxides—the reaction of iron and oxygen produces iron oxide, commonly known as rust.
The oxide layer either forms a stable, protective layer preventing further oxidation, as aluminum and chromium, or produces ongoing corrosion and the formation of oxide scales.
Changes in temperature, moisture content, and pressure helps speed up the reaction rates.
“When you take a material to higher temperatures, the oxide scales should remain stable and break or grow. They grow because the oxide reaction is energetically favorable, but we have to prevent it,” Gwalani said.
The research team began with a five-element equiatomic alloy composed of cobalt, chromium, iron, nickel, and manganese. After oxidizing the material for one hour at 400 °C, they discovered multiple stages of oxidation within that short timeframe.
To understand each phase individually and how the oxidation progressed, they used in-situ atom probe tomography to analyze each layer. They prepared a sharp needle specimen and field evaporated it into an analysis chamber to detect the elements in the sample. By analyzing samples at 2 minutes, 5 minutes, 30 minutes, 60 minutes, and 120 minutes they captured early stages of oxidation and identified the different layers formed by each element within the alloy.
They found that the fast-oxidizing element chromium controlled early oxidation, stabilizing to create the inner oxide layer, while the slower-oxidizing elements manganese, iron, and cobalt diffused outward and dominated the outer layer. Nickel maintained crystalline stability of the base alloy, forming a layer beneath the oxidation.
Analytical tools
Metallurgists have referenced the Ellingham diagram since its inception in 1944 to understand the relationship between temperature, metal, oxide, and oxygen, as well as how elements react with each other. The diagram uses Gibbs free energy — the thermodynamic potential of an element at constant temperature and pressure — to chart the oxidation potential as a function of temperature. Despite its usefulness, the Ellingham diagram only considers one parameter when evaluating elements.Martin Thuro and Andrew Martin at North Carolina State University’s Department of Materials Science and Engineering developed the preferential interactivity parameter (PIP), which PNNL and NCSU researchers applied to evaluate cohesive energy density, electronegativity, and atomic radius. While Ellingham focuses on fundamental equilibrium using Gibbs free energy as a single parameter, PIP utilizes multiple parameters to realistically assess elements' oxidation tendencies in diverse environments.
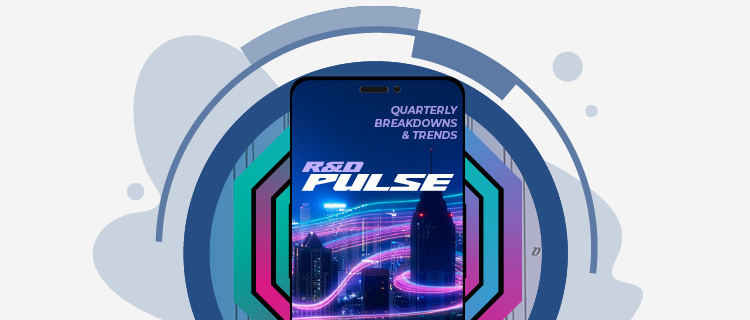
With limited research on oxidation in complex alloys, researchers input elements and parameters into the PIP chart. This provided outputs and expectations for in-situ atom probe tomography. Subsequently, they compared in-situ atom probe tomography results to PIP outputs and identified a correlation between the two.
The research team's next step involved developing gradient alloys, which comprised a single assembly with varying concentrations of an element from one end of the structure to the other. This approach enabled the team to assess the formation of oxide scales at different element concentrations within a single build, eliminating the need to construct multiple alloys with varying concentrations.
Researchers aim to provide “a new template to design microstructures that can fill in the gaps between room temperature to high temperature properties and between cheaper to expensive material to create cheaper and stronger materials for higher temperature applications,” Gwalani said.
Research on equiatomic alloys at PNNL and NCSU uncovered new insights into the oxidation behavior of high entropy alloys. The research team's promising findings pave the way for further studies on gradient alloys, potentially enhancing the understanding and engineering of oxidation-resistant materials.
Nicole Imeson is a technology writer in Calgary, Alta.
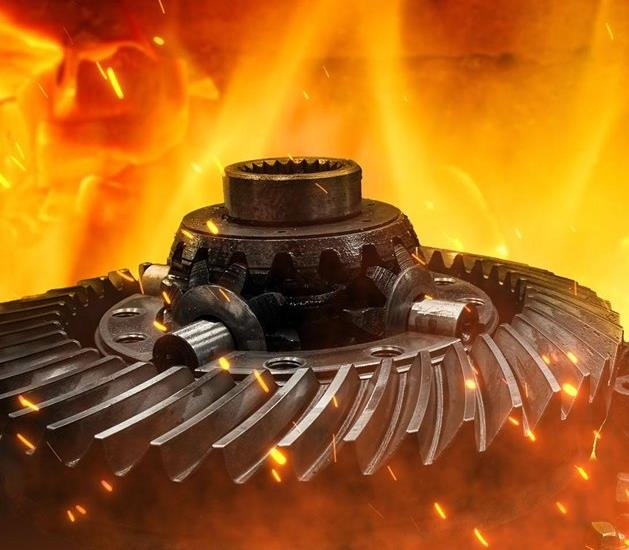
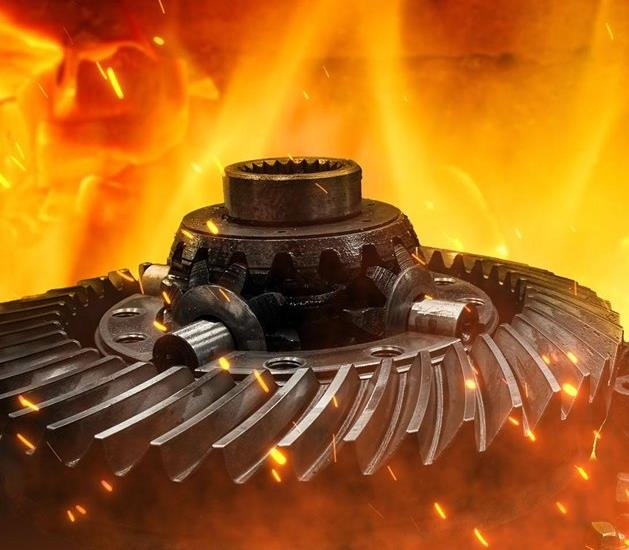