Robot Assistance that Starts at the Knees
Robot Assistance that Starts at the Knees
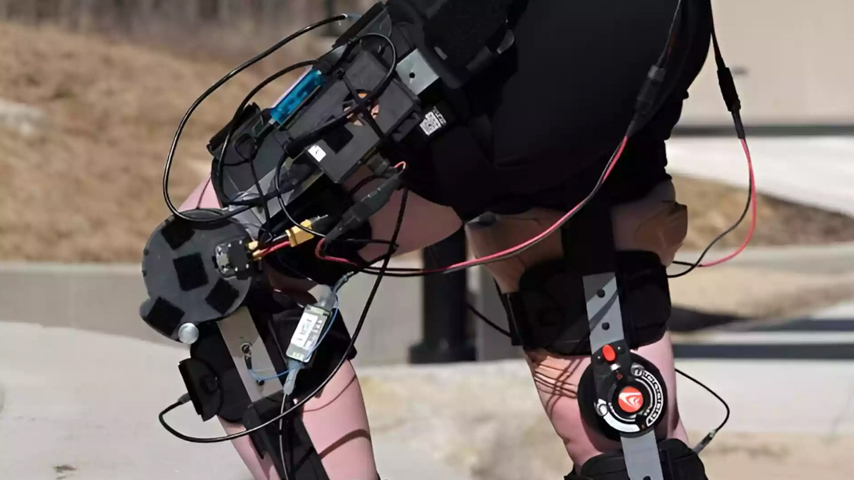
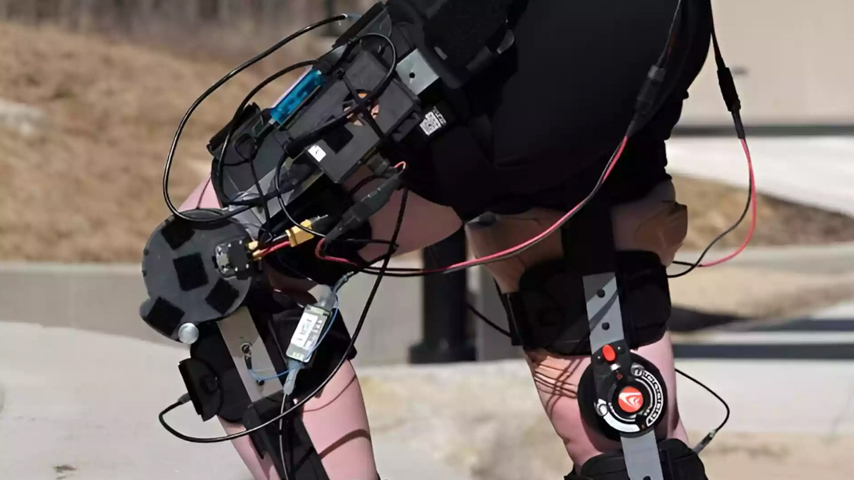
Researchers at the University of Michigan have developed a new kind of exoskeleton to better support lifting and carrying.
The World Health Organization lists lower back pain as the leading cause of disability worldwide – and that disability often starts with a strain to the lower back from repetitively lifting or carrying heavy objects. A variety of belts and braces on the market promise to prevent back injury, but there are mixed results on how much help they provide.
Now, Robert Gregg’s robotics laboratory at the University of Michigan has created a unique knee exoskeleton to provide an important assist – helping people lift safely from the legs even when fatigued.
Many robotic exoskeleton development programs have been geared toward helping individuals with injuries or impairments regain strength or mobility. But Gregg said such systems also have great potential to augment the physical performance of healthy people to prevent injuries from occurring in the first place.
“It’s very common for people who work in physically demanding workplaces, including construction sites, warehouses, and assembly lines, to engage in repetitive lowering and carrying activities, which can lead to injuries,” he said. “But with the right support, we can protect the back.”
While some have proposed some kind of back support to keep the spine in alignment, Gregg and colleagues focused on the knee. The group created an exoskeleton using commercially available knee braces and drone motors in order to support the quadriceps muscles, which, when taking on the bulk of force in a lift, can better protect the lower back. The exoskeleton, in effect, ensures the body will follow the old adage to “lift with your legs.”
“It had to be what we call back drivable, which is a technical term,” he said. “The idea is that the motor isn’t always controlling the position of the human joint. In fact, it’s preferable that humans have voluntary control of their limbs, the electric motor should only be providing assistive torque.”
To achieve this, the researchers leveraged a high torque, low speed drone motor and a specially designed generalized machine learning algorithm that uses feedback from sensors on the device to tell the motor when to generate torques that assist and rather than hinder the intended action.
More like this: Exoskeleton Boot Improves Walking Speed
“The way we created the algorithm is through a combination of physics-based models of human limbs and lots of normative data,” Gregg said. “We took a lot of motion capture of unimpaired individuals performing primary activities of daily life including lifting, lowering, ascending and descending walking. That combination enables the exoskeleton to essentially infer the corrective assistive torque from the information it gets from the sensors, which is a fraction of their biological torque as they are engaging in activities in real time.”
In addition, participants did not feel encumbered by the device. When queried about the exoskeleton, participants reported they were quite satisfied or very satisfied with it, with the exception of using it to walk on level ground.
For you: Exoskeleton Control Improved Through Machine Learning
The research team has applied for a patent for the device and hopes to continue refining the design with the goal of eventually bringing it to market.
“We would like to find a commercial partner to provide the kind of hardware expertise to miniaturize all the electronics and integrate the mechanical systems with the electrical systems to make it more compact,” Gregg said. “We’d also like to find industry partners who might want to deploy this in their workplaces. You could imagine a company with a large logistics operation might want to give this technology a try to see whether it reduces fatigue and improves performance in their workers.”
But, in the meantime, Gregg said that he hopes other researchers consider developing new robotics systems to help provide assistance for all people.
“We can use effective exoskeleton designs that help both unimpaired and impaired people,” he said. “But they need to be designed to be highly back drivable, both in terms of the hardware and the control systems that augment and enhance voluntary motion. There are so many different ways to design exoskeletons – it’s a little bit like the Wild West out there right now – but I hope our work provides some insights on how we can better produce effective outcomes, including on muscle effort and the effects of fatigue, to reduce the risk of injury.”
Kayt Sukel is a technology and business writer in Houston.
Now, Robert Gregg’s robotics laboratory at the University of Michigan has created a unique knee exoskeleton to provide an important assist – helping people lift safely from the legs even when fatigued.
Many robotic exoskeleton development programs have been geared toward helping individuals with injuries or impairments regain strength or mobility. But Gregg said such systems also have great potential to augment the physical performance of healthy people to prevent injuries from occurring in the first place.
“It’s very common for people who work in physically demanding workplaces, including construction sites, warehouses, and assembly lines, to engage in repetitive lowering and carrying activities, which can lead to injuries,” he said. “But with the right support, we can protect the back.”
While some have proposed some kind of back support to keep the spine in alignment, Gregg and colleagues focused on the knee. The group created an exoskeleton using commercially available knee braces and drone motors in order to support the quadriceps muscles, which, when taking on the bulk of force in a lift, can better protect the lower back. The exoskeleton, in effect, ensures the body will follow the old adage to “lift with your legs.”
High torque
Gregg said the team was challenged to come up with a design that would be lightweight, comfortable, and work with the natural movement of the knee.“It had to be what we call back drivable, which is a technical term,” he said. “The idea is that the motor isn’t always controlling the position of the human joint. In fact, it’s preferable that humans have voluntary control of their limbs, the electric motor should only be providing assistive torque.”
To achieve this, the researchers leveraged a high torque, low speed drone motor and a specially designed generalized machine learning algorithm that uses feedback from sensors on the device to tell the motor when to generate torques that assist and rather than hinder the intended action.
More like this: Exoskeleton Boot Improves Walking Speed
“The way we created the algorithm is through a combination of physics-based models of human limbs and lots of normative data,” Gregg said. “We took a lot of motion capture of unimpaired individuals performing primary activities of daily life including lifting, lowering, ascending and descending walking. That combination enables the exoskeleton to essentially infer the corrective assistive torque from the information it gets from the sensors, which is a fraction of their biological torque as they are engaging in activities in real time.”
Keeping pace
When the group experimentally tested the device, asking study participants to perform a variety of lifting and carrying tasks with a 20-pound kettlebell, they discovered that the exoskeleton not only helped people maintain proper posture – even as they grew more tired during the repetitive tasks – but helped them keep pace, which is important for those working on an assembly line or factory environment. Participants wearing the exoskeleton only slowed down 1 percent from their starting pace, compared to a 44 percent slowdown when they performed the task without an exoskeleton assist.In addition, participants did not feel encumbered by the device. When queried about the exoskeleton, participants reported they were quite satisfied or very satisfied with it, with the exception of using it to walk on level ground.
For you: Exoskeleton Control Improved Through Machine Learning
The research team has applied for a patent for the device and hopes to continue refining the design with the goal of eventually bringing it to market.
“We would like to find a commercial partner to provide the kind of hardware expertise to miniaturize all the electronics and integrate the mechanical systems with the electrical systems to make it more compact,” Gregg said. “We’d also like to find industry partners who might want to deploy this in their workplaces. You could imagine a company with a large logistics operation might want to give this technology a try to see whether it reduces fatigue and improves performance in their workers.”
But, in the meantime, Gregg said that he hopes other researchers consider developing new robotics systems to help provide assistance for all people.
“We can use effective exoskeleton designs that help both unimpaired and impaired people,” he said. “But they need to be designed to be highly back drivable, both in terms of the hardware and the control systems that augment and enhance voluntary motion. There are so many different ways to design exoskeletons – it’s a little bit like the Wild West out there right now – but I hope our work provides some insights on how we can better produce effective outcomes, including on muscle effort and the effects of fatigue, to reduce the risk of injury.”
Kayt Sukel is a technology and business writer in Houston.
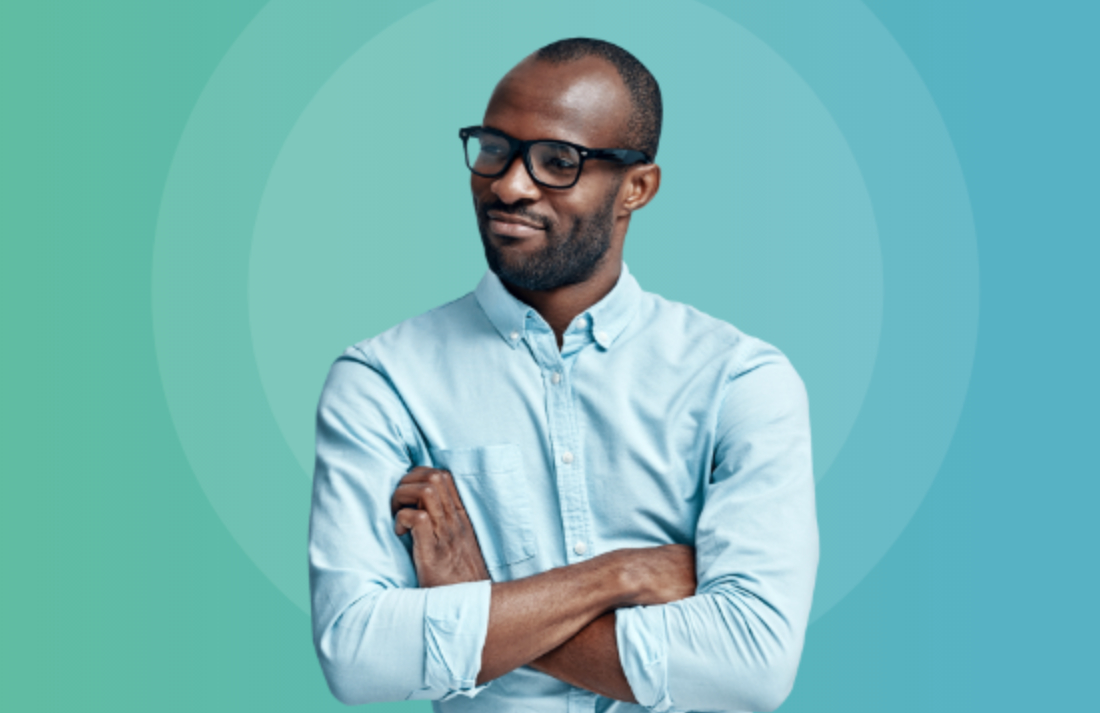
Start the New Year as a Member
Whether you’re an experienced professional or just starting your career, ASME’s membership community, resources and tools can help you with your lifelong journey.
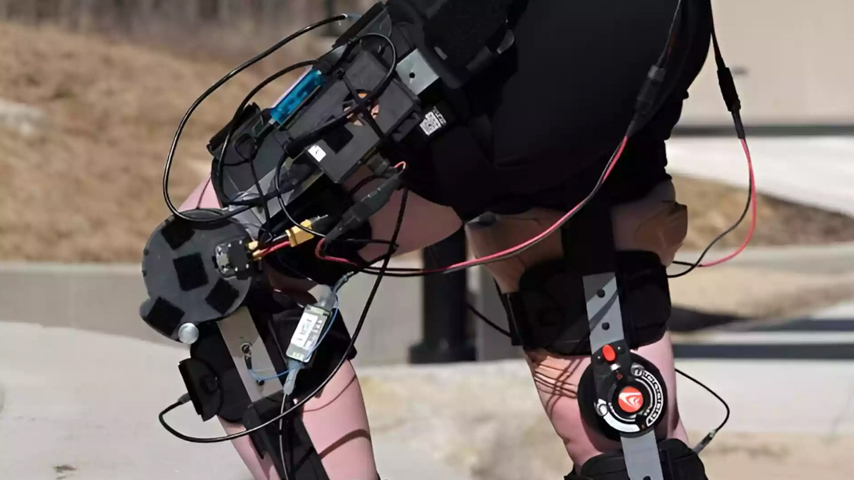
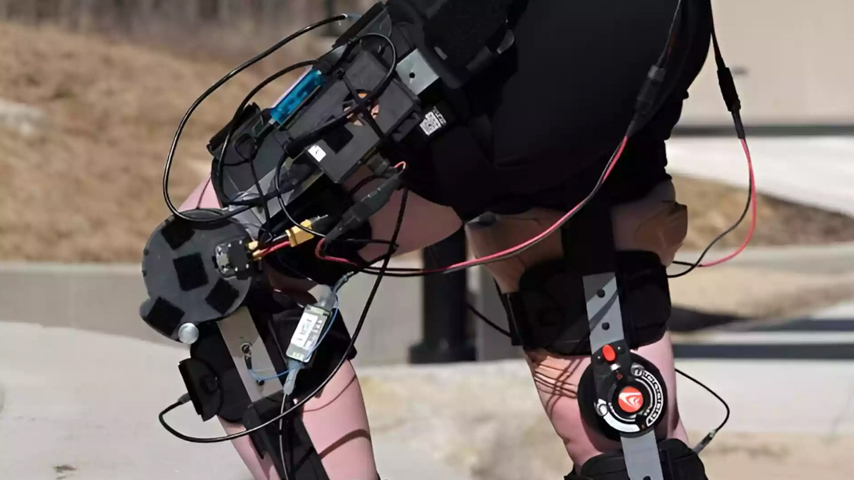