Students Improve Army Grappling Hook
Students Improve Army Grappling Hook
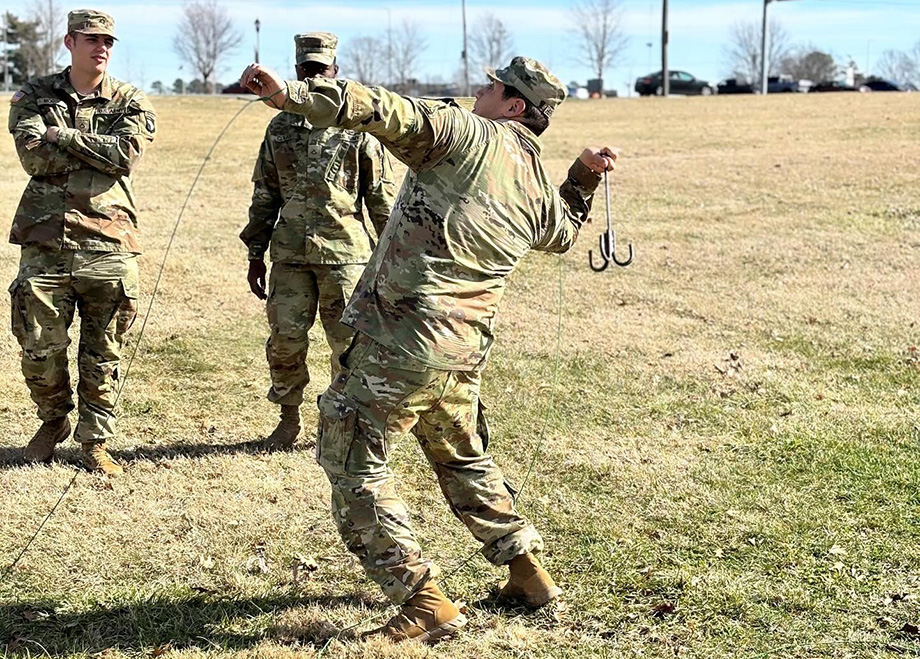
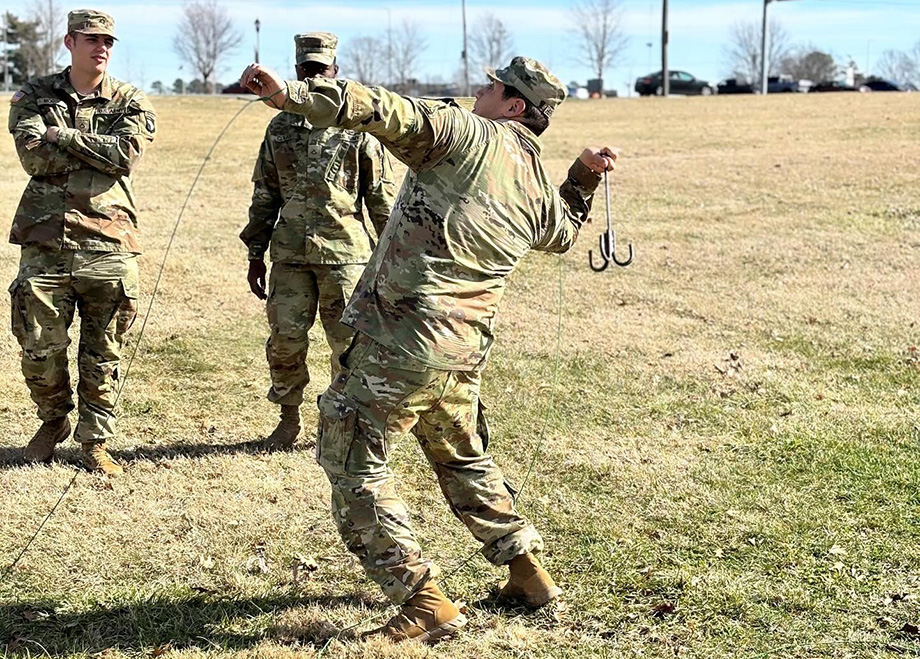
In collaboration with soldiers from Fort Campbell, engineering students developed a new design that doesn’t leave troops exposed to enemy fire.
A team of Vanderbilt University students has taken on a challenge posed by the U.S. Army: reimagining the humble grappling hook. This project is just the latest that has come from a partnership between university and Fort Campbell, which is about 60 miles from Vanderbilt’s Nashville campus.
Kevin Galloway, a research associate professor at Vanderbilt’s School of Engineering, said the collaboration began in 2018.
“I met Col. John Cogbill, now a Brigadier General, and he said he wanted to create an innovation ecosystem within the Third Brigade,” Galloway said. “One of the things soldiers wanted to learn more about was additive manufacturing, so the General challenged his combat team to pitch ideas of how they thought additive manufacturing could support operational readiness. No idea was a bad idea.”
Since then, the partnership has fostered soldier-informed innovation through a number of different projects, including an excavator tool that makes digging hasty fighting positions easier, and a process for 3D printing different components quickly and cost-effectively.
One of the primary challenges identified by soldiers for the grappling hook was the inherent danger of dismounted breaching operations. The traditional method of throwing the hook causes inaccurate positioning and exposes soldiers to significant risks, including the possibility of detonation from hidden explosives.
“Sometimes soldiers are releasing and retracting the hook over a span of 300 yards,” Galloway said. “If you're a fraction of a second off with your throw, it can go to nine o'clock instead of 12, or it can go really high up, and then land 10 feet in front of you, and the whole time, an enemy could be firing at them.”
Galloway added: “The survivability rate was less than 10 percent in this conflict scenario.”
The students immersed themselves in the problem, interviewing soldiers, observing the traditional method firsthand, and conducting extensive research. The students experimented with various design concepts. They considered drone-based delivery systems, but ultimately decided on a more practical and reliable solution, a simple handle attached to the grappling hook.
This addition allows for a more accurate and powerful throw. By using an overhand throwing motion, much like one might with a tomahawk, soldiers can achieve greater distance and precision, reducing the number of throws required to reach the target.
“It’s a simple innovation,” said Galloway. “You're still getting a lot of rotational speed up top and can launch the hook pretty far. The challenge was adding the handle without adding too much more weight.”
By making modifications to the entire design, the team was able to keep the final prototype at 734 grams, just 82 grams more than the original grapnel. The team’s modifications also focused on the durability and reliability of the new design, working with robust materials, ensuring it can withstand the rigors of military operations.
“This was an excellent project opportunity for the students,” said Galloway, who encourages students from all disciplines to take his “How to Make Almost Anything and Make it Matter” class, including computer science, electrical engineering, biomedical engineering, and mechanical engineering in addition to students entirely outside of engineering. “They could test all kinds of recipes, some work, some don’t, and this type of project is the best way to learn.”
One of the students, Gavin Stevens, a Midshipman at Vanderbilt Naval Reserve Officer Training Corps (ROTC) and engineering major, said, “I learned the value of working in an interdisciplinary team. My teammates, Jake Schorr and Lucas Slater, and I are not ‘formal’ engineers, yet our collaboration was crucial in tackling the challenges of this project. These skills were essential in ensuring our solutions were not only innovative but also aligned with the needs of the combat engineers.”
For Stevens, it was the soft skills he developed while working on this project that he appreciated the most.
“This project was a significant learning experience, teaching me various skills that extended beyond technical expertise, most notably, empathy-centered design and effective communication with sponsors. I discovered that understanding user needs, clearly communicating them to your team, and effectively presenting your ideas to sponsors are often more important than the technical intricacies of the solution itself.”
More Like This: MagniClaw Locks Wheelchairs into Place
The Vanderbilt team's innovative solution has garnered significant attention from the Army, with the potential for widespread adoption – serving as a testament to the power of collaboration and the potential for groundbreaking solutions to emerge from partnerships between universities and the military.
Recognizing this potential, The Army Futures Command launched the Civil-Military Innovation Institute (CMI2), a nonprofit that bridges the gaps in defense innovation, by creating more opportunities for university innovation and commercial research. In addition to Fort Campbell, CMI2 has also propped up innovation centers at Fort Andrew, Fort Liberty, and Fort Stewart.
“We’re trying to create these spaces where soldiers can work through their ideas,” Galloway said. “A place where you can bring in collaborators from industry and academia to partner in meaningful ways.”
Cassandra Kelly is a technology writer in Columbus, Ohio.
Kevin Galloway, a research associate professor at Vanderbilt’s School of Engineering, said the collaboration began in 2018.
“I met Col. John Cogbill, now a Brigadier General, and he said he wanted to create an innovation ecosystem within the Third Brigade,” Galloway said. “One of the things soldiers wanted to learn more about was additive manufacturing, so the General challenged his combat team to pitch ideas of how they thought additive manufacturing could support operational readiness. No idea was a bad idea.”
Since then, the partnership has fostered soldier-informed innovation through a number of different projects, including an excavator tool that makes digging hasty fighting positions easier, and a process for 3D printing different components quickly and cost-effectively.
One of the primary challenges identified by soldiers for the grappling hook was the inherent danger of dismounted breaching operations. The traditional method of throwing the hook causes inaccurate positioning and exposes soldiers to significant risks, including the possibility of detonation from hidden explosives.
“Sometimes soldiers are releasing and retracting the hook over a span of 300 yards,” Galloway said. “If you're a fraction of a second off with your throw, it can go to nine o'clock instead of 12, or it can go really high up, and then land 10 feet in front of you, and the whole time, an enemy could be firing at them.”
Galloway added: “The survivability rate was less than 10 percent in this conflict scenario.”
The students immersed themselves in the problem, interviewing soldiers, observing the traditional method firsthand, and conducting extensive research. The students experimented with various design concepts. They considered drone-based delivery systems, but ultimately decided on a more practical and reliable solution, a simple handle attached to the grappling hook.
This addition allows for a more accurate and powerful throw. By using an overhand throwing motion, much like one might with a tomahawk, soldiers can achieve greater distance and precision, reducing the number of throws required to reach the target.
“It’s a simple innovation,” said Galloway. “You're still getting a lot of rotational speed up top and can launch the hook pretty far. The challenge was adding the handle without adding too much more weight.”
By making modifications to the entire design, the team was able to keep the final prototype at 734 grams, just 82 grams more than the original grapnel. The team’s modifications also focused on the durability and reliability of the new design, working with robust materials, ensuring it can withstand the rigors of military operations.
“This was an excellent project opportunity for the students,” said Galloway, who encourages students from all disciplines to take his “How to Make Almost Anything and Make it Matter” class, including computer science, electrical engineering, biomedical engineering, and mechanical engineering in addition to students entirely outside of engineering. “They could test all kinds of recipes, some work, some don’t, and this type of project is the best way to learn.”
One of the students, Gavin Stevens, a Midshipman at Vanderbilt Naval Reserve Officer Training Corps (ROTC) and engineering major, said, “I learned the value of working in an interdisciplinary team. My teammates, Jake Schorr and Lucas Slater, and I are not ‘formal’ engineers, yet our collaboration was crucial in tackling the challenges of this project. These skills were essential in ensuring our solutions were not only innovative but also aligned with the needs of the combat engineers.”
For Stevens, it was the soft skills he developed while working on this project that he appreciated the most.
“This project was a significant learning experience, teaching me various skills that extended beyond technical expertise, most notably, empathy-centered design and effective communication with sponsors. I discovered that understanding user needs, clearly communicating them to your team, and effectively presenting your ideas to sponsors are often more important than the technical intricacies of the solution itself.”
More Like This: MagniClaw Locks Wheelchairs into Place
The Vanderbilt team's innovative solution has garnered significant attention from the Army, with the potential for widespread adoption – serving as a testament to the power of collaboration and the potential for groundbreaking solutions to emerge from partnerships between universities and the military.
Recognizing this potential, The Army Futures Command launched the Civil-Military Innovation Institute (CMI2), a nonprofit that bridges the gaps in defense innovation, by creating more opportunities for university innovation and commercial research. In addition to Fort Campbell, CMI2 has also propped up innovation centers at Fort Andrew, Fort Liberty, and Fort Stewart.
“We’re trying to create these spaces where soldiers can work through their ideas,” Galloway said. “A place where you can bring in collaborators from industry and academia to partner in meaningful ways.”
Cassandra Kelly is a technology writer in Columbus, Ohio.
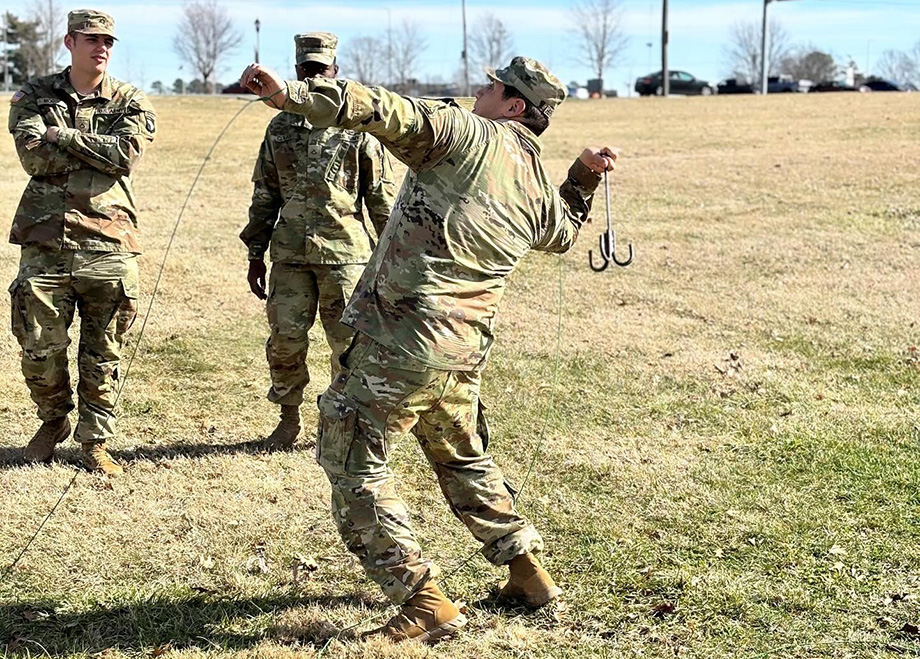
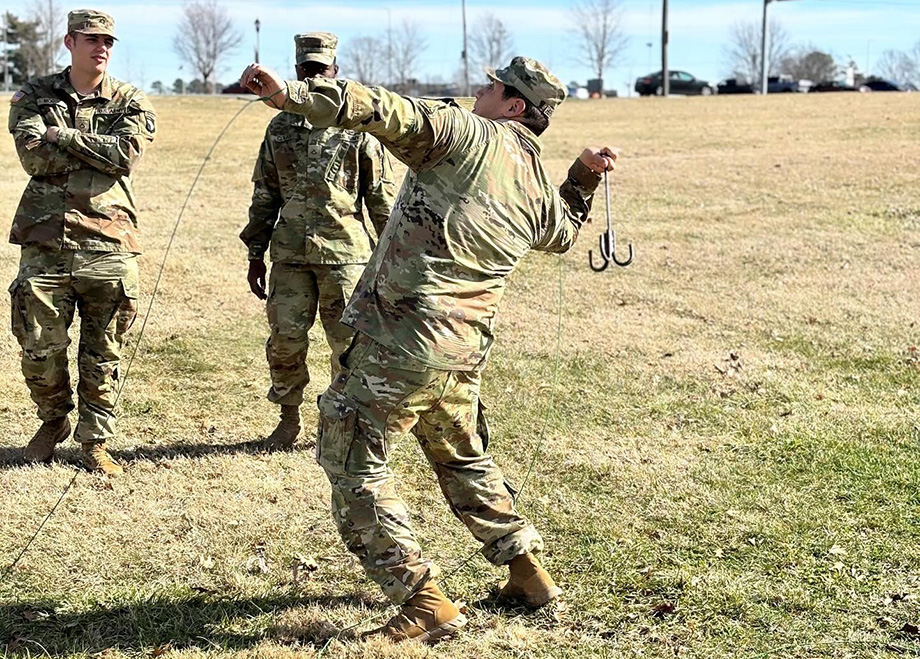