Virtual Testing of Composite Pressure Vessels
Virtual Testing of Composite Pressure Vessels
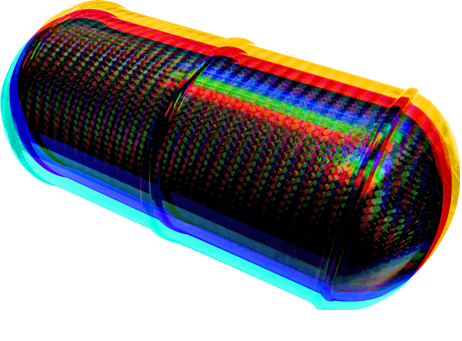
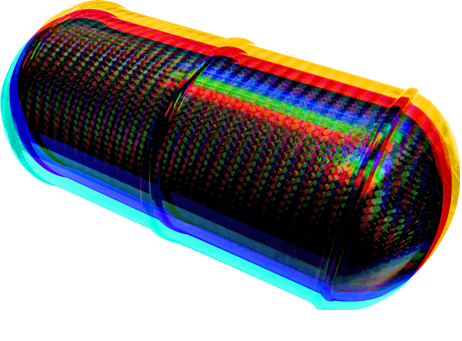
Composite pressure vessels generally perform better and last longer than traditional metallic pressure vessels. They are also more corrosion-resistant and can withstand higher pressures—for example, hydrogen needs to be pressurized to 70 MPa to achieve minimum vehicle autonomy requirements—something that is difficult to achieve with metal.
There are a number of restrictions on size, weight, efficiency, and physical reliability of hydrogen storage devices for the automotive industry. At these smaller dimensions hydrogen needs to be stored at very high pressure in order to be energy efficient, which in turn requires a very strong and fatigue-resistant container, such as a carbon fiber-reinforced composite pressure vessel.
Although stronger than metal, carbon-reinforced composites still fail. This usually starts at a microstructural level, such as fiber breaking or matrix cracking. It can also be related to variances in microstructural design elements, such as fiber orientation and fiber volume fraction, which also have great impact on overall structural performance.
Fiber Alignment
“In structures made of composite materials, damage actually starts at a very small scale compared to the size of the structure itself,” says Leandro Castro, co-founder of MultiMech Research and Development, a provider of advanced computational tools for evaluating complex engineering challenges. “For example, in carbon fiber composites, debonding, another important type of damage in composites, can occur between the fibers and the resin surrounding them, where each carbon fiber is about 0.005–0.010 millimeters in diameter.”
Fiber alignment in the composite material is also important. If fibers are aligned parallel to the load direction, then the overall composite failure is controlled by the failure of the fibers, which have very high strength. If the fibers are aligned perpendicularly to the applied load, then the failure of the composite is dominated by the matrix, as well as the interface between matrix and fiber, which is much weaker than the fiber.
Designers and engineers strive to accurately predict the physical reliability of materials and their microstructures before production starts. This requires sophisticated software and algorithms. For example, MultiMech R&D provides two-way coupled multi-scale mechanics software that can evaluate events happening at multiple scales simultaneously using multi-scale algorithms for both impact and quasi-static problems, including explicit crack modeling. This sort of approach allows the design team to build virtually any material from the ground up (fibers and resin) and accurately simulate the physical reliability of the designed structure, before the first physical prototype is ever made.
“This allows engineers to control microstructural design variables, such as fiber orientation, volume fraction, type of fiber and matrix, and assess the effect of each design variable on the overall structural performance of the component by using its unique two-way coupled multi-scale solver,” says Flavio Souza, also co-founder of MultiMech R&D. “The software can generate microstructures automatically to expedite simulation pre-requisites. It can automatically create microstructures of existing or novel materials so engineers have the most freedom of design by virtual testing combined or new materials before they are ever manufactured. In such cases, engineers can get a feeling for the mechanical response of combined resin/fibers and actually design the material to meet their design specifications.”
Optimizing Design
When designing composite pressure vessels engineers must determine:
- The most appropriate fiber and resin matrix
- How many layers/plies are needed
- Fiber orientation in each layer/ply
- The level of damage (microcracks) the composite can withstand.
These questions are mostly related to defining parameters to maximize the stiffness, strength, fatigue resistance, and long-term performance of the composite pressure vessel. “Due to either service loading or manufacturing defects, virtually all composite structures exhibit microcracks,” says Souza. “Each microcrack may or may not propagate during service life and new microcracks may be initiated when the composite is subject to thermo-mechanical loading.”
Predicting failure is extremely complicated from the engineering viewpoint because even though carbon fibers can be considered an elastic material, the surrounding matrix is mostly a thermo-viscoelastic material.
“While the fibers carry most of the load of carbon fiber composites, loaded in the fiber direction, their long-term behavior and failure arecontrolled by the viscoelastic (time-dependent) properties of the matrix surrounding those fibers,” Castro points out. “The material will also have intrinsic statistical variations due to manufacturing. Carbon fibers are relatively expensive and can account for most of the cost of a composite pressure vessel, so they need to be used wisely. Our two-way coupled multi-scale mechanics software has capabilities for modeling damage evolution in composites, which is essential when optimizing the design of composite pressure vessels.”
Mark Crawford is an independent writer.
The software can generate microstructures automatically to expedite simulation pre-requisites.Flavio Souza, co-founder, MultiMech R&D