Wearable Patch Reads Muscle Activity Remotely
Wearable Patch Reads Muscle Activity Remotely
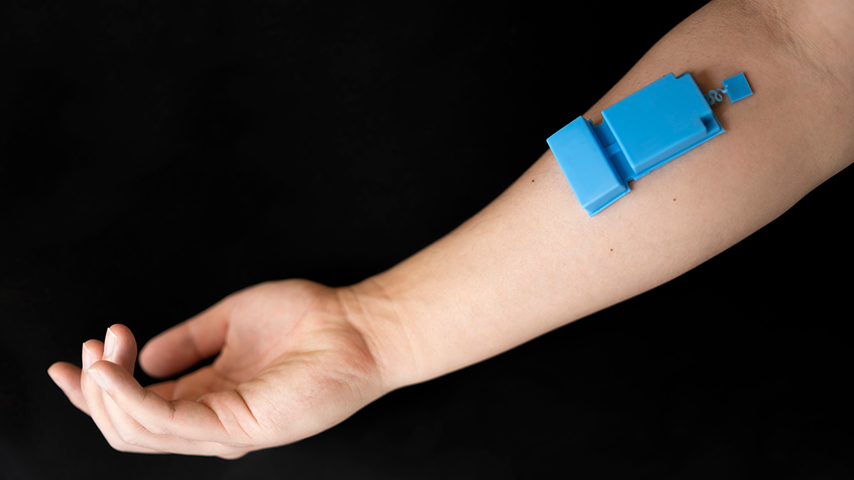
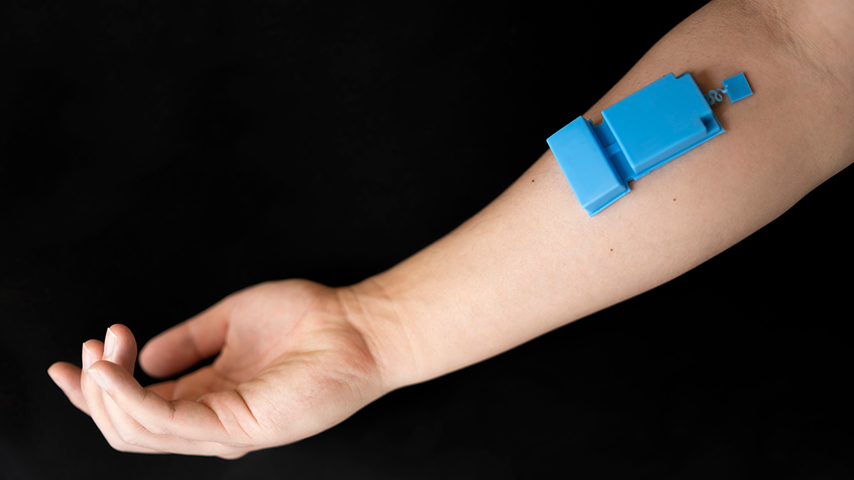
A small device could unlock multiple healthcare and human-machine interfaces, in addition to helping medical professionals gauge pulmonary health remotely.
In medical practice, monitoring muscle activity is one of the methods to gauge health. Tracking the thickness of the diaphragm, for example, helps evaluate pulmonary function. The traditional approach to monitoring muscle activity, electromyography (EMG), involves attaching metal electrodes to the body and studying resultant electrical signals. The stability and strength of the signals with such an approach is a challenge. It is also difficult to isolate activity from specific muscles because signals from neighboring groups can blend together.
A wearable ultrasound device developed by a team of researchers at the University of California, San Diego (UCSD), addresses these problems. By making long-term monitoring muscle activity noninvasive through a wearable patch and by relying on ultrasound which is able to isolate specific muscles, the device presents an effective alternative to EMG.
This research has significant promising implications in the monitoring of respiratory health. Measuring diaphragm thickness provides insight into pulmonary health by evaluating the quality of the breaths. Shallow breaths, reflected in the diaphragm measurements, could be a signal of distress. The device can also be used for evaluating the activity of other muscles, including those in the forearm.
Sheng Xu, a professor and Jacobs Faculty Scholar in the Aiiso Yufeng Li Family Department of Chemical and Nano Engineering at UCSD led the research team, which collaborated with Jinghong Li, professor of medicine at UCSD School of Medicine and pulmonologist at UCSD Health.
Measuring the diaphragm
Measuring about 2 centimeters by 3 centimeters by 1 centimeter, the device includes three components: A single transducer sends and receives ultrasound waves; a custom-designed wireless circuit controls the transducer and records and wirelessly transmits received data to a computer; and a lithium-polymer battery powers the system for at least three hours. A flexible silicone elastomer encases the entire apparatus, which uses a thin layer of adhesive, much like a Band-Aid, to stick to human skin.
Using ultrasound over other techniques is more advantageous because its ability to penetrate deeper into tissue means it delivers stronger signals with more information, Xu explained.
Similar Reading: Wearable Patch Offers Voice to the Voiceless
“Ultrasound can penetrate into the human tissue just like we see through glass,” he continued. When ultrasound waves encounter different kinds of tissue from different muscles, they get deflected, just like light on a water surface. Scientists can use this principle to measure tissue interfaces. Measuring the signal reflections at the interface between the diaphragm and other surrounding tissues for example, will give an estimate of the diaphragm’s thickness.
The most obvious advantage of the single transducer-based system is that it makes the entire apparatus small and wearable. Conventional ultrasound equipment relies on an array of transducer units to form interpretable images. Fortunately, data from one transducer alone is enough to perform simple muscle calculations, like gauging diaphragm thickness.
However, more complex assessments such as inferring hand gestures, involve understanding the distribution of muscles in the forearm. That’s a problem with single transducers. The data from a single transducer is not enough to form images, which means it’s almost impossible for humans to understand hand movement using the signals from the single transducer alone.
This is where AI comes in.
A complement to ultrasound
Using a pattern recognition algorithm, the UCSD researchers correlated the transducer’s signals to specific hand gestures. Matching the data from the transducers against the AI program enabled the team to get away with just a single transducer instead of an entire array. The wearable single transducer is able to recognize 13 degrees of freedom, covering 10 finger joints and three rotation angles of the wrist. Capturing even slight wrist and finger movements with high sensitivity enables the system to form an effective human-machine interface. To demonstrate the device’s capabilities, the researchers placed the patch on an individual’s forearm and were able to successfully pipette a fluid with a robotic arm.
Discover the Benefits of ASME Membership
While the team has thus far developed protocols to study the thickness of the diaphragm and to evaluate muscle activity in the arm, the methods can translate to other muscle groups with a little work, Xu said. “The methodology will be the same throughout the body but different muscles have different anatomy, structures and functions, so the AI algorithms will have to be retrained with relevant data,” he added.
Future applications
The small-form-factor patch can transmit data wirelessly up to about 10 meters (32 feet) and the on-board battery can provide needed low power for about three hours, which can be extended by reducing the power consumption of onboard electronics. Researchers have tested wearing the patch for 24 hours under strenuous conditions such as showering and exercising, with no damaging effects.
Future work will focus on making the AI algorithms easily retrainable so the device can be used to measure activity across multiple muscle groups. Clinical validation is also on the cards. Xu cofounded Softsonics, a spinoff from UCSD, through which he is targeting commercialization of the technology. “We are trying to get more patient data and apply for FDA clearance,” he said. The wearable hands-free operation and continuous remote monitoring potential are especially strong assets for the device, Xu added.
Poornima Apte is a technology writer based in Walpole, Mass.
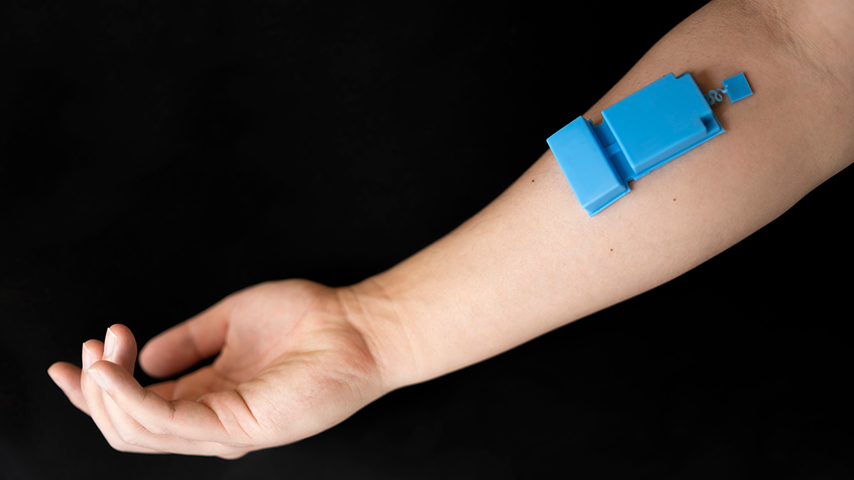
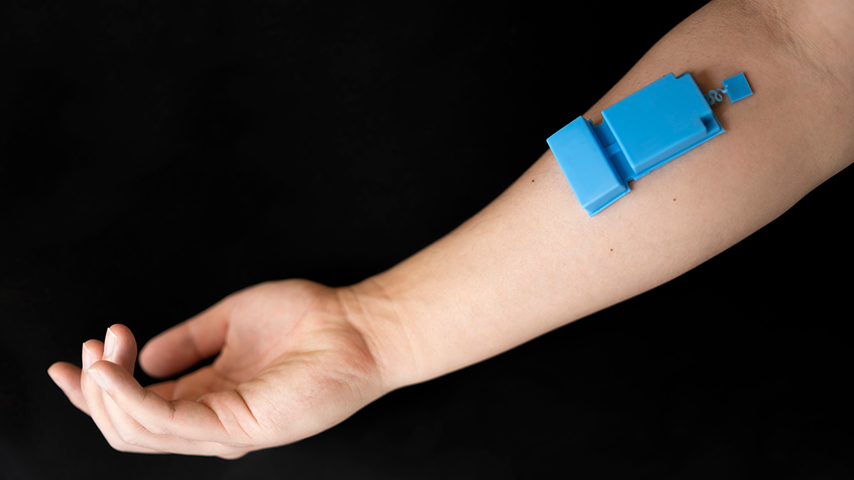