Developing a Durable Prosthetic Knee Joint
Developing a Durable Prosthetic Knee Joint
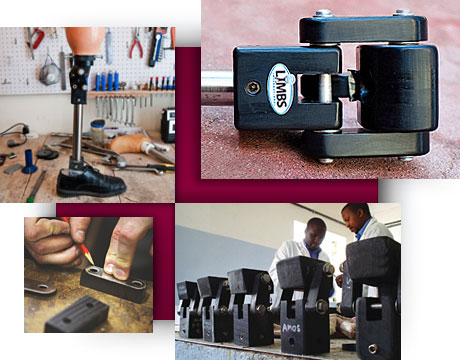
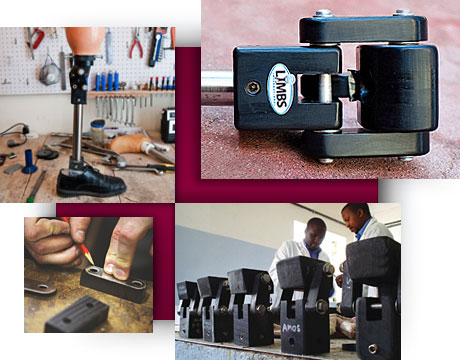
Images: LIMBS International
Millions of amputees across the world—many of them in low-income countries—are in need of prosthetic devices. This is especially true for those who are missing legs and feet, because walking is often the main mode of travel in these regions. Because these countries are often impoverished and plagued by war, landmines, and poor medical care, there continues to be a significant unmet need for prosthetic devices.
Roger V. Gonzalez, a mechanical and biomedical engineering professor at the University of Texas-El Paso, has set out to change this. He founded LIMBS International, a nonprofit that is committed to restoring mobility to millions of amputees around the world. Assisted by engineering students, LIMBS designs highly functional, innovative, ultra low-cost prosthetic devices.
The initiative grew from a senior biomedical engineering project that challenged students to design and build a durable, low-cost knee joint that would be part of an above-the-knee prosthesis. Another objective was making it simple enough that it could be fabricated locally in developing countries. Their design became the first prototype of what is known today as the “Relief Knee.”
How the Relief Knee Is Different
The biggest difference between the Relief Knee and other knees on the market is its functionality. Field tests have shown the knee is more functional than single-axis and hinge designs. The Relief Knee is a four-bar, polycentric knee that is lightweight and stable, combining sophisticated design with low-cost, durable materials that are available in developing countries.
“The knee is totally mechanical, yet provides a stable stance environment when properly fitted,” says Gonzalez. “Polycentric knees have been around for a long time. The key is designing the knee so that inexpensive materials can be used and that it can repaired in the field. Being able to take apart and reassemble the knee if a part needs to be replaced is important. The knee can be easily be repaired in the field with materials available at a local hardware store and with the skill sets available in the developing world, many times by the patients themselves. This keeps the knee functional for years to come.”
Future Plans
In 2012, LIMBS established a research partnership with the University of Texas-El Paso. This provides qualified engineering students with opportunities to design, test, and implement new prosthetic components in these countries. An injection-molded Relief Knee will soon be available that enhances the durability and functionality of the current model, at lower cost.
“We are also working on various feet and arm designs,” states Gonzalez. “We take on the challenges from various approaches so we can hopefully have a multifaceted solution. Not one solution can meet the needs of the entire developing world. We aim to give the poorest of the poor some options that we take for granted here in the U.S.”
As LIMBS expands its product line, it will continue to improve functionalityand reduce costs.
“There are times when certain parts of the world would like components with more ‘bells and whistles’ and we are looking at options to provide these, while still keeping costs very low,” says Gonzalez. “We are also working with other academic and industrial partners to develop joint programs to accelerate technological development and expand into areas that go beyond prosthetics, and even orthodics.”
For Gonzalez, the biggest surprise in designing prosthetics is the amount of attention that goes into working out the details, even with ultra-simple designs.
“It is the details that can kill a project,” says Gonzalez. “We have also learned that technology, as important as it is, is not enough. You have to couple it with a holistic approach to solving these vexing problems. We as engineers need to move beyond technology to make a difference.”
Mark Crawford is an independent writer.
The knee can be easily repaired in the field with locally available materials and the skill sets available in the developing world—many times by the patients themselves.Roger V. Gonzalez, University of Texas-El Paso
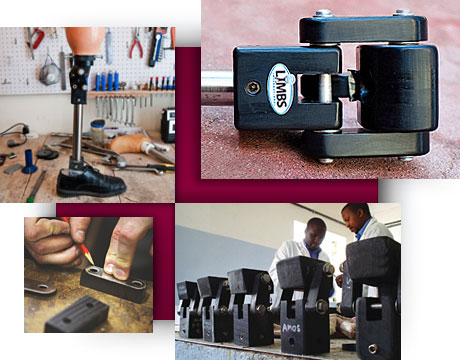
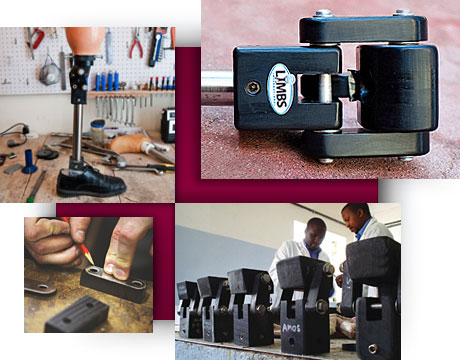