Protecting a New World of 3D-Printed Products
Protecting a New World of 3D-Printed Products
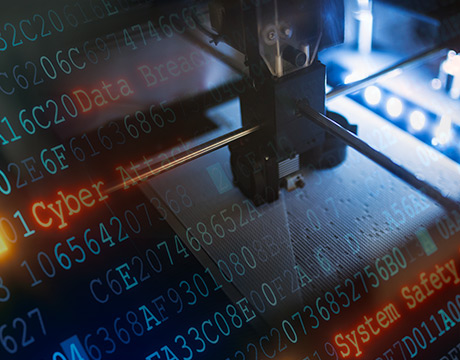
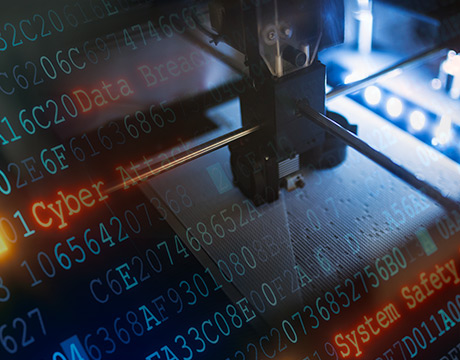
The number of 3D-printed, critical components grows each day. They make their way into vehicles, aircraft, medical devices, prostheses, human bodies, and military applications. With that increase comes more opportunities for bad actors to hack the additive manufacturing industry, potentially jeopardizing the products meant to improve our health and safety.
So far, no major hacks have been reported in the emerging industry, says Raheem Beyah, a professor at Georgia Institute of Technology’s School of Electrical and Computer Engineering. He wants to keep it that way.
“Anyone that will rely on additive manufacturing for mission-critical projects should be concerned,” Beyah says. Corporate saboteurs, nation states, and disgruntled employees are just a few of the groups he says will target AM and the products it generates.
To ease those concerns, Beyah and a team of researchers from Georgia Tech and Rutgers University have developed a three-layer system designed to verify that 3D printed objects have not been compromised. It uses acoustic measurements, printer component tracking, and detectable nanorods to protect the integrity of printed products. The system works independently of corporate computer networks, removing one of the major gateways to cybercrime.
We have plenty of cyber protections, but it will take a new kind of security to protect the physical side. It’s a new day.
Prof. Raheem Beyah, Georgia Tech
“We have plenty of cyber protections, but it will take a new kind of security to protect the physical side,” says Beyah, who has a deep background in cybersecurity. “It’s a new day. It’s going to be critical to make sure everything is secure.”
He’s not the only one who thinks so. Last summer, the National Science Foundation awarded the team a three-year, $250,000 grant to continue to improve and strengthen the system.
All of the metrics captured through each segment of the security system are compared to what Beyah calls the “golden copy,” which includes a properly printed finished product and the documentation of the printer’s key performance metrics during the production process. The researchers tested their security system using different types of 3D printers and a computer numerical control machine while manufacturing a polyethylene tibial knee prosthesis. They then compared different stages of the printing processes to the golden copy. “We got close to one hudred percent accuracy on the tests,” Beyah says.
The system’s three components include an acoustic monitor made up of inexpensive microphones located above and/or around the printer and filtering software that detect changes in the usual sound a printer makes. The software, he says, works in much the same way as the Shazam and SoundHound apps that can accurately identify millions of different songs through the microphone of a smartphone.
“The basic thesis is that you have mechanical components that have to make some noise,” he says. “When I’m printing the same exact thing, the printer should sound the exact same way when I make the next copy.”
The system’s physical tracking piece uses linear potentiometers and gyroscopic sensors placed on the extruders to make sure they follow the same path when printing the same objects.
To detect variations or flaws in the final product, the researchers placed gold nanorods into the filament material used in the printer. They used Raman spectroscopy and computed tomography to detect the location of the nanorods in the final product. “I know beforehand where I’m going to place them,” Beyah says, adding that the nanorods don’t affect the integrity of the material. “Think of it as a 3D watermark.”
Beyah is using the grant, in part, to improve the accuracy of the system’s sensors and the microphones, especially when it comes to isolating and focusing on the noise one printer makes from the others around it. The researchers are experimenting with different camera arrays that can be used to monitor stages of the printing process in real time.
Beyah says the system is proof-of-concept but feels it could be ready for market in about a year. A major selling point, he says, is that it doesn’t have to operate on a connected network.
Considering the possible vulnerabilities that exist in each stage of the 3D printing process – creating the product design on a computer, pushing the design package over the network to the printer, downloading printer firmware – Beyah believes extra layers of protection can’t come fast enough to the AM industry.
“Think about the entire 3D-printing ecosystem and all of its different stages; the software, the STL file, the OS, the firmware can be compromised. The network’s intrusion detection system can be bypassed,” he says. “We need something in addition to protect the system.”
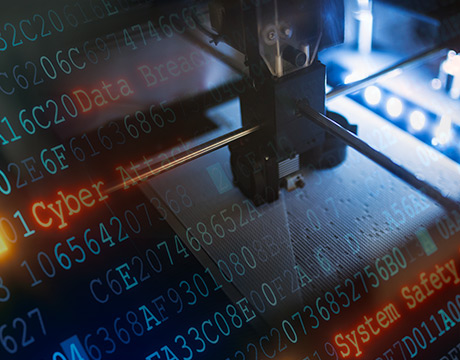
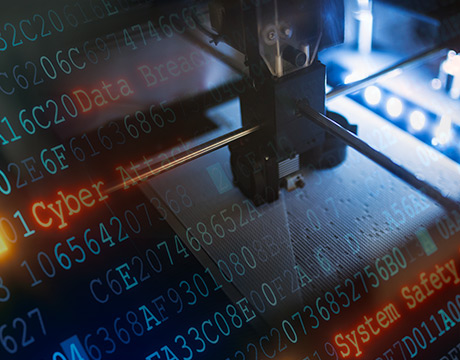