Bases and Application of Piping Flexibility Analysis to ASME B31 Codes (In-Person)
Course Type:
Course Number:
Language:
This interactive, two-day course provides a thorough insight into the history and bases for the rules for piping design - including ASME B31.1 and B31.3.
This Standard was last reviewed and reaffirmed in {{activeProduct.ReaffirmationYear}}. Therefore this version remains in effect.
{{activeProduct.Title}}
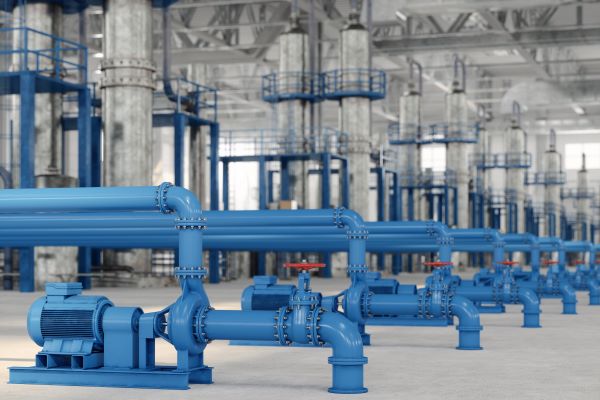
This course is not currently available.
Course Not Available
Thank you for your interest in this course. To be notified of future availability, please provide your information.
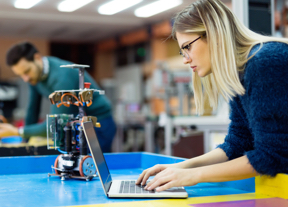
Get papers online in the ASME Digital Collection
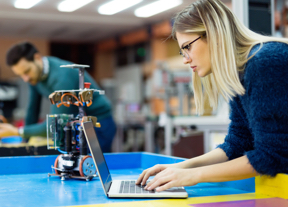
Sorry, we only have available spots for this course. Would you like to add those to your cart?