Design by Analysis Requirements in ASME BPV Code, Section VIII, Division 2 – Alternative Rules (In-Person)
Course Type:
Course Number:
Credits:
Language:
Design by Analysis Requirements in ASME BPV Code, Sec 8, Div 2 – Alternative Rules focuses on the analytical methods & guiding FEA use to meet requirements
This Standard was last reviewed and reaffirmed in {{activeProduct.ReaffirmationYear}}. Therefore this version remains in effect.
{{activeProduct.Title}}

Digital products are restricted to one per purchase.
{{activeProduct.CurrencySymbol}}{{ formatPrice(activeProduct.ListPrice) }} was {{activeProduct.CurrencySymbol}}{{ formatPrice(originalPrice) }}
{{activeProduct.CurrencySymbol}}{{ formatPrice(activeProduct.ListPriceSale) }} was {{activeProduct.CurrencySymbol}}{{ formatPrice(activeProduct.ListPrice) }}
{{activeProduct.CurrencySymbol}}{{ formatPrice(activeProduct.ListPrice) }} was {{activeProduct.CurrencySymbol}}{{ formatPrice(originalPrice) }}
{{activeProduct.CurrencySymbol}}{{ formatPrice(activeProduct.ListPriceSale) }} was {{activeProduct.CurrencySymbol}}{{ formatPrice(originalPrice) }}
{{activeProduct.CurrencySymbol}}{{ formatPrice(activeProduct.MemberPrice) }} was {{activeProduct.CurrencySymbol}}{{ formatPrice(originalPrice) }}
{{activeProduct.CurrencySymbol}}{{ formatPrice(activeProduct.MemberPriceSale) }} was {{activeProduct.CurrencySymbol}}{{ formatPrice(originalPrice) }}
*Excluding Lite Members
Final invoices will include applicable sales and use tax.
Print or Share
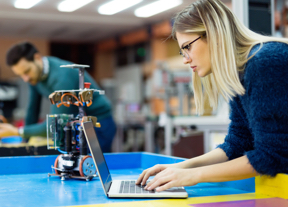
Get papers online in the ASME Digital Collection
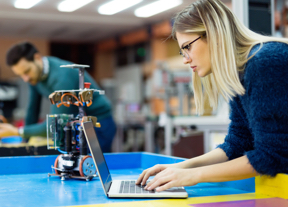
Sorry, we only have available spots for this course. Would you like to add those to your cart?