Forooza Samadi, assistant director of the Alabama Industrial Training and Assessment Center and assistant professor of mechanical engineering at the University of Alabama in Tuscaloosa, recently studied ways factories could cut costs and carbon emissions. She was coauthor on the paper, “Strategic Evaluation of Sustainable Practices for HVAC Systems in Small- and Medium-Sized U.S. Manufacturers,” published in the ASME Journal of Engineering for Sustainable Buildings and Cities in August 2024. Here, she described some of her findings.
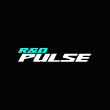
Industries are so varied that their energy usage and carbon emissions tend to be difficult to reduce. Can you put some of this into context for us?