3D-Printed Copper Alloy Can Withstand 6,000 °F
3D-Printed Copper Alloy Can Withstand 6,000 °F
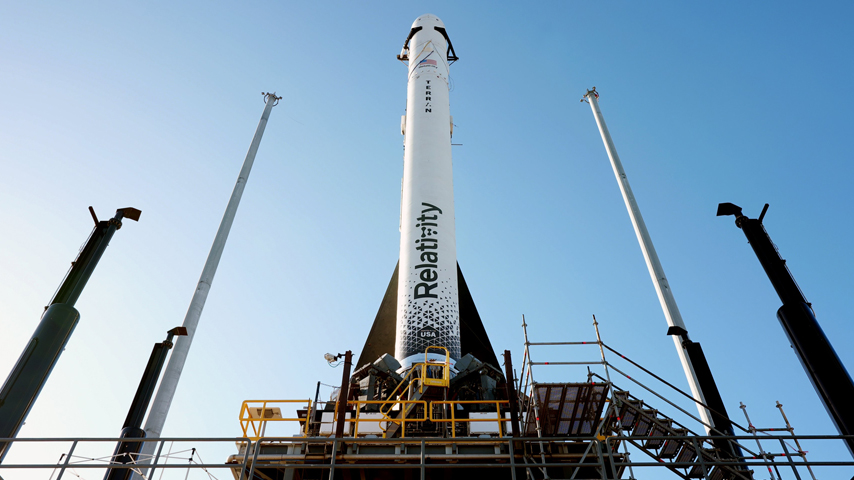
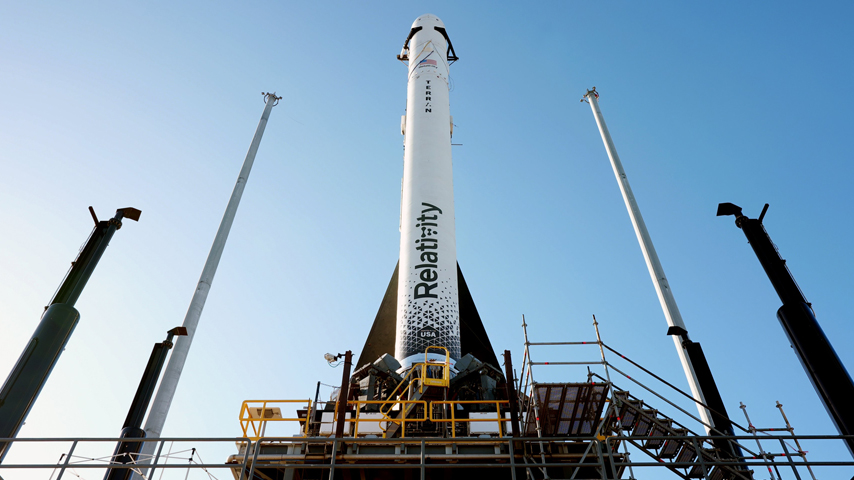
NASA has developed a copper-chromium-niobium alloy for combustion chambers that can be additively manufactured using laser powder bed fusion or directed energy deposition technologies.
In March 2023, NASA launched the Relativity Space Terran 1 rocket from Cape Canaveral Space Force Station in Florida. This was the first launch of a test rocket made entirely from 3D-printed parts, including multiple engines made from an innovative copper alloy that can withstand temperatures as high as 6,000 °F.
Created at NASA’s Glenn Research Center, this family of copper-based alloys is called Glenn Research Copper (GRCop) and was designed for use in combustion chambers of high-performance rocket engines. David Ellis, materials research engineer at the Glenn Research Center, has supervised the development of GRCop since the late 1980s.
GRCop is an alloy of copper, chromium, and niobium. It is engineered for high strength, high thermal conductivity, and high creep resistance—making it ideal for high-temperature applications. GRCop’s resistance to extreme temperatures results in higher-performance components and greater reusability, as well as a huge cost savings.
“For example, our research showed that GRCop-84 would easily meet the goal of 100 missions between maintenance service and 500 missions of engine life,” Ellis said.
Using metallurgical principles, researchers designed the latest alloy and determined the best compositions. Copper was chosen for its thermal conductivity and high melting point. Chromium and niobium were selected for their high and low solubilities in liquid and solid copper, respectively.
“We overcame potential hydrogen embrittlement issues using a thermodynamic understanding of the alloy system and a slight excess of chromium,” Ellis said. “Our team also found and eliminated issues such as 200-250 parts per million iron decreasing the thermal conductivity. We also figured out ways to prevent erosion of the refractory ceramics using our understanding of the materials in the system.”
Become a Member: How to Join ASME
The hardest part of alloy design was the melting and atomizing of the alloys. “To get a uniform melt, we must raise the temperature to over 1750 °C. The niobium will attack alumina and eat away the crucible and tundish,” Ellis explained. “Once a uniform melt is obtained, it must be cooled at >104 K/sec or the chromium-niobium will grow to as large as 1 cm, when we need it to be <1 micrometer to provide strengthening.”
GRCop alloys are very stable. During these experiments, they retained most of their properties, even when exposed to temperatures up to 98 percent of their melting points.
“The GRCop alloys were far easier to print using laser powder bed fusion compared to other copper-based alloys,” Ellis added. “They produced superior properties, such as tensile strength up to 400 °C.”
The team was also concerned about surface roughness in the channels of the liners. The roughness increased the pressure drop but also increased heat flow, essentially balancing each other out. The researchers were still able to achieve acceptable fatigue properties, despite the very rough surfaces.
GRCop alloys were a key reason for the success of the 3D-printed rocket.
“The cost and time savings were much greater than what we expected,” Ellis said. “For example, we demonstrated a 58 percent to 68 percent reduction in time and a 27 percent to 32 percent reduction in cost to make a jacketed liner. One senior Marshall Space Flight Center manager told me it was the first time they had seen a program where he felt that there was a true promise of decreased time and cost.”
You Might Also Enjoy: Getting Closer to the Ability to 3D Print Tiny Structures
The team was successful in creating a dispersion-strengthened material from a molten alloy using laser powder bed fusion to melt and create GRCop alloys from elemental powders.
“We hope to be able one day to provide site-specific compositions that maximize the most important properties for a design,” Ellis said. “For mechanical engineers, that means the potential ability to tune material properties throughout the part to optimize the design.”
The GRCop alloys are nearing commercialization. Ellis’ team is working on a final report detailing the natural variation in mechanical and thermophysical properties of commercially produced GRCop-42 and GRCop-84 to support commercial users for the foreseeable future.
The main barrier to more widespread adoption of GRCop in high-temperature heat sinks and other thermal control applications has been the cost of the powder. As costs come down, applications such as high-temperature electronics and heat exchangers (air-to-air, liquid-to-air, liquid-to-liquid) will become more affordable.
“The use of additive manufacturing could result in unique designs that increase the heat flow and efficiency of the designs,” Ellis concluded.
Mark Crawford is technology writer in Corrales, N.M.
Created at NASA’s Glenn Research Center, this family of copper-based alloys is called Glenn Research Copper (GRCop) and was designed for use in combustion chambers of high-performance rocket engines. David Ellis, materials research engineer at the Glenn Research Center, has supervised the development of GRCop since the late 1980s.
GRCop is an alloy of copper, chromium, and niobium. It is engineered for high strength, high thermal conductivity, and high creep resistance—making it ideal for high-temperature applications. GRCop’s resistance to extreme temperatures results in higher-performance components and greater reusability, as well as a huge cost savings.
“For example, our research showed that GRCop-84 would easily meet the goal of 100 missions between maintenance service and 500 missions of engine life,” Ellis said.
Taking an additive approach
Using metallurgical principles, researchers designed the latest alloy and determined the best compositions. Copper was chosen for its thermal conductivity and high melting point. Chromium and niobium were selected for their high and low solubilities in liquid and solid copper, respectively.
“We overcame potential hydrogen embrittlement issues using a thermodynamic understanding of the alloy system and a slight excess of chromium,” Ellis said. “Our team also found and eliminated issues such as 200-250 parts per million iron decreasing the thermal conductivity. We also figured out ways to prevent erosion of the refractory ceramics using our understanding of the materials in the system.”
Become a Member: How to Join ASME
The hardest part of alloy design was the melting and atomizing of the alloys. “To get a uniform melt, we must raise the temperature to over 1750 °C. The niobium will attack alumina and eat away the crucible and tundish,” Ellis explained. “Once a uniform melt is obtained, it must be cooled at >104 K/sec or the chromium-niobium will grow to as large as 1 cm, when we need it to be <1 micrometer to provide strengthening.”
GRCop alloys are very stable. During these experiments, they retained most of their properties, even when exposed to temperatures up to 98 percent of their melting points.
“The GRCop alloys were far easier to print using laser powder bed fusion compared to other copper-based alloys,” Ellis added. “They produced superior properties, such as tensile strength up to 400 °C.”
The team was also concerned about surface roughness in the channels of the liners. The roughness increased the pressure drop but also increased heat flow, essentially balancing each other out. The researchers were still able to achieve acceptable fatigue properties, despite the very rough surfaces.
Next steps
GRCop alloys were a key reason for the success of the 3D-printed rocket.
“The cost and time savings were much greater than what we expected,” Ellis said. “For example, we demonstrated a 58 percent to 68 percent reduction in time and a 27 percent to 32 percent reduction in cost to make a jacketed liner. One senior Marshall Space Flight Center manager told me it was the first time they had seen a program where he felt that there was a true promise of decreased time and cost.”
You Might Also Enjoy: Getting Closer to the Ability to 3D Print Tiny Structures
The team was successful in creating a dispersion-strengthened material from a molten alloy using laser powder bed fusion to melt and create GRCop alloys from elemental powders.
“We hope to be able one day to provide site-specific compositions that maximize the most important properties for a design,” Ellis said. “For mechanical engineers, that means the potential ability to tune material properties throughout the part to optimize the design.”
The GRCop alloys are nearing commercialization. Ellis’ team is working on a final report detailing the natural variation in mechanical and thermophysical properties of commercially produced GRCop-42 and GRCop-84 to support commercial users for the foreseeable future.
The main barrier to more widespread adoption of GRCop in high-temperature heat sinks and other thermal control applications has been the cost of the powder. As costs come down, applications such as high-temperature electronics and heat exchangers (air-to-air, liquid-to-air, liquid-to-liquid) will become more affordable.
“The use of additive manufacturing could result in unique designs that increase the heat flow and efficiency of the designs,” Ellis concluded.
Mark Crawford is technology writer in Corrales, N.M.
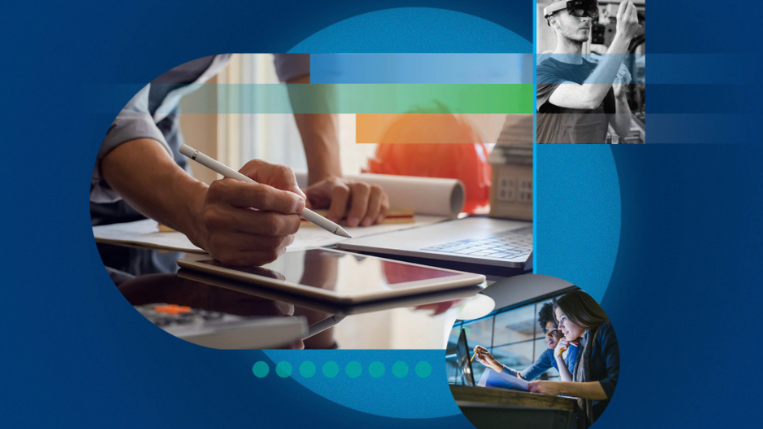
Pulse of the Profession: Career-Ready Soft Skills
From VR to AI, big data to nanoengineering, engineering advancements are reshaping the mechanical engineering field at a dizzying rate.