5 Ways to Reduce CO2 Emissions in Concrete Manufacturing
5 Ways to Reduce CO2 Emissions in Concrete Manufacturing
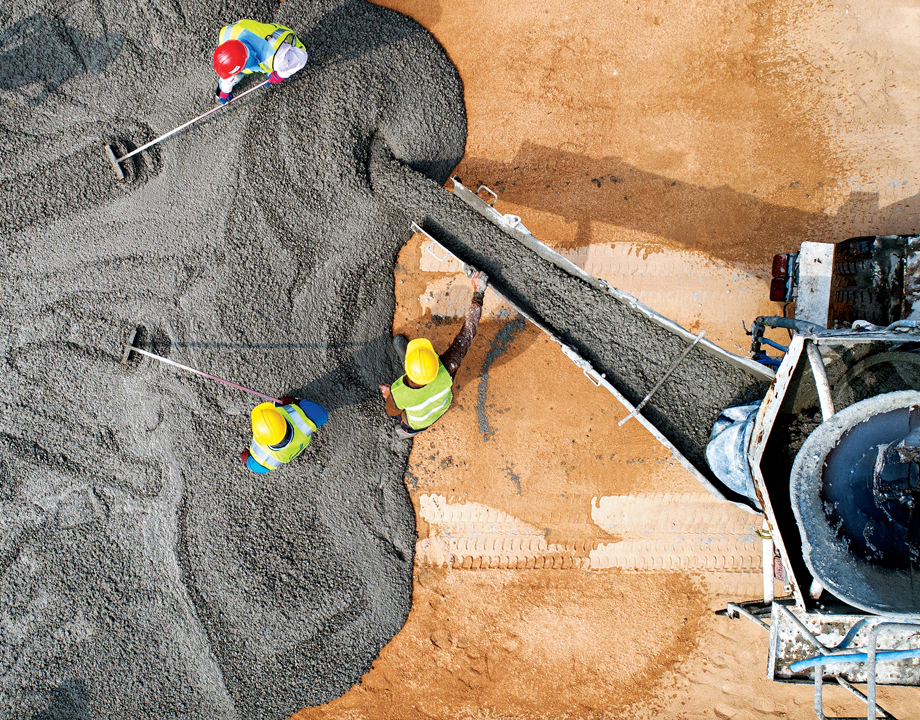
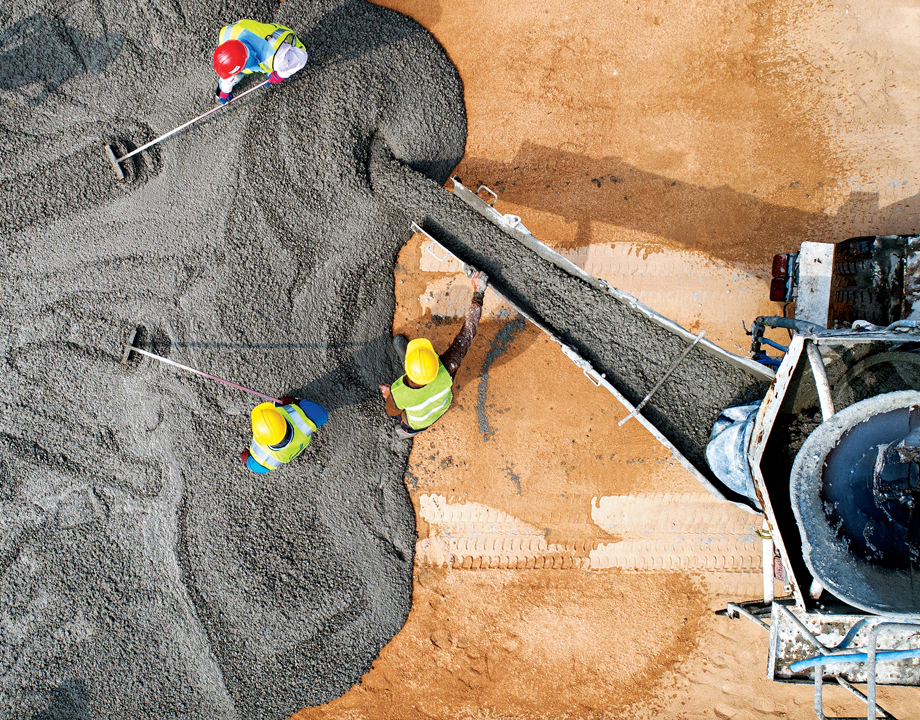
The Portland Cement Association has created a “roadmap to carbon neutrality” to reduce the more than 1.25 percent of U.S. carbon dioxide emissions from concrete manufacturing.
Date updated: October 23, 2024
Concrete is one of the most used man-made materials in the world, with the majority of concrete composed of Portland cement mixed with other cementitious materials, such as slag cement, fly ash, sand and gravel aggregates, water, and chemical additives.
More than 30 billion metric tons of concrete is used globally each year to build transportation infrastructure, sewage systems, dams, bridges, and high-rise buildings. However, manufacturing concrete also releases significant amounts of carbon dioxide into the atmosphere—about 8 percent of the world’s anthropogenic CO₂. Making concrete requires heating pulverized limestone and clay to roughly 1,450 °C. This process converts the main component of limestone (CaCO3) into calcium oxide (CaO), or lime, releasing CO2.
With that in mind, concrete manufacturers are working to reduce carbon dioxide emissions throughout their value chains. To that end, the Portland Cement Association created a “roadmap to carbon neutrality,” a strategic guide for achieving net-zero carbon in concrete manufacturing.
More Like This: How 5 Countries Work Toward Decarbonization
Five Ways to Reduce CO2 Emissions
One of the most effective approaches for achieving decarbonization is by using less Portland cement in the concrete mix. Below are five ways to change composition of concrete without reducing any of its mechanical characteristics.
- Rubber concrete. Researchers from the Royal Melbourne Institute of Technology in Australia have developed a new type of concrete that includes pulverized rubber tires, as well as construction and demolition waste, resulting in a concrete that is up to 35% percent stronger than traditional concrete. This “crumb rubber” reduces the volume of Portland cement in the concrete and also provides a market for end-of-life tires.
- CO2 injection systems. Captured carbon dioxide is injected into the concrete during mixing, where it is chemically converted into nano-sized particles of calcium carbonate. This process makes the concrete stronger and reduces the amount of CO₂ as an end product.
- Calcium silicate hydrate (CSH). Adding CSH nanoparticles to the concrete mix improves the strength of concrete by 15-20% and modulus of elasticity by up to 7%, without adversely affecting the durability of concrete. This reduces the total cement content in the concrete mix, while actually increasing strength and flexibility with fewer CO₂ emissions.
- Clay-based concrete. Clays can become active cementitious materials when they are heated to about 800 °C—far lower than the 1,450 °C required to produce ordinary cement. Not only does this result in using less CO2-emitting fuel, it also does not involve decomposing limestone, which is a major source of carbon dioxide release in traditional cement manufacturing.
- Geopolymers. The manufacture of geopolymer-based concrete emits far less CO2 emissions than standard concrete manufacturing—its carbon footprint is only about 10% of Portland cement. An alkali-activated alumina-silicate matrix serves as the binder. Geopolymer concrete does not require high-temperature processing and reduces CO2 emissions by 70% to 80% relative to traditional cement.
Using AI to Make Concrete
In 2022, Meta began working with researchers at the University of Illinois to develop low-carbon-dioxide concrete mixes for a data center. Using an artificial intelligence (AI) model, the research team quickly generated dozens of potential concrete formulas much faster than they could have on their own. Further adjustments were made in the AI model for variables such as local material availability and cold-weather conditions. The AI model determined that a mix of 57 percent cement substitution with a combination of fly ash and slag was the ideal formulation.
Fast forward to 2024 and Meta started investing in a clean concrete company to help further reduce the amount of embodied carbon—the amount of greenhouse gas emissions released in the life cycle of building materials—created by the construction of its buildings. Tech giants like Amazon and Microsoft are likewise using concrete with lower embodied carbon to hopefully reduce their carbon footprints. Microsoft recently completed several pilot programs in 2024 using a net-negative embodied carbon limestone that has 65 percent less embodied carbon than traditional concrete.
With billions of tons of used every year, concrete is absolutely essential to the development of society and the world around us. Its environmental impacts, however, especially its CO2 production, need to be mitigated; fortunately, the concrete industry is working toward that goal.
Related Content: Low-Carbon Concrete Can Fight Global Warming
“We can’t do without concrete,” says Karen Scrivener, a professor and research group leader at the Swiss Federal Institute of Technology, Lausanne (EPFL) and a concrete specialist. “But we can do without a significant amount of the emissions it produces.”
Mark Crawford is an independent writer.
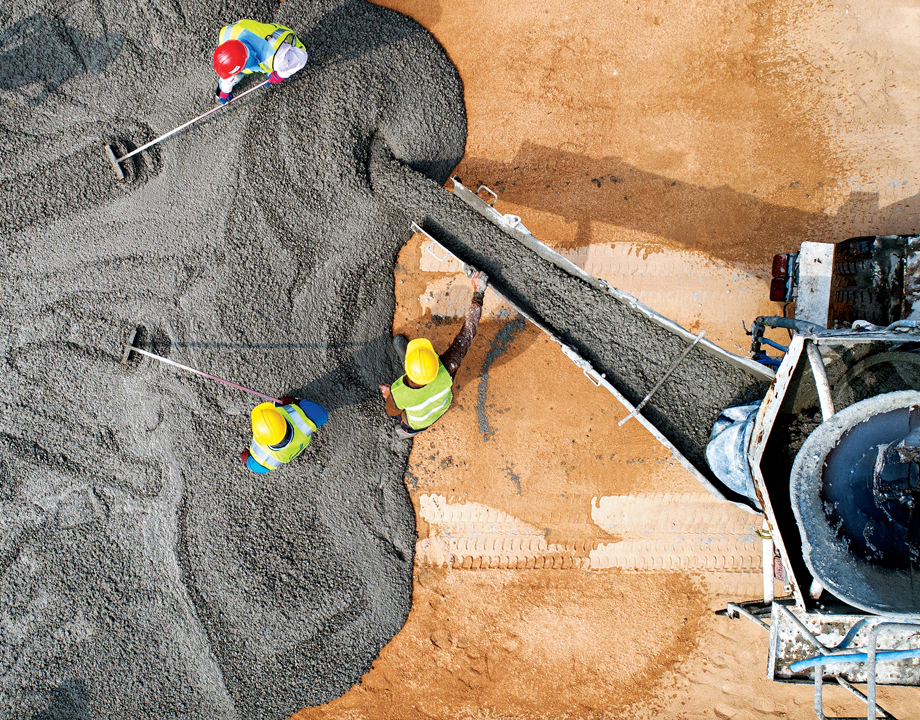
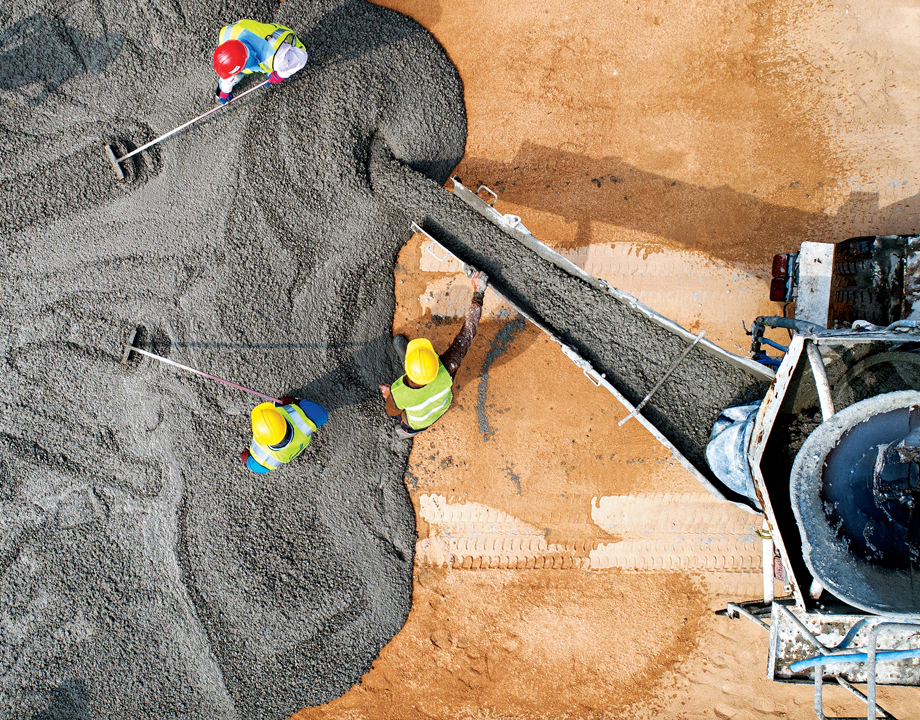