A Faster Solar Farm
A Faster Solar Farm
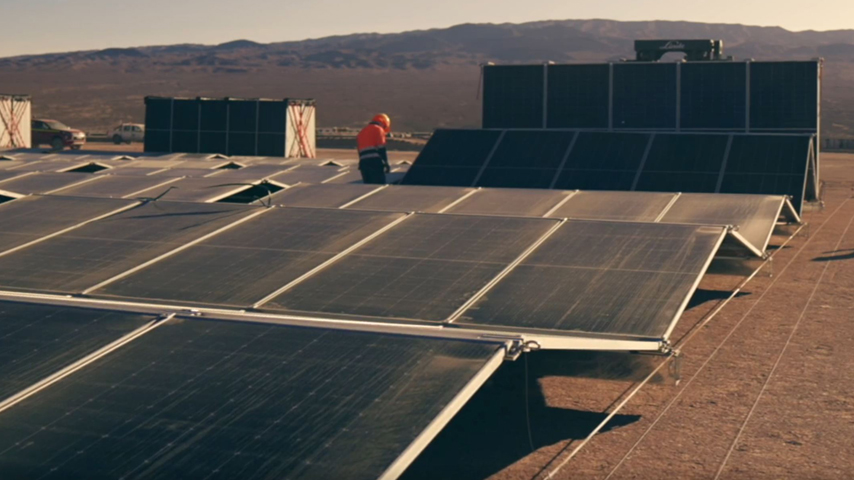
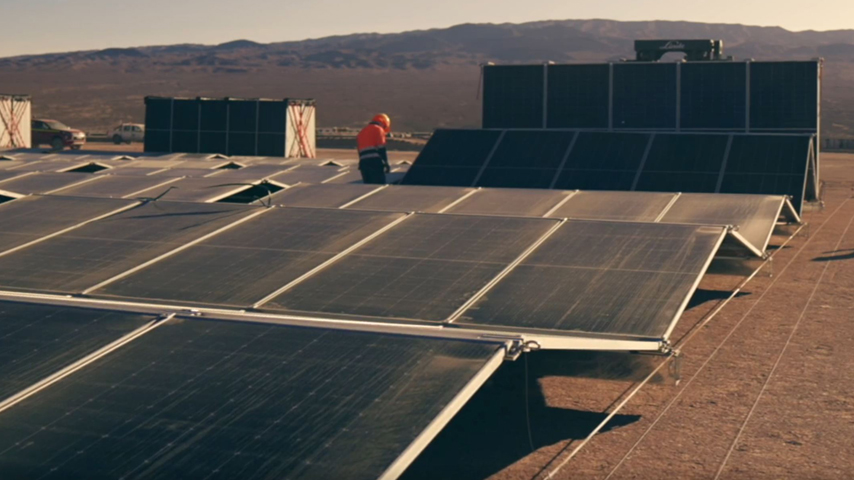
However cheap the solar cell, the cost of building has slowed the growth of solar farms. Now a company out of Australia has found a way to unfold them like an accordion.
The key component for making sun juice—the photovoltaic cell—costs less than it ever has. But the price of putting one in the sun to do its job as part of a solar farm hasn’t changed much over the same period. And that cost is slowing the expansion of solar power.
“We’ve seen a radical decline in the cost of those key components over the last two decades,” said Simeon Baker-Finch, chief product officer for the Australian company 5B. “But construction costs have remained stubbornly high.” The founders of 5B, Chris McGrath and Eden Tehan, wanted to change the way that solar farms are deployed, so they could reduce their overall costs and accelerate their proliferation.
The method for doing so came to them while they were standing in a field that had the potential to become a solar farm. “They saw two solar modules leaning up against a fence looking a little bit like the 5B Maverick as it exists today,” said Baker-Finch. Standing flat against each other, they were compact, easily stacked, and easily transported.
With the addition of a simple hinge, they might be unfolded into position at their ultimate destination.
In essence, the Maverick of 2023 is an array of panels that can be compressed and expanded like an accordion—without the polka music. Each array is made of multiple hinged racks that rest on encased concrete beams. When folded flat they fit neatly in a shipping container or on a truck.
It takes a team of just three to 10 workers—and a forklift with some custom attachments—to unload a group of Mavericks, unfold them on a field, and make them operational. The forklift attachment is key to a quick, safe, and precise deployment. The arrays are 40 meters to 50 meters long, and there might be four in a row, with the space between each row being just 600 millimeters.
Become a Member: How to Join ASME
“When you drive straight backward for 200 meters, you can't move by more than 100 millimeters side to side,” said Baker-Finch. “So that custom machine takes the cognitive load away from the driver and the operators.”
Once they’ve been unfolded, the racks sit in the sun with an angle of 10 degrees. It’s a tradeoff between a zero-degree tilt, which would be optimal for electricity generation, and a more acute angle, which would be more structurally sound and allow the panels to be more effectively cleaned when it rains.
The tent-like shapes of the zig-zagging arrays look like they’d easily catch wind and, in a hurricane, go sailing. But 5B tested the Maverick in a wind tunnel. Because of the concrete beams at the base of each panel, the arrays can easily stay put in windspeeds of more than 230 feet per second.
Winds that fast are a 700-year occurrence… in Puerto Rico. “That mass counteracts the wind uplift,” said Baker-Finch. “It stops the maverick from acting like a kite without any additional ground penetration.”
The compact shipping and speedy deployment (roughly 30 to 40 minutes for each Maverick unit) represent the bulk of the price reduction. But there are other savings that come with the system. It has digital tools that tell the operators what metrics to use in different situations, like undulating or sloping land.
Full Coverage: The Energy Transformation Collection
“The engineering process is much simplified, because you're using a standardized block instead of a whole list of potential options,” said Baker-Finch. Anyone who has built a large solar farm, as they’ve existed until now, might over order something like cabling. That won’t be an issue with the Maverick. “We can specify, exactly, to the meter, what's needed, because we have very standardized layouts.”
5B has already installed over 80 projects worldwide, with a total capacity of 70.7-MW peak—that’s 2122 Mavericks soaking in the sun right now.
But there’s plenty more to come. The company has other ways of reducing the costs of deployment in the works. Currently, much of the manufacturing of the Mavericks is subcontracted. 5B is now moving toward creating more of the arrays in house to go from CAD to production more efficiently. They’re also testing a protype for a dedicated machine that would reduce deployment from 30 minutes, with three or so operators, to five minutes, with one.
“That will radically change our ability to scale out this technology and to take on some of the gigawatt scale projects,” said Baker-Finch.
“We’ve seen a radical decline in the cost of those key components over the last two decades,” said Simeon Baker-Finch, chief product officer for the Australian company 5B. “But construction costs have remained stubbornly high.” The founders of 5B, Chris McGrath and Eden Tehan, wanted to change the way that solar farms are deployed, so they could reduce their overall costs and accelerate their proliferation.
The method for doing so came to them while they were standing in a field that had the potential to become a solar farm. “They saw two solar modules leaning up against a fence looking a little bit like the 5B Maverick as it exists today,” said Baker-Finch. Standing flat against each other, they were compact, easily stacked, and easily transported.
With the addition of a simple hinge, they might be unfolded into position at their ultimate destination.
In essence, the Maverick of 2023 is an array of panels that can be compressed and expanded like an accordion—without the polka music. Each array is made of multiple hinged racks that rest on encased concrete beams. When folded flat they fit neatly in a shipping container or on a truck.
It takes a team of just three to 10 workers—and a forklift with some custom attachments—to unload a group of Mavericks, unfold them on a field, and make them operational. The forklift attachment is key to a quick, safe, and precise deployment. The arrays are 40 meters to 50 meters long, and there might be four in a row, with the space between each row being just 600 millimeters.
Become a Member: How to Join ASME
“When you drive straight backward for 200 meters, you can't move by more than 100 millimeters side to side,” said Baker-Finch. “So that custom machine takes the cognitive load away from the driver and the operators.”
Once they’ve been unfolded, the racks sit in the sun with an angle of 10 degrees. It’s a tradeoff between a zero-degree tilt, which would be optimal for electricity generation, and a more acute angle, which would be more structurally sound and allow the panels to be more effectively cleaned when it rains.
The tent-like shapes of the zig-zagging arrays look like they’d easily catch wind and, in a hurricane, go sailing. But 5B tested the Maverick in a wind tunnel. Because of the concrete beams at the base of each panel, the arrays can easily stay put in windspeeds of more than 230 feet per second.
Winds that fast are a 700-year occurrence… in Puerto Rico. “That mass counteracts the wind uplift,” said Baker-Finch. “It stops the maverick from acting like a kite without any additional ground penetration.”
The compact shipping and speedy deployment (roughly 30 to 40 minutes for each Maverick unit) represent the bulk of the price reduction. But there are other savings that come with the system. It has digital tools that tell the operators what metrics to use in different situations, like undulating or sloping land.
Full Coverage: The Energy Transformation Collection
“The engineering process is much simplified, because you're using a standardized block instead of a whole list of potential options,” said Baker-Finch. Anyone who has built a large solar farm, as they’ve existed until now, might over order something like cabling. That won’t be an issue with the Maverick. “We can specify, exactly, to the meter, what's needed, because we have very standardized layouts.”
5B has already installed over 80 projects worldwide, with a total capacity of 70.7-MW peak—that’s 2122 Mavericks soaking in the sun right now.
But there’s plenty more to come. The company has other ways of reducing the costs of deployment in the works. Currently, much of the manufacturing of the Mavericks is subcontracted. 5B is now moving toward creating more of the arrays in house to go from CAD to production more efficiently. They’re also testing a protype for a dedicated machine that would reduce deployment from 30 minutes, with three or so operators, to five minutes, with one.
“That will radically change our ability to scale out this technology and to take on some of the gigawatt scale projects,” said Baker-Finch.
Michael Abrams is a technology writer in Westfield, N.J.