A Wireless and Self-Powered Answer to Monitor Critical Screws
A Wireless and Self-Powered Answer to Monitor Critical Screws
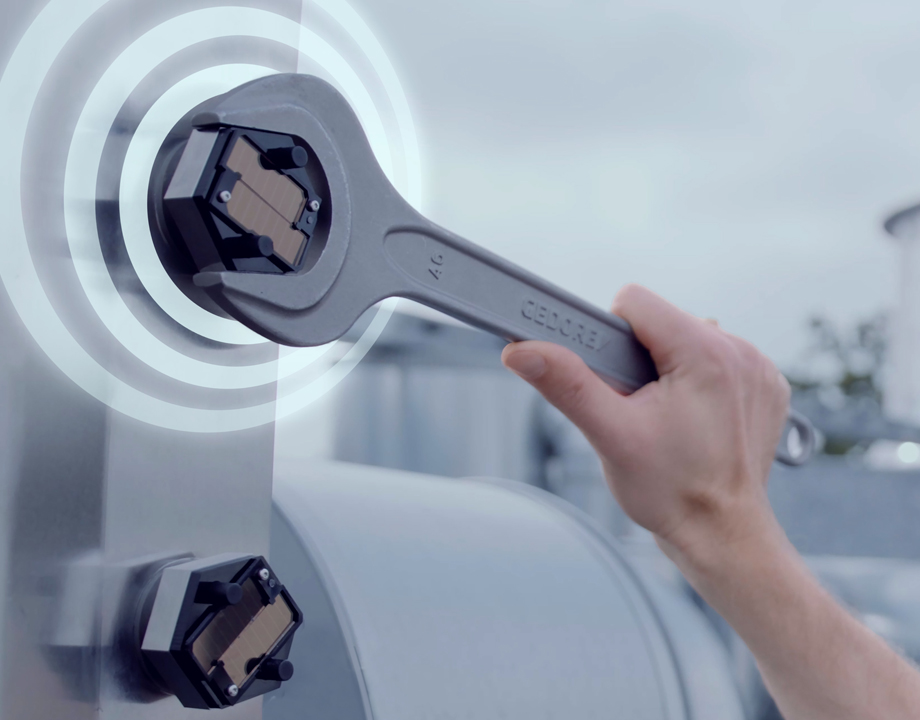
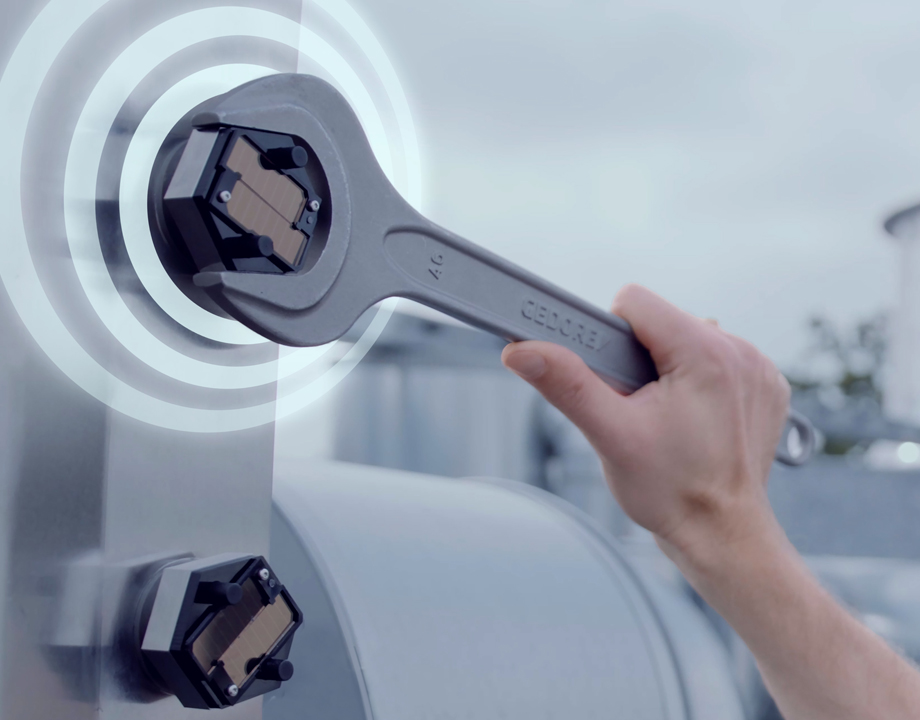
Remote monitoring of screws using a piezoresistive solution can save on maintenance costs. Image: Fraunhofer IIS
Like a canary in a coal mine, a loose screw can be an early sign of impending catastrophe. Screws are integral to machines, infrastructure and more, and that makes monitoring them a critical part of ongoing asset maintenance. Given that the U.S. infrastructure received a barely passing C- grade in 2021, every little efficiency helps.
Now, German researchers have developed a wireless monitoring system that gives early warning of loose or deteriorating screws. Q-Bo, the smart screw connection from Fraunhofer-Gesellschaft, a Germany-based applied research organization, provides an Internet of Things (IoT) sensor-based solution. It enables wireless remote monitoring of the preload force of screw connections through a self-powered piezoresistive unit.
Equally important, said Peter Spies, project manager and group manager of integrated energy supplies at the Fraunhofer Institute for Integrated Circuits IIS, the system is retrofittable. “It can be used with any existing connection with standardized screws. You don’t need to modify the screw.”
Q-Bo’s two components, a washer and electronic housing, are linked by a short cord. The washer comprises three pressure sensors built with a thin piezoresistive film.
To begin, the screw is thread through the washer and pulled tight. The head of the screw presses down on the washer and that pressure profile relays the baseline for the preload force on the screw connection. If the screw begins to loosen, that preload force will change, which shows up as changing resistance in the piezoresistive thin film. The encrypted change in baseline information relays on to a radio module in the electronic housing and routes to a base station for analysis and action.
The solution also houses a three-axis accelerometer to measure the vibration profile. “If the screw is used on a pump on a vibrating motor, or in a moving object, you can measure the vibration of the whole system during operation,” Spies said.
The electronic housing hosts the radio module, power supply and components to ensure data security.
Q-Bo uses the mioty low-power wide-area network (LPWAN) protocol to send small packets of data over long distances, up to 15 kilometers.
Reader’s Choice: Self-Powered, Wireless Sensing Platform May Take Wearable Electornics to the Next Level
“The mioty protocol is especially suited to difficult environments, where a lot of metallic objects might cause reflections to interfere with radio signals or where radio signals might be corrupted by other signals,” Spies said.“The signal is very robust so we can lose up to 50 percent of the data packages we send out and still reconstruct the information in the base station.”
In addition, the solution is scalable: One base station can monitor up to 100,000 sensors.
The system is self-powered with thermoelectric, solar or battery options available.
“The thermoelectric generator uses any thermal difference between the head of the screw and the environment to generate electrical power and power the radio transceiver and the sensor module,” Spies said.
A light-based solution with an illumination level of 500 lux (indoors), for example, will allow for data transmission every 30 minutes. A battery of capacity 230 mAh, which relays information once every hour, will last 2.6 years.
Before installation, each screw can be placed in a shielded programming box to receive an individual ID and a set of encryption keys via short-range RFID.
More for You: Reprogamming MRI to Light Up Cancer
Alternative ways of measuring changes to pressure forces, like strain gauges, exist, but they might detect problems when it’s already too late. “Strain gauges measure strain in the connection, which means you [already have] some modification [in the infrastructure],” Spies said.
Piezoelectric systems also work only when dynamic forces are involved, Spies said. “But with the piezoresistive approach, we can also measure static variation, which is extremely important with a screw connection because the change of the preload force might not be very fast, it’s usually very slow,” he added.
The supplier or the systems integrator for the smart screw solution will determine cost, but Spies expects production costs of approximately a low three-digit euro amount per system. For those worried about costs adding up for hundreds of thousands of screws in a system, not every one needs to be outfitted with the solution, Spies noted.
“If you’re using ten screws to hold up an object, measuring the preload force on three or four strategically placed screws should be enough,” he said.
Editor’s Pick: Graphene Tool to Measure Light
The thickness of the washer might be a challenge during retrofitting as would the placement of the electronic module. “Typically we place the electronic module on the screw head but if there’s not enough space, then other options can be explored,” Spies said, adding that such challenges should not deter implementation as the solution ramps up for test installations.
Gains in remote monitoring of screws can be significant for installations such as an offshore wind turbine. “For maintenance, you might need helicopters or ships and these are expensive,” he said..” By doing this in a wireless, remote way, you can save a lot of effort and maintenance costs.”
Poornima Apte is a Boston-based mechanical engineer turned technology writer. Find her at wordcumulus.com.
Now, German researchers have developed a wireless monitoring system that gives early warning of loose or deteriorating screws. Q-Bo, the smart screw connection from Fraunhofer-Gesellschaft, a Germany-based applied research organization, provides an Internet of Things (IoT) sensor-based solution. It enables wireless remote monitoring of the preload force of screw connections through a self-powered piezoresistive unit.
Equally important, said Peter Spies, project manager and group manager of integrated energy supplies at the Fraunhofer Institute for Integrated Circuits IIS, the system is retrofittable. “It can be used with any existing connection with standardized screws. You don’t need to modify the screw.”
Q-Bo’s two components, a washer and electronic housing, are linked by a short cord. The washer comprises three pressure sensors built with a thin piezoresistive film.
To begin, the screw is thread through the washer and pulled tight. The head of the screw presses down on the washer and that pressure profile relays the baseline for the preload force on the screw connection. If the screw begins to loosen, that preload force will change, which shows up as changing resistance in the piezoresistive thin film. The encrypted change in baseline information relays on to a radio module in the electronic housing and routes to a base station for analysis and action.
The solution also houses a three-axis accelerometer to measure the vibration profile. “If the screw is used on a pump on a vibrating motor, or in a moving object, you can measure the vibration of the whole system during operation,” Spies said.
The electronic housing hosts the radio module, power supply and components to ensure data security.
Q-Bo uses the mioty low-power wide-area network (LPWAN) protocol to send small packets of data over long distances, up to 15 kilometers.
Reader’s Choice: Self-Powered, Wireless Sensing Platform May Take Wearable Electornics to the Next Level
“The mioty protocol is especially suited to difficult environments, where a lot of metallic objects might cause reflections to interfere with radio signals or where radio signals might be corrupted by other signals,” Spies said.“The signal is very robust so we can lose up to 50 percent of the data packages we send out and still reconstruct the information in the base station.”
In addition, the solution is scalable: One base station can monitor up to 100,000 sensors.
The system is self-powered with thermoelectric, solar or battery options available.
“The thermoelectric generator uses any thermal difference between the head of the screw and the environment to generate electrical power and power the radio transceiver and the sensor module,” Spies said.
A light-based solution with an illumination level of 500 lux (indoors), for example, will allow for data transmission every 30 minutes. A battery of capacity 230 mAh, which relays information once every hour, will last 2.6 years.
Before installation, each screw can be placed in a shielded programming box to receive an individual ID and a set of encryption keys via short-range RFID.
More for You: Reprogamming MRI to Light Up Cancer
Alternative ways of measuring changes to pressure forces, like strain gauges, exist, but they might detect problems when it’s already too late. “Strain gauges measure strain in the connection, which means you [already have] some modification [in the infrastructure],” Spies said.
Piezoelectric systems also work only when dynamic forces are involved, Spies said. “But with the piezoresistive approach, we can also measure static variation, which is extremely important with a screw connection because the change of the preload force might not be very fast, it’s usually very slow,” he added.
The supplier or the systems integrator for the smart screw solution will determine cost, but Spies expects production costs of approximately a low three-digit euro amount per system. For those worried about costs adding up for hundreds of thousands of screws in a system, not every one needs to be outfitted with the solution, Spies noted.
“If you’re using ten screws to hold up an object, measuring the preload force on three or four strategically placed screws should be enough,” he said.
Editor’s Pick: Graphene Tool to Measure Light
The thickness of the washer might be a challenge during retrofitting as would the placement of the electronic module. “Typically we place the electronic module on the screw head but if there’s not enough space, then other options can be explored,” Spies said, adding that such challenges should not deter implementation as the solution ramps up for test installations.
Gains in remote monitoring of screws can be significant for installations such as an offshore wind turbine. “For maintenance, you might need helicopters or ships and these are expensive,” he said..” By doing this in a wireless, remote way, you can save a lot of effort and maintenance costs.”
Poornima Apte is a Boston-based mechanical engineer turned technology writer. Find her at wordcumulus.com.