Artemis Transcends Apollo
Artemis Transcends Apollo
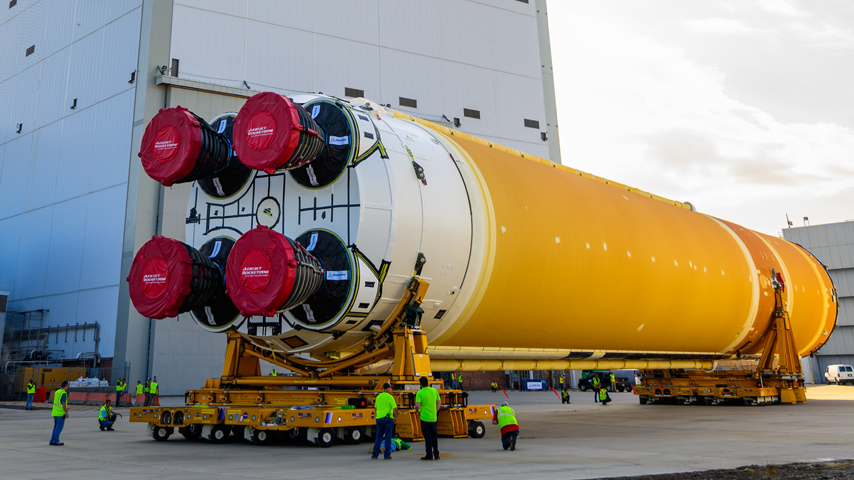
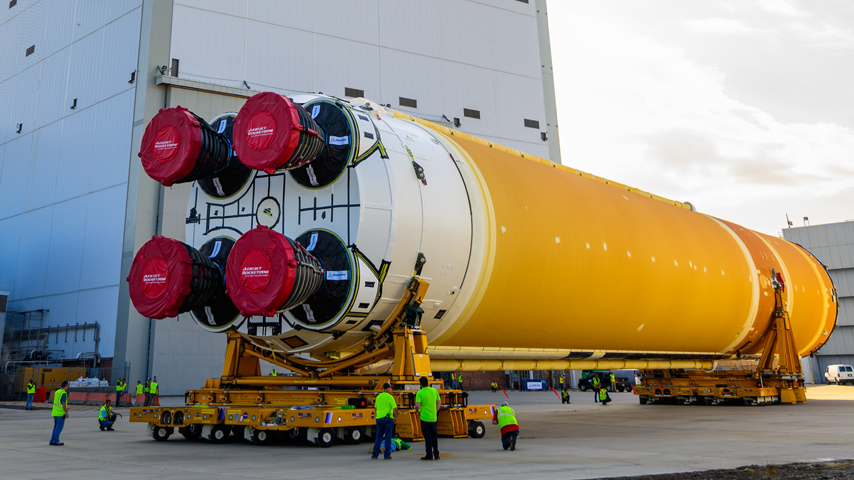
The Artemis mission is set for takeoff, with new lunar exploration and discovery missions right around the corner, propelled by incredible feats of engineering.
The following is an excerpt from the January 2025 Mechanical Engineering cover story, “Artemis Transcends Apollo.” The fully digital issue is available to ASME members at magazine.asme.org.
The middle of July is not the best time to stand on a tarmac in New Orleans, given the oppressive heat. So, NASA chose the dawn of July 16, 2024, the 55th anniversary of the Apollo 11 launch, to gather a crowd at its Michoud Assembly Facility to watch as crews rolled out the 212-foot-long core stage of its Space Launch System (SLS).
The rocket core stage is the largest NASA has ever built and it is an integral part of the Artemis program, which is working toward landing astronauts on the moon as early as this year. The event marked a major milestone for Artemis: The first time since the Apollo program that a fully assembled moon rocket stage for a crewed mission has rolled out of Michoud.
From Michoud—one of the largest manufacturing facilities on the planet—the stage would make a 900-mile journey by barge to the Kennedy Space Center in Florida, ready to be joined with the other SLS components.
“For over 60 years, Michoud has been America’s rocket factory,” said NASA’s associate administrator Jim Free to the crowd assembled at Michoud, noting that this latest product was the only rocket capable of launching astronauts into deep space. “The work does not end here. We have big plans for the moon and we’re going to need more SLS rockets.”
Much has changed in the 55 years since NASA last had big plans for the moon. Technology is the most obvious, having advanced greatly from the days of slide rulers and handwritten code. The purpose has changed as well. The Space Race was a scramble to be first to plant a flag on the moon. The Artemis program, on the other hand, will not only carry astronauts back to the moon but also aim to establish a permanent presence on the lunar south pole. Vital research carried out there could eventually help send humans to Mars.
Check This Out: Axiom Space designs the most advanced spacesuit for Artemis III
But getting back to the moon is going to require quite the rocket. The design of SLS was unveiled in 2011, and the first variant, called Block 1, launched the uncrewed Artemis I mission around the moon in 2022. Four more missions are expected to launch before 2030, with Artemis II gearing up to send a crew of four astronauts to complete a lunar flyby in April 2026—just ahead of the United States’s 250th anniversary. Artemis III is scheduled for mid-2027 and is set to be NASA’s first crewed lunar landing since 1972.
Building upon the engineering feats of the past six decades, more than 1,100 companies across the United States and at every NASA facility are supporting the program in some fashion. Although many of the same contractors, from Boeing to Lockheed Martin to Aerojet Rocketdyne, are developing solutions for Artemis much as they did on Apollo, they’re using vastly different tools, solutions, and engineering knowhow.
Generating the kick
The 212-foot-tall, 27.6-foot-diameter SLS core stage is the largest rocket core stage NASA has ever built. Boeing is leading the core stage’s development, design, testing, and integration. Housed within 10 barrel sections, four dome sections and nine rings, the core stage has five major components: a liquid hydrogen (LH2) tank, a liquid oxygen (LOX) tank, an engine section, the intertank, and the forward skirt. This portion of the SLS is the rocket’s backbone, both supporting and carrying the thrust generated by the dual five-segment solid rocket boosters from Northrop Grumman and four RS-25 engines from Aerojet Rocketdyne that are mounted to the engine and intertank sections.
Each booster is 12 feet in diameter and weighs 1.6 million pounds. Combined, the two boosters will provide a maximum of 3.6 million pounds of thrust during launch, which accounts for more than 75 percent of the rocket’s thrust during the first two minutes of flight.
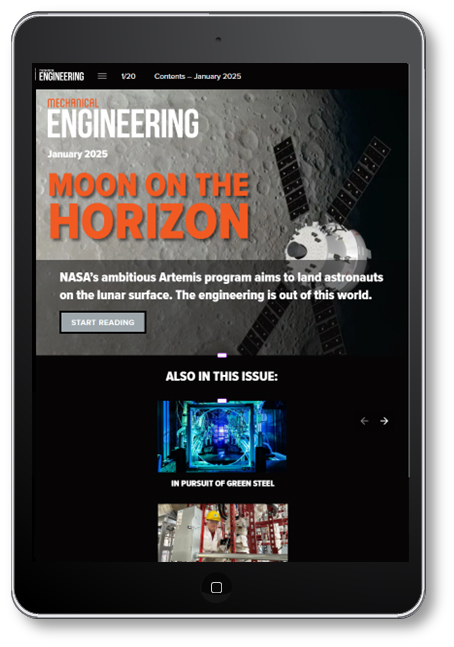
We've Gone Digital
All four engines use a staged-combustion cycle, which will require more than 733,000 gallons of cryogenic LH2 and LOX housed in those two tanks, insulated with the help of an orange spray-on foam on the rocket’s exterior. They’ll burn propellant at the rate of 1,500 gallons per second.
“I still believe this LH2, LOX staged-combustion machine is one of the greatest engineering marvels that’s ever been concocted—and of course, it was conceived in the 1970s,” said Mike Lauer, RS-25 deputy program manager at Aerojet Rocketdyne. “We have 6,000 °F hot gas in the main combustion chamber and we have -400 °F hydrogen less than an inch away. It is just amazing heat transfer that is involved in an engine like that.”
Streamlining production
Although all eyes are on the upcoming Artemis II mission, the multiyear nature of building these mammoth rockets means that the Stennis Space Center—NASA’s premier rocket testing facility in Mississippi, about 40 miles from Michoud—is already working on the launch system for a potential Artemis VIII.
“At Stennis Space Center, we have Artemis III and IV engines ready to go as well. Then what we’ve been working on is the next evolution of the rocket engine for Artemis V and subsequent missions,” Lauer said. Hot fire tests were held at Stennis in early 2024 for Aerojet Rocketdyne’s new restart engine, which is similar to the space shuttle engines but is more affordable.
Of course, advanced manufacturing and robotics are playing a vital role in improving affordability and production speed, as is 3D modeling—a lot of the drawings from the recent Space Shuttle era were in fact still hand drawn, Lauer noted.
Podcast: Space Exploration and the Engineering Workforce
“We’ve done a whole lot of things to evolve it to this vehicle so we can make more of them and faster for future Artemis missions,” he added. “We have a whole bunch of 3D-printed metal parts on the restart engines. We’ll take what was previously a bunch of parts welded all together, subtractively manufactured, and we will print it.”
3D models are also being used for performance, behavioral, structural, and thermal analysis, Lauer said. Computing advances allow for the manufacture of hardware to much tighter tolerances. The exploration upper stage (EUS), which will provide the thrust for inserting crewed capsules and other payload into lunar orbit for Artemis IV onward, was digitally engineered from the ground up, said Matt Stites, senior director and chief engineer of the Space Launch System program at Boeing. That allowed the team to move through the design phases much quicker.
“From a computing power perspective, what we can do today with analysis is very impressive and allows us to get much more accurate, higher fidelity models of what the rocket will see in flight and how it’ll react,” Stites said. “It allows us to go in and mitigate any potential issues before they’re discovered during flight testing.”
Want to read more? Be sure to check out the complete story at magazine.asme.org.
Louise Poirier is senior editor.
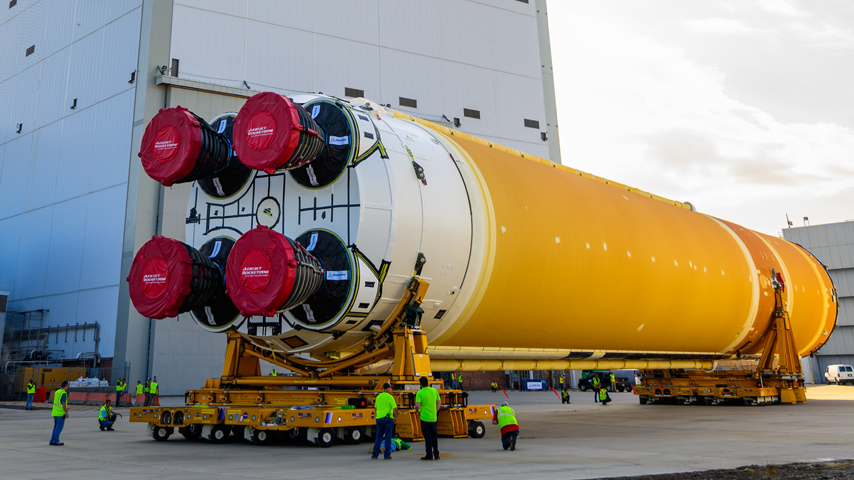
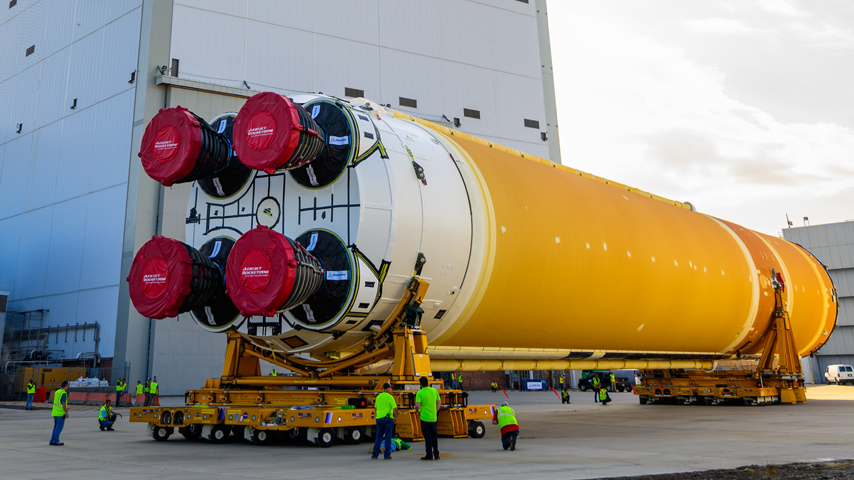