You’d be Hard Pressed to Find a More Dazzling ASME Landmark
You’d be Hard Pressed to Find a More Dazzling ASME Landmark
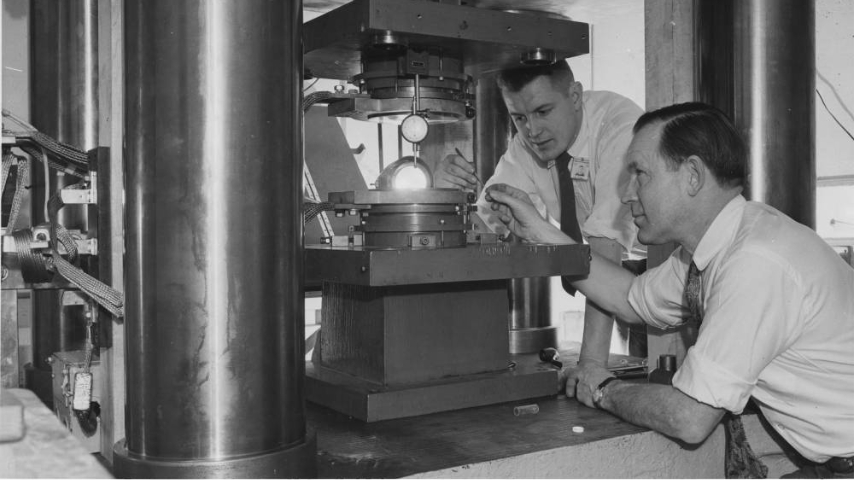.jpg?width=854&height=480&ext=.jpg)
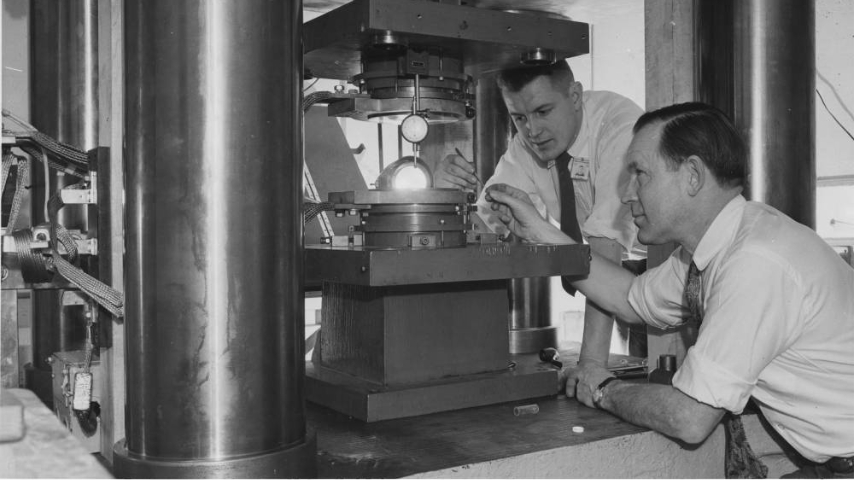.jpg?width=854&height=480&ext=.jpg)
This ASME Landmark made diamonds using high heat and great pressure, proving, for the first time, that synthetic, man-made diamonds were really possible.
Just as soon as scientists decided that diamonds form from carbon under very high heat and pressure, researchers worked overtime to “make” the much sought-after gemstones. But it wasn’t until General Electric (G.E.) Research Laboratories announced in 1955 that it had achieved the first reproducible process, that the world agreed that humans were able to create the stone that up until that day was only formed in the Earth’s mantle and delivered to the surface by volcanic eruptions.
It was on December 16, 1954, that the engineer H. Tracy Hall produced the first verifiable synthetic diamond using reproducible means. In the article, “Man-Made Diamonds,” published in Nature on July 9, 1955, G.E.’s Hall, along with Francis P. Bundy, Herbert M. Strong, and Robert H. Wentorf detailed the workings of the apparatus.
In 1998 the ultra high-pressure apparatus for the production of diamonds became an ASME Landmark. And it’s a “first” according to the Guiness World Records that described it as a “donut-sized chamber surrounded by conical pistons.” Today, the Museum of Innovation and Science (miSci) in Schenectady, N.Y., houses papers and artifacts from the Diamond Team and G.E. Research. A group of papers and photos can be accessed online. According to Chris Hunter, miSci’s vice-president of collections and exhibitions, the museum periodically hosts a display dedicated to man-made diamonds, and it maintains a small display in the archives.
The process that would eventually generate millions in revenue for G.E. is not without controversy. The real story is as astonishing as the high-pressure high temperature (HPHT) material that Hall, a National Inventors Hall of Fame inductee, produced. According to the Los Angeles Times in Hall’s 2008 obituary, when the scientist joined the “Superpressure” project, G.E. just allocated $125,000 to buy a massive press that was capable of generating 1.6 million pounds of pressure per square inch in a tiny, confined space. But Hall, convinced of his own process, built a pressure chamber that he called the “half-belt” that the paper described as a “35-year-old Watson-Stillman press that leaked so much water from its hydraulics that he had to wear rubber boots while working with it.”
According to the obituary, “When he envisioned a better pressure chamber, the company refused to come up with the $1,000 it would require and refused him official time in the G.E. machine shop to build it. He persuaded a friend in the shop to do the work during off hours, and a former supervisor persuaded the company to purchase the expensive carboloy (tungsten carbide dispersed in cobalt) that he needed.”
According to Lydia Pyne in “Genuine Fakes: How Phony Things Teach Us About Real Stuff,” Hall added two diamond seed crystals to iron sulfide and placed everything in a cylindrical graphite heater. “He placed thin disks of tantalum metal between the sample and the belt anvils to facilitate current to heat the sample.” The temperature of the chamber reached 1,600 °C (2,912 °F) and it was put under 100,000 atmospheres of pressure.
Hall ran a final test with his device on Dec. 16, 1954. On New Year’s Eve, Hugh H. Woodbury used Hall’s equipment, and the results were reported to G.E. officials. Hall’s superiors suspected that the chemist had exaggerated his findings. But Hall was ushered out of the building and the experiment was repeated in front of it with the same result. So on Feb. 14, 1955, the company announced that it had created the first synthetic diamonds.
Discover the Benefits of ASME Membership
Given the results, G.E. gave Hall a salary bump of $1,000 and gave him a $10 savings bond, wrote Pyne. Hall left G.E. to take a research position at Brigham Young University and eventually started the company MegaDiamond, which became G.E.'s biggest domestic competitor in the diamond-making business. Fortunately, for everyone involved the process was established, it worked, and synthetic diamonds, and the industry it spawned, were introduced to the world.
According to Sally Magana, research scientist and senior manager of identification at GIA in Carlsbad, Calf., industry still uses naturally occurring diamonds in their industrial applications. “Gem and near-gem diamonds are a fraction of the total diamonds recovered from mining operations and the remainder is generally moved towards industrial applications,” she explained. The chemical engineer explained that the percentage of industrial diamonds that are naturally sourced has decreased over the years, however, as manufactured diamonds can be better customized for specific applications such as sensing magnetic fields to searching for new subatomic particles.
Magana further explained that the vast majority of natural diamonds have high amounts of nitrogen impurities (classified as type I). “They can also have a variety of structural impurities and inclusions,” she explained. These “flaws” can impart a wide range of beautiful colors—red, green, blue, pink, yellow—and can make a diamond quite beautiful and memorable. The inclusions can be other minerals that were incorporated within the diamond and then were brought from deep in the Earth up to the surface. “Geologists use these ‘hitchhiking minerals’ to discover the otherwise unattainable secrets of what is happening far below us and deep in the Earth,” Magana added. “These ‘flaws’ make each natural diamond unique with its own story to tell.”
But for laboratory-grown diamonds the story is quite different. “For gem quality, it is generally advantageous to reduce flaws (whether it is impurities or structural imperfections) which is why many laboratory-grown diamonds, especially CVD grown, go through post-growth treatments to improve the color and clarity,” Magana explained. Chemical vapor deposition, or CVD, takes place at low pressures, with a vapor of carbon-rich gas being deposited on a surface.
Another ASME Landmark: The Edison Phonograph Was the First Time Machine
Looking at an old G.E. press release, the company summed up the achievement as a “climax to a 125-year effort to duplicate nature’s hardest and most glamorous substance.” As for the apparatus that started it all, according to Hunter, it’s believed to have been “demolished a few years back” and the space renovated for a high-voltage laboratory. What has lived on, however, is the process of extreme pressures coupled with high temperatures to produce synthesized materials with advanced properties undreamed of in 1955.
Cathy Cecere is membership content program manager.
It was on December 16, 1954, that the engineer H. Tracy Hall produced the first verifiable synthetic diamond using reproducible means. In the article, “Man-Made Diamonds,” published in Nature on July 9, 1955, G.E.’s Hall, along with Francis P. Bundy, Herbert M. Strong, and Robert H. Wentorf detailed the workings of the apparatus.
In 1998 the ultra high-pressure apparatus for the production of diamonds became an ASME Landmark. And it’s a “first” according to the Guiness World Records that described it as a “donut-sized chamber surrounded by conical pistons.” Today, the Museum of Innovation and Science (miSci) in Schenectady, N.Y., houses papers and artifacts from the Diamond Team and G.E. Research. A group of papers and photos can be accessed online. According to Chris Hunter, miSci’s vice-president of collections and exhibitions, the museum periodically hosts a display dedicated to man-made diamonds, and it maintains a small display in the archives.
Diamonds are forever
The process that would eventually generate millions in revenue for G.E. is not without controversy. The real story is as astonishing as the high-pressure high temperature (HPHT) material that Hall, a National Inventors Hall of Fame inductee, produced. According to the Los Angeles Times in Hall’s 2008 obituary, when the scientist joined the “Superpressure” project, G.E. just allocated $125,000 to buy a massive press that was capable of generating 1.6 million pounds of pressure per square inch in a tiny, confined space. But Hall, convinced of his own process, built a pressure chamber that he called the “half-belt” that the paper described as a “35-year-old Watson-Stillman press that leaked so much water from its hydraulics that he had to wear rubber boots while working with it.” According to the obituary, “When he envisioned a better pressure chamber, the company refused to come up with the $1,000 it would require and refused him official time in the G.E. machine shop to build it. He persuaded a friend in the shop to do the work during off hours, and a former supervisor persuaded the company to purchase the expensive carboloy (tungsten carbide dispersed in cobalt) that he needed.”
According to Lydia Pyne in “Genuine Fakes: How Phony Things Teach Us About Real Stuff,” Hall added two diamond seed crystals to iron sulfide and placed everything in a cylindrical graphite heater. “He placed thin disks of tantalum metal between the sample and the belt anvils to facilitate current to heat the sample.” The temperature of the chamber reached 1,600 °C (2,912 °F) and it was put under 100,000 atmospheres of pressure.
Hall ran a final test with his device on Dec. 16, 1954. On New Year’s Eve, Hugh H. Woodbury used Hall’s equipment, and the results were reported to G.E. officials. Hall’s superiors suspected that the chemist had exaggerated his findings. But Hall was ushered out of the building and the experiment was repeated in front of it with the same result. So on Feb. 14, 1955, the company announced that it had created the first synthetic diamonds.
Discover the Benefits of ASME Membership
Given the results, G.E. gave Hall a salary bump of $1,000 and gave him a $10 savings bond, wrote Pyne. Hall left G.E. to take a research position at Brigham Young University and eventually started the company MegaDiamond, which became G.E.'s biggest domestic competitor in the diamond-making business. Fortunately, for everyone involved the process was established, it worked, and synthetic diamonds, and the industry it spawned, were introduced to the world.
Diamonds today
According to Sally Magana, research scientist and senior manager of identification at GIA in Carlsbad, Calf., industry still uses naturally occurring diamonds in their industrial applications. “Gem and near-gem diamonds are a fraction of the total diamonds recovered from mining operations and the remainder is generally moved towards industrial applications,” she explained. The chemical engineer explained that the percentage of industrial diamonds that are naturally sourced has decreased over the years, however, as manufactured diamonds can be better customized for specific applications such as sensing magnetic fields to searching for new subatomic particles.Magana further explained that the vast majority of natural diamonds have high amounts of nitrogen impurities (classified as type I). “They can also have a variety of structural impurities and inclusions,” she explained. These “flaws” can impart a wide range of beautiful colors—red, green, blue, pink, yellow—and can make a diamond quite beautiful and memorable. The inclusions can be other minerals that were incorporated within the diamond and then were brought from deep in the Earth up to the surface. “Geologists use these ‘hitchhiking minerals’ to discover the otherwise unattainable secrets of what is happening far below us and deep in the Earth,” Magana added. “These ‘flaws’ make each natural diamond unique with its own story to tell.”
But for laboratory-grown diamonds the story is quite different. “For gem quality, it is generally advantageous to reduce flaws (whether it is impurities or structural imperfections) which is why many laboratory-grown diamonds, especially CVD grown, go through post-growth treatments to improve the color and clarity,” Magana explained. Chemical vapor deposition, or CVD, takes place at low pressures, with a vapor of carbon-rich gas being deposited on a surface.
Another ASME Landmark: The Edison Phonograph Was the First Time Machine
Looking at an old G.E. press release, the company summed up the achievement as a “climax to a 125-year effort to duplicate nature’s hardest and most glamorous substance.” As for the apparatus that started it all, according to Hunter, it’s believed to have been “demolished a few years back” and the space renovated for a high-voltage laboratory. What has lived on, however, is the process of extreme pressures coupled with high temperatures to produce synthesized materials with advanced properties undreamed of in 1955.
Cathy Cecere is membership content program manager.
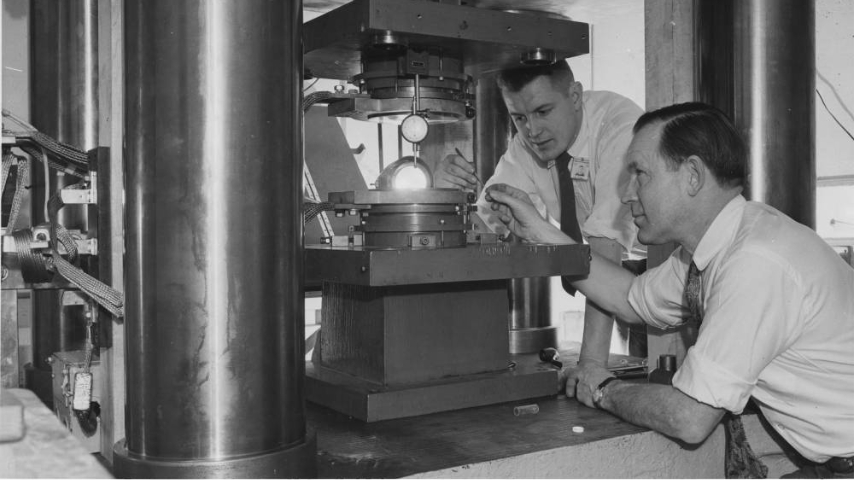.jpg?width=854&height=480&ext=.jpg)
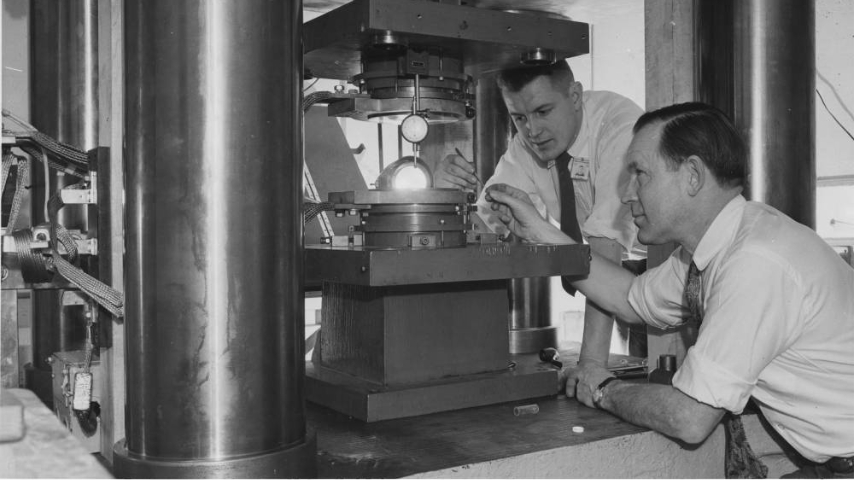.jpg?width=854&height=480&ext=.jpg)