Below and Beyond for Geothermal's Frontier
Below and Beyond for Geothermal's Frontier
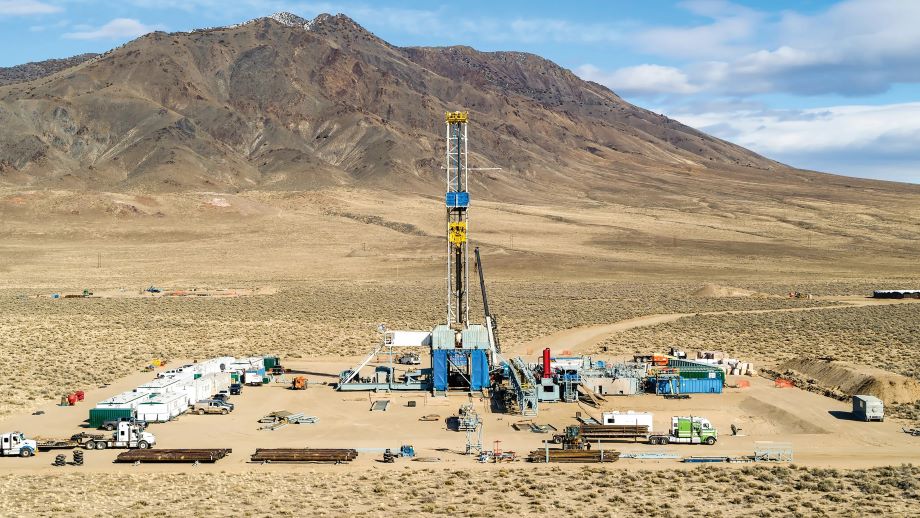
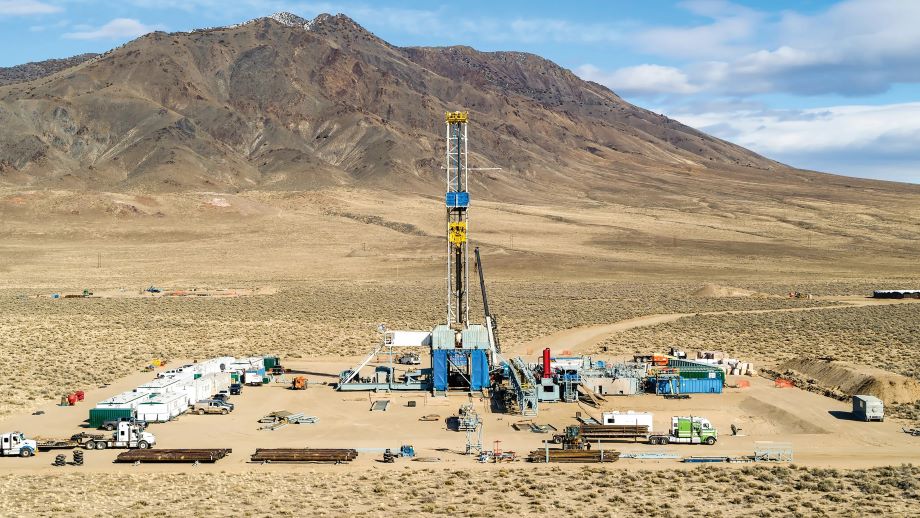
A new generation of startups is developing the drilling technology needed to reach rocks hot enough to provide clean, sustainable power whenever we need it.
There’s a genre of movie about would-be oil barons drilling a well in an unproven province. The roughnecks keep adding pipe, the drill bit grinds through ever more rock, all seems lost, and then—a rumble. The ground shakes. And out of the top of the well spouts a fountain of hot, black oil.
In the movies—and in real life until recently—the focus was on the oil. And for good reason: Petroleum was the lifeblood of the 20th century and the fuel that made great fortunes. Today, in this carbon-constrained century, the heat is equally sought after or even more so.
It’s true that within the first hundred feet of the surface, the temperature matches the average surface temperature. Past that point, though, and the temperature starts to rise—around 70 °F per mile of depth, or more where geological conditions are right. The first mile is not terribly useful unless you are on top of a volcanic feature. The Geysers plant in northern California has been producing electricity for more than 60 years and now has a capacity of more than 1.5 GW. Iceland is famous for tapping its volcanic fields for both heat and power, and Kenya relies on geothermal heat from an extinct volcano to supply more than 40 percent of its electricity.
Beyond those sure-thing sites, however, geothermal prospecting has been an iffy proposition. Drilling miles deep into the Earth’s crust brought all sorts of uncertainty, and at a steep cost.
“If you look historically, across the global average of geothermal, about 40 percent of the wells are failures,” said Jack Norbeck, cofounder and chief technology officer of Fervo, a Houston-based geothermal power company. “When drilling makes up 50 percent of your capex costs and nearly half are failures—that’s not a recipe for success.”
Norbeck is one of a new cohort of entrepreneurs looking for ways to drill deeper, cheaper, and more successfully than before by borrowing methods honed by the oil and gas industry.
“We want to go from a 60 percent success rate to a 100 percent real success rate—and that has very much been proven in the oil and gas industry,” he said.
Fervo and startups like it are bringing—or will be bringing within the year—enhanced geothermal power systems online that promise sustainable, zero-carbon electricity that is not dependent on the time of day or the local weather. The hope is that by capitalizing on more than a century of petroleum-industry expertise, geothermal wells can operate reliably and relatively inexpensively well into the next century.
Another ongoing project is more ambitious. Fervo has drilled 15 wells near Milford in southwest Utah. By the time it reaches full capacity in 2028, the Cape Station project is expected to produce 400 MW, on par with a coal-fired power plant.
The technologies they’re using to drill those wells are the same ones developed and refined by the petroleum industry to exploit unconventional deposits in shale formations, which has transformed the American oil and gas sector. Crews at the Nevada site, for instance, drilled down to something like 8,000 feet and then steered the bit until it ran horizontally for thousands more feet. Explosive charges placed in the drilled-out rock fractured the geologic formation, and high-pressure water forced minuscule grains of proppant into the fractures to keep them open.
The big difference between a hydrocarbon well and Fervo’s approach is that Fervo uses a pair of wells, one for injection and one for production. Water pumped down the injection well flows through the reservoir of fractures, absorbing heat before it’s pumped up the production well to the surface.
“After you pass that hot fluid through the power generation cycle, it comes out cold,” Norbeck said, “and you can reinject that to basically create a cycle.”
Just how far the two wells are from each other is critical. They must be spaced close enough to guarantee a high flow rate from the injection well to the production well, but far enough away from each other that they’re not short circuiting the system and cooling it off too quickly.
“It’s not a simple calculation,” Norbeck said. In fact, the equation that gives rise to that number is proprietary.
The shale revolution also required oil and gas companies to drill many more wells than was customary for conventional deposits. As a necessity, they’ve improved their operations and shortened drilling time considerably.
“It used to take 30 or 40 days to drill a well,” Norbeck said, “and now they’re getting it down to where it takes less than 10 days.” Geothermal companies are applying those learnings to their own operations to keep costs low.
Listen to the Podcast: Geothermal in Texas
Fervo is improving on traditional geothermal in other areas, too. For instance, geothermal plants that exploit volcanic features receive superheated steam from their wells; it’s cleaned and descaled and then sent through a steam turbine. The fluid then goes to an evaporative cooling system where as much as 50 percent of it is lost to the atmosphere. New water must be injected, or the wells will run dry.
Instead of a steam turbine, Fervo uses an Organic Rankine Cycle (ORC) turbine to produce power at the surface. An ORC sends the hot water to a heat exchanger to vaporize a refrigerant. That refrigerant goes to the turbine while the water, now cooled, is pumped back into the injection well.
The advantages are many. No water is lost to evaporation, no pressure is lost in the wells, the turbine spins through the entire power cycle, and the water stays in a single phase and so requires no descaling. Most importantly, the ORC allows rock as cool as 200 °C to generate electricity.
One drawback is that plant efficiency is in the 15 to 20 percent range, well below the 32 percent of a coal-fired power plant. “They are lower efficiency, but the fuel source is free,” Norbeck said. “That’s the trick. That’s how to make it economic.”
“What happens is a lot of your fractures go off in different directions, and only a certain percentage of them go from one to the other,” said Cook, who worked for Shell in oilfield services, including a stint as vice president of Wells Technology. “If you’ve got a single point, which is what we do, then any line you draw is connected to your point.”
Sage’s business model is different from Fervo’s. While Fervo is looking to replicate baseload power, Sage is developing something more akin to a pumped energy storage reservoir flipped upside down, though the company has to pressurize the well rather than allow gravity to do the work.
ASME Landmarks: Ingenuity Turned the Geysers into a Powerhouse
“Let’s say we want a 100,000-barrel fracture network,” Cook explained. “We create that network with that one well and then we cycle 10,000 barrels at a time. We use that fracture like a lung: we fill it up, it breathes in, and then it compresses, breathes out.”
Just as your lungs never collapse totally, a Sage well will stay about 80 percent full at all times. The remaining 20 percent is hot, pressurized water for use in power production. With the well capped, the pressurized water—3,800 psi at Sage’s test site—sits there waiting till it’s needed.
At the surface, a Pelton turbine—“a higher-pressure Pelton than has ever been built before,” Cook said—will turn that pressure into electricity. And after the water has turned the Pelton turbine, it runs through an ORC to turn the heat to electricity as well.
“This is what's unique about us, we’re the only ones that are recovering this pressure component,” Cook said. “Everybody else is just venting it off.”
Sage is deliberately using high pressure for more than just storage. Keeping the fractures open allows for easy exchange of hot water with denser cold water, so the hot water is available as needed at the surface.
Cook said the company’s emphasis was on not inventing anything new. “That’s sort of our philosophy: to try to use off-the-shelf proven technology and just arrange it differently than what’s ever been done before,” Cook said. The first such arrangement—Sage’s three-megawatt demo plant in Texas—should be fully operational in the first quarter of 2025.
After that, the dream is to put in as many wells as financial resources allow.
“There are over four terawatts of geothermal resources, mainly from Texas to the west,” Cook said. “If you wanted to go just pure geothermal, you could do it—you could do the whole grid with geothermal if you wanted to. We would need 2,500 wells. The oil and gas industries drill 20,000 wells a year, so there’s a lot of surplus capacity in the oil and gas industry. We could put a gigawatt in fairly quickly with the oil and gas equipment currently sitting on the sidelines.”
“It’s a slower process,” said Jeanine Vany, a geoscientist and Eavor’s vice president of corporate affairs. “That’s why when you look at our well construction profiles, you’ll see many more wells being drilled to get the same megawatts—thermal or electric—out of the ground. But it also means that we have the ability to be truly scalable, and truly flexible, and truly reliable.”
Best of all, Vany said, instead of looking for sites with hot rock close to the surface that can be fracked, “we are looking for pretty much standard geothermal gradients, with sort of boring rock, no special characteristics.”
In addition to using proven petroleum-industry technology, Eavor has eliminated the need for steel casing, lining the length of the well with a proprietary rock pipe sealant instead. Once that’s done, crews fill the network of pipes with roughly enough water to fill an Olympic-size swimming pool.
See the Infographic: Geothermal Energy is Heat Under Our Feet
The water then circulates passively, free of pumps—it’s essentially a giant thermosiphon.
“The water that we put into that set of pipes is the water that goes around and around forever,” Vany said. “We have hardly any operating costs because we don’t have big plants that move water around.”
Like Sage and Fervo, Eavor will use an ORC to generate electricity, but the company is also looking for use cases that can apply the heat directly. Its first set of four wells (which the company calls “Eavor Loops”) in Geretsried, Germany, about 10 miles south of Munich, will generate 8 MW of electricity but also provide 64 MW of process heat when fully complete in 2027.
“We have a follow-on project in Hanover,” Vany said. “It is a city of half a million people, and we have a heat purchase agreement with the Enercity utility. They are looking to shut down their coal-fired fed heat and plug in geothermal.”
One challenge is the drill bit. Today’s bits must be pulled from the hole and replaced every 100-or-so meters—a days-long affair.
Quaise Energy is working to build a better drill bit by replacing the grinding teeth of a conventional bit with a gyrotron borrowed from the fusion industry. A 1 MW gyrotron would produce millimeter waves that, with the assistance of a metallic waveguide, would vaporize anything in its path.
“We don’t have contact with the rock, so there’s actually no wear and tear on the parts,” said Henry Phan, Quaise’s vice president of engineering and a 19-year veteran with oil services giant Schlumberger. Instead, the gyrotron will turn the rocks into a kind of ash-like flake which will be lifted out of the hole with a purge gas.
Quaise estimates their drilling speed to be three to five meters an hour, without any downtime needed to change a bit.
Gyrotrons are commercial products available to anyone with the money to buy them, but the sticking point is building them robustly enough for field applications.
“This equipment is made for laboratory applications,” Phan said. “That’s one obstacle that we have to overcome: making this thing where we can scale up without being so expensive.”
Quaise has already demonstrated that they can drill a small hole with the gyrotron—in the lab. The company has plans to drill a handful of 100-meter holes in the field by mid-2025.
More Podcasts: Engineering Geothermal Heat Pumps
“And we will continue to push that into next year to go an additional length as well,” Phan said. The company hopes to have a pilot hole to full depth within three years.
If successful—and if it can keep costs down—its method could be used for the Fervos, Sages, and Eavors of the world as well.
“The Holy Grail is what Quaise is working on, to be able to drill into the center of the Earth cheaply with this millimeter wave technology,” said Eavor’s Jeanine Vany. “We definitely could see ourselves ultimately using something like that to drill down.”
Michael Abrams is a technology writer in Westfield, N.J.
In the movies—and in real life until recently—the focus was on the oil. And for good reason: Petroleum was the lifeblood of the 20th century and the fuel that made great fortunes. Today, in this carbon-constrained century, the heat is equally sought after or even more so.
It’s true that within the first hundred feet of the surface, the temperature matches the average surface temperature. Past that point, though, and the temperature starts to rise—around 70 °F per mile of depth, or more where geological conditions are right. The first mile is not terribly useful unless you are on top of a volcanic feature. The Geysers plant in northern California has been producing electricity for more than 60 years and now has a capacity of more than 1.5 GW. Iceland is famous for tapping its volcanic fields for both heat and power, and Kenya relies on geothermal heat from an extinct volcano to supply more than 40 percent of its electricity.
Beyond those sure-thing sites, however, geothermal prospecting has been an iffy proposition. Drilling miles deep into the Earth’s crust brought all sorts of uncertainty, and at a steep cost.
“If you look historically, across the global average of geothermal, about 40 percent of the wells are failures,” said Jack Norbeck, cofounder and chief technology officer of Fervo, a Houston-based geothermal power company. “When drilling makes up 50 percent of your capex costs and nearly half are failures—that’s not a recipe for success.”
Norbeck is one of a new cohort of entrepreneurs looking for ways to drill deeper, cheaper, and more successfully than before by borrowing methods honed by the oil and gas industry.
“We want to go from a 60 percent success rate to a 100 percent real success rate—and that has very much been proven in the oil and gas industry,” he said.
Fervo and startups like it are bringing—or will be bringing within the year—enhanced geothermal power systems online that promise sustainable, zero-carbon electricity that is not dependent on the time of day or the local weather. The hope is that by capitalizing on more than a century of petroleum-industry expertise, geothermal wells can operate reliably and relatively inexpensively well into the next century.
Breaking rocks
Reliability is a big selling point for geothermal power. A Google server facility Nevada is purchasing power from Fervo’s 3.5-MW geothermal plant that started operations in 2023. Unlike power from wind or solar farms, the electricity from the geothermal power plant is online around the clock.Another ongoing project is more ambitious. Fervo has drilled 15 wells near Milford in southwest Utah. By the time it reaches full capacity in 2028, the Cape Station project is expected to produce 400 MW, on par with a coal-fired power plant.
The technologies they’re using to drill those wells are the same ones developed and refined by the petroleum industry to exploit unconventional deposits in shale formations, which has transformed the American oil and gas sector. Crews at the Nevada site, for instance, drilled down to something like 8,000 feet and then steered the bit until it ran horizontally for thousands more feet. Explosive charges placed in the drilled-out rock fractured the geologic formation, and high-pressure water forced minuscule grains of proppant into the fractures to keep them open.
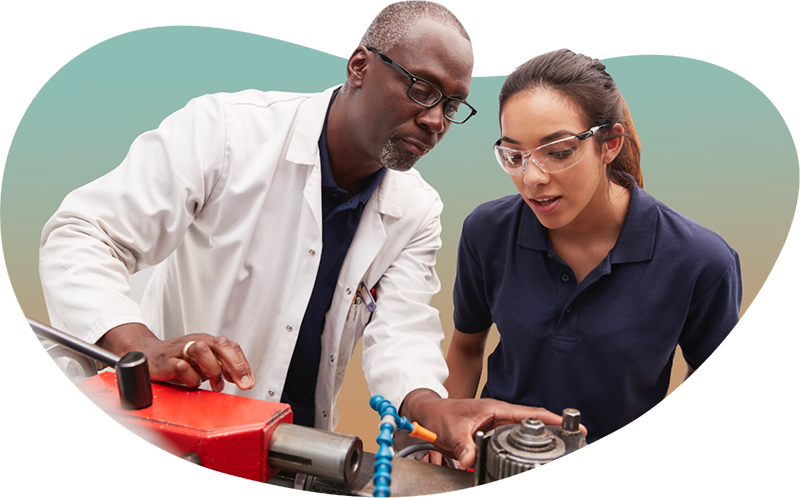
Make Connections
Whether you’re an experienced professional or just starting your career, ASME’s membership community, resources and tools can help you with your lifelong journey.
“After you pass that hot fluid through the power generation cycle, it comes out cold,” Norbeck said, “and you can reinject that to basically create a cycle.”
Just how far the two wells are from each other is critical. They must be spaced close enough to guarantee a high flow rate from the injection well to the production well, but far enough away from each other that they’re not short circuiting the system and cooling it off too quickly.
“It’s not a simple calculation,” Norbeck said. In fact, the equation that gives rise to that number is proprietary.
The shale revolution also required oil and gas companies to drill many more wells than was customary for conventional deposits. As a necessity, they’ve improved their operations and shortened drilling time considerably.
“It used to take 30 or 40 days to drill a well,” Norbeck said, “and now they’re getting it down to where it takes less than 10 days.” Geothermal companies are applying those learnings to their own operations to keep costs low.
Listen to the Podcast: Geothermal in Texas
Fervo is improving on traditional geothermal in other areas, too. For instance, geothermal plants that exploit volcanic features receive superheated steam from their wells; it’s cleaned and descaled and then sent through a steam turbine. The fluid then goes to an evaporative cooling system where as much as 50 percent of it is lost to the atmosphere. New water must be injected, or the wells will run dry.
Instead of a steam turbine, Fervo uses an Organic Rankine Cycle (ORC) turbine to produce power at the surface. An ORC sends the hot water to a heat exchanger to vaporize a refrigerant. That refrigerant goes to the turbine while the water, now cooled, is pumped back into the injection well.
The advantages are many. No water is lost to evaporation, no pressure is lost in the wells, the turbine spins through the entire power cycle, and the water stays in a single phase and so requires no descaling. Most importantly, the ORC allows rock as cool as 200 °C to generate electricity.
One drawback is that plant efficiency is in the 15 to 20 percent range, well below the 32 percent of a coal-fired power plant. “They are lower efficiency, but the fuel source is free,” Norbeck said. “That’s the trick. That’s how to make it economic.”
Taking pressure
Other startups are looking to reduce complexity—and cost—by cutting the number of wells in half. While horizontal drilling is now a mature process, the actual fractures that are created are subject to the whims of the rocks, making the connection of two wells a bit tricky, according to Lance Cook, president and CTO of Sage Geosystems, another Houston-based startup.“What happens is a lot of your fractures go off in different directions, and only a certain percentage of them go from one to the other,” said Cook, who worked for Shell in oilfield services, including a stint as vice president of Wells Technology. “If you’ve got a single point, which is what we do, then any line you draw is connected to your point.”
Sage’s business model is different from Fervo’s. While Fervo is looking to replicate baseload power, Sage is developing something more akin to a pumped energy storage reservoir flipped upside down, though the company has to pressurize the well rather than allow gravity to do the work.
ASME Landmarks: Ingenuity Turned the Geysers into a Powerhouse
“Let’s say we want a 100,000-barrel fracture network,” Cook explained. “We create that network with that one well and then we cycle 10,000 barrels at a time. We use that fracture like a lung: we fill it up, it breathes in, and then it compresses, breathes out.”
Just as your lungs never collapse totally, a Sage well will stay about 80 percent full at all times. The remaining 20 percent is hot, pressurized water for use in power production. With the well capped, the pressurized water—3,800 psi at Sage’s test site—sits there waiting till it’s needed.
At the surface, a Pelton turbine—“a higher-pressure Pelton than has ever been built before,” Cook said—will turn that pressure into electricity. And after the water has turned the Pelton turbine, it runs through an ORC to turn the heat to electricity as well.
“This is what's unique about us, we’re the only ones that are recovering this pressure component,” Cook said. “Everybody else is just venting it off.”
Sage is deliberately using high pressure for more than just storage. Keeping the fractures open allows for easy exchange of hot water with denser cold water, so the hot water is available as needed at the surface.
Cook said the company’s emphasis was on not inventing anything new. “That’s sort of our philosophy: to try to use off-the-shelf proven technology and just arrange it differently than what’s ever been done before,” Cook said. The first such arrangement—Sage’s three-megawatt demo plant in Texas—should be fully operational in the first quarter of 2025.
After that, the dream is to put in as many wells as financial resources allow.
“There are over four terawatts of geothermal resources, mainly from Texas to the west,” Cook said. “If you wanted to go just pure geothermal, you could do it—you could do the whole grid with geothermal if you wanted to. We would need 2,500 wells. The oil and gas industries drill 20,000 wells a year, so there’s a lot of surplus capacity in the oil and gas industry. We could put a gigawatt in fairly quickly with the oil and gas equipment currently sitting on the sidelines.”
In the loop
Both Fervo and Sage rely on the hydraulic fracturing of heated rocks, but fracking has become a hot-button topic in some places. To get around that opposition, Calgary-based Eavor has developed an enhanced geothermal system that relies on a radiator-like series of parallel pipes, called multilateral wells. The heat is taken from the rock conductively.“It’s a slower process,” said Jeanine Vany, a geoscientist and Eavor’s vice president of corporate affairs. “That’s why when you look at our well construction profiles, you’ll see many more wells being drilled to get the same megawatts—thermal or electric—out of the ground. But it also means that we have the ability to be truly scalable, and truly flexible, and truly reliable.”
Best of all, Vany said, instead of looking for sites with hot rock close to the surface that can be fracked, “we are looking for pretty much standard geothermal gradients, with sort of boring rock, no special characteristics.”
In addition to using proven petroleum-industry technology, Eavor has eliminated the need for steel casing, lining the length of the well with a proprietary rock pipe sealant instead. Once that’s done, crews fill the network of pipes with roughly enough water to fill an Olympic-size swimming pool.
See the Infographic: Geothermal Energy is Heat Under Our Feet
The water then circulates passively, free of pumps—it’s essentially a giant thermosiphon.
“The water that we put into that set of pipes is the water that goes around and around forever,” Vany said. “We have hardly any operating costs because we don’t have big plants that move water around.”
Like Sage and Fervo, Eavor will use an ORC to generate electricity, but the company is also looking for use cases that can apply the heat directly. Its first set of four wells (which the company calls “Eavor Loops”) in Geretsried, Germany, about 10 miles south of Munich, will generate 8 MW of electricity but also provide 64 MW of process heat when fully complete in 2027.
“We have a follow-on project in Hanover,” Vany said. “It is a city of half a million people, and we have a heat purchase agreement with the Enercity utility. They are looking to shut down their coal-fired fed heat and plug in geothermal.”
Electric drill
While the temperatures at a depth of around 8,000 feet are high enough in many places to support power production, geologists know that hot rock exists everywhere at a depth of six miles or so. Getting to it, however, is a chore and only a handful of oil wells have reached that depth.One challenge is the drill bit. Today’s bits must be pulled from the hole and replaced every 100-or-so meters—a days-long affair.
Quaise Energy is working to build a better drill bit by replacing the grinding teeth of a conventional bit with a gyrotron borrowed from the fusion industry. A 1 MW gyrotron would produce millimeter waves that, with the assistance of a metallic waveguide, would vaporize anything in its path.
“We don’t have contact with the rock, so there’s actually no wear and tear on the parts,” said Henry Phan, Quaise’s vice president of engineering and a 19-year veteran with oil services giant Schlumberger. Instead, the gyrotron will turn the rocks into a kind of ash-like flake which will be lifted out of the hole with a purge gas.
Quaise estimates their drilling speed to be three to five meters an hour, without any downtime needed to change a bit.
Gyrotrons are commercial products available to anyone with the money to buy them, but the sticking point is building them robustly enough for field applications.
“This equipment is made for laboratory applications,” Phan said. “That’s one obstacle that we have to overcome: making this thing where we can scale up without being so expensive.”
Quaise has already demonstrated that they can drill a small hole with the gyrotron—in the lab. The company has plans to drill a handful of 100-meter holes in the field by mid-2025.
More Podcasts: Engineering Geothermal Heat Pumps
“And we will continue to push that into next year to go an additional length as well,” Phan said. The company hopes to have a pilot hole to full depth within three years.
If successful—and if it can keep costs down—its method could be used for the Fervos, Sages, and Eavors of the world as well.
“The Holy Grail is what Quaise is working on, to be able to drill into the center of the Earth cheaply with this millimeter wave technology,” said Eavor’s Jeanine Vany. “We definitely could see ourselves ultimately using something like that to drill down.”
Michael Abrams is a technology writer in Westfield, N.J.
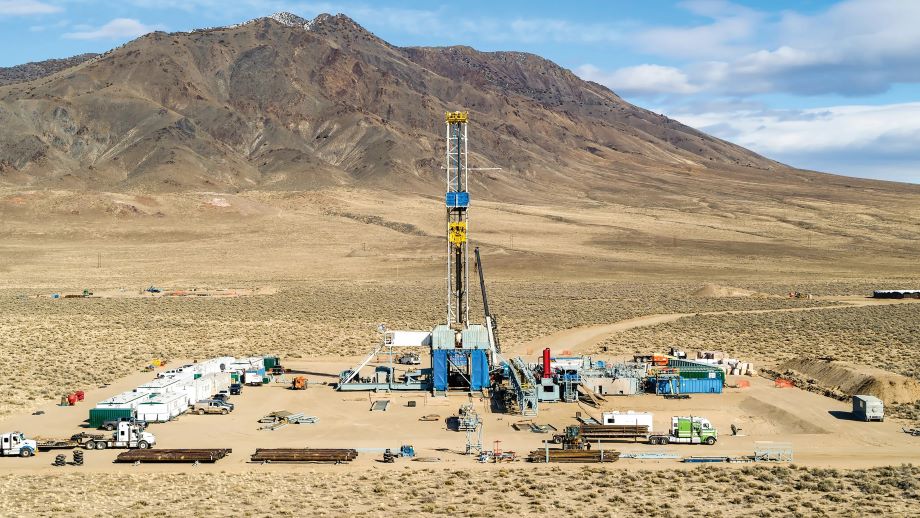
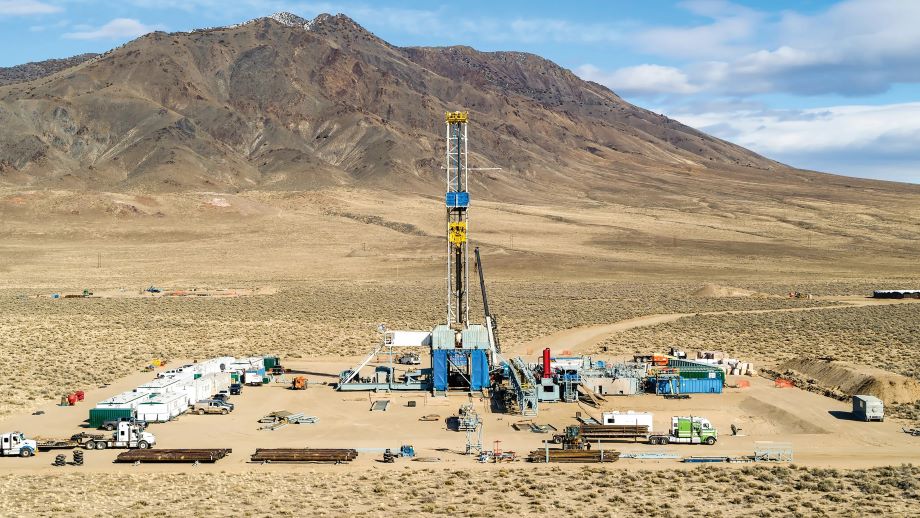