Better Airflow and Heat Transfer, Thanks to Dimples
Better Airflow and Heat Transfer, Thanks to Dimples
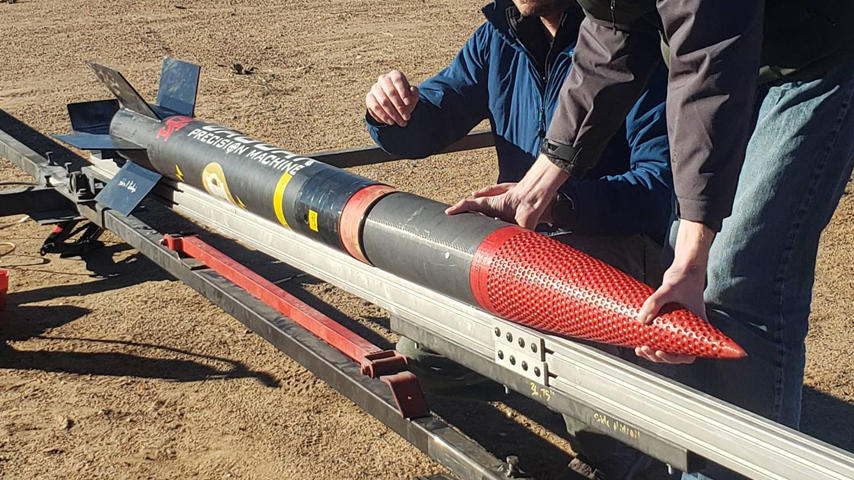
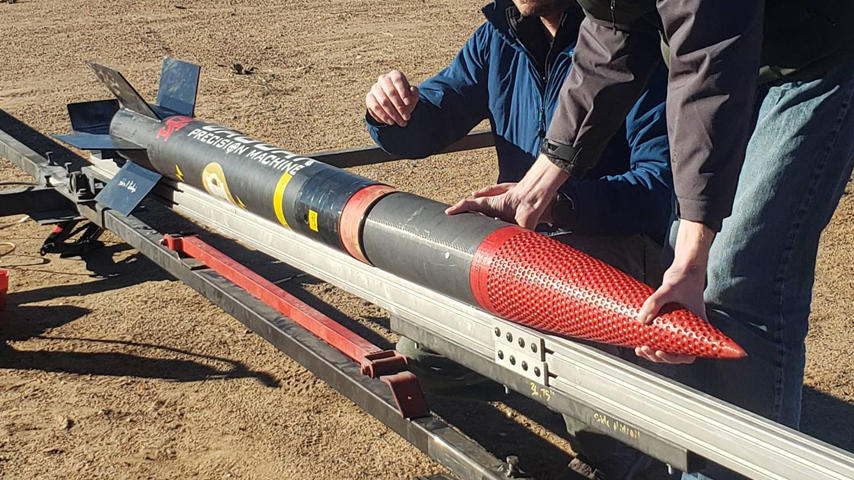
Dimples on rockets, planes, drones, and more could be on the horizon, thanks to research that has shown the addition of such patterns to objects improves aerodynamic performance.
Any object that travels through the air (or water) experiences drag. But a deceptively simple solution is showing promise in optimizing those aerodynamics. Researchers at Sandia National Laboratories in partnership with the University of New Mexico have found that applying dimples in specific sizes and patterns to an object can drastically improve air flow and reduce drag.
But figuring out exactly which sizes and patterns to apply on such objects has taken some time to develop.
“I've always been interested in turbulence modeling, and so when I got my Ph.D. through the University of New Mexico, they wanted me to do computational fluid dynamics and turbulence modeling as a course, which I did,” recalled Sal Rodriguez, a nuclear engineer at Sandia National Laboratories. While preparing presentations, he began to wonder why there are so many turbulence equations.
In an effort to streamline things for his students, Rodriguez began working on a set of equations that would allow him to explain concisely how turbulence works. “I was looking for a minimal set that basically captures all the physics of turbulence,” he said.
Inspiration struck shortly afterward in an unexpected place. Rodriguez happened to be watching the sky during a drive when he noticed a cloud that looked like a flow tube with a boundary layer inside.
“When I saw it, I knew exactly what I needed to do was wrap up my set of equations based on that cloud formation that had a turbulent boundary in there," he said.
What these equations do is they look at an object’s geometry, then take the velocity and the fluid it’s traveling through—be it water, air, or some other kind of fluid—and the program generates a specific dimple pattern that will optimize the object’s aerodynamics.
New equations in hand, Rodriguez set out to prove their potential with some testing on a golf ball.
“I said, if the dimples don't come out right, if the answer comes out to a meter or a mile, then toss everything out and forget about looking at the clouds. And so, I programmed it; and I was shocked,” he recalled.
That initial test yielded an aerodynamic improvement within 10 percent of what he found with commercial-sized golf balls. From there, Rodriguez started testing other systems and kept getting consistent results.
That was in 2014 and just three years later, the dimpling program was copyrighted.
Become a Member: How to Join ASME
Since then, Rodriguez and his team have used the program and equations to calculate dimple size for a range of different objects, from a golf ball to a piston, wind turbine blade, and even the hood of a Mustang racing car.
One of the most recent tests has been with the nosepieces of rockets, which was completed over the past year. On a high-power competition rocket traveling at Mach 0.64, the dimpled nosepiece showed an average drag reduction of 20.5 percent, peaking at nearly 39.1 percent, when compared to a smooth rocket.
“All you have to do is just modify the material properties, the physical properties of the fluid through which you move, and then apply the equations,” Rodriguez said. “We’ve been getting some good results.”
Controlled chaos
When an object has these precisely calculated dimples applied to it, the dimples generate a flow pattern that is so aerodynamic that the object only generates small, disorderly flow currents, Rodriguez explained. In other words, the dimples generate turbulence, redistribute turbulent energy, accelerate flow within the dimpled areas, and reduce boundary layer's size.
“The beauty of this set of equations that I've developed is it considers any object shape, any fluid it's going through, so long as it's turbulent,” he said.
But on top of the improved aerodynamics, the dimples are showing promise as a way to improve heat transfer, through a series of experiments over the last year.
In one such experiment, the team utilized two boxes, each one with three sides made of plexiglass and the fourth made of aluminum plates—one smooth, one dimpled. The boxes were then filled with water and connected to a heat source. Along the smooth plate, water moved gently, whereas the dimpled plate showed the fluid moving turbulently, Rodriguez recalled.
"When something is turbulent, it mixes more,” he continued. “When something is more aerodynamic, that means you have more flow near the wall and that means the fluid has a higher velocity—when you have a higher velocity, that means you have more heat transfer.”
This experiment showed that the flow on the dimpled plate was about three times faster, resulting in 2.4 times more heat transfer. Rodriguez added that a patent on this process is now pending.
The team also recently submitted a patent for a dimpled wind turbine blade, which during testing showed reduced frictional drag by about 5 percent to 10 percent. Computational fluid dynamics showed the boundary layer remained attached to the dimpled wind turbine blade, while detachment occurred for the unmodified wind turbine blade, he explained.
Rodriguez’s program was even used to verify the efficacy of a dimpling pattern on a diesel piston designed by Speed of Air Engine Technologies. Independent testing showed that a dimpled piston created 30 percent to 54 percent less nitrogen oxides when compared to a normal piston, all thanks to increased fluid turbulence, which enhances the mix of diesel and air during combustion.
“I'm able to give you the size of dimples that will give you the best heat transfer and the best aerodynamic drag reduction. That's very exciting because now we can apply this to reduce nitrous oxides and soot from diesel,” Rodriguez said. “But why just diesel? Why not consider gasoline powered vehicles? EVs may be the future, but it's not here yet, and given that it's a different exterior geometry, it's going to require different sizes of dimples.”
Looking ahead, Rodriguez plans to focus on a few applications that will help further demonstrate and validate the dimple concept, and to partner with interested parties to complete demonstrations.
“If we prove significant performance, then let's license it. That should be significant proof of concept. And then go on to another application, one at a time,” he said. “We've validated the copyright from subsonic to transonic, supersonic, and also hypersonic. We have independent evidence that it works.”
Louise Poirier is senior editor.