Carbon Nanotube Super Springs
Carbon Nanotube Super Springs
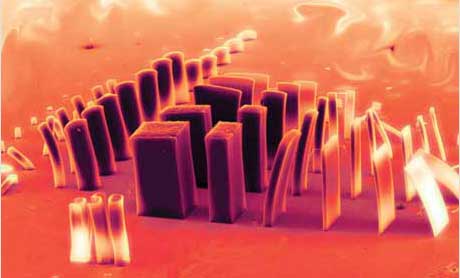
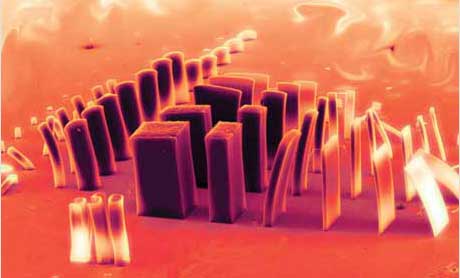
Carbon nanotubes, shown here in tufts several millimeters tall, have the strength and suppleness to make superior springs.
For certain applications, mechanical springs are superior to electrochemical batteries. A spring’s stored energy can be released quickly, with high power density. Springs can be recharged (redeformed) many times without degradation (as long as they are not deformed beyond their limits) and can hold stored energy without leakage. Springs also store energy robustly in the face of wide temperature swings.
The energy density of springs made of conventional materials, however, is much lower than the energy density of batteries. Current lithium-ion batteries offer energy densities of about 500 kJ/kg—three orders of magnitude greater than the energy densities of high-performance steel springs in bending. But batteries have their own limitations, being typically optimized for either high power density or high energy density; it is difficult to optimize simultaneously for both.
What if you want the robustness and power capabilities of springs, but also need the energy density of batteries? One option is to look for new materials for springs.
The ideal high-performance spring material will have both high material stiffness (like high-carbon steel) and high deformability (like rubber). Advanced nanoscale materials offer new options.
Like graphene, the effective material stiffness of CNTs is quite high—about five times that of high-carbon steel. Moreover, the low-defect structure of the carbon lattice enables CNTs to undergo large deformations before suffering failure—up to six times the maximum yield strains of high-carbon steel under tensile loading (stretching).
Although a single carbon nanotube may have exceptional mechanical properties, it is far too small to store a macroscopically useful amount of energy. Large numbers of CNTs must be deformed in a uniform way. For high energy density per unit volume, the CNTs must be tightly packed. And the complete system must be braced in a lightweight structure that can support the load of stored mechanical energy, plus have a means of extracting the energy for use.
To examine the potential for elastic energy storage in CNTs, in 2006, Timothy Havel and I formed a team at the Massachusetts Institute of Technology. Continuum modeling revealed that for maximum energy storage, the ideal system would consist of many long, small-diameter, single-wall CNTs in well-ordered groupings and loaded in tension. Moreover, the system needs a support structure made of a high-performance material such as diamond or silicon carbide.
When A. John Hart at the University of Michigan joined our group, we could test our mathematical models in experiments on real CNT springs. Hart pioneered a thermal chemical vapor deposition technique that grows well-aligned "forests" of multi-wall CNTs, as well as "pillars" (patterned sections of the forest). Although they do not have the single-wall structure that our modeling identified as ideal, a small piece of a CNT forest has 1 to 10 million parallel nanotubes several millimeters long, a significant fraction of them extending the full length of the test structure. The chunk of forest may be tested as is, or may be densified first using capillary forces or mechanical rolling to bring the CNTs closer together.
So far, we have looked at when and how the multi-wall CNT springs fail when they are stretched in tension; we have also tested their performance under cyclic tensile loading, mimicking the storage and extraction of energy from CNT springs. To date, the maximum recoverable energy density measured to date is about 5 kJ/kg, corresponding to total energy stored of about 1.5 microjoules. Although this energy density is much lower than the maximum theoretical energy density of springs composed of ideally ordered single-wall CNTs, it already exceeds the maximum energy density per unit weight of steel in bending by a factor of ten.
What could be done with an energy storage medium having the energy density of batteries and the temperature insensitivity and burst power capability of a spring? For high-power applications, springs could be released in groups; for low-power applications, energy could be released gradually through a ratcheting mechanism similar to the spring-driven escapement of a mechanical clock.
One potential application might be portable home tools that currently run on gasoline engines. For example, after winding up your spring-powered leaf blower, you could clear leaves more quietly and cleanly than with a gas-powered blower. Spring-based energy storage may also have advantages for leak-free long-term backup power supplies.
Given the promise of CNT springs, it’s easy to imagine ways they could help power a green and efficient future.
[Adapted from “Carbon Super Springs” by Carol Livermore, for Mechanical Engineering, March 2010.]
The ideal high-performance spring material will have both high material stiffness (like high-carbon steel) and high deformability (like rubber).
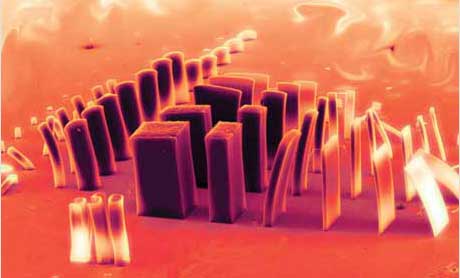
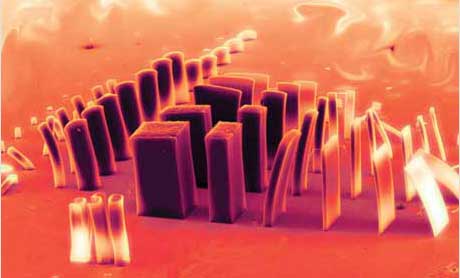