Cycloidal Reducer Technology Provides High-Precision Motion and Positioning Control
Cycloidal Reducer Technology Provides High-Precision Motion and Positioning Control
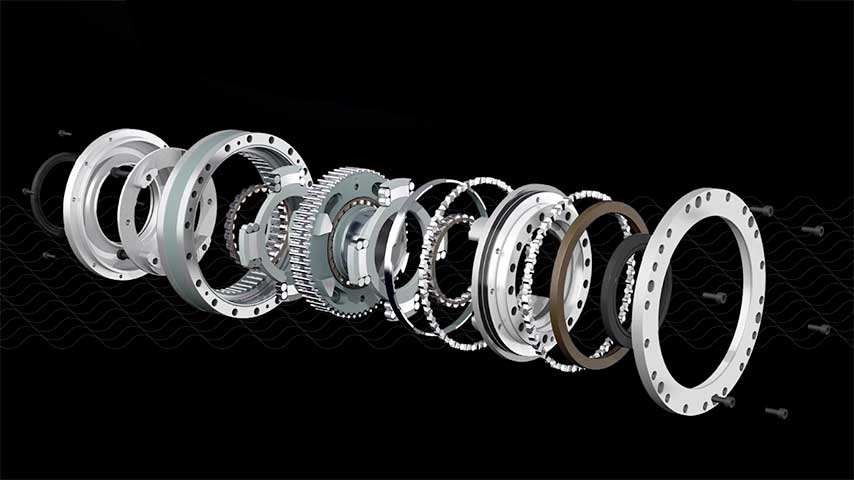
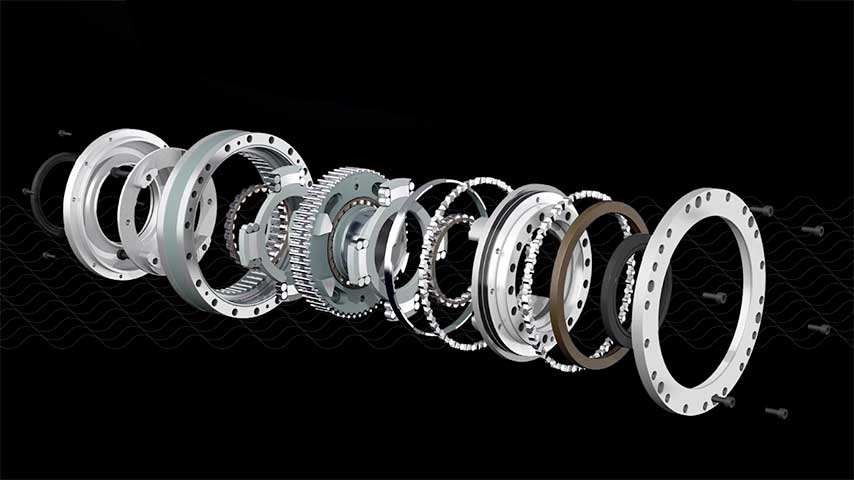
Zero-backlash cycloidal reducers offer very high positioning accuracy.
Cycloidal speed reducer technology is used in any ultra-high precision application where torque density and rigid construction are a must. These devices deliver relatively high reduction ratios and are produced in sizes as small as 50 mm in diameter. Compact and rigid speed reducers are essential for precise motion control in sophisticated systems such as robotics, military/defense equipment, medical equipment and satellite antennas to name a few.
Cycloidal gearboxes rely on eccentric motion using rolling elements to achieve speed reduction. Cycloidal technology provides greater accuracy and functionality compared to traditional precision planetary and flex spline designs. Flex spline reducers, when compared to cycloidal reducers, often lack the torque density and robustness (or the ability to tolerate torque shock) that is needed to deliver ultra-low or zero backlash performance during operation.
Key markets for cycloidal reducers are agriculture, automation and mechatronics, defense and security, custom machinery, medical systems, robotics, and transportation. Target applications within these markets are optical system positioning, antenna positioning, automated weapon station positioning, surveillance, areal gimbal positioning, radar, surgical robots, imaging, and many more.
Cycloidal reducers are ideal for applications requiring a high reduction ratio, high kinematic accuracy, low lost-motion, high moment capacity, high stiffness, low mass, and a compact design for limited installation envelopes. Cycloidal reducer technology can compete very effectively with flex spline reducers.
A flex spline is a flexible, thin-walled cylindrical cup with external teeth. The mechanical principle of flex spline differs from cycloidal drives in that the flex spline uses an elliptical disc called a wave generator to turn a geared ring. The Achilles heel of the flex spline design is the thin-walled cylindrical cup. It cannot withstand shock loading or instances of over torque. In these situations the thin walled cup has little strength and the gear teeth with skip, resulting in the output losing position.
In comparison, cycloidal reducers can transmit two to three times more torque than flex spline designs of similar size, and are much more rigid, supporting higher tilting moments. Cycloidal reducers also provide higher axial and radial loading capacity, lower input inertia, higher overloading capacity, and greater reliability.
When compared to planetary designs, the overwhelming advantage is the precision of the cycloidal design. A precision cycloidal has true zero backlash and higher rigidity because of its rolling element design. By comparison a planetary gearbox uses gears, a sun gear meshing with three (or more) planet gears revolving within an outer ring gear. To function properly there must be clearance between the gears to allow for lubrication. This clearance is in part the definition of backlash.
Among the other benefits cycloidal reducers provide are:
Zero-backlash reduction. Zero backlash is essential for applications that demand high degrees of positional accuracy in the relationship between the input and output rotation.
Excellent positioning accuracy and positioning repeatability. Robotic systems and robotic positioning actuators demand high kinematic accuracy to ensure that all movements are tightly controlled, without unanticipated movement. Accuracy of position as a load at the end-of-arm tooling must follow a critical path; any play within the mechanical system can translate into position lag or play within system. A zero-backlash reducer delivers high precision and tightly controlled motion, with accuracy of movement.
Cycloidal reducers also can be connected to servomotors for enhanced performance..
Cycloidal reducers and actuators are compact solutions for applications that call for repeatability, smoothness of movement, and position accuracy, and are often found in applications in the defense, security, surveillance, and communications industries. For example, precision targeting for weapons systems. External forces that are typically associated with weapon recoil or rapid position transitions can induce platform oscillation. Low lost-motion values enable higher targeting precision. Cycloidal reducers also provide additional security for weapon station crews during operations due to their ability to work reliably, even in extreme climatic conditions. For pan-tilt surveillance cameras, SPINEA reducers resist vibration and maintain their position in harsh conditions over a wide range of temperatures.
Top industrial applications include:
Robotics. The dominant feature for robotics is the pure rolling friction inside the reduction gear, and a single stage of reduction with a very high gear ratio, from 33 to 191. These two features improve the final properties of the robot, such as repeatable precision, dynamic movements of arms, running costs, low vibration, and low noise—ideal for 6-axis robots, gantry robots, and manipulators.
Manufacturing equipment. Cycloidal reduction gears are often used to maintain the rotary positioning of tools and workpieces for computer numerically controlled (CNC) machines, grinding machines, and lathes. Common applications include milling heads, grinding heads, cutting heads, rotary tables, tool changers, and pallet changers. Low vibrations and high torsional and tilting stiffness, combined with high positioning accuracy and low runout, ensure high machining precision.
Medical equipment. Cycloidal reduction gears are engineered for quiet operation in sensitive environments. In the medical equipment manufacturing space, cycloidal reducers are utilized for extremely precise positioning of a workpiece in dental milling machines and precise positioning of robot heads in surgical robots and imaging machines.
Defense industry. Cycloidal reducers are incorporated in biaxial manipulators for weapon stations, remote-controlled vehicles, and training and simulation systems. Special lubricants are available to ensure accurate operation over extreme temperature ranges. The technology is also built into monitoring and surveillance systems, using the latest generation of pan-tilt heads with higher payload and higher precision in all axes. For radar systems, cycloidal reducers provide high load capacity and high tilting capacity for smooth and efficient operation in extreme temperature fluctuations, high winds, heavy rains, and sandstorms.
Cycloidal reducers integrate high load-carrying reduction gears with a unique reduction mechanism and high-load-carrying output bearings in a single, compact unit. Cycloidal reducers and servo actuators offer exceptional precision over a wide range of dimensions and gear ratios. They are well-suited for applications that require high reduction ratios, high kinematic precision, zero-backlash motion, high torque capacity, and high rigidity. They also have excellent parameters of tilting and torsional stiffness and are easy to implement.
Stable performance, high precision, and small dimensions are key advantages of cycloidal reduction technology that attract mechanical engineers from a range of industries, including defense and security, automation, robotics, machining, surveillance, and medical systems.
Tom Kahn is a senior level, results-oriented, sales and marketing professional at DieQua. He has experience in sales management, product marketing management, and strategic solution sales to diverse market segments and customer bases.
Cycloidal gearboxes rely on eccentric motion using rolling elements to achieve speed reduction. Cycloidal technology provides greater accuracy and functionality compared to traditional precision planetary and flex spline designs. Flex spline reducers, when compared to cycloidal reducers, often lack the torque density and robustness (or the ability to tolerate torque shock) that is needed to deliver ultra-low or zero backlash performance during operation.
Key markets for cycloidal reducers are agriculture, automation and mechatronics, defense and security, custom machinery, medical systems, robotics, and transportation. Target applications within these markets are optical system positioning, antenna positioning, automated weapon station positioning, surveillance, areal gimbal positioning, radar, surgical robots, imaging, and many more.
Cycloidal reducers versus flex spines
Cycloidal reducers are ideal for applications requiring a high reduction ratio, high kinematic accuracy, low lost-motion, high moment capacity, high stiffness, low mass, and a compact design for limited installation envelopes. Cycloidal reducer technology can compete very effectively with flex spline reducers.
A flex spline is a flexible, thin-walled cylindrical cup with external teeth. The mechanical principle of flex spline differs from cycloidal drives in that the flex spline uses an elliptical disc called a wave generator to turn a geared ring. The Achilles heel of the flex spline design is the thin-walled cylindrical cup. It cannot withstand shock loading or instances of over torque. In these situations the thin walled cup has little strength and the gear teeth with skip, resulting in the output losing position.
In comparison, cycloidal reducers can transmit two to three times more torque than flex spline designs of similar size, and are much more rigid, supporting higher tilting moments. Cycloidal reducers also provide higher axial and radial loading capacity, lower input inertia, higher overloading capacity, and greater reliability.
When compared to planetary designs, the overwhelming advantage is the precision of the cycloidal design. A precision cycloidal has true zero backlash and higher rigidity because of its rolling element design. By comparison a planetary gearbox uses gears, a sun gear meshing with three (or more) planet gears revolving within an outer ring gear. To function properly there must be clearance between the gears to allow for lubrication. This clearance is in part the definition of backlash.
Among the other benefits cycloidal reducers provide are:
Zero-backlash reduction. Zero backlash is essential for applications that demand high degrees of positional accuracy in the relationship between the input and output rotation.
Excellent positioning accuracy and positioning repeatability. Robotic systems and robotic positioning actuators demand high kinematic accuracy to ensure that all movements are tightly controlled, without unanticipated movement. Accuracy of position as a load at the end-of-arm tooling must follow a critical path; any play within the mechanical system can translate into position lag or play within system. A zero-backlash reducer delivers high precision and tightly controlled motion, with accuracy of movement.
Cycloidal reducers also can be connected to servomotors for enhanced performance..
Industrial applications
Cycloidal reducers and actuators are compact solutions for applications that call for repeatability, smoothness of movement, and position accuracy, and are often found in applications in the defense, security, surveillance, and communications industries. For example, precision targeting for weapons systems. External forces that are typically associated with weapon recoil or rapid position transitions can induce platform oscillation. Low lost-motion values enable higher targeting precision. Cycloidal reducers also provide additional security for weapon station crews during operations due to their ability to work reliably, even in extreme climatic conditions. For pan-tilt surveillance cameras, SPINEA reducers resist vibration and maintain their position in harsh conditions over a wide range of temperatures.
Top industrial applications include:
Robotics. The dominant feature for robotics is the pure rolling friction inside the reduction gear, and a single stage of reduction with a very high gear ratio, from 33 to 191. These two features improve the final properties of the robot, such as repeatable precision, dynamic movements of arms, running costs, low vibration, and low noise—ideal for 6-axis robots, gantry robots, and manipulators.
Manufacturing equipment. Cycloidal reduction gears are often used to maintain the rotary positioning of tools and workpieces for computer numerically controlled (CNC) machines, grinding machines, and lathes. Common applications include milling heads, grinding heads, cutting heads, rotary tables, tool changers, and pallet changers. Low vibrations and high torsional and tilting stiffness, combined with high positioning accuracy and low runout, ensure high machining precision.
Medical equipment. Cycloidal reduction gears are engineered for quiet operation in sensitive environments. In the medical equipment manufacturing space, cycloidal reducers are utilized for extremely precise positioning of a workpiece in dental milling machines and precise positioning of robot heads in surgical robots and imaging machines.
Defense industry. Cycloidal reducers are incorporated in biaxial manipulators for weapon stations, remote-controlled vehicles, and training and simulation systems. Special lubricants are available to ensure accurate operation over extreme temperature ranges. The technology is also built into monitoring and surveillance systems, using the latest generation of pan-tilt heads with higher payload and higher precision in all axes. For radar systems, cycloidal reducers provide high load capacity and high tilting capacity for smooth and efficient operation in extreme temperature fluctuations, high winds, heavy rains, and sandstorms.
Precise, efficient, durable
Cycloidal reducers integrate high load-carrying reduction gears with a unique reduction mechanism and high-load-carrying output bearings in a single, compact unit. Cycloidal reducers and servo actuators offer exceptional precision over a wide range of dimensions and gear ratios. They are well-suited for applications that require high reduction ratios, high kinematic precision, zero-backlash motion, high torque capacity, and high rigidity. They also have excellent parameters of tilting and torsional stiffness and are easy to implement.
Stable performance, high precision, and small dimensions are key advantages of cycloidal reduction technology that attract mechanical engineers from a range of industries, including defense and security, automation, robotics, machining, surveillance, and medical systems.
Tom Kahn is a senior level, results-oriented, sales and marketing professional at DieQua. He has experience in sales management, product marketing management, and strategic solution sales to diverse market segments and customer bases.
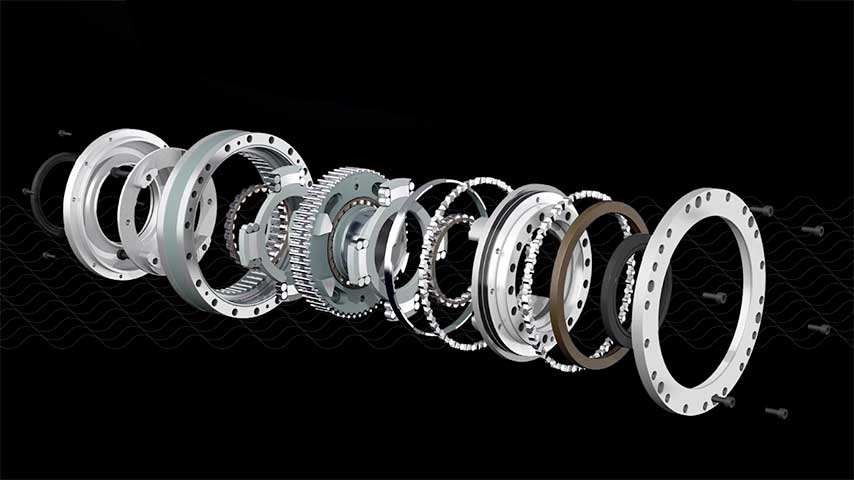
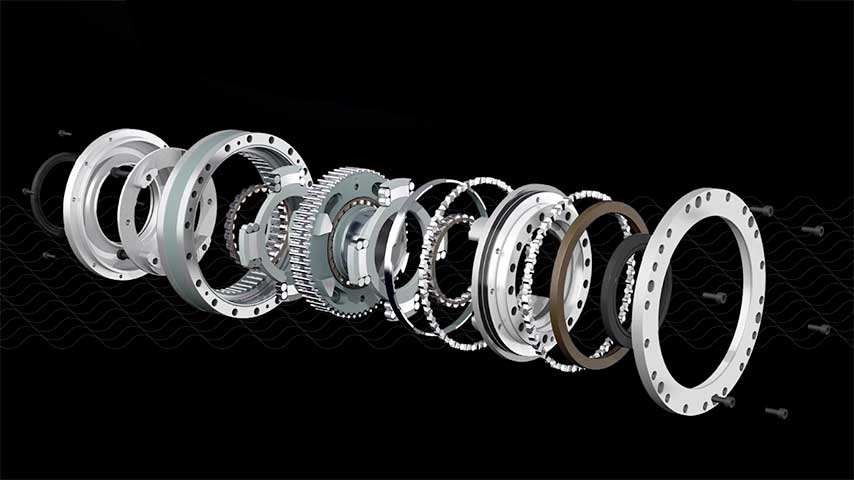