Electronic Skin Sends Sensations to the Brain
Electronic Skin Sends Sensations to the Brain
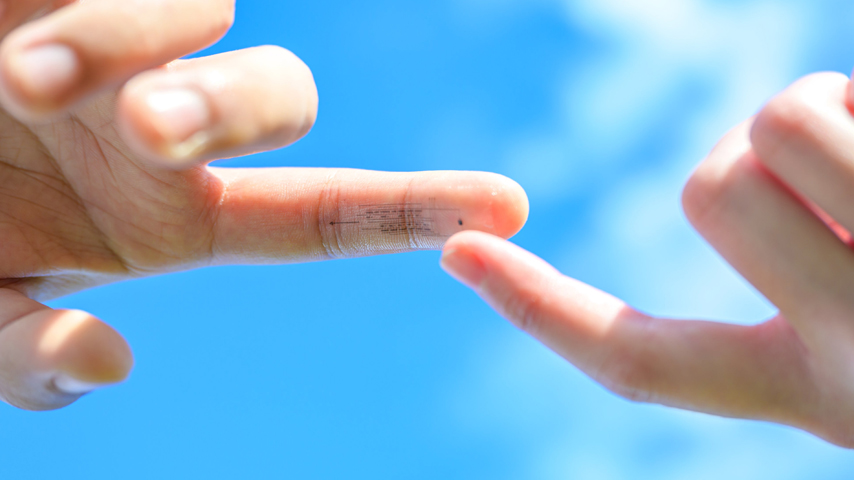
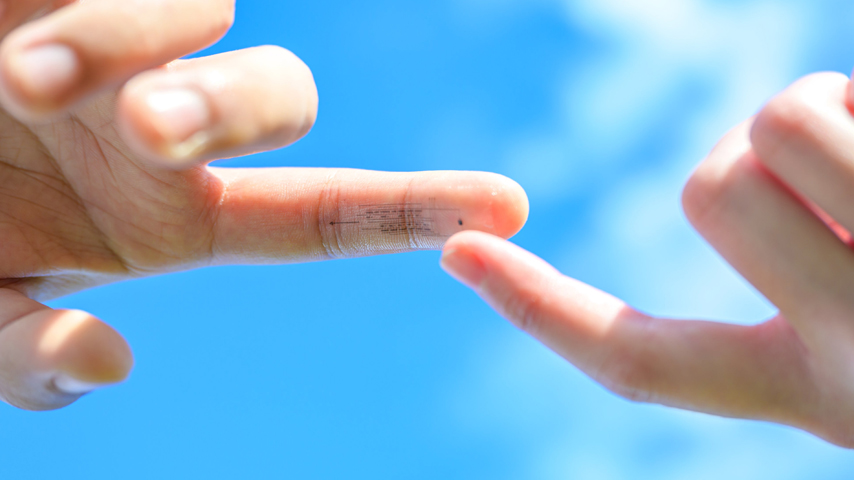
Researchers have developed an artificial “e-skin” that is soft and stretchable, with integrated nerve-like electronics that can sense pressure, temperature, and strain.
Prosthetic limbs can be a life-changer for those who have lost an arm or leg. But up to now, the limbs have not provided the kind of environmental information that skin sends to the brain every moment. Now, a research team at Stanford University, led by material science and chemical engineering professor Zhenan Bao, has created a soft, multilayer, and stretchable material with integrated nerve-like electronics that can sense pressure, temperature, and strain—just like real skin.
This “e-skin” generates nerve-like impulses that can communicate with brain via an implanted electrode. The different frequencies in the signals help the brain tell the difference between sensations, such as hot and cold.
Join ASME Today
Thin and stretchable, e-skin adheres to real skin like a Band-Aid. The ability to replicate these sensations in the human nervous system could allow people with prosthetics to sense pressure and temperature, helping them interact with their environment at a much higher level.
Bao’s researchers had to overcome several major design challenges to create the e-skin. First, they needed to find the right combination of skin-like materials with the proper physical and chemical characteristics—for example, the materials had to stretch and return to their original shapes without fail and always maintain its nerve-like electrical characteristics.
The materials also had to operate at a safe, low voltage.
To achieve this, the team invented a tri-layer dielectric structure that helped increase the mobility of electrical charge carriers by 30 times compared to a single-layer dielectrics, allowing the circuits to operate at only 5 volts. Each sensory input had its own integrated circuit consisting of organic nanostructures that transmit electrical signals, even when stretched. All the various sensory layers were then combined into a single material using materials that did not delaminate, tear, or lose electrical function. The final e-skin was less than a micron in total thickness.
“Not only does our electronic skin have sophisticated sensors and signal processing capabilities, it also has the ability to self-heal,” Bao said. “We accomplished this with a rationally designed, multi-layer stack of functional self-healing materials that also self-aligns to self-heal. When multi-layer laminates of these polymers are misaligned after damage, these structures autonomously realign during healing to minimize interfacial area. We were surprised by how even few micrometer-thick multi-layer stacks were able to self-align and self-heal autonomously.”
To test the system, Bao implanted the e-skin into a live rat. When the e-skin was touched, a pulse was transmitted to the rat’s somatosensory cortex, the part of the brain that processes physical sensations. The rat’s brain responded by sending an electrical signal down its leg, making it twitch. The degree of movement varied according to the amount of pressure applied to the e-skin.
Bao’s system combines sensing and all the desired electrical and mechanical features of human skin in a soft, durable form that could be used in next-generation prosthetic skins and innovative human-machine interfaces to provide a human-like sense of touch. Bao and his team are now working to increase the complexity and scalability of their technology, adding wireless functionality.
“Mechanical engineers will be interested to know that our multi-layer self-healing materials can be combined with magnetic materials to allow magnetic-field-directed assembly for soft robotic applications,” Bao said. “There may be medical applications for such materials.”
Mark Crawford is a technology writer in Corrales, N.M.
This “e-skin” generates nerve-like impulses that can communicate with brain via an implanted electrode. The different frequencies in the signals help the brain tell the difference between sensations, such as hot and cold.
Join ASME Today
Thin and stretchable, e-skin adheres to real skin like a Band-Aid. The ability to replicate these sensations in the human nervous system could allow people with prosthetics to sense pressure and temperature, helping them interact with their environment at a much higher level.
Tri-layer dielectric structure
Bao’s researchers had to overcome several major design challenges to create the e-skin. First, they needed to find the right combination of skin-like materials with the proper physical and chemical characteristics—for example, the materials had to stretch and return to their original shapes without fail and always maintain its nerve-like electrical characteristics.
The materials also had to operate at a safe, low voltage.
To achieve this, the team invented a tri-layer dielectric structure that helped increase the mobility of electrical charge carriers by 30 times compared to a single-layer dielectrics, allowing the circuits to operate at only 5 volts. Each sensory input had its own integrated circuit consisting of organic nanostructures that transmit electrical signals, even when stretched. All the various sensory layers were then combined into a single material using materials that did not delaminate, tear, or lose electrical function. The final e-skin was less than a micron in total thickness.
“Not only does our electronic skin have sophisticated sensors and signal processing capabilities, it also has the ability to self-heal,” Bao said. “We accomplished this with a rationally designed, multi-layer stack of functional self-healing materials that also self-aligns to self-heal. When multi-layer laminates of these polymers are misaligned after damage, these structures autonomously realign during healing to minimize interfacial area. We were surprised by how even few micrometer-thick multi-layer stacks were able to self-align and self-heal autonomously.”
To test the system, Bao implanted the e-skin into a live rat. When the e-skin was touched, a pulse was transmitted to the rat’s somatosensory cortex, the part of the brain that processes physical sensations. The rat’s brain responded by sending an electrical signal down its leg, making it twitch. The degree of movement varied according to the amount of pressure applied to the e-skin.
Next-generation prototype
Bao’s system combines sensing and all the desired electrical and mechanical features of human skin in a soft, durable form that could be used in next-generation prosthetic skins and innovative human-machine interfaces to provide a human-like sense of touch. Bao and his team are now working to increase the complexity and scalability of their technology, adding wireless functionality.
“Mechanical engineers will be interested to know that our multi-layer self-healing materials can be combined with magnetic materials to allow magnetic-field-directed assembly for soft robotic applications,” Bao said. “There may be medical applications for such materials.”
Mark Crawford is a technology writer in Corrales, N.M.
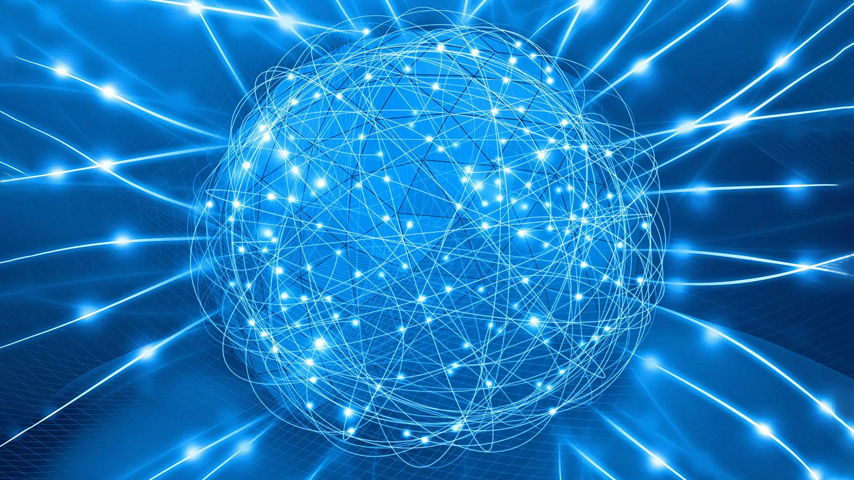
Pulse of the Profession: Digital Transformation
To bolster organizational resilience and efficiency—and leverage technologies for competitive advantage—organizations across the engineering landscape are investing in digital transformation.