Engineers Work to Quiet the Ocean
Engineers Work to Quiet the Ocean
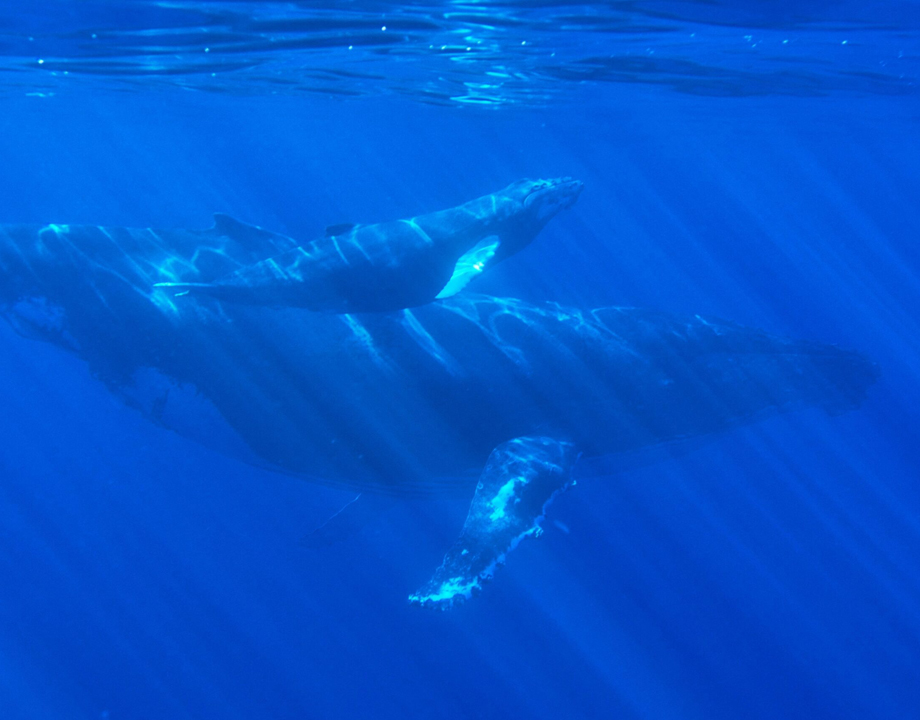
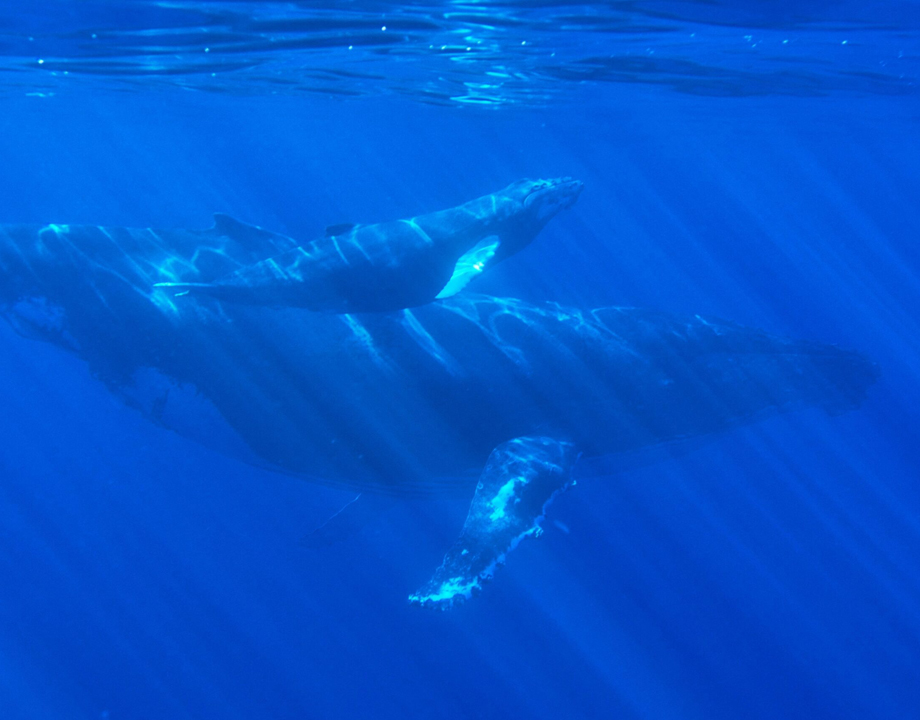
Researchers at the University of British Columbia are working to reduce the shipping industry’s underwater sound footprint through strategies such as passive design and AI machine learning.
Human maritime activity, from shipping to energy exploration and production, keeps getting louder. More than a thousand species of animals living in and near the ocean rely on echolocation. With all that interference bogging down the “waterwaves,” marine life is being impacted in numerous ways—affecting behavior, communication, reproduction, and even causing death in some situations.
A team of researchers at the University of British Columbia is looking to help by finding ways to reduce the amount of noise ship propellers generate. Methods include design changes to propellers and structures, plus some assistance from AI.
UBC’s CAD$2 million to CAD$3 million, five-year effort is being funded by various sources, including the Natural Sciences and Engineering Research Council of Canada, with about 20 researchers, PhDs, graduate students, and postdocs collaborating.
Propellers chopping through water are the primary source of underwater noise. “A lot of complex turbulence and vortices are being created,” explained UBC project lead Rajeev Jaiman, an associate professor in the Department of Mechanical Engineering. “The two types of noise are tonal, how you're chopping and at what frequency, and the other is broadband, which is your turbulence and vortex energy.”
UBC’s team is first aiming to fully decode the physics of underwater sound generated by ships, the intervening turbulence, cavitation (bubbles), and water shedding process, to minimize non-cavitating noise. The next part is a much bigger component: cavitation causes about 60 percent to 70 percent of noise from ships.
“At the low-pressure side of a propeller, we create a lot of bubbles in different forms—sheets, clouds—and they grow and they explode. That process is very complex. They can harm your propellers, but we are concerned about the explosion and how they create noise,” Jaiman said.
Sound from a massive container ship’s propellers can go up to 180 decibels, comparable to the sound generated by an aircraft engine or rocket launch, Jaiman added. Sound also travels five times faster underwater, he said. Sound from a shipping vessel’s propellers can travel up to a 60-mile or 100-kilometer radius.
One of the first solutions the UBC team is developing is modifying propellers through passive design. Adding serrated edges or waves to the blades or modifying the blades at the tip and trailing edge could help mitigate high shear and turbulence effects, Jaiman explained.
“The next idea is to introduce a jet of fluid,” he continued. “So, there's a tip or X like you see in the plane wing, and we are injecting some jet to provide more mixing so that you can destroy those kinds of high frequency or high noise causing flow patterns.”
Similar Reading: Researchers Use Acoustic Metamaterials to Block Out Sound
Another consideration is the noise generated by vibrations coming from machinery onboard vessels, which travels through the air, through the ship’s structures and into the water. Innovative material layouts could reduce the weight of structural components by up to 50 percent while also dampening noise, explained Jasmin Jelovica, project co-lead, naval architect and assistant professor of mechanical and civil engineering in the Faculty of Applied Science.
“We want to introduce advanced structures and position them strategically in some locations around the engine rooms, possibly one day replace even a larger part of that structure,” Jelovica said. “That's a challenging thing to do because the structure has many things to fulfill. It needs to have good structural integrity for 25 years.”
The team is examining architected materials that have more advanced mechanical properties than materials that are currently used in ships.
But in looking at advanced materials that would reduce sound transmission into the water, there could be production limitations. “There could be a range of different solutions and some simple ones would be just kind of in a way adding certain structures to the existing structure,” he said. “There are so many components, and the question is what do you want to replace and what's going to happen there? So, we are planning to do some tests in this project that would kind of demonstrate some of these benefits.”
AI machine learning is another primary research goal. This includes developing an AI-based framework that could quickly analyze the fluid interactions and dynamics behind noise and offer fast solutions to marine engineers.
Transport Canada’s Quiet Vessel Initiative also recently granted the UBC team additional funding to build a machine learning-based noise-prediction toolkit that will allow ships to adjust their noise based on the location of nearby marine mammals, as well as new AI software tools that can predict how much underwater noise a vessel will generate during early design and engineering.
Become A Member: How to Join ASME
Use of AI could help fill in gaps “specifically when it comes to noise,” Jelovica said. “No one checks the noise characteristics just because they don't have the means. Very efficient AI tools can be of tremendous help” in enabling engineers to rapidly perform analysis and simulations on any proposed structural or propeller modifications.
UBC researchers also recently published a paper, “Predicting transmission loss in underwater acoustics using convolutional recurrent autoencoder network,” in The Journal of the Acoustical Society of America that demonstrated how AI machine learning can be very efficient in predicting noise in the far field, Jaiman explained. Solving the noise issue involves “very complex physics,” he said. “So, we need to look at both the near field and far field. Solutions have to be cost-effective, adaptive, and feedback based.”
Government and public agencies and NGOs around the world are paying attention to the noise situation and are pushing for noise regulations to be set by the International Maritime Organization, the UN regulatory and standard-setting body for the international shipping industry.
Although IMO currently has a guideline for propeller noise, it’s not a strict regulation. At the end of January, IMO released a new draft of guidelines, updating the previous version set in 2014, which recognizes “that commercial shipping is one of the main contributors to underwater radiated noise.” While specific details were not released, IMO will submit the draft guidelines to the Marine Environment Protection Committee for approval during its meeting in July.
Check Out This Infographic: Are Maritime Climate Targets Off Course?
Actual regulations should be on the way within the next 5-10 years, Jaiman said. Once regulations are in effect, the shipping industry will need to modify vessels with new designs and forms for propellers, hulls and more.
Reducing noise pollution is a long-term commitment with which the marine industry is on board, Jaiman noted.
At the moment, the shipping industry is focused on reducing climate impacts and CO2 emissions. “A lot of these techniques and let's say modifications on the structures or propellers have other goals,” Jelovica added. “Energy efficiency is a long goal and it's not something we will stop working on, so if we allow ourselves to look into better production techniques or modifications to structures, propellers, those can have multiple benefits not only in terms of noise, but also in reducing the greenhouse gas emissions.”
Louise Poirier is senior editor.
A team of researchers at the University of British Columbia is looking to help by finding ways to reduce the amount of noise ship propellers generate. Methods include design changes to propellers and structures, plus some assistance from AI.
UBC’s CAD$2 million to CAD$3 million, five-year effort is being funded by various sources, including the Natural Sciences and Engineering Research Council of Canada, with about 20 researchers, PhDs, graduate students, and postdocs collaborating.
Propellers chopping through water are the primary source of underwater noise. “A lot of complex turbulence and vortices are being created,” explained UBC project lead Rajeev Jaiman, an associate professor in the Department of Mechanical Engineering. “The two types of noise are tonal, how you're chopping and at what frequency, and the other is broadband, which is your turbulence and vortex energy.”
UBC’s team is first aiming to fully decode the physics of underwater sound generated by ships, the intervening turbulence, cavitation (bubbles), and water shedding process, to minimize non-cavitating noise. The next part is a much bigger component: cavitation causes about 60 percent to 70 percent of noise from ships.
“At the low-pressure side of a propeller, we create a lot of bubbles in different forms—sheets, clouds—and they grow and they explode. That process is very complex. They can harm your propellers, but we are concerned about the explosion and how they create noise,” Jaiman said.
Sound from a massive container ship’s propellers can go up to 180 decibels, comparable to the sound generated by an aircraft engine or rocket launch, Jaiman added. Sound also travels five times faster underwater, he said. Sound from a shipping vessel’s propellers can travel up to a 60-mile or 100-kilometer radius.
Propelling quietly
One of the first solutions the UBC team is developing is modifying propellers through passive design. Adding serrated edges or waves to the blades or modifying the blades at the tip and trailing edge could help mitigate high shear and turbulence effects, Jaiman explained.
“The next idea is to introduce a jet of fluid,” he continued. “So, there's a tip or X like you see in the plane wing, and we are injecting some jet to provide more mixing so that you can destroy those kinds of high frequency or high noise causing flow patterns.”
Similar Reading: Researchers Use Acoustic Metamaterials to Block Out Sound
Another consideration is the noise generated by vibrations coming from machinery onboard vessels, which travels through the air, through the ship’s structures and into the water. Innovative material layouts could reduce the weight of structural components by up to 50 percent while also dampening noise, explained Jasmin Jelovica, project co-lead, naval architect and assistant professor of mechanical and civil engineering in the Faculty of Applied Science.
“We want to introduce advanced structures and position them strategically in some locations around the engine rooms, possibly one day replace even a larger part of that structure,” Jelovica said. “That's a challenging thing to do because the structure has many things to fulfill. It needs to have good structural integrity for 25 years.”
The team is examining architected materials that have more advanced mechanical properties than materials that are currently used in ships.
But in looking at advanced materials that would reduce sound transmission into the water, there could be production limitations. “There could be a range of different solutions and some simple ones would be just kind of in a way adding certain structures to the existing structure,” he said. “There are so many components, and the question is what do you want to replace and what's going to happen there? So, we are planning to do some tests in this project that would kind of demonstrate some of these benefits.”
Smart assistance
AI machine learning is another primary research goal. This includes developing an AI-based framework that could quickly analyze the fluid interactions and dynamics behind noise and offer fast solutions to marine engineers.
Transport Canada’s Quiet Vessel Initiative also recently granted the UBC team additional funding to build a machine learning-based noise-prediction toolkit that will allow ships to adjust their noise based on the location of nearby marine mammals, as well as new AI software tools that can predict how much underwater noise a vessel will generate during early design and engineering.
Become A Member: How to Join ASME
Use of AI could help fill in gaps “specifically when it comes to noise,” Jelovica said. “No one checks the noise characteristics just because they don't have the means. Very efficient AI tools can be of tremendous help” in enabling engineers to rapidly perform analysis and simulations on any proposed structural or propeller modifications.
UBC researchers also recently published a paper, “Predicting transmission loss in underwater acoustics using convolutional recurrent autoencoder network,” in The Journal of the Acoustical Society of America that demonstrated how AI machine learning can be very efficient in predicting noise in the far field, Jaiman explained. Solving the noise issue involves “very complex physics,” he said. “So, we need to look at both the near field and far field. Solutions have to be cost-effective, adaptive, and feedback based.”
Change beyond
Government and public agencies and NGOs around the world are paying attention to the noise situation and are pushing for noise regulations to be set by the International Maritime Organization, the UN regulatory and standard-setting body for the international shipping industry.
Although IMO currently has a guideline for propeller noise, it’s not a strict regulation. At the end of January, IMO released a new draft of guidelines, updating the previous version set in 2014, which recognizes “that commercial shipping is one of the main contributors to underwater radiated noise.” While specific details were not released, IMO will submit the draft guidelines to the Marine Environment Protection Committee for approval during its meeting in July.
Check Out This Infographic: Are Maritime Climate Targets Off Course?
Actual regulations should be on the way within the next 5-10 years, Jaiman said. Once regulations are in effect, the shipping industry will need to modify vessels with new designs and forms for propellers, hulls and more.
Reducing noise pollution is a long-term commitment with which the marine industry is on board, Jaiman noted.
At the moment, the shipping industry is focused on reducing climate impacts and CO2 emissions. “A lot of these techniques and let's say modifications on the structures or propellers have other goals,” Jelovica added. “Energy efficiency is a long goal and it's not something we will stop working on, so if we allow ourselves to look into better production techniques or modifications to structures, propellers, those can have multiple benefits not only in terms of noise, but also in reducing the greenhouse gas emissions.”
Louise Poirier is senior editor.
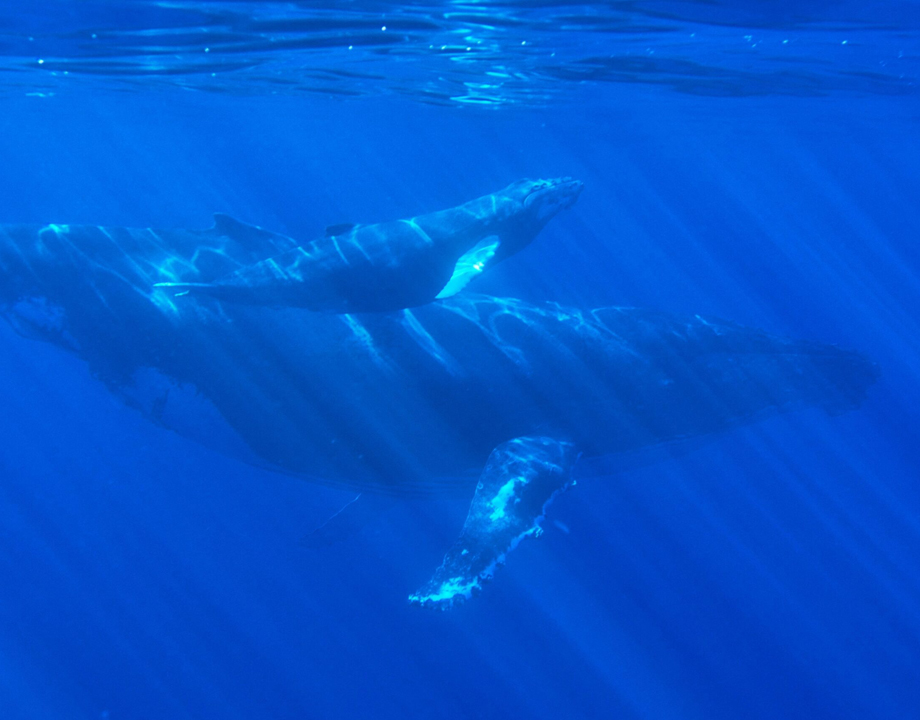
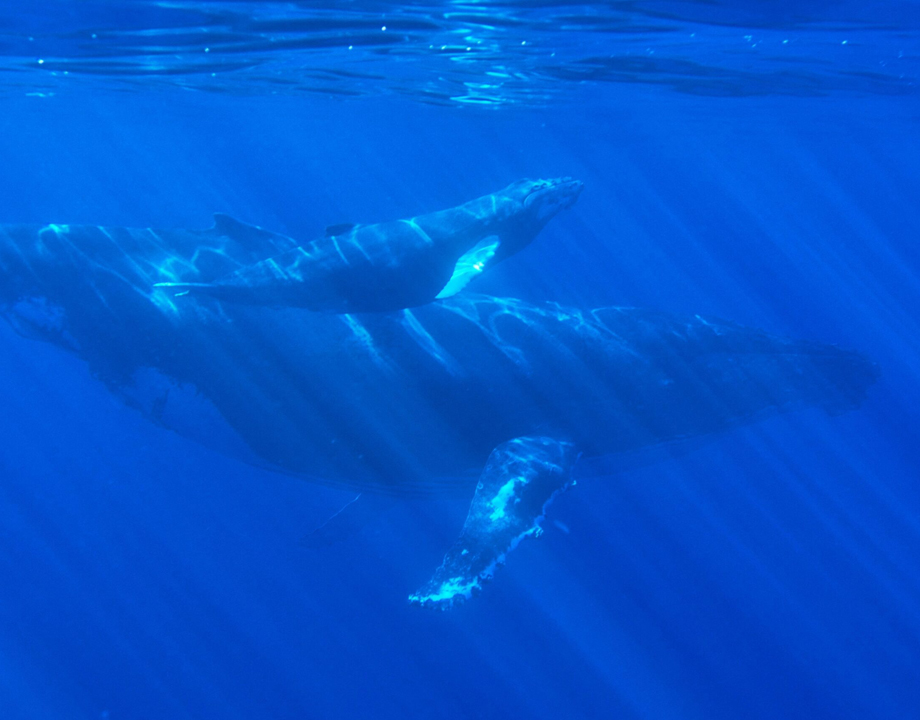