High-Tech Sails Bring Wind Power to Big Ships
High-Tech Sails Bring Wind Power to Big Ships
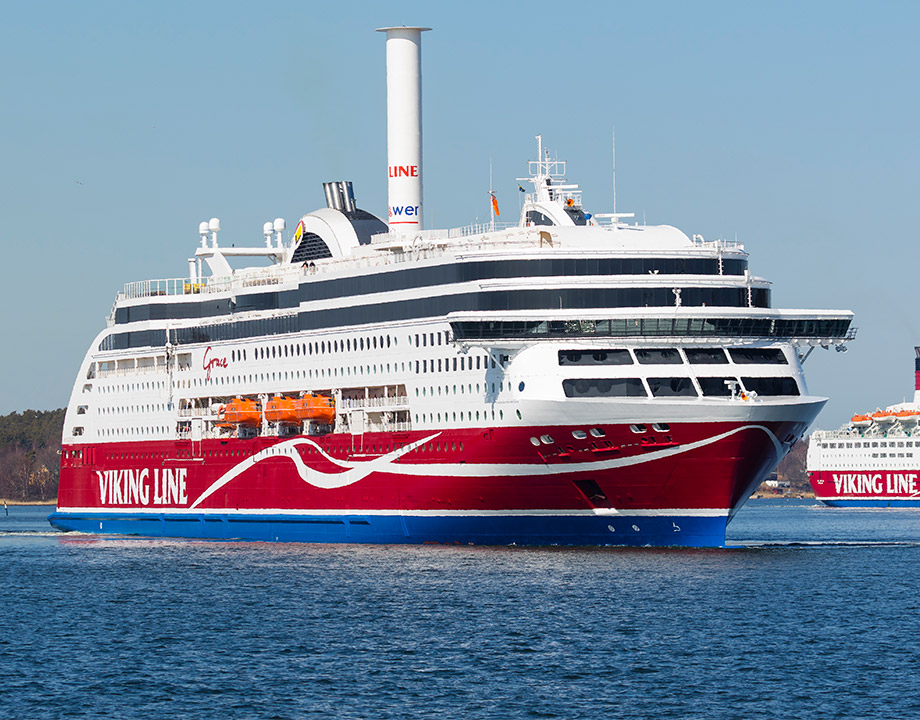
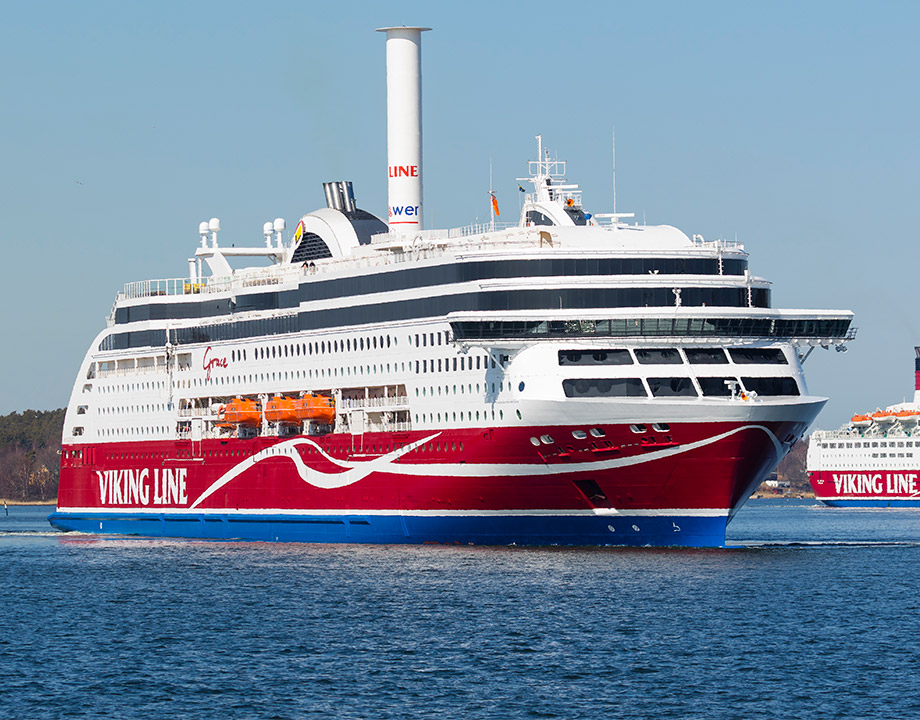
The Viking Line's Viking Grace combines natural gas engines with wind power to make the wind half-day journey between Stockholm, Sweden, and Turku, Finland. Photo: Norsepower
Over the past year, an unusual-looking Maersk tanker, Pelican, has been plying the world seas. It carries the same cargo as similar commercial ships, but it has one unique feature that gives it an unusual profile. Towering over its deck are two 30-meter-tall and 5-meter-wide columns.
From a distance, they may look like smokestacks. But on closer inspection—particularly a high wind—they are clearly spinning.
The two white towers are part of a sophisticated propulsion mechanism that has already helped the Pelican helping reduce fuel use and greenhouse gas emissions by 8 percent.
Built and installed by Norsepower, a Helsinki-based clean technology and engineering company, the spinning columns allow ships to harness wind power for thrust, much the way sailing ships did in the past. While the two towers do not generate as much power as a schooner under full sail, they do produce enough thrust to make a significant difference in fuel consumption.
Called Rotor Sails, the towers are based on something called the Magnus effect. This is the force that enables pitchers to throw curve balls and soccer players to bend it like David Beckham.
In a ball, the Magnus effect occurs because one side of the ball is spinning toward the direction of the ball’s flight, fighting and slowing the air flowing over it, while the other side of the ball turns away from its forward motion, accelerating the flow of air around it. This creates a pressure differential between the two flows, and pulls the ball toward the region of lower pressure where the air is moving faster.
The Magnus effect was a scientific curiosity until Anton Flettner, a German engineer, came up with the idea of harnessing it for ships. Instead of a spinning ball, he envisioned using a motor to spin a column that would generate Magnus forces along its length. The forces produced by the spinning column would act perpendicular to the direction of a vector of wind and the vessel’s forward motion.
Learn More About: Harvesting the Power of the Ocean
Armed with his calculations, Flettner convinced the Germania Shipyard in Kiel to back him. In 1924, Germania launched the first rotor sail-powered ship, the Buckau, which Flettner sent across the Atlantic in 1926 to drum up business in America. That same year, Germania built a larger freighter, Barbara, which plied the Mediterranean for three years. While the new technology proved reliable, it was buried by a combination of more efficient diesel engines, cheap fuel, and the Great Depression.
Today, Norsepower and its competitors are seeking to revitalize Flettner rotors as a complement, rather than a replacement, for ship engines. So far, Norsepower has partnered with three companies to install Rotor Sails on three very different types of ships.
The first was Bore’s Estraden, a roll-on/roll-off (RoRo) cargo ferry that carries trucks, rail cars, and other vehicles around the North Sea. Next came Viking Line’s Viking Grace, a passenger cruise ferry that makes the half-day journey between Stockholm, Sweden, and Turku, Finland, powered by natural gas.
The most recent launch was the Maersk Pelican, a crude oil tanker that installed two Rotor Sails in September 2018. In a trial that lasted a full year and took it from Europe and the Middle East to Asia and Australia, the rotors reduced fuel consumption by 8.2 percent.
There is a reason for the growing interest in green shipping, particularly in Europe, said Gavin Allwright. He is secretary of the United Kingdom’s International Windship Association (IWSA), which promotes wind propulsion solutions.
Today, Allwright explained, ship owners are under pressure from fuel costs and especially new regulations. While ship owners are always looking for ways to cut down on fuel use, they must also prepare new International Maritime Organization regulations. In addition to calling for 40 percent carbon emission reductions by 2030, they require ships to reduce sulfur—an environmental pollutant and health hazard—to 0.5 percent of emissions, from 3 percent, starting in January 2020.
There are two ways shippers can do this, and both are costly. The first is to install scrubbers, which strip sulfur from emissions as they leave the smoke stack. The second is to switch to cleaner, but more expensive, fuel. As a result, many owners and operators are looking to greener and cost-saving alternatives. This has renewed industry interest in a centuries-old but never ceasing source of natural power—fair winds.
The efficiency and fuel-saving potentials of Rotor Sails depend on the number installed and the consistency and strength of prevailing air currents in the region where the ship typically sails. Southern areas usually have less powerful winds, while northern waters, like the North Sea, are known for strong air currents.
Depending on how many rotors the ships carry, their fuel and emissions savings can range from five to 20 percent, said Norsepower’s chief sales officer Jukka Kuuskoski. In some conditions, the savings may be even higher,” he said. “On good wind days with winds coming from the right direction, it could even be 30 or 40 percent.”
Norsepower’s three rotor-powered test ships have totaled 45,000 hours of operating time. During that period, they have saved 1,700 tons of fuel and 5,000 tons of CO2 emissions.
One of the attractions of Rotor Sails is their compact profile, which makes them easy to install and highly efficient for the amount of space they take up. Norsepower claims they are 10 times more efficient than conventional sails on an areal basis. Also, shipyards can install them on new vessels or retrofit them onto existing ones. Norsepower’s rotors come in three sizes—-18 m x 3 m, 24 m x 4 m, and 30 m x 5 m—to accommodate different size ships.
Built from modern composites, the rotors are durable and relatively light, so they do not add much weight to the ship. They use a low-voltage electric motor for spinning, automatically adjusting to optimize forward thrust. They can also spin clockwise or counter-clockwise, depending on wind direction, to maximize power output.
“Everything is done automatically,” said Kuuskoski. “The crew does not have to pay attention to weather conditions or ship’s speed and direction to make sure the Rotor Sails are operating optimally. Our control system takes the info from the wind sensors and the GPS signals and maximizes the net benefit.”
You May Also Like: Sailing Toward Autonomy: Future of Self-Driving Cargo Ships
Business is picking up. Norsepower recently signed an agreement to install a Rotor Sail on the passenger ferry, Copenhagen, operated by Denmark’s Scandlines, in 2020. The vessel is already a showcase of green technology, using a combination of diesel motors and batteries to improve the efficiency of the ferry in port and at sea.
Norsepower also signed a joint development project with Shanghai Waigaoqiao Ship Building, a subsidiary of China State Shipbuilding, which included Rotor Sails installation on a very large crude carrier (VLCC) used for transporting oil. The design displayed during the announcement showed a tanker with six rotors.
Others are also building Flettner systems. Germany’s third largest wind turbine manufacturer, Enercon, commissioned the 130-meter-long E-Ship 1 to deliver large wind turbines. The ship, which launched in 2010, uses four large Flettner rotor sails, driven by a Siemens steam turbine, to supplement its Caterpillar diesel generators.
Meanwhile, Germany’s Eco-Flettner installed a single large rotor on the 90-meter-long Fehn Pollux in 2018. The crew took measurements with the rotor sail switched on and off under identical sea and wind conditions. According to the company, the ship exceeded wind tunnel estimates and could eventually reduce fuel costs by 10 percent to 25 percent.
Thanks to EU funding, rotor sails are not the only game in town. One example is The Netherlands’ company, eConowind, whose Ventifoils are based on aircraft wings rather than rotating cylinders, though they also use pressure differentials to generate thrust.
“It’s best explained as a comparison to an airplane wing,” Frank Nieuwenhuis, the company’s CEO, explained. “Airplane wings have a shape that creates a low pressure area above the wing and a high pressure area underneath the wing. That’s what we are doing, only we optimize this wing to work on low speeds.”
“This wing was invented by French explorer Jacques Cousteau who first tried it in the 1980s,” Nieuwenhuis said. “He put the wing on his ship and sailed around the world, but it was never commercialized because until recently no one really worried about CO2. Now the market is really good for it.”
The Lady Christina, a 108-meter-long cargo vessel owned by Netherland’s Wijnne Barends, has already made her maiden voyage with an eConowind-unit. Another Netherlands company, Jan van Dam Shipping, has signed a contract for an eConowind installation on its cargo vessel Ankie.
The company aims to use these aluminum wings on containerships, not the type of vessel anyone would associate with free deck space. Yet eConowind has come up with a clever way to surmount this barrier: It packages its propulsion units in a standard, 40-foot-long sea container, just like the ones used to transport ocean freight. After placing the container on the top of the container stack, the wings unfold to harness the wind.
Containerizing the wings enables shipping companies to install and fold the wings back into the container at any time. This flexibility allows ships to load the Ventifoils by crane, just like any other cargo, or switch them to vessels heading into more advantageous winds. At sea, sailors can take down the wings to fit under low hanging bridges or to clear the deck of obstructions in stormy weather.
Using aluminum—as opposed to more expensive options like composite materials—keeps prices down, Nieuwenhuis noted. Outfitting a ship with a pair of foldable wings costs under Euro 300,000. Larger units, which the company plans to build in the future, would cost more. Still, Nieuwenhuis remains mindful of affordability.
“Overall, we strive for a solution that allows customers to break even within three years,” he said.
French innovator Airseas, a spinoff of aircraft giant Airbus, is also in the wind game. It is developing a massive parafoil sail that can pull a large ship the way parasails now pull skiers and surfers.
Parafoils are sails that have an aerodynamic cell structure. When they deploy, wind inflates those cells into a classic wing-shaped cross-section, which gives the sail extra lift.
Airseas wants to put that lift to work with Seawing, a 1,000-square-meter parasail that would fly in front of a vessel. Shippers would install it in a storage space on a ship’s forecastle and unfurl it like a humongous kite when the ship was running with the wind.
Like all modern wind devices, this one relies on software. It would inform the captain and crew when the conditions would be most favorable to launch or fold the kite, which would be automatically controlled.
“By a simple press of a button you can deploy it or retrieve it,” explained Luc Reinhard, who heads business development at Seawing. “We will use eco-routing — a solution that uses weather data and sensors to tell the crew which route to take to harness the most wind possible to maximize fuel savings.”
The technology is best suited for bulkers, tankers, containerships, liquefied natural gas carriers and RoRo ships, but it can also work on passenger vessels, Reinhard said. While he cannot yet discuss costs or how long it would take ship operators to break even, he expects the parafoil to save about 20 percent of fuel costs.
Editors' Pick: Two for the Price of One: Offshore Wind and Marine Power Platform
There are not any ships currently sailing with Seawing, but that will change by the end of 2020, when Airbus plans to install a 500-square-meter Seawing on one of its own RoRo vessels.
Japanese ship owner Kawasaki Kisen Kaisha (K-Line) has already signed an agreement to install a 1,000-square-meter parafoil on one of its bulk carriers in 2021. If all goes well, K-Line would consider equipping 50 more bulkers, which carry unpackaged goods, with Seawing.
Although wind propulsion is not yet mainstream, it is certainly trending in that direction.
“In 2014, we had a smattering of projects,” said the International Windship Association’s Allwright. “Now we are seeing 15 to 20 projects going steadily through research and development or coming into sea trials.”
He thinks the industry’s embrace of wind will accelerate over the next 18 month as the IMO’s new sulfur standards go into effect. One recent report estimated vessel operators could install 3,500 to 10,500 wind propulsion systems over the next 10 years. Europe is leading the trend, but Asia is catching on too, and there’re some developments in Vancouver, Allwright said.
“Today, everyone is looking at de-carbonization and cost reduction,” he said. The fair winds are one way to do it—and they come clean and free.
Lina Zeldovich is a science, engineering and technology writer based in New York.
From a distance, they may look like smokestacks. But on closer inspection—particularly a high wind—they are clearly spinning.
The two white towers are part of a sophisticated propulsion mechanism that has already helped the Pelican helping reduce fuel use and greenhouse gas emissions by 8 percent.
Built and installed by Norsepower, a Helsinki-based clean technology and engineering company, the spinning columns allow ships to harness wind power for thrust, much the way sailing ships did in the past. While the two towers do not generate as much power as a schooner under full sail, they do produce enough thrust to make a significant difference in fuel consumption.
Called Rotor Sails, the towers are based on something called the Magnus effect. This is the force that enables pitchers to throw curve balls and soccer players to bend it like David Beckham.
In a ball, the Magnus effect occurs because one side of the ball is spinning toward the direction of the ball’s flight, fighting and slowing the air flowing over it, while the other side of the ball turns away from its forward motion, accelerating the flow of air around it. This creates a pressure differential between the two flows, and pulls the ball toward the region of lower pressure where the air is moving faster.
The Magnus effect was a scientific curiosity until Anton Flettner, a German engineer, came up with the idea of harnessing it for ships. Instead of a spinning ball, he envisioned using a motor to spin a column that would generate Magnus forces along its length. The forces produced by the spinning column would act perpendicular to the direction of a vector of wind and the vessel’s forward motion.
Learn More About: Harvesting the Power of the Ocean
Armed with his calculations, Flettner convinced the Germania Shipyard in Kiel to back him. In 1924, Germania launched the first rotor sail-powered ship, the Buckau, which Flettner sent across the Atlantic in 1926 to drum up business in America. That same year, Germania built a larger freighter, Barbara, which plied the Mediterranean for three years. While the new technology proved reliable, it was buried by a combination of more efficient diesel engines, cheap fuel, and the Great Depression.
Today, Norsepower and its competitors are seeking to revitalize Flettner rotors as a complement, rather than a replacement, for ship engines. So far, Norsepower has partnered with three companies to install Rotor Sails on three very different types of ships.
The first was Bore’s Estraden, a roll-on/roll-off (RoRo) cargo ferry that carries trucks, rail cars, and other vehicles around the North Sea. Next came Viking Line’s Viking Grace, a passenger cruise ferry that makes the half-day journey between Stockholm, Sweden, and Turku, Finland, powered by natural gas.
The most recent launch was the Maersk Pelican, a crude oil tanker that installed two Rotor Sails in September 2018. In a trial that lasted a full year and took it from Europe and the Middle East to Asia and Australia, the rotors reduced fuel consumption by 8.2 percent.
There is a reason for the growing interest in green shipping, particularly in Europe, said Gavin Allwright. He is secretary of the United Kingdom’s International Windship Association (IWSA), which promotes wind propulsion solutions.
Today, Allwright explained, ship owners are under pressure from fuel costs and especially new regulations. While ship owners are always looking for ways to cut down on fuel use, they must also prepare new International Maritime Organization regulations. In addition to calling for 40 percent carbon emission reductions by 2030, they require ships to reduce sulfur—an environmental pollutant and health hazard—to 0.5 percent of emissions, from 3 percent, starting in January 2020.
There are two ways shippers can do this, and both are costly. The first is to install scrubbers, which strip sulfur from emissions as they leave the smoke stack. The second is to switch to cleaner, but more expensive, fuel. As a result, many owners and operators are looking to greener and cost-saving alternatives. This has renewed industry interest in a centuries-old but never ceasing source of natural power—fair winds.
Towers for Wind Power Generation
The efficiency and fuel-saving potentials of Rotor Sails depend on the number installed and the consistency and strength of prevailing air currents in the region where the ship typically sails. Southern areas usually have less powerful winds, while northern waters, like the North Sea, are known for strong air currents.
Depending on how many rotors the ships carry, their fuel and emissions savings can range from five to 20 percent, said Norsepower’s chief sales officer Jukka Kuuskoski. In some conditions, the savings may be even higher,” he said. “On good wind days with winds coming from the right direction, it could even be 30 or 40 percent.”
Norsepower’s three rotor-powered test ships have totaled 45,000 hours of operating time. During that period, they have saved 1,700 tons of fuel and 5,000 tons of CO2 emissions.
One of the attractions of Rotor Sails is their compact profile, which makes them easy to install and highly efficient for the amount of space they take up. Norsepower claims they are 10 times more efficient than conventional sails on an areal basis. Also, shipyards can install them on new vessels or retrofit them onto existing ones. Norsepower’s rotors come in three sizes—-18 m x 3 m, 24 m x 4 m, and 30 m x 5 m—to accommodate different size ships.
Built from modern composites, the rotors are durable and relatively light, so they do not add much weight to the ship. They use a low-voltage electric motor for spinning, automatically adjusting to optimize forward thrust. They can also spin clockwise or counter-clockwise, depending on wind direction, to maximize power output.
“Everything is done automatically,” said Kuuskoski. “The crew does not have to pay attention to weather conditions or ship’s speed and direction to make sure the Rotor Sails are operating optimally. Our control system takes the info from the wind sensors and the GPS signals and maximizes the net benefit.”
You May Also Like: Sailing Toward Autonomy: Future of Self-Driving Cargo Ships
Business is picking up. Norsepower recently signed an agreement to install a Rotor Sail on the passenger ferry, Copenhagen, operated by Denmark’s Scandlines, in 2020. The vessel is already a showcase of green technology, using a combination of diesel motors and batteries to improve the efficiency of the ferry in port and at sea.
Norsepower also signed a joint development project with Shanghai Waigaoqiao Ship Building, a subsidiary of China State Shipbuilding, which included Rotor Sails installation on a very large crude carrier (VLCC) used for transporting oil. The design displayed during the announcement showed a tanker with six rotors.
Others are also building Flettner systems. Germany’s third largest wind turbine manufacturer, Enercon, commissioned the 130-meter-long E-Ship 1 to deliver large wind turbines. The ship, which launched in 2010, uses four large Flettner rotor sails, driven by a Siemens steam turbine, to supplement its Caterpillar diesel generators.
Meanwhile, Germany’s Eco-Flettner installed a single large rotor on the 90-meter-long Fehn Pollux in 2018. The crew took measurements with the rotor sail switched on and off under identical sea and wind conditions. According to the company, the ship exceeded wind tunnel estimates and could eventually reduce fuel costs by 10 percent to 25 percent.
Other Sails for Power Generation
Thanks to EU funding, rotor sails are not the only game in town. One example is The Netherlands’ company, eConowind, whose Ventifoils are based on aircraft wings rather than rotating cylinders, though they also use pressure differentials to generate thrust.
“It’s best explained as a comparison to an airplane wing,” Frank Nieuwenhuis, the company’s CEO, explained. “Airplane wings have a shape that creates a low pressure area above the wing and a high pressure area underneath the wing. That’s what we are doing, only we optimize this wing to work on low speeds.”
“This wing was invented by French explorer Jacques Cousteau who first tried it in the 1980s,” Nieuwenhuis said. “He put the wing on his ship and sailed around the world, but it was never commercialized because until recently no one really worried about CO2. Now the market is really good for it.”
The Lady Christina, a 108-meter-long cargo vessel owned by Netherland’s Wijnne Barends, has already made her maiden voyage with an eConowind-unit. Another Netherlands company, Jan van Dam Shipping, has signed a contract for an eConowind installation on its cargo vessel Ankie.
The company aims to use these aluminum wings on containerships, not the type of vessel anyone would associate with free deck space. Yet eConowind has come up with a clever way to surmount this barrier: It packages its propulsion units in a standard, 40-foot-long sea container, just like the ones used to transport ocean freight. After placing the container on the top of the container stack, the wings unfold to harness the wind.
Containerizing the wings enables shipping companies to install and fold the wings back into the container at any time. This flexibility allows ships to load the Ventifoils by crane, just like any other cargo, or switch them to vessels heading into more advantageous winds. At sea, sailors can take down the wings to fit under low hanging bridges or to clear the deck of obstructions in stormy weather.
Using aluminum—as opposed to more expensive options like composite materials—keeps prices down, Nieuwenhuis noted. Outfitting a ship with a pair of foldable wings costs under Euro 300,000. Larger units, which the company plans to build in the future, would cost more. Still, Nieuwenhuis remains mindful of affordability.
“Overall, we strive for a solution that allows customers to break even within three years,” he said.
French innovator Airseas, a spinoff of aircraft giant Airbus, is also in the wind game. It is developing a massive parafoil sail that can pull a large ship the way parasails now pull skiers and surfers.
Parafoils are sails that have an aerodynamic cell structure. When they deploy, wind inflates those cells into a classic wing-shaped cross-section, which gives the sail extra lift.
Airseas wants to put that lift to work with Seawing, a 1,000-square-meter parasail that would fly in front of a vessel. Shippers would install it in a storage space on a ship’s forecastle and unfurl it like a humongous kite when the ship was running with the wind.
Like all modern wind devices, this one relies on software. It would inform the captain and crew when the conditions would be most favorable to launch or fold the kite, which would be automatically controlled.
“By a simple press of a button you can deploy it or retrieve it,” explained Luc Reinhard, who heads business development at Seawing. “We will use eco-routing — a solution that uses weather data and sensors to tell the crew which route to take to harness the most wind possible to maximize fuel savings.”
The technology is best suited for bulkers, tankers, containerships, liquefied natural gas carriers and RoRo ships, but it can also work on passenger vessels, Reinhard said. While he cannot yet discuss costs or how long it would take ship operators to break even, he expects the parafoil to save about 20 percent of fuel costs.
Editors' Pick: Two for the Price of One: Offshore Wind and Marine Power Platform
There are not any ships currently sailing with Seawing, but that will change by the end of 2020, when Airbus plans to install a 500-square-meter Seawing on one of its own RoRo vessels.
Japanese ship owner Kawasaki Kisen Kaisha (K-Line) has already signed an agreement to install a 1,000-square-meter parafoil on one of its bulk carriers in 2021. If all goes well, K-Line would consider equipping 50 more bulkers, which carry unpackaged goods, with Seawing.
Although wind propulsion is not yet mainstream, it is certainly trending in that direction.
“In 2014, we had a smattering of projects,” said the International Windship Association’s Allwright. “Now we are seeing 15 to 20 projects going steadily through research and development or coming into sea trials.”
He thinks the industry’s embrace of wind will accelerate over the next 18 month as the IMO’s new sulfur standards go into effect. One recent report estimated vessel operators could install 3,500 to 10,500 wind propulsion systems over the next 10 years. Europe is leading the trend, but Asia is catching on too, and there’re some developments in Vancouver, Allwright said.
“Today, everyone is looking at de-carbonization and cost reduction,” he said. The fair winds are one way to do it—and they come clean and free.
Lina Zeldovich is a science, engineering and technology writer based in New York.
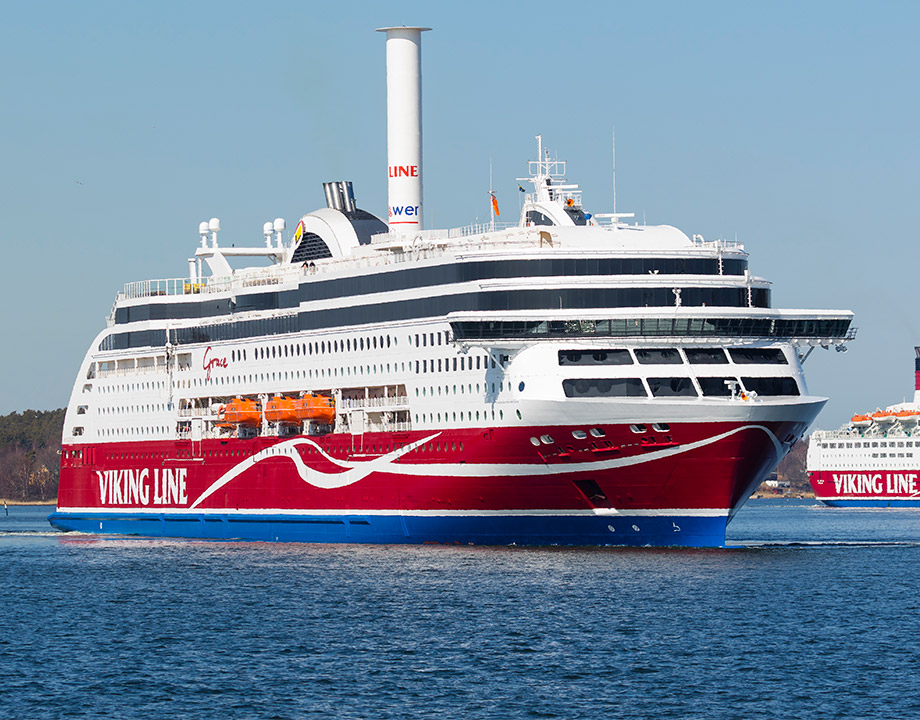
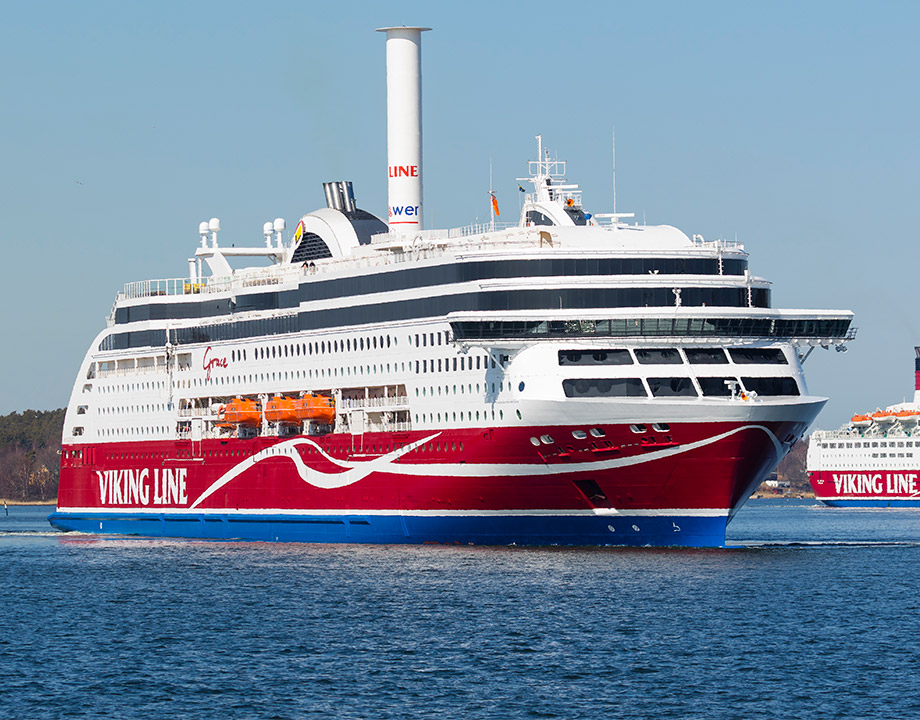