Leveraging Plastic Components for Solar-Powered Applications
Leveraging Plastic Components for Solar-Powered Applications
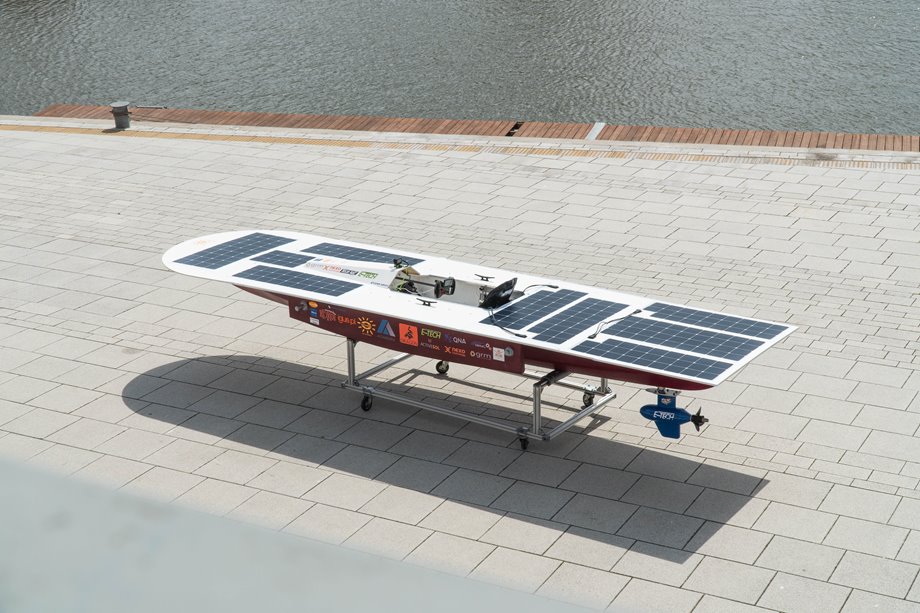
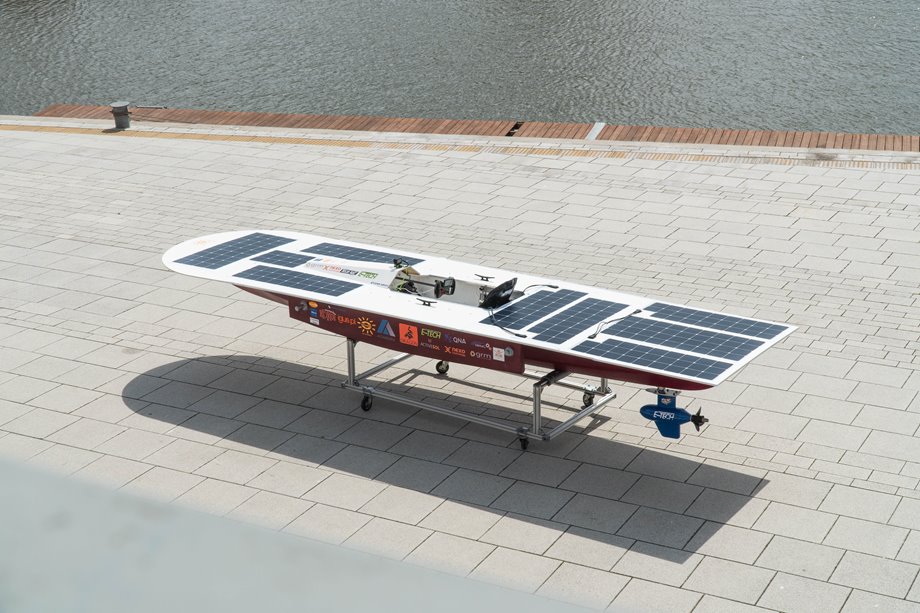
Students at an engineering school in Poland designed a solar-powered boat that included lubrication-free and seawater-resistant plastic bearings. Image: igus®
Sanford, FL, is perhaps most notable for its proximity to the abundant attractions in nearby Orlando. The city in the state’s central region is the county seat of Seminole, but there are no rollercoasters, princesses, or daily fireworks. Sanford, however, is home to wastewater management systems that rely almost exclusively on solar power.
The system is designed by Germany-based compnay HUBER. The treatment plant processes wet, thin sludge and converts it into dry granulate via solar power. The process results in reducing the sludge volume by 75 percent. Solar sludge drying also dramatically reduces sewage disposal costs and is far more environmentally friendly than incineration.
The innovative technology in the wastewater treatment systems produced by HUBER, which runs its North American operations from North Carolina, is one example of how many engineers are harnessing the power of solar energy.
Inside these systems, plastic components, like the ones developed by igus, the Germany-based manufacturer of motion plastics, are being used to develop products that rely on harnessing the sun’s power. Projects big and small are being designed that are environmentally friendly. As the appetite for more carbon-neutral products increases, more and more applications that rely on solar energy become widely available.
Recommended for You: Pandemic Spotlights on Innovation
The new frontier is here for mechanical engineers designing products with solar energy, and many of them are embracing it. Let’s explore some industry examples of how plastic components are being used in renewable energy applications.
The system installed in Sanford and several other United States municipalities is similar to Egypt’s largest wastewater treatment plant that treats flow from the The Bahr El-Baqar drainage channel, a waterway considered one of the most polluted tributaries globally. The facility in Egypt can treat up to 475,00 tons of sludge per year at a rate of 20 kWh per ton.
Like the system in Egypt, Sanford’s new plant is using solar power for wastewater treatment. In Egypt, the plant is able to generate 33.6 GWh per year of solar radiation that is used for solar drying. In Sanford, the amount of energy generated will equal 2,520 GWh.
While using solar energy to treat wastewater is not a revolutionary idea, doing so on a large scale is a far more recent development. More communities have considered solar power for its wastewater treatment in the past few years.
Orascom Construction and Arab Contractors were awarded over $700 million in 2018 to build the water treatment plant. HUBER manufactured 128 of its SOLSTICE® sludge turners for the project. The purification process produces large quantities of sludge during water treatment. The sludge is dewatered and dried by the solar-powered sludge turners to reduce the amount of sludge to be disposed. The units dry the sludge produced during water treatment to a quarter of the original size of the mass and volume of the sludge. The dry granules can then be used as fertilizer or as an efficient heating source.
The SOLSTICE® units operate in 16 greenhouses, each with eight lines. The turner travels on rails and repeatedly rearranges the sludge on the ground. During the movement, the sludge is dried by solar energy. At the end of the drying lane, the sludge turner picks up the dry granules in the tool that repositions the sludge during its forward movement. The dry material is relocated to a recess in the ground, then collected and transported to a container.
Among the critical components of the solar sludge dryers are plastic energy chains. The energy chains contain chainflex cables that provide reliable energy supply and data flow for the sludge turners.
The energy chains, each of which is about 100 meters, are one of the critical pieces of the SOLSTICE® units. The energy chains are self-lubricating, but their durability, easy installation, and maintenance were important factors for HUBER in the system’s design.
“Energy chains are the best solution for cable guidance on long travels,’’ said André Großer, HUBER SE product manager. “It requires little room, protects the cable, and is easy to install and maintain.”
Engineers considered festoons but found the energy chains to be a better solution. “The problem with festoons is that the cables are always moving,” Großer said. “The movement puts stress on the strands and necessitates more maintenance than is the case with energy chains. The festoon also hangs in the air, causing obstruction, and its trolley takes up valuable space.”
The chainflex cables, which provide reliable data transfer and energy supply, were also critical. The cables are designed specifically for use in energy chains. They also include an abrasion-resistant outer jacket and special interior stranding.
The chains include all of the proper cablings already in place, which reduces the number of suppliers and makes on-site installation easier. The chains are also pre-assembled, which allows for faster installation.
Finbin is developing a trash compactor that significantly reduces operating costs and the ecological footprint. The technology ensures that waste is compressed in a ratio of 6:1. The bin also automatically notifies the waste management system when it reaches capacity. While small in stature – units are approximately as tall as a standard outdoor grill – the bins can hold over 1,200 liters of litter.
Engineers designed the units using plastic bearings for the hatch, pedal and pedal rods. The bearings have high-wear resistance, and are also resistant to dirt and dust. The compactor opens via foot pedal – no touching is required – and stores the same amount of refuse as 20 traditional 60-liter street bins. Besides its solar power, the system also supports sustainability by significantly decreasing the carbon footprint of waste management.
While engineers explore new frontiers for harnessing solar energy and using it in applications, transportation that draws on the sun for power is one of the more enduring explorations by engineers. Teams worldwide are making significant progress, and many of them are young minds studying at prestigious universities.
You May Also Like: Space-Based Solar Power Offers Out-of-This World Challenges
In the United States, an ambitious group of undergraduate students launched the University of Minnesota Solar Vehicle Project in 1990, and three years later, designed its first solar car. Since then, the team has built 13 vehicles and has raced in 30 solar challenges on three continents.
A student team at the Wroclaw University of Science and Technology developed a solar-powered boat in Poland. The young engineers designed a boat that relies entirely on photovoltaic cells to ensure environmentally-friendly propulsion.
The car uses chainflex cables, while the boat designers installed lubrication-free and seawater-resistant iglide J bearings in the steering system. The bearings offer good chemical resistance, low moisture absorption, and effective for low-pressure loads. “They reduce overall system weight, eliminate lubricants, and are easy to install,” said Dominika Dewor of the PWr solar boat team.
Engineers are leaving no stone unturned in the quest to retrieve more energy from the sun. One of the most extreme applications is a single-axis solar tracking solution for large PV systems.
The ZIMMERMANN PV-Steel group from Germany has been developing, planning, and supplying substructures for solar projects since 2009. This includes the ZIM Track System.
The solar trackers move according to the sun’s path and can thus increase the energy yield by more than 30 percent compared to static solutions. The combination of steel and plastic provides the tracker with a particularly robust, durable, and functional design, guaranteeing low maintenance.
The pedestal bearings connect the profiles of the PV system. An adjustable bearing consists of two half-shells made of plastic (i.e., a housing connected to the metal frame and an inner part mounted inside.) The parts are made of lubricant-free and UV-resistant high-performance plastic that is robust even when exposed to high temperatures or dirt. The upper part is a metal bracket manufactured by ZIMMERMANN. The division into a lower and an upper part allows for easy assembly and disassembly.
Editor’s Pick: The New Job Market in the Green Economy
Despite its low overall weight, this solution is suitable for storing heavy loads of up to 1.5 tons. Due to the overall structural design, the rows of solar panels in the ZIM Track System can be up to 96 meters long. The ZIMMERMANN PV trackers are located in Europe, Australia, and South America, among other countries.
While terms such as net-zero, sustainability, and reducing greenhouse emissions have been discussed for decades, there finally appears to be sustained and consistent movement toward developing technologies that will help tackle the climate crisis. Engineers and their brilliant innovations are leading the way in the revolution. There are no limits, just possibilities, and an entire world is ready to accept change. It is coming.
“As a company that is working in the environment, we are always looking for solutions,’’ said Großer, the product manager at HUBER. “We not only want to make water clean, but we also want to reduce our reliance on electric energy. We are developing the process, and we are on the right track. In any project, we are concerned about the environmental impact and look for the best practices to protect our environment.”
Thomas Renner is a technology writer and public relations executive for igus.
The system is designed by Germany-based compnay HUBER. The treatment plant processes wet, thin sludge and converts it into dry granulate via solar power. The process results in reducing the sludge volume by 75 percent. Solar sludge drying also dramatically reduces sewage disposal costs and is far more environmentally friendly than incineration.
The innovative technology in the wastewater treatment systems produced by HUBER, which runs its North American operations from North Carolina, is one example of how many engineers are harnessing the power of solar energy.
Inside these systems, plastic components, like the ones developed by igus, the Germany-based manufacturer of motion plastics, are being used to develop products that rely on harnessing the sun’s power. Projects big and small are being designed that are environmentally friendly. As the appetite for more carbon-neutral products increases, more and more applications that rely on solar energy become widely available.
Recommended for You: Pandemic Spotlights on Innovation
The new frontier is here for mechanical engineers designing products with solar energy, and many of them are embracing it. Let’s explore some industry examples of how plastic components are being used in renewable energy applications.
Plastic Chains for Energy Supply
The system installed in Sanford and several other United States municipalities is similar to Egypt’s largest wastewater treatment plant that treats flow from the The Bahr El-Baqar drainage channel, a waterway considered one of the most polluted tributaries globally. The facility in Egypt can treat up to 475,00 tons of sludge per year at a rate of 20 kWh per ton.
Like the system in Egypt, Sanford’s new plant is using solar power for wastewater treatment. In Egypt, the plant is able to generate 33.6 GWh per year of solar radiation that is used for solar drying. In Sanford, the amount of energy generated will equal 2,520 GWh.
While using solar energy to treat wastewater is not a revolutionary idea, doing so on a large scale is a far more recent development. More communities have considered solar power for its wastewater treatment in the past few years.
Orascom Construction and Arab Contractors were awarded over $700 million in 2018 to build the water treatment plant. HUBER manufactured 128 of its SOLSTICE® sludge turners for the project. The purification process produces large quantities of sludge during water treatment. The sludge is dewatered and dried by the solar-powered sludge turners to reduce the amount of sludge to be disposed. The units dry the sludge produced during water treatment to a quarter of the original size of the mass and volume of the sludge. The dry granules can then be used as fertilizer or as an efficient heating source.
The SOLSTICE® units operate in 16 greenhouses, each with eight lines. The turner travels on rails and repeatedly rearranges the sludge on the ground. During the movement, the sludge is dried by solar energy. At the end of the drying lane, the sludge turner picks up the dry granules in the tool that repositions the sludge during its forward movement. The dry material is relocated to a recess in the ground, then collected and transported to a container.
Among the critical components of the solar sludge dryers are plastic energy chains. The energy chains contain chainflex cables that provide reliable energy supply and data flow for the sludge turners.
The energy chains, each of which is about 100 meters, are one of the critical pieces of the SOLSTICE® units. The energy chains are self-lubricating, but their durability, easy installation, and maintenance were important factors for HUBER in the system’s design.
“Energy chains are the best solution for cable guidance on long travels,’’ said André Großer, HUBER SE product manager. “It requires little room, protects the cable, and is easy to install and maintain.”
Engineers considered festoons but found the energy chains to be a better solution. “The problem with festoons is that the cables are always moving,” Großer said. “The movement puts stress on the strands and necessitates more maintenance than is the case with energy chains. The festoon also hangs in the air, causing obstruction, and its trolley takes up valuable space.”
The chainflex cables, which provide reliable data transfer and energy supply, were also critical. The cables are designed specifically for use in energy chains. They also include an abrasion-resistant outer jacket and special interior stranding.
The chains include all of the proper cablings already in place, which reduces the number of suppliers and makes on-site installation easier. The chains are also pre-assembled, which allows for faster installation.
Smaller Scale Projects
Finbin is developing a trash compactor that significantly reduces operating costs and the ecological footprint. The technology ensures that waste is compressed in a ratio of 6:1. The bin also automatically notifies the waste management system when it reaches capacity. While small in stature – units are approximately as tall as a standard outdoor grill – the bins can hold over 1,200 liters of litter.
Engineers designed the units using plastic bearings for the hatch, pedal and pedal rods. The bearings have high-wear resistance, and are also resistant to dirt and dust. The compactor opens via foot pedal – no touching is required – and stores the same amount of refuse as 20 traditional 60-liter street bins. Besides its solar power, the system also supports sustainability by significantly decreasing the carbon footprint of waste management.
Solar-Powered Transportation
While engineers explore new frontiers for harnessing solar energy and using it in applications, transportation that draws on the sun for power is one of the more enduring explorations by engineers. Teams worldwide are making significant progress, and many of them are young minds studying at prestigious universities.
You May Also Like: Space-Based Solar Power Offers Out-of-This World Challenges
In the United States, an ambitious group of undergraduate students launched the University of Minnesota Solar Vehicle Project in 1990, and three years later, designed its first solar car. Since then, the team has built 13 vehicles and has raced in 30 solar challenges on three continents.
A student team at the Wroclaw University of Science and Technology developed a solar-powered boat in Poland. The young engineers designed a boat that relies entirely on photovoltaic cells to ensure environmentally-friendly propulsion.
The car uses chainflex cables, while the boat designers installed lubrication-free and seawater-resistant iglide J bearings in the steering system. The bearings offer good chemical resistance, low moisture absorption, and effective for low-pressure loads. “They reduce overall system weight, eliminate lubricants, and are easy to install,” said Dominika Dewor of the PWr solar boat team.
Solar Tracking Systems
Engineers are leaving no stone unturned in the quest to retrieve more energy from the sun. One of the most extreme applications is a single-axis solar tracking solution for large PV systems.
The ZIMMERMANN PV-Steel group from Germany has been developing, planning, and supplying substructures for solar projects since 2009. This includes the ZIM Track System.
The solar trackers move according to the sun’s path and can thus increase the energy yield by more than 30 percent compared to static solutions. The combination of steel and plastic provides the tracker with a particularly robust, durable, and functional design, guaranteeing low maintenance.
The pedestal bearings connect the profiles of the PV system. An adjustable bearing consists of two half-shells made of plastic (i.e., a housing connected to the metal frame and an inner part mounted inside.) The parts are made of lubricant-free and UV-resistant high-performance plastic that is robust even when exposed to high temperatures or dirt. The upper part is a metal bracket manufactured by ZIMMERMANN. The division into a lower and an upper part allows for easy assembly and disassembly.
Editor’s Pick: The New Job Market in the Green Economy
Despite its low overall weight, this solution is suitable for storing heavy loads of up to 1.5 tons. Due to the overall structural design, the rows of solar panels in the ZIM Track System can be up to 96 meters long. The ZIMMERMANN PV trackers are located in Europe, Australia, and South America, among other countries.
Sustainable Engineering
While terms such as net-zero, sustainability, and reducing greenhouse emissions have been discussed for decades, there finally appears to be sustained and consistent movement toward developing technologies that will help tackle the climate crisis. Engineers and their brilliant innovations are leading the way in the revolution. There are no limits, just possibilities, and an entire world is ready to accept change. It is coming.
“As a company that is working in the environment, we are always looking for solutions,’’ said Großer, the product manager at HUBER. “We not only want to make water clean, but we also want to reduce our reliance on electric energy. We are developing the process, and we are on the right track. In any project, we are concerned about the environmental impact and look for the best practices to protect our environment.”
Thomas Renner is a technology writer and public relations executive for igus.
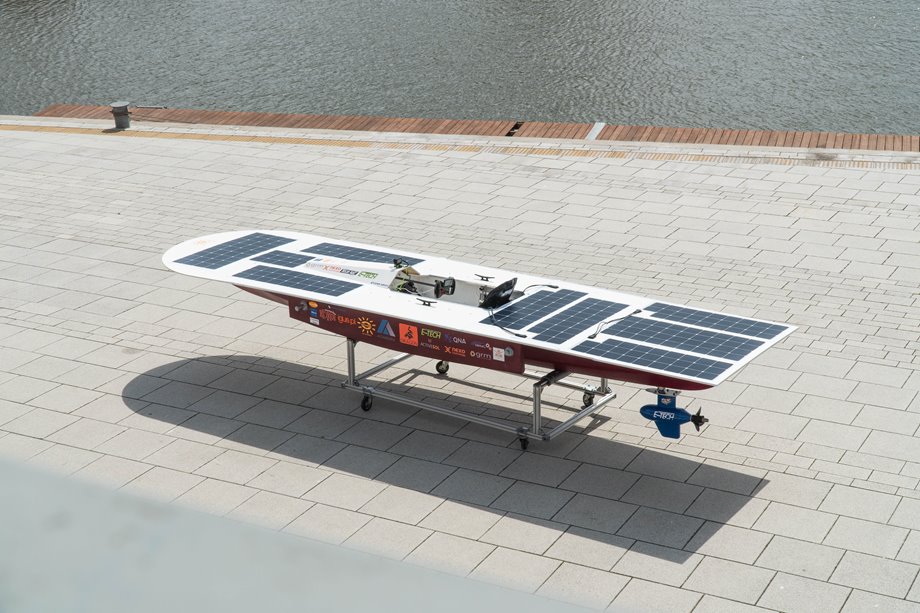
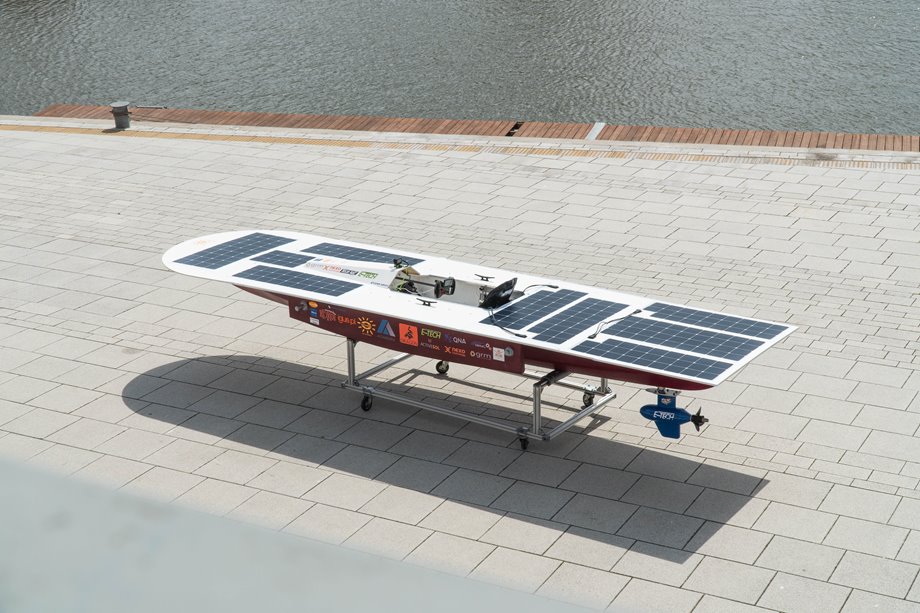