Making Polymers for Lithium-ion Batteries from Waste Plastic Bottles
Making Polymers for Lithium-ion Batteries from Waste Plastic Bottles
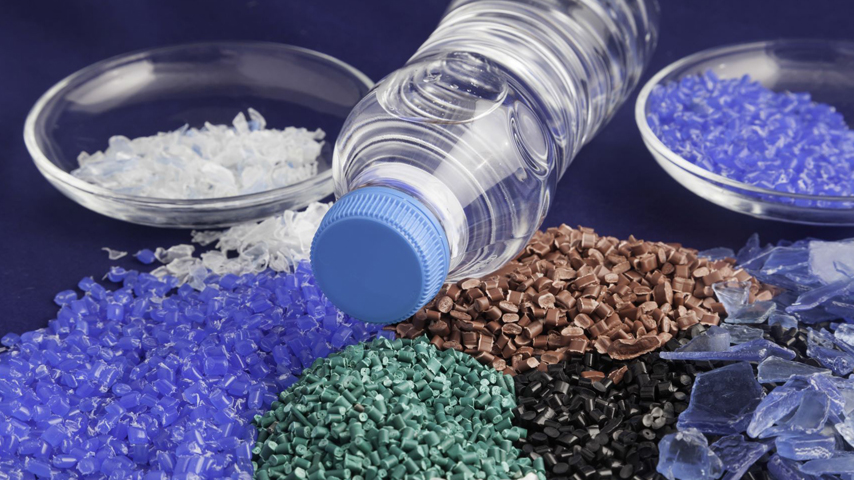
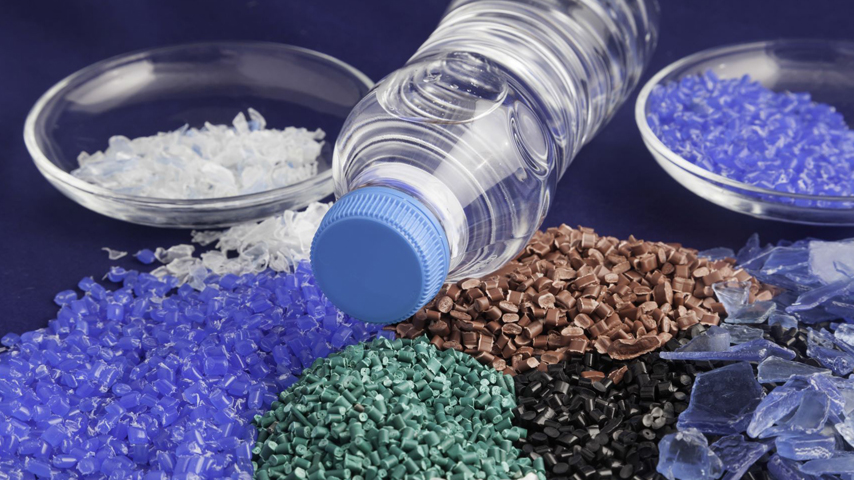
A team of Singapore scientists has developed a way to make polymer electrolytes, which are key components for safer lithium-ion batteries, from waste polyethylene terephthalate (PET) plastic bottles.
To turn trash into treasure, a team of Singapore scientists from the Agency for Science, Technology and Research (A*STAR) explored the potential of discarded water bottles by transforming them into lithium-ion battery components for useful energy storage.
Problem meets solution
PET (Polyethylene terephthalate) plastic is a ubiquitous material globally, creating good opportunities for upcycling due to its abundant material supply. Indeed, plastic waste is a huge problem, with PET plastic water bottles being a major culprit. In the U.S., plastic bottled water sales have grown from a mere 2.8 billion units in 1996 to 70.7 million units in 2018.
While conventional science is slowly increasing the percentage of recycled PET content—less than 5 percent in 1996 to 11.5 percent in 2020, according to CRI—municipalities across the globe are also creating programs that not only collect plastic but clean it, which removes the need to manufacture new containers from virgin materials.
Striving to design future sustainable polymer electrolyte (PE) materials from waste plastics is a good approach as the main consideration to have a continuous and reliable line of feedstock. This is why the team of researchers from A*STAR tapped on PET, which is readily available.
Become a Member: How to Join ASME
According to Derrick Fam, deputy head of the Polymer Composites department at A*STAR’s Institute of Materials Research and Engineering (IMRE), who led this study together with Jason Lim, deputy head of the Soft Materials department at IMRE, PET is amongst the most collected waste plastics in the world, with the added benefit of possessing well-established waste collection logistics.
Fam noted that PET has other favorable properties that make it the perfect material. “It can be easily converted to small molecules using mild reaction conditions with readily available reagents, where rigid fragments in the polymer structure gives the polymer electrolytes structural rigidity,” he said.
What and how
PET bottles are essentially made of chemically linked long polymer molecules. “One of the first few crucial steps in turning PET bottles into something useful would be to ‘break’ these chemically linked molecules up into shorter molecules in a process called depolymerization,” Lim explained. “That way we can then use the new material for different purposes, such as new functional materials.”
Positioning these waste plastics at the beginning of the value chain as a feedstock for functional materials production seems like a successful strategy. PETs are used as containers (bottles, packaging, textiles, etc.) because of their rigidity. “Beyond its abundance, the structural properties of PET provide strength and rigidity to future batteries,” Lim explained.
Mechanical strength is important in batteries as they are used in applications where the devices are charged and discharged, sometimes at a high current (for fast charging). Under repeated charging and discharging, the overall shape of the anode inside the battery sometimes changes and if it distorts too much, the anode can come in contact with the cathode, causing a short circuit which could result in fires.
More for You: A New Enzyme Eats Plastics
“This is a phenomenon that is common in liquid electrolytes as there is no physical barrier strong enough to prevent this from happening. Using PET-derivative as an electrolyte can potentially mitigate that by reducing the ability for the anode to distort and cause a short circuit,” Fam said.
PEs are promising alternative components in batteries not only because they may eliminate safety hazards such as the risks of electrolyte leakage, uncontrolled heating, volume expansion, and fire hazards, but also dendrite growth.
How does it work?
The team obtained PEs from PET bottles by taking advantage of the susceptibility of PET’s ester linkages for chemical solvolysis and the structural rigidity of the terephthalate aromatic components. They also found that the material also allows for free-standing conductive film formation.
Furthermore, the PET-derived polyurethane PEs showed ionic conductivity when used as both solid and gel polymer electrolytes, which allowed it to be assembled into a working lithium-ion battery.
Findings from the study showed the potential of the polyurethanes derived from waste PET as polymer electrolytes for LiBs including the ability to achieve a room room-temperature conductivity comparable to existing commercial systems containing liquid electrolytes. The team successfully assembled working LiB using these polymers, was repeatedly charged, and discharged up to 150 cycles.
Feasibility
“This promising performance paves the way for a future powered by more sustainable energy,” said Fam. But how feasible is it for PET plastic waste to be turned into PE materials for use in batteries?
The feasibility of the scheme “depends” on some “push and pull” factors, Fam explained.
Secondly, the team envisions that the cost of developing a process that can produce these PET batteries will be palatable to startups as they have the agility to pivot their manufacturing processes to adapt to new formats and materials. Therefore, if the benefits (using sustainable and cost-effective materials like PETs) can outweigh the cost of processing, this is definitely a viable solution to companies.
Finally, the scientists’ work is on the proof of the concept of upcycling sustainable plastics (e.g. PET) for high value applications (e.g. energy storage). In their current form, the PET-based batteries can only power devices that require low energy. This is because engineering processes that can achieve an optimized dimension for higher ionic conductivity (ionic conductivity is important to achieve higher power in a battery) are currently not at a mature stage.
The key to success will be its ability to optimize the performance of these upcycled plastic-based batteries. The team at A*STAR’s IMRE plan to improve the design of polymer electrolyte materials from more sustainable feedstock. They also plan to further “green” the synthesis process of polymer electrolytes by using even milder synthesis conditions than those used in their existing processes.
Cathy Cecere is Membership Content Program Manager.
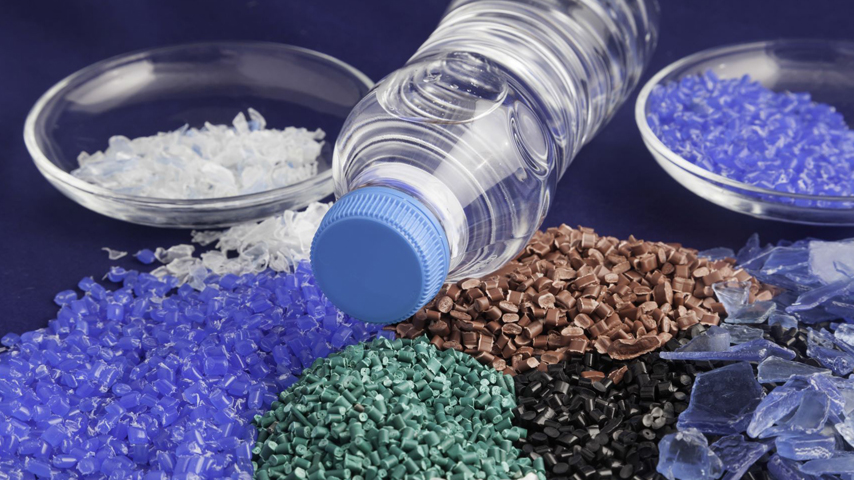
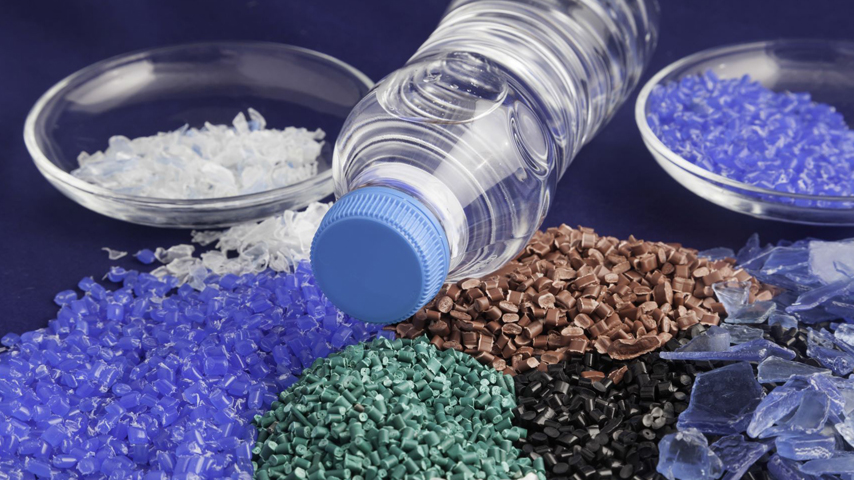