Microstructures and Mechanical Engineers
Microstructures and Mechanical Engineers
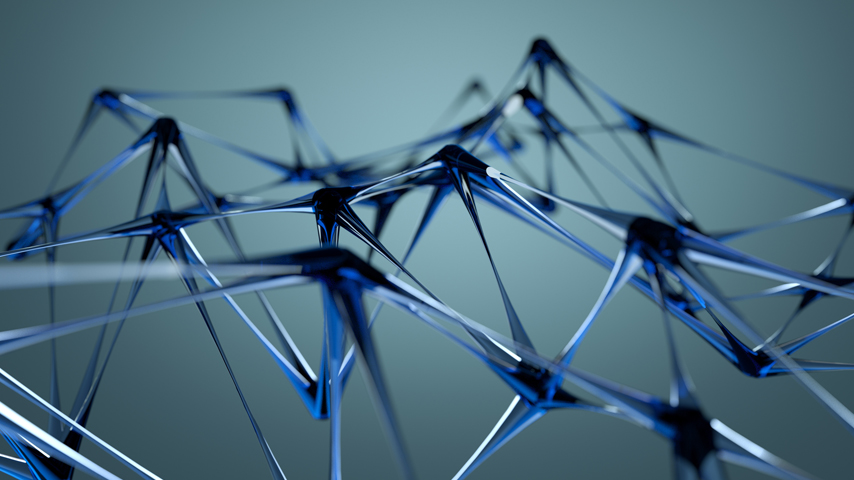
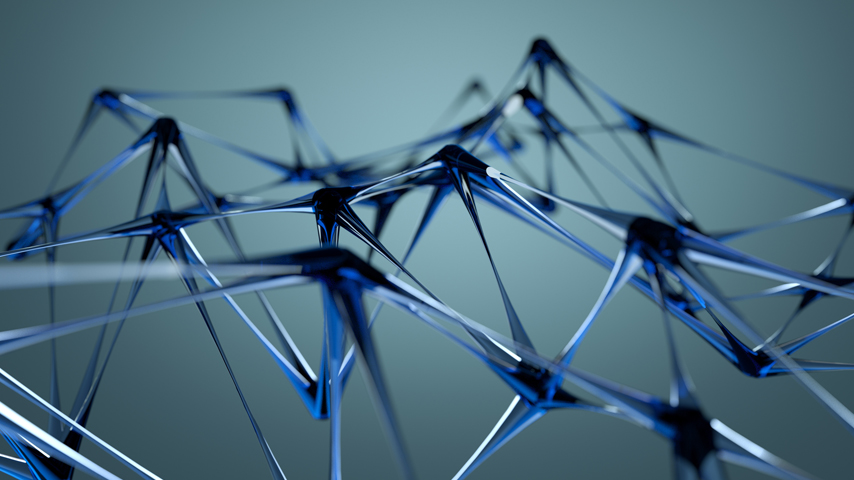
Additive manufacturing is changing the way microstructures are formed and studied. AM allows them to be made with unprecedented precision and complexity.
Mechancial engineers have traditionally viewed materials from the standpoint of their properities and associated mechanical behaviors. The paradigm now is shifting as computational micromechanics methods and codes assist in understanding what to focus on in control of material processing that gives rise to microstructures that improve performance, according to researchers and engineers. Understanding microstructures can be both an art and a science that takes MEs years to become proficient. This second installment of a two-part series on microstructures looks at validation, advances, and the changing role of mechanical engineers in working with them.
Microstructures used in commercial products must be thoroughly reviewed, tested, and validated to ensure they are reliable and safe for their intended uses. This process typically involves experimental testing and computational simulations to assess the performance of the microstructures and how the component will perform.
The level of testing typically depends on the application and the risk tolerance of the industry.
“Industries such as aerospace and nuclear will be very risk adverse,” said Matthew Daly, assistant professor in the Department of Civil, Materials, and Environmental Engineering at the University of Illinois in Chicago. “There are standard test methods that are maintained by professional/technical societies. Typically, a material must have a long track record and well-understood performance before it will be accepted in a risk-adverse field.”
For example, microstructures used in critical components such as turbine blades must undergo rigorous testing to ensure they can withstand the high temperatures and stresses of operation. The testing may include mechanical testing, thermal cycling, and environmental exposure to simulate the conditions the microstructures will experience in service.
Become a Member: How to Join ASME
“Actually, there are very few standards that specify microstructures,” said Anthony Rollett, professor of metallurgical engineering and materials science at Carnegie Mellon University in Pittsburgh, “It is much more common to specify processing sequences that constrain the resulting microstructure.”
Historically, the variability or uncertainty of existing materials is based on experimentally measured microstructures and properties. Increasingly, material scientists seek new ways of estimating uncertainty based on computational materials science and mechanics.
“This becomes even more important as we move toward discovery and design of new or improved materials that have not previously existed,” said David McDowell, professor of mechanical engineering and materials science at Georgia Institute of Technology in Atlanta. “There is an even stronger role for predictive simulations of new properties that characterize uncertainty, suggesting experiments that are necessary to further characterize and ensure reliable, safe implementation in new products.”
There have been many exciting advances in microstructures in recent years. Here are just a few:
“Advances are especially being made in laser powder bed fusion, a slow but quite reliable technology for making metal parts in a wide range of alloys, with tolerances on the order of 100 microns,” said Rollett.
Additive manufacturing techniques can produce microstructures with a wide range of materials, including polymers, metals, ceramics, and composites, offering engineers a broad range of options for designing and creating microstructures tailored to specific applications. Research is also being carried out on how to combine artificial intelligence (AI) and AM to create better geometries, design flexibility, and reduced production time and cost.
“The whole area of AI and design is untapped in terms of using AI to help design optimum structure-properties-manufacturing relationships,” said Mary Wells, dean of engineering at the University of Waterloo in Waterloo, Ontario,. “For example, AI should be helpful in identifying the best materials and microstructures spatially depending on what is needed at different locations based on sustainability, design, and property requirements, such as corrosion resistance versus bulk properties.”
Microstructures are becoming increasingly important in many areas of mechanical engineering, including materials science, manufacturing, and design. As such, it is important for mechanical engineers to have a good understanding of microstructures and their effects on materials and systems. This knowledge will help them create enhanced material properties, expand novel design options, and improve performance and functionality of their products.
Today’s mechanical engineering degree programs at universities typically offer courses that interface mechanics of materials with microstructure. It may be advisable to take some courses across disciplines, for example in materials science, that integrate well with mechanics of materials and design. Modern data science courses are sometimes offered in computer science departments or engineering departments that integrate digital materials information. Attending workshops and conferences related to microstructures can be an excellent way to learn about the latest advances and network with other professionals in the field. These events may be organized by professional associations, research institutions, or industry groups.
Editor’s Pick: New Metal Alloy Is Stronger than the Toughest Aerospace Materials
“Participating in research projects related to microstructures can provide hands-on experience and help mechanical engineers develop practical skills,” said Wells. “This may involve working as a research assistant or intern in a laboratory or research group.”
Certainly, mechanical engineers today should strive to be conversant with materials engineers and manufacturing engineers.
“While their roles and capabilities are distinct, accelerated materials development and integrated materials and product design work best when they understand each other and can communicate effectively,” said McDowell. “I would advise anyone interested to spend some time on the QuesTek LLC website to learn about what their mechanical engineers and material scientists are doing to design and develop new and improved materials with significant performance.”
Mark Crawford is a science and technology writer in Corrales, N.M.
The first installment in this two-part series on microstructures was posted on May 23, and can be viewed here: https://www.asme.org/topics-resources/content/microstructures-improve-design-and-function
Microstructures used in commercial products must be thoroughly reviewed, tested, and validated to ensure they are reliable and safe for their intended uses. This process typically involves experimental testing and computational simulations to assess the performance of the microstructures and how the component will perform.
The level of testing typically depends on the application and the risk tolerance of the industry.
“Industries such as aerospace and nuclear will be very risk adverse,” said Matthew Daly, assistant professor in the Department of Civil, Materials, and Environmental Engineering at the University of Illinois in Chicago. “There are standard test methods that are maintained by professional/technical societies. Typically, a material must have a long track record and well-understood performance before it will be accepted in a risk-adverse field.”
For example, microstructures used in critical components such as turbine blades must undergo rigorous testing to ensure they can withstand the high temperatures and stresses of operation. The testing may include mechanical testing, thermal cycling, and environmental exposure to simulate the conditions the microstructures will experience in service.
Become a Member: How to Join ASME
“Actually, there are very few standards that specify microstructures,” said Anthony Rollett, professor of metallurgical engineering and materials science at Carnegie Mellon University in Pittsburgh, “It is much more common to specify processing sequences that constrain the resulting microstructure.”
Historically, the variability or uncertainty of existing materials is based on experimentally measured microstructures and properties. Increasingly, material scientists seek new ways of estimating uncertainty based on computational materials science and mechanics.
“This becomes even more important as we move toward discovery and design of new or improved materials that have not previously existed,” said David McDowell, professor of mechanical engineering and materials science at Georgia Institute of Technology in Atlanta. “There is an even stronger role for predictive simulations of new properties that characterize uncertainty, suggesting experiments that are necessary to further characterize and ensure reliable, safe implementation in new products.”
Exciting advances
There have been many exciting advances in microstructures in recent years. Here are just a few:
- Advanced 3D printing technology makes it possible to create microstructures with unprecedented precision and complexity.
- Techniques such as atomic layer deposition (ALD) and molecular beam epitaxy (MBE) can create microstructures with sub-nanometer precision.
- Microstructures inspired by nature have been developed to mimic the properties of biological materials and organisms.
- Microstructures play increasing key roles in the development solar cells, fuel cells, and batteries, which increase energy density and reduce charging time.
- MEs use microstructures to create surfaces that are highly water-repellent (superhydrophobic).
- Additive manufacturing is a highly transformative technology and the microstructure-property relationships created by AM are still not very well understood. Because AM methods typically involve high-energy deposition followed by rapid cooling, the fine-scale structures are challenging to control, and emphasis is placed more on the morphologies of microstructures that emerge, including orientation, and their influence on properties.
“Advances are especially being made in laser powder bed fusion, a slow but quite reliable technology for making metal parts in a wide range of alloys, with tolerances on the order of 100 microns,” said Rollett.
Additive manufacturing techniques can produce microstructures with a wide range of materials, including polymers, metals, ceramics, and composites, offering engineers a broad range of options for designing and creating microstructures tailored to specific applications. Research is also being carried out on how to combine artificial intelligence (AI) and AM to create better geometries, design flexibility, and reduced production time and cost.
“The whole area of AI and design is untapped in terms of using AI to help design optimum structure-properties-manufacturing relationships,” said Mary Wells, dean of engineering at the University of Waterloo in Waterloo, Ontario,. “For example, AI should be helpful in identifying the best materials and microstructures spatially depending on what is needed at different locations based on sustainability, design, and property requirements, such as corrosion resistance versus bulk properties.”
Microstructure and the role of the ME
Microstructures are becoming increasingly important in many areas of mechanical engineering, including materials science, manufacturing, and design. As such, it is important for mechanical engineers to have a good understanding of microstructures and their effects on materials and systems. This knowledge will help them create enhanced material properties, expand novel design options, and improve performance and functionality of their products.
Today’s mechanical engineering degree programs at universities typically offer courses that interface mechanics of materials with microstructure. It may be advisable to take some courses across disciplines, for example in materials science, that integrate well with mechanics of materials and design. Modern data science courses are sometimes offered in computer science departments or engineering departments that integrate digital materials information. Attending workshops and conferences related to microstructures can be an excellent way to learn about the latest advances and network with other professionals in the field. These events may be organized by professional associations, research institutions, or industry groups.
Editor’s Pick: New Metal Alloy Is Stronger than the Toughest Aerospace Materials
“Participating in research projects related to microstructures can provide hands-on experience and help mechanical engineers develop practical skills,” said Wells. “This may involve working as a research assistant or intern in a laboratory or research group.”
Certainly, mechanical engineers today should strive to be conversant with materials engineers and manufacturing engineers.
“While their roles and capabilities are distinct, accelerated materials development and integrated materials and product design work best when they understand each other and can communicate effectively,” said McDowell. “I would advise anyone interested to spend some time on the QuesTek LLC website to learn about what their mechanical engineers and material scientists are doing to design and develop new and improved materials with significant performance.”
Mark Crawford is a science and technology writer in Corrales, N.M.
The first installment in this two-part series on microstructures was posted on May 23, and can be viewed here: https://www.asme.org/topics-resources/content/microstructures-improve-design-and-function
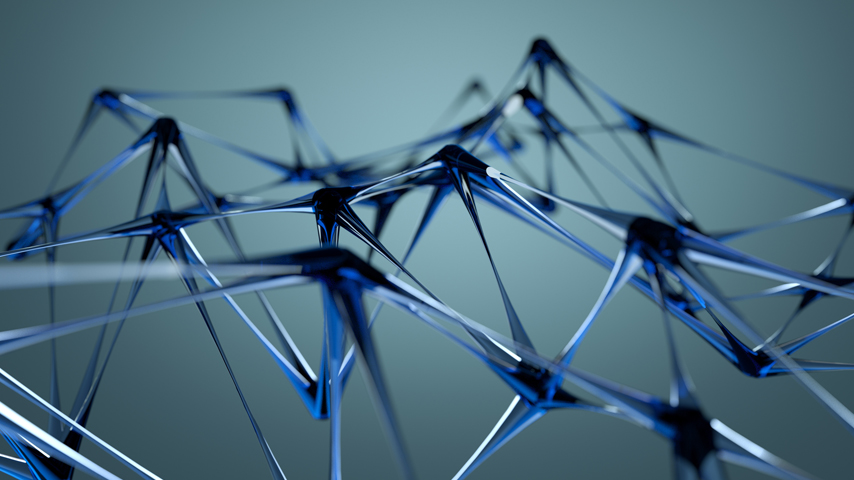
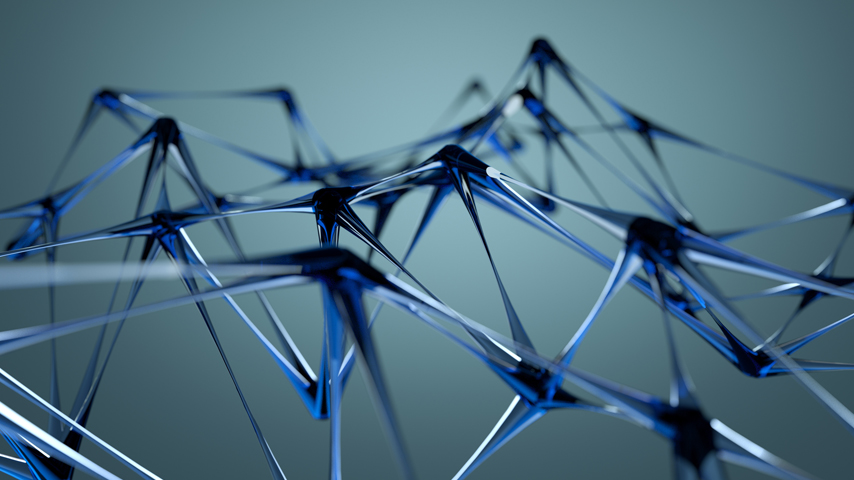