Next Gen Concrete Warms from Within
Next Gen Concrete Warms from Within
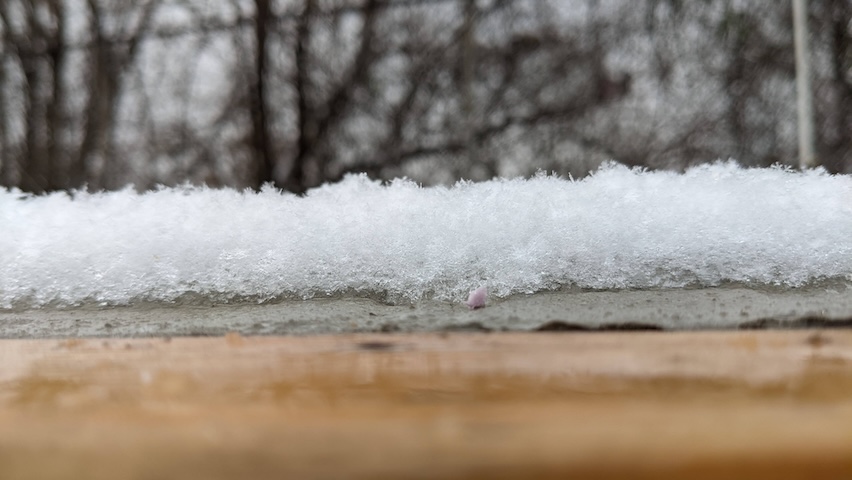
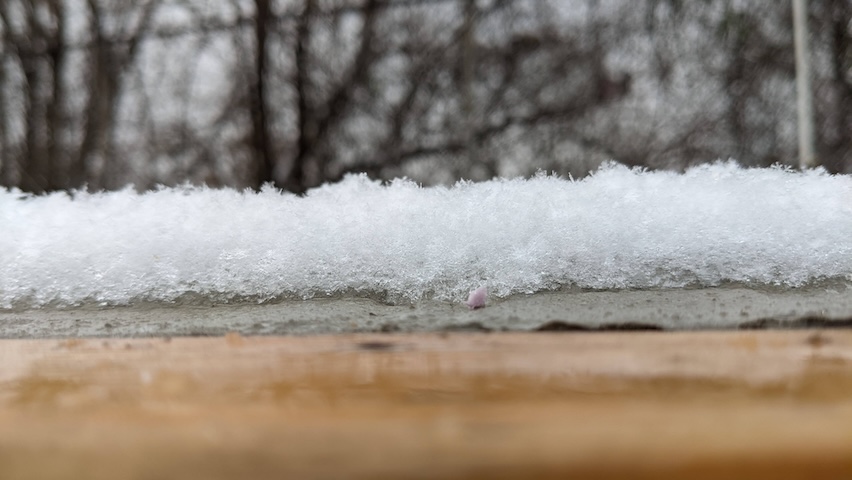
A phase-change material integrated into concrete could reduce the need for shoveling and plowing snow.
On Drexel University’s campus, two modest 30-inch-by-30-inch concrete slabs are demonstrating a potential frost-free future for sidewalks and highways across the Northeast. Located near a parking lot for university vehicles, these slabs have successfully resisted snow, sleet, and freezing rain autonomously for more than three years, eliminating the need for shoveling, salting, or scraping.
Researchers from Drexel’s College of Engineering have unveiled the science behind this self-heating concrete, which is a phase-change material (PCM) that activates as temperatures near freezing. This innovation is part of broader efforts to develop more sustainable and resilient infrastructure, especially in areas where winter weather significantly impacts maintenance budgets and road safety.
The team has been testing two concrete slabs, one embedded with phase-change material and the other a control slab, since December 2021. These slabs have faced 32 freeze-thaw events and five significant snowfalls. Equipped with cameras and thermal sensors, the researchers observed that the phase-change slabs maintain temperatures between 42 °F to 55 °F for up to 10 hours in sub-freezing conditions.
More for You: Designing Better Concrete for SMRs
Although this heating effectively melted about a quarter inch of snow per hour, enhancing road deicing and transportation safety, it has not yet been enough to replace plowing during heavy snow events.
“Our research goals are focused on achieving successful integration of innovative technology in real-time applications,” said Robin Deb, a doctoral student at Drexel Engineering’s College of Engineering. “The concept of using low-temperature PCM has been touted by several researchers for developing deicing and self-heating concrete. Our work has bridged the gap between conceptualization and practical application in real-time conditions. We found that PCM-integrated concrete can demonstrate melting on top surfaces during snow and reduction of freezing and thawing cycles in the element, which improves longevity of concrete.”
Refining Applications
Further research into PCM-incorporated concrete will explore improving its use in ice clearing situations and developing both the materials and thermodynamics necessary for improved deicing and self-healing properties.
“We studied the thermal response of the PCM-incorporated concrete in outdoor conditions over three winter cycles,” Deb said. “We have valuable data of snow melting, reduction of frosting cycles, concrete strength, and stability of PCM. This knowledge is essential to develop an improved and efficient version of PCM-integrated concrete, tailored for achieving a better success rate in snow melting. Thermodynamic modeling can also be performed using real-time experimental knowledge, which may open more possibilities.”
In a comparative study, Drexel researchers found that slabs made from lightweight aggregate treated with PCM sustained heat longer, maintaining temperatures above freezing for up to 10 hours. In contrast, slabs containing microencapsulated PCM heated up faster, but could only retain warmth for about five hours.
This difference in performance is dependent upon the PCM distribution—more evenly within the aggregate and more concentrated within microcapsules. The porosity of the aggregate helps keep the paraffin in a liquid state below its typical freezing point, delaying heat release until the temperature drops to 39 °F, unlike the microencapsulated paraffin, which releases heat at 42 °F. The gradual heat release and broader temperature range make the lightweight aggregate concrete more effective for deicing at sub-zero temperatures.
Discover the Benefits of ASME Membership
Achieving these milestones has come with challenges. Concrete is somewhat fragile and it’s also affected by time. Although additives can help concrete mixtures achieve desired research properties, researchers then face the difficulty of replicating climates where this concrete might be used.
“Freshly mixed concrete is sensitive to interfacial features and strong bond formation between additives is critical for strength development,” Deb explained. “Another challenge was the comprehensive understanding of ambient climactic conditions before and during snowfall. We found that these conditions play a critical role on heat flux properties of PCM-integrated concrete.”
So far, the team has seen promising results in preventing snow and ice accumulation on pavement. PCM within the concrete can effectively raise temperatures to between 53 °F and 55 °F, sufficient to melt snowfalls of less than two inches. However, performance declines with heavier snowfall and when the PCM doesn’t have time to recharge between events.
These findings highlight the PCM’s potential to reduce the need for pre-salting and improve freeze-thaw durability, suggesting a more sustainable alternative to traditional concrete.
For now, the research team is aiming to optimize this technology further, focusing on enhancing heating duration and melting capacity, which could significantly extend the lifespan of concrete infrastructures under seasonal weather conditions.
Jim Romeo is a technology writer in Chesapeake, Va.
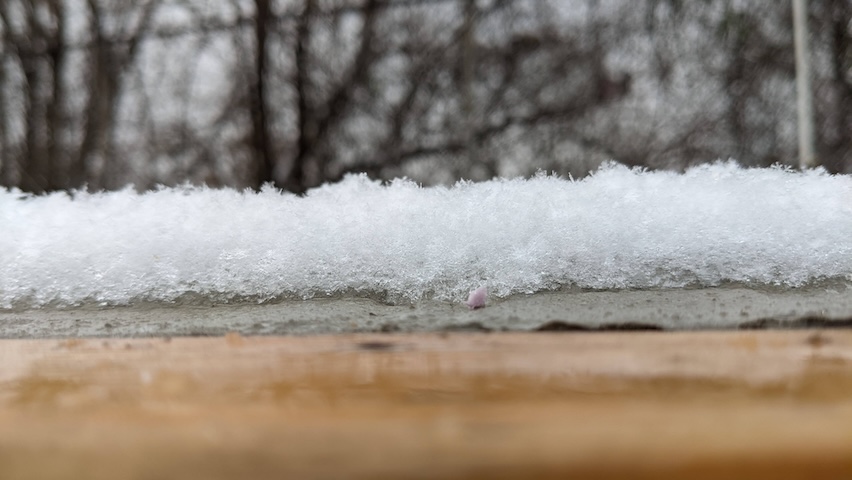
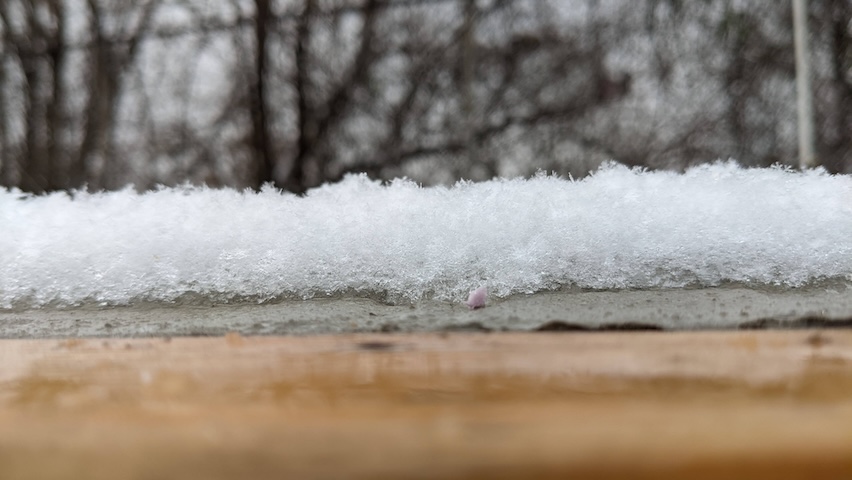