One Device to Grip Them All
One Device to Grip Them All
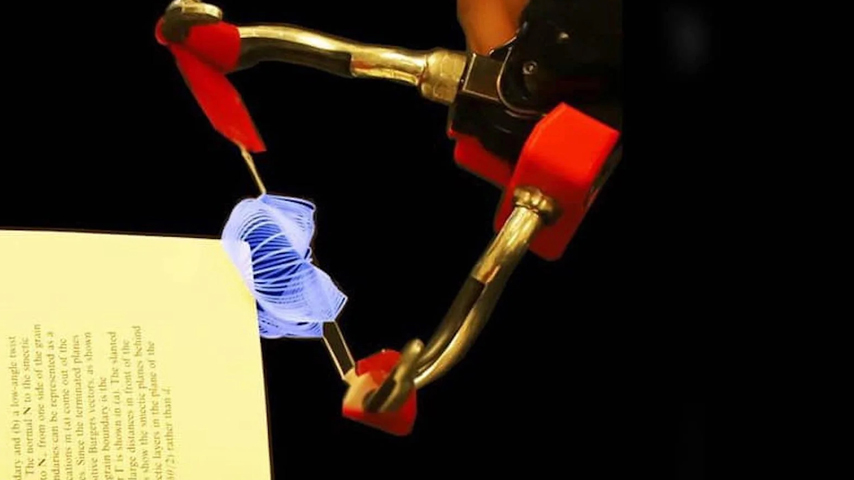
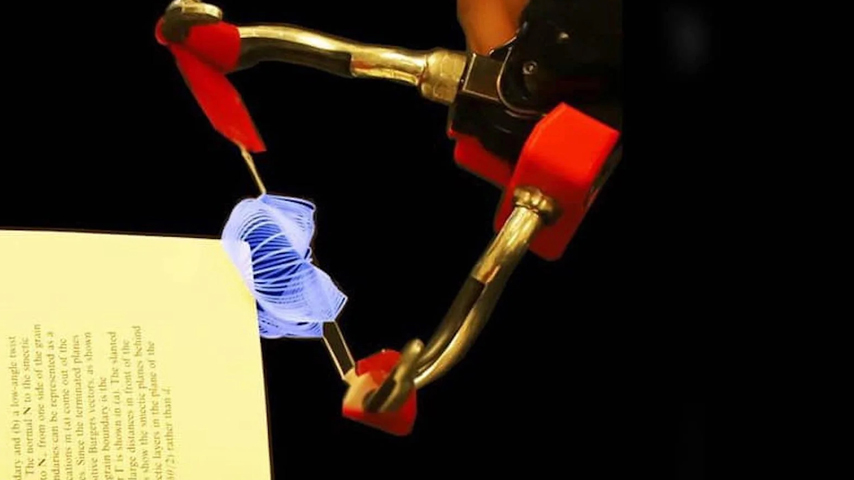
Researchers at North Carolina State University have developed a new robotic gripping device that manages to balance both strength and delicacy.
As engineers have attempted to design robots for different tasks, they’ve hit upon one major challenge: how to handle objects. Over the past decade, roboticists have come up with a variety of different gripper designs in hopes of finding a solution that allows robots to pick up, hold, and transfer objects with the appropriate force. Those designs, for the most part, were application specific—firm, two-jaw grippers to manage sturdier objects, soft grippers to manipulate more delicate items.
Now, however, researchers at North Carolina State University have developed a new gripper design that can handle ultrasoft, ultrathin, and heavy objects with ease.
Many jobs
“We wanted to develop one gripper for all,” said Jie Yin, an associate professor of mechanical and aerospace engineering at North Carolina State. “Human hands can pick up fragile objects, but also very heavy objects and even tiny objects. They can do all these things with ease. We wanted to come up with a design for a gripper that could deal with all these things so it could be directly integrated with an industrial robotic arm or even an arm prosthetic.”
Become a Member: How to Join ASME
One of the most challenging aspects of coming up with a one-size-grips-all design is finding ways to manage force. For example, when a traditional two-jaw gripper goes to pick some grapes off the vine, it has difficulty controlling the force in such a way that they can remove the fruit from the plant without breaking the grape. Yin said he and his colleagues were inspired by the Japanese art of kirigami, which cuts and folds paper to form complex three-dimensional shapes. While this approach is not a new one, Yin said their grippers build off older designs, and provide greater capabilities.
“When you want to do a gentle pick up, a pinch gripper is not a good way to do that. Pinching has more contact and a greater chance of damaging the object. Instead, our design, which is made of polyethylene terephthalate (PET), encapsulates the object. It goes around the object and envelopes it horizontally before picking it up. The force is very small,” he said. “But then, if you want to pick up a heavier object, you can use vertical force to support the heavy load and the structure will support that, too.”
The unique gripper design, which weighs less than half a gram, can lift up to 6.4 kilograms, but can also provide precision and gentleness where required. Yin said they have successfully picked up a drop of water, folded cloth, turned the page of a book, and picked up microfilms thinner than a human hair. This, he stated, means this design could be integrated into a wide variety of different applications.
“Think of agriculture. Blueberries are very fragile. Most grippers cannot pick them. But our grippers can easily do that without damaging the fruit,” he said. “They could also be used in food processing. Meat or pork can be very slippery, and it is also quite heavy. But these grippers could work in meat processing, too.”
Prosthetic design
Another promising application is integrating these grippers into existing prosthetic upper extremity devices including a myoelectric prosthetic hand, which is controlled by the wearer’s own muscle activity. Yin partnered with Helen Huang, the Jackson Family Distinguished Professor in the Joint Department of Biomedical Engineering at North Carolina State and the University of North Carolina at Chapel hill to test this enhanced device.
More for You: Gripper's Soft Touch Promises Gentler Harvest Automation
They found that the grippers, as part of the myoelectric prosthetic, can easily zip up a zipper and pick up coins. This could enhance the capabilities of future prosthetic designs.
But Yin maintains that there is probably much more that this one gripper for all can do. He and his colleagues are working to see what other applications it might be suited for—and hoping industry partners will help them determine which ways this innovative design can best be used in the future. He is also looking at testing other, more sustainable materials for the grippers.
“There are different materials we can use. My students went outside, and they found a leaf. They then used a laser cutter to cut into a grip shape and stretched it. This is exciting because it’s a biodegradable material and you can imagine that you can use these natural, elastic materials for applications where you need the grippers maybe once or twice and need to throw them away,” he said.
“The gripper design is material independent; you can apply it to different materials. It’s also size independent. You can make it very tiny. You can make it very large. This means this design can be used for many different applications. We are only starting to understand all the places where this kind of gripper can be used,” he added.
Kayt Sukel is a technology writer and author in Houston, Tex.
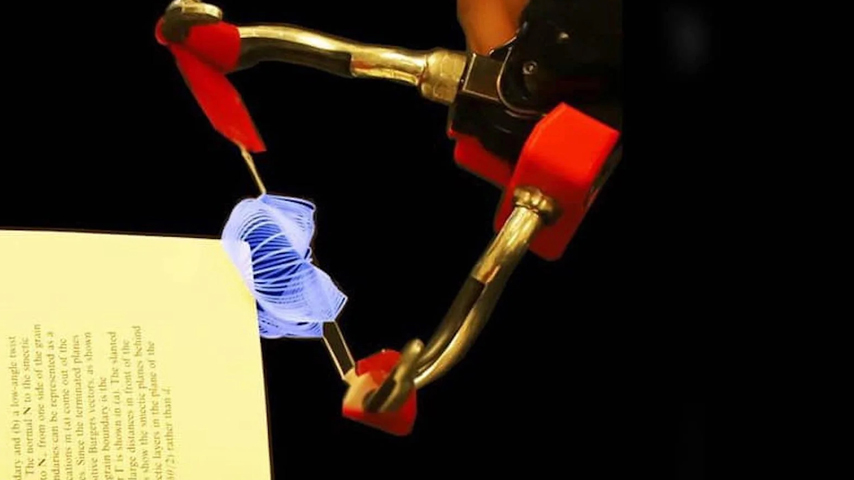
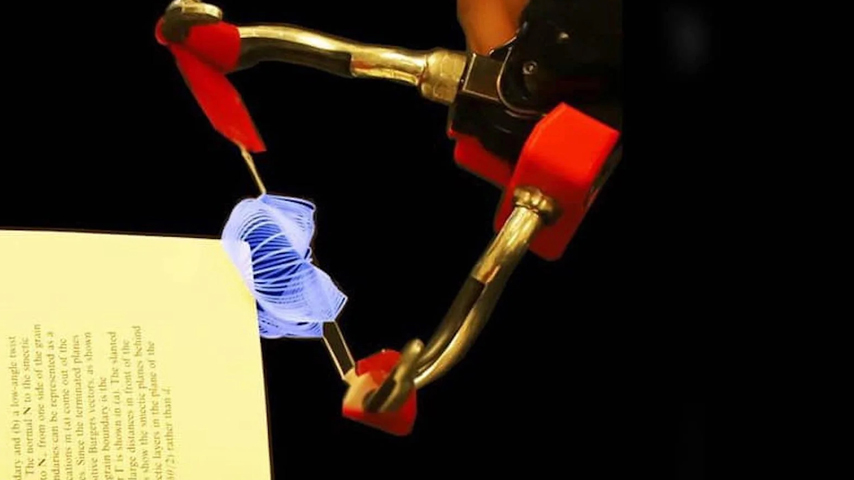