Recreating the Sun
Recreating the Sun
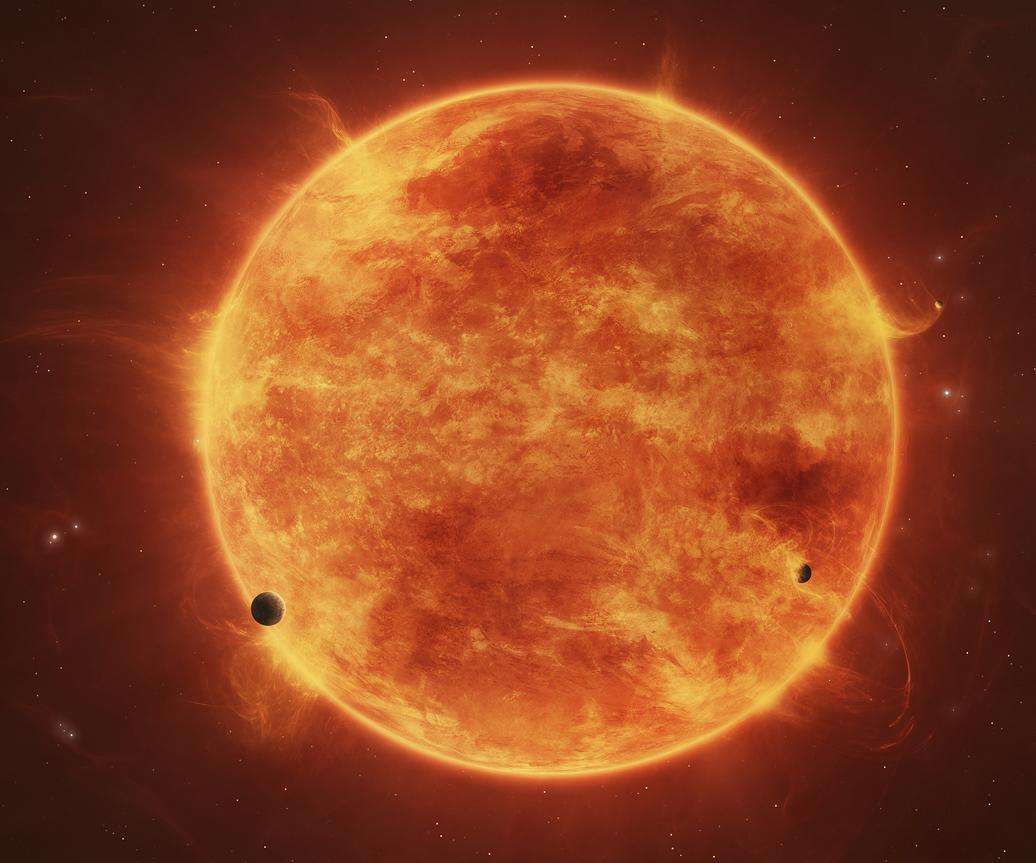
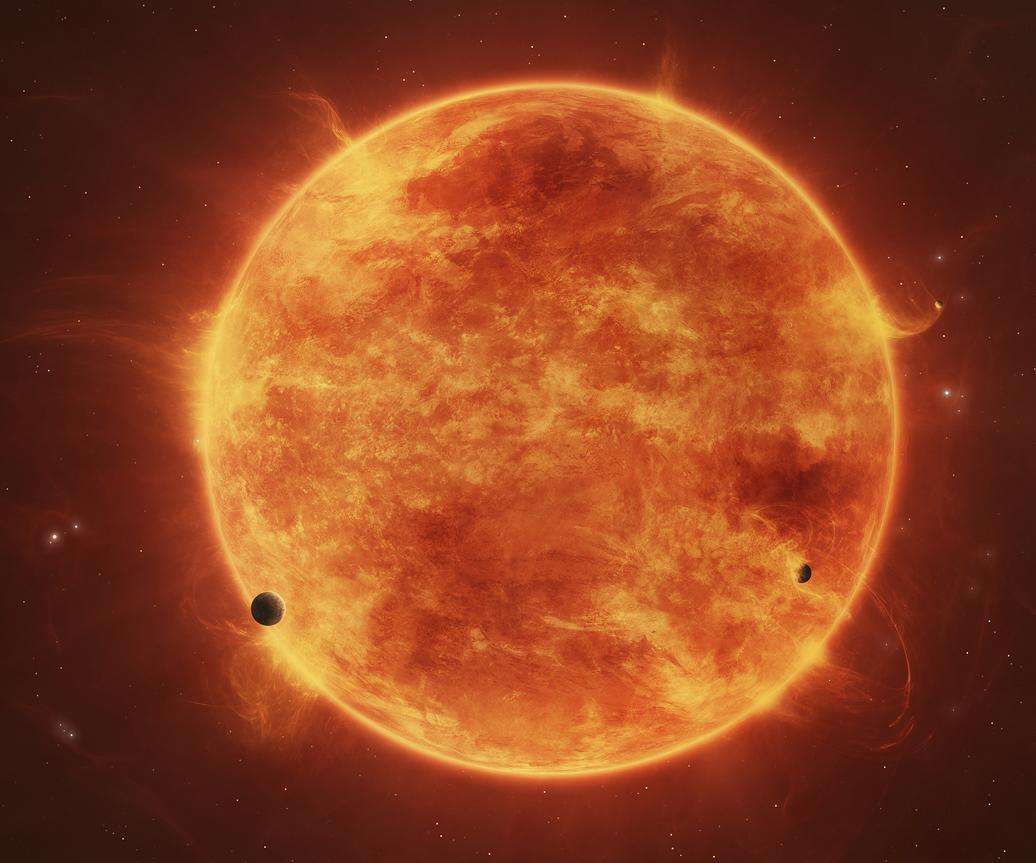
By achieving ignition, scientists are moving closer to recreating the sun's power source using laser fusion technology.,
The stage for the biggest show in nuclear fusion fits on your fingertip. It’s a 2-millimeter capsule of hydrogen isotopes the size of a peppercorn, meticulously positioned inside a 130-metri-ton welded aluminum chamber that can replicate the natural phenomenon of the sun.
It sits at the center of 192 laser beams and 40,000 optics, a collection of lasers, mirrors, waveplates, laser amplifier slabs, and polarizers. Making the world’s largest laser system work requires all 700,000 square feet of the National Ignition Facility (NIF) at the U.S. Department of Energy’s Lawrence Livermore National Laboratory (LLNL) in California.
It doesn’t take long to realize why this is colloquially referred to as the “smartest square mile on Earth.” A crew of roughly 800 employees is trying to create an artificial sun in a laboratory, and every detail of each experiment is nanomanipulated to be as precise as possible.
For decades, researchers at NIF have been trying to achieve nuclear fusion ignition—a reaction that produces more energy than it consumes by forcing atoms to combine. Scientists are excited that doing this on a large scale would bring us closer to an infinite, self-sustaining, and clean energy source that is truly carbon free.
Although fusion energy had (and still has) a number of vocal critics, in the early hours of Dec. 5, 2022, researchers at NIF made headlines around the world with their breakthrough achievement when they created the first energy gain at a factor of 1.5. The experiment yielded 3.15 megajoules (MJ), roughly the energy produced by three sticks of dynamite.
“This was incredibly exciting for us to do with the laser that we have, with bonus energy to tap, because we still, even at this point of operation, have a lot of cards that we haven't played yet,” said Bruno Van Wonterghem, a laser physicist who serves as NIF’s operations director. “We still have room to improve targets, improve target finishing, and imperfections to get more energy, power, and precision out of the laser.
Experts have compared this historic achievement to the first Wright brothers flight, which only traveled 120 feet. There’s a long way to go to achieve commercial-grade fusion energy, but the early-December ignition proved it’s possible.
A NIF experiment, or “shot,” travels 1,500 meters in only five microseconds, but it takes much longer to explain. With the click of a button in the control room, a laser pulse that’s a few billionths of a joule is carried on optical fibers to 48 pre-amplifiers of active neodymium-doped phosphate laser glass that enhances the pulse’s energy several billion times and defines its shape.
The 48 laser beams split into four beams apiece, injecting the pulse into the 192 laser amplifier beamlines that are roughly 40 x 40 square centimeters. Laser mirrors and lenses guide each beam through two large main amplifiers containing laser glass slabs. A special optical switch enables the laser light to travel back and forth four times, while special deformable mirrors, spatial filters, and other devices ensure each beam is high quality, uniform, and smooth.
From there, the laser beams enter two 10-story switchyards and head toward the target chamber. After they pass through the switchyards and into the target bay, the beams travel through the final optics assemblies just before the target chamber and convert 4 million joules of infrared energy to 2 million joules of ultraviolet energy, because shorter wavelengths are better for ignition.
That blue, ultraviolet light gets shot into the target, where the fusion occurs. NIF was created to allow temperatures and pressures that aren’t possible anywhere else on Earth. NIF’s lasers compress the fuel to 100 times the density of lead, creating temperatures more than 100,000,000° C , or more than seven times hotter than the core of the sun. For a mere fraction of a billionth of a second, NIF was the hottest place in our solar system.
NIF takes about 400 laser shots each year. Some of these are discovery science experiments conducted by universities and other partners; most are in-house research experiments for the Department of Energy Defense Program. NIF usually takes one high-powered shot twice each month to try to achieve ignition. Laser glass plays a key role each time an experiment is performed. Improvements to the glass or other optics allow NIF to increase shot rate and increase a beam’s energy and power.
“The optics effort is like peeling a growing onion,” said Tayyab Suratwala, program director of optics and materials science & technology at NIF. “When you make an improvement to an optical component, our customers take advantage of it. They turn up the knob and a new damage phenomenon comes up and we have to solve that problem. Hence, the efforts to improve optics performance is never ending.”
Laser glass’ leading role
Twelve years before NIF broke ground in 1997, LLNL was already working with manufacturers like SCHOTT to develop laser glass for fusion experiments. Based on experiments at LLNL’s Nova Laser Fusion Facility, NIF’s predecessor, scientists knew they needed a new glass composition.
Glass is an ideal host material for rare-earth ions that power lasers. Homogeneity is a key marker of quality for laser glass and SCHOTT’s innovations have led to developments like platinum particle reduction, which was utilized to deliver glass to NIF. SCHOTT is engaged in workshops with potential customers interested in obtaining some of the glass provided to the largest laser systems like NIF, Novette, NOVA, Beamlet, and Laser MegaJoule.
SCHOTT worked with NIF to better understand how changes in composition can affect mechanical properties, laser properties, and manufacturability. The company also accelerated production. Its United States manufacturing base wasn’t large enough at the time to build NIF’s glass on schedule, so proficiency was required.
At its Duryea, Pa., facility, SCHOTT optics experts pioneered a continuous melting process to create larger slabs of glass that could be cut into smaller pieces. This was exponentially more efficient than other processes that only yielded one substrate per day. To achieve this, the glass scientists needed not just hardware expertise, but material expertise to achieve the properties NIF required.
“Getting the right glass for this particular application took significant development,” said Bill James, head of research and development at SCHOTT North America. “Joe Hayden on our side and Jack Campbell on the Livermore side were instrumental in really understanding the chemistry, the optical physics, and what was required to get what they needed out of the discoveries to really produce platinum-particle-free laser glass.”
All the trials were documented in a large book published by LLNL, encapsulating decades of development and partnership that turned into the final product. From 2000 to 2004, SCHOTT delivered 4,000 pieces of LG-770, the phosphate glass that is still used at NIF today. Its facility in Jena, Germany, creates the steady flow of BOROFLOAT® glass that NIF uses each year as debris shields, as well as many of the substrates used in the mirrors.
Protective shields for laser optics
BOROFLOAT® is the world’s first floated borosilicate glass. Introduced in 1993, it has outstanding thermal resistance, exceptional transparency, high chemical durability, and excellent mechanical strength. “Its robust properties have made BOROFLOAT® glass the ideal material for extreme environments from medical applications to aerospace, automotive, and now laser fusion,” said Tina Gallo, manager of applications & logistic services at SCHOTT North America.
Fusion energy and the future Interest in shifting toward clean, renewable energy has picked up over the years, and a White House initiative in 2022 doubled down on that vision, laying out a “bold decadal strategy to accelerate the realization of commercial fusion.”
“There's a marathon to go,” said Gernot Weber, product manager for Laser Glass at SCHOTT. “It won't be a 100-meter race; it will be much longer than a 100-meter race for private companies, for the government, as well as for people who are providing materials and technology for fusion energy.”
The efficiency of NIF is less than 1 percent, so it’s not viable to create power on a large scale as is. Bruno estimates NIF would need high-efficiency lasers that could run at 10 times per second, and a reaction chamber that could harness the energy and turn the energy of neutrons into steam, which would then drive turbines and be converted into electricity. A pilot plant to demonstrate all this is a long-term goal of the national labs working with private industry and the academic world. All of that would require near-perfect optics that are resistant to damage, able to withstand billions of shots, and capable of optimizing the gain of the laser.
Another area of focus for efficiency is the targets. They are time consuming and costly to produce, so they need an innovative design that lends itself to mass production. A mechanism like a pellet gun would be required to go from one shot per day to 10 shots per second.
NIF’s ignition breakthrough is expected to further expand SCHOTT’s laser glass business, as the company is the only manufacturer of large format laser glass in the Western Hemisphere. Laser glass will play a leading role in the pursuit of the power plant of the future, and put meaningful action behind the company’s sustainability goals.
Lea Kaiser writes about glass and technology for Schott.
It sits at the center of 192 laser beams and 40,000 optics, a collection of lasers, mirrors, waveplates, laser amplifier slabs, and polarizers. Making the world’s largest laser system work requires all 700,000 square feet of the National Ignition Facility (NIF) at the U.S. Department of Energy’s Lawrence Livermore National Laboratory (LLNL) in California.
It doesn’t take long to realize why this is colloquially referred to as the “smartest square mile on Earth.” A crew of roughly 800 employees is trying to create an artificial sun in a laboratory, and every detail of each experiment is nanomanipulated to be as precise as possible.
For decades, researchers at NIF have been trying to achieve nuclear fusion ignition—a reaction that produces more energy than it consumes by forcing atoms to combine. Scientists are excited that doing this on a large scale would bring us closer to an infinite, self-sustaining, and clean energy source that is truly carbon free.
Although fusion energy had (and still has) a number of vocal critics, in the early hours of Dec. 5, 2022, researchers at NIF made headlines around the world with their breakthrough achievement when they created the first energy gain at a factor of 1.5. The experiment yielded 3.15 megajoules (MJ), roughly the energy produced by three sticks of dynamite.
“This was incredibly exciting for us to do with the laser that we have, with bonus energy to tap, because we still, even at this point of operation, have a lot of cards that we haven't played yet,” said Bruno Van Wonterghem, a laser physicist who serves as NIF’s operations director. “We still have room to improve targets, improve target finishing, and imperfections to get more energy, power, and precision out of the laser.
Experts have compared this historic achievement to the first Wright brothers flight, which only traveled 120 feet. There’s a long way to go to achieve commercial-grade fusion energy, but the early-December ignition proved it’s possible.
What’s in a laser shot?
A NIF experiment, or “shot,” travels 1,500 meters in only five microseconds, but it takes much longer to explain. With the click of a button in the control room, a laser pulse that’s a few billionths of a joule is carried on optical fibers to 48 pre-amplifiers of active neodymium-doped phosphate laser glass that enhances the pulse’s energy several billion times and defines its shape.
The 48 laser beams split into four beams apiece, injecting the pulse into the 192 laser amplifier beamlines that are roughly 40 x 40 square centimeters. Laser mirrors and lenses guide each beam through two large main amplifiers containing laser glass slabs. A special optical switch enables the laser light to travel back and forth four times, while special deformable mirrors, spatial filters, and other devices ensure each beam is high quality, uniform, and smooth.
From there, the laser beams enter two 10-story switchyards and head toward the target chamber. After they pass through the switchyards and into the target bay, the beams travel through the final optics assemblies just before the target chamber and convert 4 million joules of infrared energy to 2 million joules of ultraviolet energy, because shorter wavelengths are better for ignition.
The hottest place in our solar system
That blue, ultraviolet light gets shot into the target, where the fusion occurs. NIF was created to allow temperatures and pressures that aren’t possible anywhere else on Earth. NIF’s lasers compress the fuel to 100 times the density of lead, creating temperatures more than 100,000,000° C , or more than seven times hotter than the core of the sun. For a mere fraction of a billionth of a second, NIF was the hottest place in our solar system.
NIF takes about 400 laser shots each year. Some of these are discovery science experiments conducted by universities and other partners; most are in-house research experiments for the Department of Energy Defense Program. NIF usually takes one high-powered shot twice each month to try to achieve ignition. Laser glass plays a key role each time an experiment is performed. Improvements to the glass or other optics allow NIF to increase shot rate and increase a beam’s energy and power.
“The optics effort is like peeling a growing onion,” said Tayyab Suratwala, program director of optics and materials science & technology at NIF. “When you make an improvement to an optical component, our customers take advantage of it. They turn up the knob and a new damage phenomenon comes up and we have to solve that problem. Hence, the efforts to improve optics performance is never ending.”
Laser glass’ leading role
Twelve years before NIF broke ground in 1997, LLNL was already working with manufacturers like SCHOTT to develop laser glass for fusion experiments. Based on experiments at LLNL’s Nova Laser Fusion Facility, NIF’s predecessor, scientists knew they needed a new glass composition.
Glass is an ideal host material for rare-earth ions that power lasers. Homogeneity is a key marker of quality for laser glass and SCHOTT’s innovations have led to developments like platinum particle reduction, which was utilized to deliver glass to NIF. SCHOTT is engaged in workshops with potential customers interested in obtaining some of the glass provided to the largest laser systems like NIF, Novette, NOVA, Beamlet, and Laser MegaJoule.
SCHOTT worked with NIF to better understand how changes in composition can affect mechanical properties, laser properties, and manufacturability. The company also accelerated production. Its United States manufacturing base wasn’t large enough at the time to build NIF’s glass on schedule, so proficiency was required.
At its Duryea, Pa., facility, SCHOTT optics experts pioneered a continuous melting process to create larger slabs of glass that could be cut into smaller pieces. This was exponentially more efficient than other processes that only yielded one substrate per day. To achieve this, the glass scientists needed not just hardware expertise, but material expertise to achieve the properties NIF required.
“Getting the right glass for this particular application took significant development,” said Bill James, head of research and development at SCHOTT North America. “Joe Hayden on our side and Jack Campbell on the Livermore side were instrumental in really understanding the chemistry, the optical physics, and what was required to get what they needed out of the discoveries to really produce platinum-particle-free laser glass.”
All the trials were documented in a large book published by LLNL, encapsulating decades of development and partnership that turned into the final product. From 2000 to 2004, SCHOTT delivered 4,000 pieces of LG-770, the phosphate glass that is still used at NIF today. Its facility in Jena, Germany, creates the steady flow of BOROFLOAT® glass that NIF uses each year as debris shields, as well as many of the substrates used in the mirrors.
Protective shields for laser optics
BOROFLOAT® is the world’s first floated borosilicate glass. Introduced in 1993, it has outstanding thermal resistance, exceptional transparency, high chemical durability, and excellent mechanical strength. “Its robust properties have made BOROFLOAT® glass the ideal material for extreme environments from medical applications to aerospace, automotive, and now laser fusion,” said Tina Gallo, manager of applications & logistic services at SCHOTT North America.
Fusion energy and the future Interest in shifting toward clean, renewable energy has picked up over the years, and a White House initiative in 2022 doubled down on that vision, laying out a “bold decadal strategy to accelerate the realization of commercial fusion.”
“There's a marathon to go,” said Gernot Weber, product manager for Laser Glass at SCHOTT. “It won't be a 100-meter race; it will be much longer than a 100-meter race for private companies, for the government, as well as for people who are providing materials and technology for fusion energy.”
The efficiency of NIF is less than 1 percent, so it’s not viable to create power on a large scale as is. Bruno estimates NIF would need high-efficiency lasers that could run at 10 times per second, and a reaction chamber that could harness the energy and turn the energy of neutrons into steam, which would then drive turbines and be converted into electricity. A pilot plant to demonstrate all this is a long-term goal of the national labs working with private industry and the academic world. All of that would require near-perfect optics that are resistant to damage, able to withstand billions of shots, and capable of optimizing the gain of the laser.
Another area of focus for efficiency is the targets. They are time consuming and costly to produce, so they need an innovative design that lends itself to mass production. A mechanism like a pellet gun would be required to go from one shot per day to 10 shots per second.
NIF’s ignition breakthrough is expected to further expand SCHOTT’s laser glass business, as the company is the only manufacturer of large format laser glass in the Western Hemisphere. Laser glass will play a leading role in the pursuit of the power plant of the future, and put meaningful action behind the company’s sustainability goals.
Lea Kaiser writes about glass and technology for Schott.
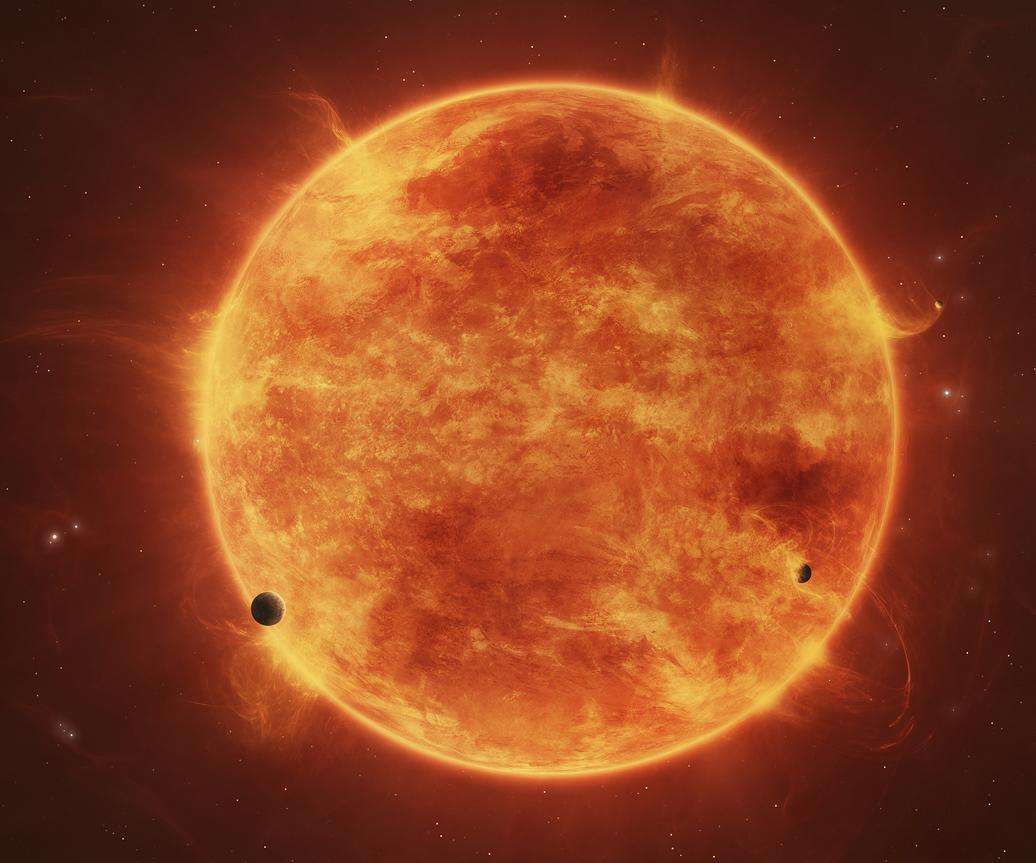
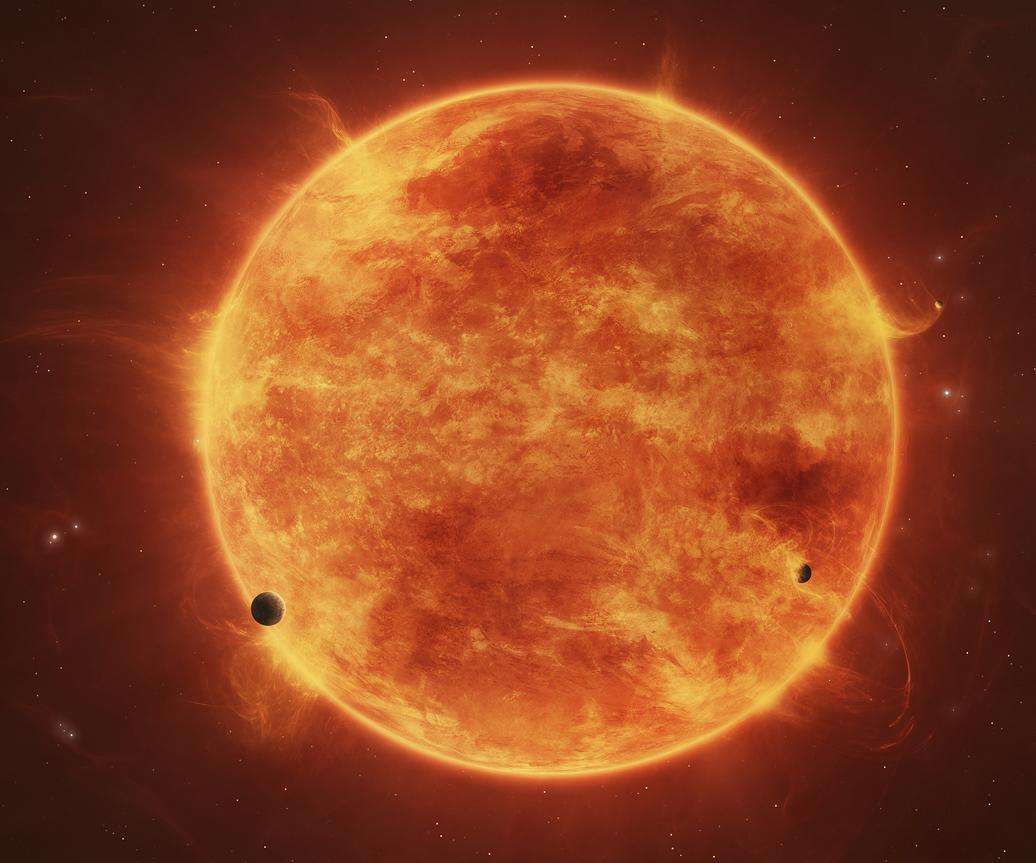