Shock-Absorbing Metamaterial Holds Promise for Impact Protection
Shock-Absorbing Metamaterial Holds Promise for Impact Protection
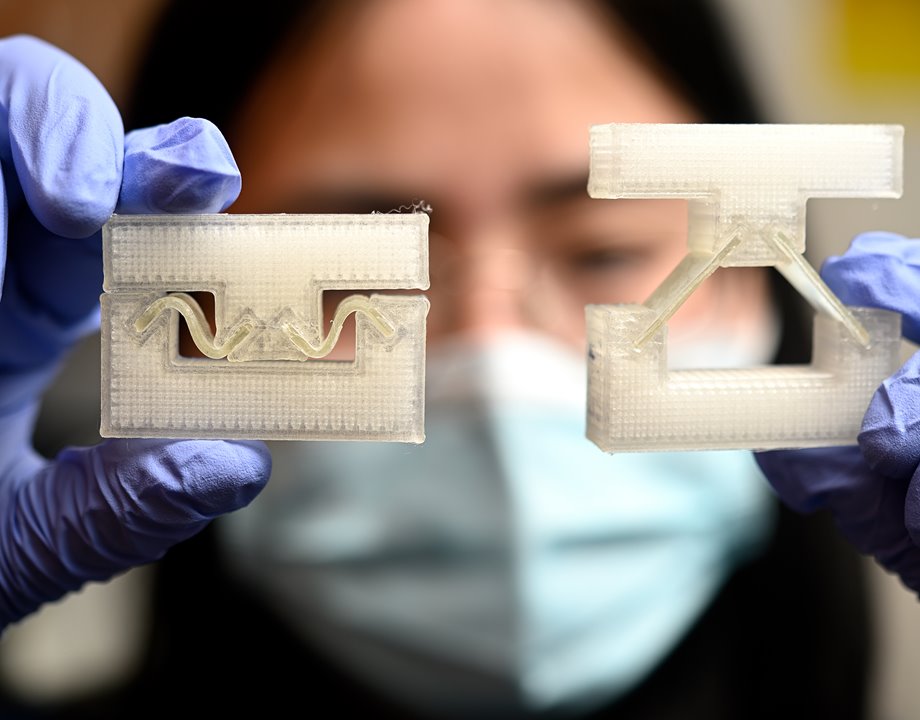
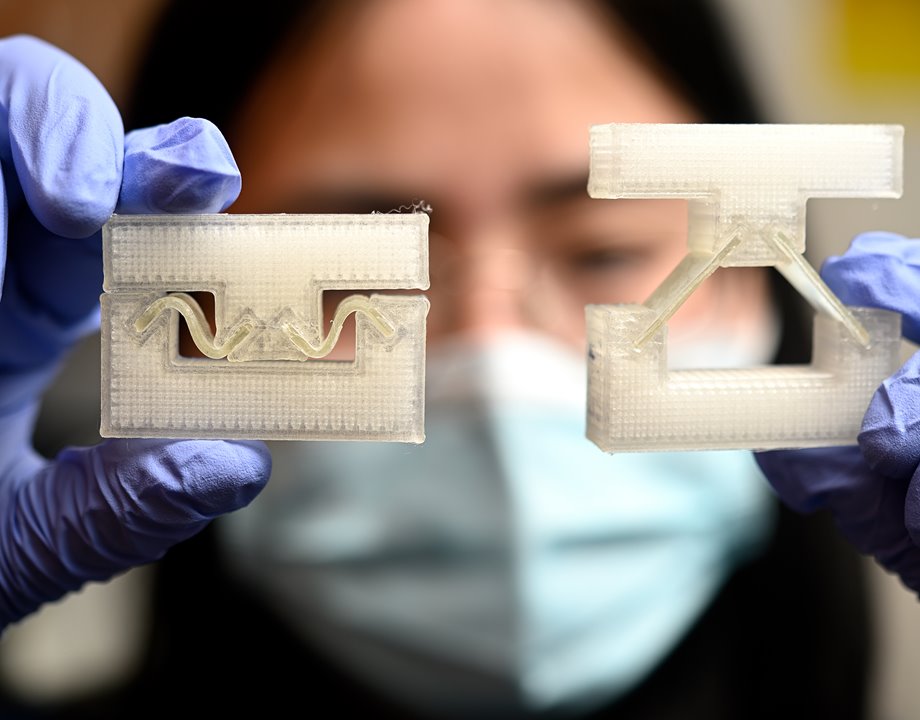
Metamaterial made from liquid crystal elastomers turns into hard plastic on impact. Photo: Will Kirk, Johns Hopkins University photographer
Metals and plastics are typically the materials used to absorb energy in high-impact situations—for example, car bumpers or helmets. However, these materials typically do not perform well at higher speeds, are heavy, and are not reusable.
To improve this situation, a team of Johns Hopkins University researchers led by Sung Hoon Kang, assistant professor in the department of mechanical engineering and Hopkins Extreme Materials Institute, investigated materials that could deliver greater energy absorption at higher speeds of impact, while being lighter weight and also reusable. They focused on liquid crystal elastomers (LCEs), which have ideal material characteristics for this application.
LCEs, while softer than typical elastomers at static conditions, transform into hard, shock-absorbing plastics at higher speeds of impact. The foam-based LCE material the team developed is lighter than metal, displays better energy absorption at higher impact speeds, and can be reused. Commercial applications abound, such as helmets, body armor, and automobile and aerospace parts.
To date, high-energy-absorbing LCEs have been used mainly in actuators and robotics. Kang harnessed the energy dissipation capabilities of LCEs by designing foam-like, multilayered structures that amplify the energy dissipation density upon impact.
More for You: Metamaterials Expand Possibilities in Biomedical Engineering
The architected materials consist of repeating unit cells of bistable tilted LCE beams sandwiched between stiff supports, as described in a paper Kang coauthored and published in Advanced Materials. The viscoelastic behavior of the LCE causes the energy absorption to increase with strain rate, according to a power-law relationship, which can be modulated by changing the degree of mesogen alignment and the loading direction relative to the director.
“Introducing the foam-like geometry and stacking them allowed us to have a synergy between material and geometry, thus achieving a much higher energy absorption density compared with that of a bulk material,” Kang said. “We were also not expecting the power-law relation between energy absorption density and strain rate so that the energy absorption density showed orders of magnitude increase at an impact regime.”
In addition, the vertical stacking of LCE units caused nonuniform buckling due to viscoelasticity of LCE, which produced additional viscous dissipation and further increased the energy absorption density. This synergistic interaction between viscoelastic dissipation and snap-through buckling also caused the energy absorption density to increase with the number of layers.
“Greater enhancement of the energy absorption density was realized by varying the thicknesses of the LCE beams from top to bottom to ensure sequential buckling,” Kang said. “The sequence of cell collapse can be controlled by grading the beam thickness to further promote viscous dissipation and enhance the energy absorption density.”
Take the Quiz: What in the World are Metamaterials?
The enhancement of the energy absorption density caused by the vertical stacking of foam-like geometries “suggests that if we scale down the foam-like geometry, we can have a large increase in energy absorption using the same amount of a material,” he said.
Experiments showed the material withstood strikes from objects weighing about 4 to 15 pounds, coming at speeds of up to about 22 miles per hour. The tests were limited to 22 miles per hour due to limits of the testing machines, but the team is confident the padding could safely absorb even greater impacts.
“Understanding the interplay between energy absorption mechanism through material and geometry and finding ways to have a synergy between them was the biggest challenge,” Kang said. “It is exciting that our architected LCEs showed an energy absorption density comparable to that of a metal in an impact regime.”
Reader’s Choice: An Uncrushable Metamaterial
For this experiment, Kang used LCE as a beam material for a simple 1D metastructure. Greater enhancement of energy absorption is expected through systematic structural designs in the future.
“We are optimistic our work will contribute not only to the fundamental understanding of the nonlinear energy absorption mechanisms of architected LCE structures, but also applications where lightweight and extreme energy absorption are desirable,” Kang said.
Kang’s team is currently assessing other mechanisms for improving the material’s strength and energy absorption capability. The researchers have already received several inquiries from helmet companies and are exploring collaboration with industries to design, fabricate, and test next-generation lightweight energy-absorbing materials for various applications, including automotive and aerospace parts and personal protections.
Mark Crawford is a science and technology writer in Corrales, N.M.
To improve this situation, a team of Johns Hopkins University researchers led by Sung Hoon Kang, assistant professor in the department of mechanical engineering and Hopkins Extreme Materials Institute, investigated materials that could deliver greater energy absorption at higher speeds of impact, while being lighter weight and also reusable. They focused on liquid crystal elastomers (LCEs), which have ideal material characteristics for this application.
LCEs, while softer than typical elastomers at static conditions, transform into hard, shock-absorbing plastics at higher speeds of impact. The foam-based LCE material the team developed is lighter than metal, displays better energy absorption at higher impact speeds, and can be reused. Commercial applications abound, such as helmets, body armor, and automobile and aerospace parts.
To date, high-energy-absorbing LCEs have been used mainly in actuators and robotics. Kang harnessed the energy dissipation capabilities of LCEs by designing foam-like, multilayered structures that amplify the energy dissipation density upon impact.
More for You: Metamaterials Expand Possibilities in Biomedical Engineering
The architected materials consist of repeating unit cells of bistable tilted LCE beams sandwiched between stiff supports, as described in a paper Kang coauthored and published in Advanced Materials. The viscoelastic behavior of the LCE causes the energy absorption to increase with strain rate, according to a power-law relationship, which can be modulated by changing the degree of mesogen alignment and the loading direction relative to the director.
“Introducing the foam-like geometry and stacking them allowed us to have a synergy between material and geometry, thus achieving a much higher energy absorption density compared with that of a bulk material,” Kang said. “We were also not expecting the power-law relation between energy absorption density and strain rate so that the energy absorption density showed orders of magnitude increase at an impact regime.”
In addition, the vertical stacking of LCE units caused nonuniform buckling due to viscoelasticity of LCE, which produced additional viscous dissipation and further increased the energy absorption density. This synergistic interaction between viscoelastic dissipation and snap-through buckling also caused the energy absorption density to increase with the number of layers.
“Greater enhancement of the energy absorption density was realized by varying the thicknesses of the LCE beams from top to bottom to ensure sequential buckling,” Kang said. “The sequence of cell collapse can be controlled by grading the beam thickness to further promote viscous dissipation and enhance the energy absorption density.”
Take the Quiz: What in the World are Metamaterials?
The enhancement of the energy absorption density caused by the vertical stacking of foam-like geometries “suggests that if we scale down the foam-like geometry, we can have a large increase in energy absorption using the same amount of a material,” he said.
Experiments showed the material withstood strikes from objects weighing about 4 to 15 pounds, coming at speeds of up to about 22 miles per hour. The tests were limited to 22 miles per hour due to limits of the testing machines, but the team is confident the padding could safely absorb even greater impacts.
“Understanding the interplay between energy absorption mechanism through material and geometry and finding ways to have a synergy between them was the biggest challenge,” Kang said. “It is exciting that our architected LCEs showed an energy absorption density comparable to that of a metal in an impact regime.”
Reader’s Choice: An Uncrushable Metamaterial
For this experiment, Kang used LCE as a beam material for a simple 1D metastructure. Greater enhancement of energy absorption is expected through systematic structural designs in the future.
“We are optimistic our work will contribute not only to the fundamental understanding of the nonlinear energy absorption mechanisms of architected LCE structures, but also applications where lightweight and extreme energy absorption are desirable,” Kang said.
Kang’s team is currently assessing other mechanisms for improving the material’s strength and energy absorption capability. The researchers have already received several inquiries from helmet companies and are exploring collaboration with industries to design, fabricate, and test next-generation lightweight energy-absorbing materials for various applications, including automotive and aerospace parts and personal protections.
Mark Crawford is a science and technology writer in Corrales, N.M.
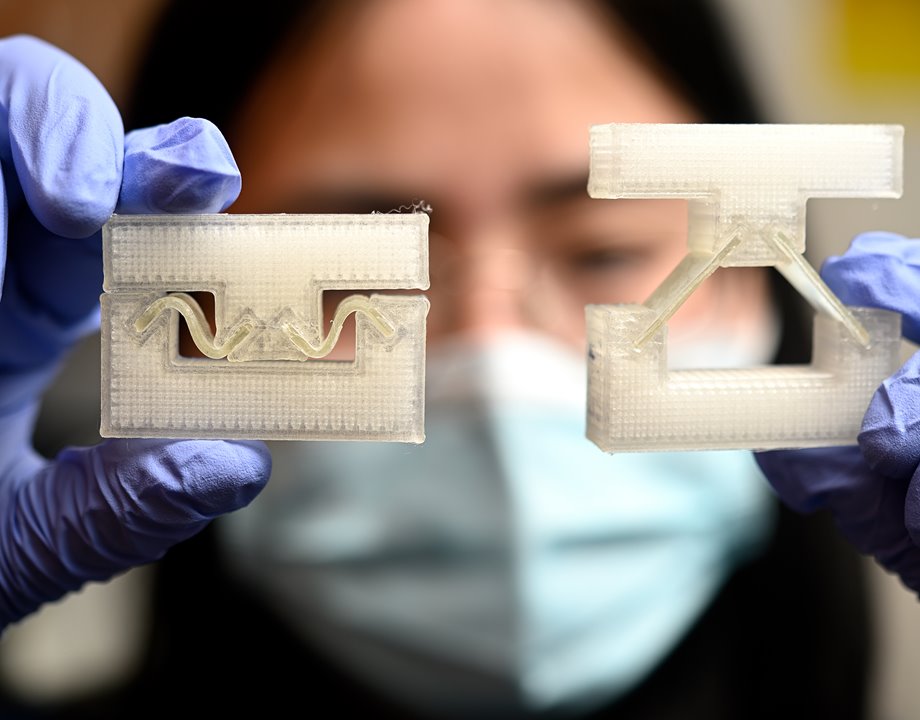
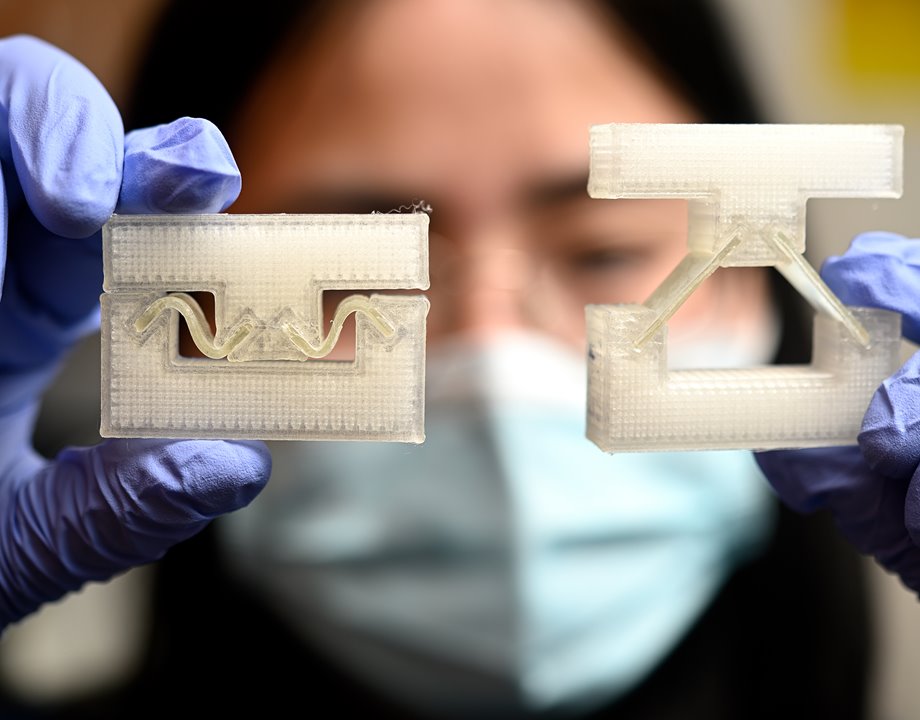