Springfield Armory Showcases the Machines that Shaped a Nation
Springfield Armory Showcases the Machines that Shaped a Nation
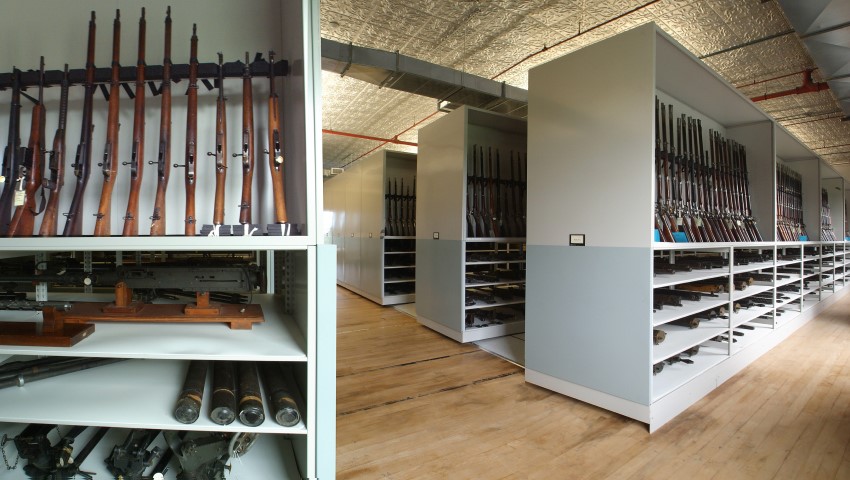
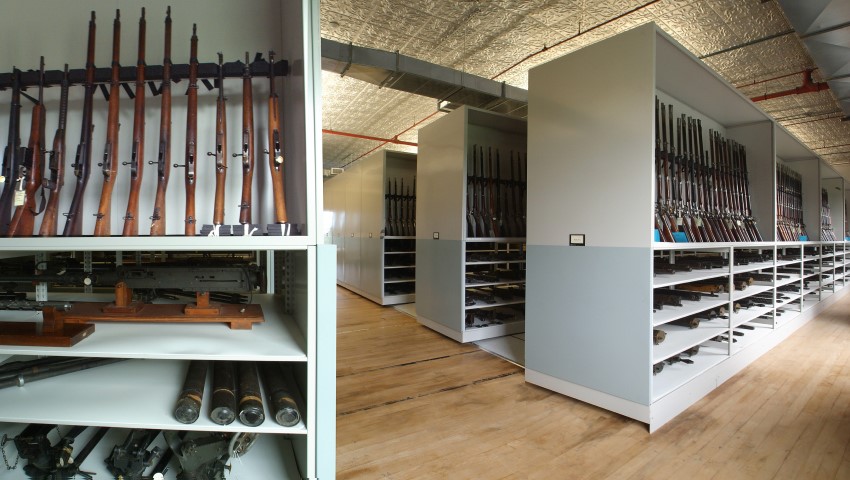
ASME Landmark Springfield Armory, now a museum, offers visitors a chance to see historical arms and the amazing machines that made them.
Before the engineer Thomas Blanchard put his invention to work, craftsmen would hand carve rifle butt stock. With the Blanchard Lathe, however, workers could duplicate irregular-shaped parts a dozen at a time. Today, you can see the original lathe at the Springfield Armory Museum in Massachusetts.
Like other makers of precision interchangeable parts, the Springfield Armory was a machining center. But unlike other factories, this site dedicated its machines and workers to the design and mass production of firearms.
Read ASME's Landmark Description: Springfield Armory
Today, visitors are able to see one of the largest collections of small firearms—about 20,000—and learn how Americans made these weapons for 174 years for the U.S. military. Visitors come from all over the United States, explained Susan Ashman, park ranger and historic weapons supervisor at the Springfield Armory. She said visitors from the surrounding area join those from out-of-state who are “firearm and military enthusiasts. Others like history and engineering. And some, are visiting all the national parks.”
Those who take the time can learn how a thief made off with a rare 1842 pattern pistol in 1971 and returned last year due to the diligence of a police history buff and the history of lesser-known finishing processes, milling operations, materials treatment, and research and development practices that it established during its many years of operation. The armory became a National Historic Landmark in 1963 and a National Historic Mechanical Engineering Landmark in 1980.
Because of George Washington’s concern over the need to standardize rifles for the Continental Army, the armory began construction in Springfield, Massachusetts. When completed in 1794, the Springfield Armory became the first national armory in the United States.
In 1861, the armory added steam engines and new machinery to improve production. That same year, Harper’s Monthly featured the armory’s manufacturing processes. It describes eighteen tilt-hammers driven by immense water wheels under the building for welding the gun barrels. The story covered the operation of forges and tilt-hammers and the use of reflecting mirrors to help workers check the straightness of gun barrels.
By 1864, the output of the new machinery was 10 times the amount the armory produced at the beginning of the Civil War. Between 1862 and 1864 alone, production doubled, and by 1865, the armory employed 3,000 workers.
Become a Member: How to Join ASME
In 1891, the armory created the forerunner of a modern research and development division—the experimental department of the armory, where engineers developed sophisticated weapons. One such gun was the "03 Springfield.” The armory produced more than 250,000 units during World War I.
Today, the Organ of Muskets creates the most enthusiasm, Ashman explained. These are the last two original storage racks that currently hold 648 longarms. Park Ranger Scott Gausen agreed. “It is a dramatic display that a lot of people gravitate to. It is the last (that we know of) remaining storage rack from the pre-Civil War storage methods at the Armory,” he said.
The blank firing demonstrations that the armory puts on are also crowd-pleasers, Ashman said. Happening outside starting in the spring and straight through until the fall the exhibition takes place on the national historic site that now encompasses 20 acres of the original 55-acre historic “Hillshop” location.
A most significant contribution to manufacturing was the development of a precise set of gauges by Cyrus Buckland, adopted by the Bureau of Standards. Probably the most noted employee of the armory was John Garand. In 1936, Garand submitted a design to the government for the first semi-automatic rifle, the M-1. His design came after approximately 20 years of successful research, experimentation, and testing. Because of the M-1’s success, the armory installed the most modern mass production. Other ordnance manufacturers copied these processes and uses of broaches and on-machine gauges because they worked so well.
The M-1 “display is something that people shouldn’t miss when they visit,” Gausen said. “We also have one of the nine pistols Colt made for the trials that decided which pistol would be adopted by the Amy.”
In addition to its weapons development, the Armory contributed to industry as a whole in the following ways: continuous automatic parkerizing process, horizontal and vertical slab broaching, barrel rifling broaching, continuous heat treatment process for rifle barrels (including special equipment design), chrome plating process for rifle barrel bores and chambers, ultra-high speed machining of wood using carbine tools, special heat treatment wood oil process for wood preservation, dichromate process for stainless steel, application of refractory or exotic metals, and applicability of numerical controlled machine tools to small lot and pilot production.
Ashman explained that a no-miss attraction for anyone to check out is the display that highlights the women who worked at the armory. The women “were called WOWs: Women Ordnance Workers,” she explained. “Rosie had dots on her bandanas. WOWs had bombs.”
Cathy Cecere is membership content program manager.
Like other makers of precision interchangeable parts, the Springfield Armory was a machining center. But unlike other factories, this site dedicated its machines and workers to the design and mass production of firearms.
Read ASME's Landmark Description: Springfield Armory
Today, visitors are able to see one of the largest collections of small firearms—about 20,000—and learn how Americans made these weapons for 174 years for the U.S. military. Visitors come from all over the United States, explained Susan Ashman, park ranger and historic weapons supervisor at the Springfield Armory. She said visitors from the surrounding area join those from out-of-state who are “firearm and military enthusiasts. Others like history and engineering. And some, are visiting all the national parks.”
Those who take the time can learn how a thief made off with a rare 1842 pattern pistol in 1971 and returned last year due to the diligence of a police history buff and the history of lesser-known finishing processes, milling operations, materials treatment, and research and development practices that it established during its many years of operation. The armory became a National Historic Landmark in 1963 and a National Historic Mechanical Engineering Landmark in 1980.
Wartime needs
Because of George Washington’s concern over the need to standardize rifles for the Continental Army, the armory began construction in Springfield, Massachusetts. When completed in 1794, the Springfield Armory became the first national armory in the United States.
In 1861, the armory added steam engines and new machinery to improve production. That same year, Harper’s Monthly featured the armory’s manufacturing processes. It describes eighteen tilt-hammers driven by immense water wheels under the building for welding the gun barrels. The story covered the operation of forges and tilt-hammers and the use of reflecting mirrors to help workers check the straightness of gun barrels.
By 1864, the output of the new machinery was 10 times the amount the armory produced at the beginning of the Civil War. Between 1862 and 1864 alone, production doubled, and by 1865, the armory employed 3,000 workers.
Become a Member: How to Join ASME
In 1891, the armory created the forerunner of a modern research and development division—the experimental department of the armory, where engineers developed sophisticated weapons. One such gun was the "03 Springfield.” The armory produced more than 250,000 units during World War I.
Armory made
Today, the Organ of Muskets creates the most enthusiasm, Ashman explained. These are the last two original storage racks that currently hold 648 longarms. Park Ranger Scott Gausen agreed. “It is a dramatic display that a lot of people gravitate to. It is the last (that we know of) remaining storage rack from the pre-Civil War storage methods at the Armory,” he said.
The blank firing demonstrations that the armory puts on are also crowd-pleasers, Ashman said. Happening outside starting in the spring and straight through until the fall the exhibition takes place on the national historic site that now encompasses 20 acres of the original 55-acre historic “Hillshop” location.
A most significant contribution to manufacturing was the development of a precise set of gauges by Cyrus Buckland, adopted by the Bureau of Standards. Probably the most noted employee of the armory was John Garand. In 1936, Garand submitted a design to the government for the first semi-automatic rifle, the M-1. His design came after approximately 20 years of successful research, experimentation, and testing. Because of the M-1’s success, the armory installed the most modern mass production. Other ordnance manufacturers copied these processes and uses of broaches and on-machine gauges because they worked so well.
The M-1 “display is something that people shouldn’t miss when they visit,” Gausen said. “We also have one of the nine pistols Colt made for the trials that decided which pistol would be adopted by the Amy.”
In addition to its weapons development, the Armory contributed to industry as a whole in the following ways: continuous automatic parkerizing process, horizontal and vertical slab broaching, barrel rifling broaching, continuous heat treatment process for rifle barrels (including special equipment design), chrome plating process for rifle barrel bores and chambers, ultra-high speed machining of wood using carbine tools, special heat treatment wood oil process for wood preservation, dichromate process for stainless steel, application of refractory or exotic metals, and applicability of numerical controlled machine tools to small lot and pilot production.
Ashman explained that a no-miss attraction for anyone to check out is the display that highlights the women who worked at the armory. The women “were called WOWs: Women Ordnance Workers,” she explained. “Rosie had dots on her bandanas. WOWs had bombs.”
Cathy Cecere is membership content program manager.