Startup Suns
Startup Suns
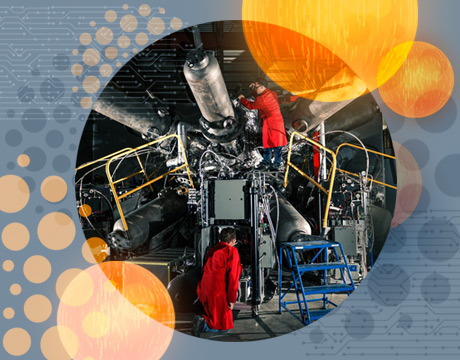
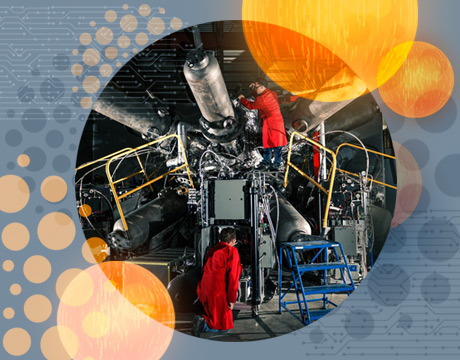
There is scarcely a more futuristic sounding technology than nuclear fusion. It is the power source in the heart of every star, the process that created every atom of oxygen, carbon, and iron in the universe, and the far-off hope of clean and bountiful energy.
In Vancouver, B.C., a team of engineers and technicians is developing a machine that will demonstrate a path to making practical, affordable fusion power. Talk to Mike Donaldson, vice president of engineering at General Fusion, the startup that’s building the machine, and he will go on excitedly about the world’s biggest plasma injector his team has built and the smoke ring-like vortices that will hold their shape due to magnetic fields the rings themselves produce.
But there are also hammers.
Not exactly hammers, but pistons that mechanically smash the sphere of molten lead that encases the plasma. The hollow space in the center of the sphere crunches down on the plasma, raising its density to the point where the ions of heavy hydrogen merge together to make helium and release energy.
If all goes well, the pistons will compress and recoil once every second for months on end, unleashing around 80 kWh of thermal energy with every stroke.
“We’ve already built the pistons at scale and demonstrated that they will have the repeatability required to do this compression,” Donaldson said.
It sounds outlandish, squashing plasmas with hammers to make pollution-free energy. But no more outlandish than the contention that General Fusion and a number of other startups have made—and made convincingly enough to attract millions of dollars from such billionaire tech investors as Jeff Bezos and the late Paul Allen—that a demonstration commercial fusion reactor will be ready by the end of the next decade. And that it will be built not by an international Big Science research project but by a scrappy startup.
Commonwealth Fusion, launched in March 2018 as a spin-off of MIT’s Plasma Science and Fusion Center. Others have been operating under the radar for nearly two decades. Befitting the merging of plasma physics and startup culture, each company has a bit of secret sauce that they hope will make the difference between success and failure.
Blackboard Panacea
With wind and solar power growing at incredibly fast rates—and with their prices now rivaling some of the cheapest power on the grid—it’s easy to imagine that no new sources of power are necessary. Why even bother with fusion?
“When you take any technology and scale it up by many orders of magnitude, there are issues that arise with a massive deployment that don’t necessarily arise at a smaller scale,” said Stewart Prager, the former head of the Princeton Plasma Physics Laboratory, a fusion research facility in New Jersey. “The problem of clean energy is so significant that it would be foolhardy not to pursue all attractive approaches.”
The nuclear power that has been deployed up to now is based on fission, the process in which heavy atoms capture stray neutrons, become unstable, and split into two or more parts. The energy embodied by one atom of uranium or plutonium is greater than the sum of all the daughter particles, so when an atom fissions, the result is a release of energy. Capture that energy in a reactor and it can power a city.
The basic insight of fusion is similar to that behind fission: the mass-energy equivalent of two atoms of heavy hydrogen, known as either deuterium or tritium depending on how many neutrons they have, is greater than that of one atom of helium. When those deuteriums or tritiums fuse together to form helium, that extra energy must be released. Astrophysicists in the 1920s and 1930s realized that process is what powered the stars, and weapons designers adapted it to produce higher-yield thermonuclear weapons. Once physicists began sketching out how much energy could be captured through extracting heavy hydrogen from seawater and fusing it, fusion became a byword for clean, unlimited power.
Getting from a blackboard calculation to a viable energy source has been almost impossibly difficult.
Recommended for You: Special Report on Clean Energy
Some of the difficulty has been in the physics. Unlike uranium and plutonium, which can fission spontaneously in a large enough pile, atoms don’t fuse together unless given a mighty shove. That’s because each atomic nucleus is positively charged and as the nuclei get closer together, the repulsive electromagnetic force ramps up exponentially. To overcome that force, atoms have to move incredibly fast; expressed as a temperature, the atoms need to be hundreds of millions or billions of degrees, so hot that the electrons are stripped away.
One doesn’t want a billion-degree plasma hitting a wall—the plasma will cool and the wall will be damaged—so proposed fusion designs have bottled the plasma up in a magnetic field. But that makes extracting the energy from a fusion reaction tricky. Also, while fusion is usually described as clean, the fusion reactions that are easiest to produce (involving neutron-bearing isotopes of hydrogen) wind up throwing off lots of stray neutrons, which embed themselves in the surrounding equipment and create radioactive waste.
Until recently, fusion was a challenge so daunting that it took resources on a national or international scale to tackle them. The U.S. Department of Energy built a series of large facilities to blast small pellets of hydrogen with high-energy lasers in hopes of producing a plasma hot enough for fusion. Sandia National Laboratory’s Z machine has the same goal, via running a nanosecond pulse of 18 million amp current through a wire. A number of groups built facilities to contain plasmas within doughnut-shape magnetic fields, called tokamaks, with the aim of eventually holding them long enough to ignite fusion.
The biggest effort, the international research facility known as ITER, is under construction in southern France. The culmination of decades of Big Science research, the $20 billion project to build an enormous magnetic bottle will be considered a success if it can run continuously for 20 minutes and fuse atoms together sometime after 2035.
Negating Neutrons
ITER is emblematic of Big Science and casts a huge shadow, but there are a surprising number of publicly announced smaller fusion efforts. In 2014, for instance, aerospace giant Lockheed Martin released promotional materials about a fusion reactor development program being run out of its famed Skunk Works research complex in Palmdale, Calif. The goal of its “compact fusion” effort was to create a reactor small enough to fit on the back of a flatbed truck. The company has filed for several patents derived from this research, but to date little concrete information has been divulged.
Fusion start-up TAE Technologies sprung from a very public source—a 1997 paper in the journal Science—before spending most of the next two decades in so-called stealth mode. The papers proposed accelerating two beams of ions to very high speed then slamming them together, much as what happens within a particle accelerator. The hope was that colliding beams would be more efficient at creating fusion-friendly conditions than the plasmas that had been used up to that time.
As research at TAE continued through the 2000s at its headquarters in Foothills Ranch in suburban Orange County, Calif., the original beam concept was abandoned. But another fresh idea in the Science paper lives on.
Instead of fusing isotopes of hydrogen together, TAE is working toward fusing single protons into nuclei of boron. That reaction results in an ion of standard carbon, but one that is too energetic to remain stable. It quickly falls apart, decaying into three helium ions and a burst of gamma rays. (The name TAE is contracted from “tri-alpha energy,” a reference to the atomic physics name for helium ions: alpha particles.) One thing that the reaction doesn’t produce is stray neutrons, which means proton-boron fusion would make less radioactive waste than other types of fusion. The boron itself is also non-radioactive and is more abundant in the Earth’s crust than uranium or thorium, and unlike deuterium or other exotic forms of hydrogen, it can be mined and stored as a solid.
“Hydrogen-boron is difficult to do. It requires 20 to 30 times more energy to ‘cook’ than deuterium-tritium fuel,” said Michl Binderbauer, president and chief technology officer at TAE and one of the co-authors of the 1997 Science paper. “But the upside is that over a 40-year lifetime of our machine, there will be no consequential damage from neutrons. That is a huge difference.”
Even so, the energy requirement is not trivial. Whereas the plasma to be created at ITER is expected to be 100 million °C, TAE will need to reach 3 billion °C to create the force necessary to push the protons and the boron ions together.
The magnetic bottle to contain this hot plasma is configured differently than most conventional designs. Instead of a doughnut-shape vessel to avoid open magnetic field lines from which the plasma could escape, the TAE reactor is long and designed to allow some of the plasma to leak out the ends so that the helium produced via fusion doesn’t dampen reactions.
“You can control the plasma profile with the outflow,” Binderbauer said. “And when you do it right, you can select what you are pulling out.” TAE plans to draw energy from the decelerating outflow of electrically charged particles as they fly past electrodes outside the magnetic envelope.
The company has spent more than a decade developing the technology to hold the plasma in place long enough to achieve fusion, and researchers there believe they have reached that benchmark. In February 2018, the company announced that its latest experimental plasma generator, a $100 million machine nicknamed “Norman” for one of the company’s founders, had been making progress toward hitting the “hot enough” benchmark.
Though Binderbauer and his team are confident they can overcome the technical issues needed to achieve fusion in the next decade, Princeton’s Prager noted dryly that opting for proton-boron fusion makes reaching that goal daunting. Compared to other efforts, Prager said, “the physics challenges of the TAE approach are very much harder.”
Atom Smasher
If TAE’s secret weapon is its fuel, General Fusion is betting on its reactor—simultaneously ungainly and elegant. The rendering of the reactor makes it look like an elephantine pincushion: a massive sphere with large cylinders radiating outward. Rather than contain a plasma within a magnetic bottle for seconds until the ions smack into each other, the reactor actively compresses the magnetically held plasma to the point of ignition—which should take just milliseconds.
It’s a daring departure from conventional fusion set-ups, and it will require some innovative engineering to work. In addition to the injectors that create a ring of deuterium-tritium plasma in the center of the sphere, the General Fusion reactor must spin a wall of molten lead and lithium then, once a second, fire pistons that drive the wall symmetrically to the center. To produce the maximum compression, the compressed gas-powered pistons need to move in sync with an accuracy of a few tens of microseconds, repeatedly, for as long as the reactor runs.
For all its smashing atoms with hammers vibe, the concept, called magnetized target fusion, offers some decided advantages. For one, the lead-lithium blanket soaks up all the stray neutrons produced through the fusion of deuterium and tritium, and absorbs their energy as well. That heats up the blanket and conventional heat exchangers along the wall of the reactor to generate steam for power conversion. The molten blanket also protects the rest of the reactor from damage from the high-temperature plasma.
“A lot of the other fusion schemes have the problem where, even if they create fusion, their machines are going to get brittle due to neutron bombardment,” Donaldson said. “We’ve taken care of that as part of our architecture.”
In its Vancouver facility, General Fusion has already fabricated and tested many of the subsystems needed to make the hydrogen plasma and compress it to the point of fusion. They’ve even made cavities in liquid metal, as they will need to in a working fusion reactor, and pounded the metal with a few pistons—“That’s the biggest engineering challenge we’ve tackled to date.” The ethos has been to build devices, test them, and then iterate based on the results. The pace is more like that of a software company than an international science experiment like ITER.
The next step, Donaldson said, is to integrate all these systems into a demonstration of the technology—firing once a day rather than once a second.
“We feel our concept has the easiest and most practical path to commercialization,” Donaldson said. Though Donaldson and his team are confident they are working toward a power plant, they are following a less proven route to fusion, so they will need to demonstrate that the concept is practical.
Small and Fast
Commonwealth Fusion doesn’t have that problem—they are building on the work that has been done by large-scale fusion researchers for decades. According to Bob Mumgaard, Commonwealth’s CEO, the number of unknowns in their design is vanishingly small.
“ITER is a science experiment, and it’s being built in that bespoke, scientific experiment manner,” Mumgaard said. “In our case, we feel the tokamak has reached a level of maturity where we can strip things out of it, simplify it, and make it more applicable to a commercial product.”
Mumgaard says the model is much like space launch vehicles: NASA built generation after generation of experimental launch vehicles to push the limits of the technology, then startups like SpaceX could come in, strip out the redundant features, and create new products that were both more reliable and less expensive.
The startup emerged from the plasma physics lab at MIT in early 2018. Many of the company’s principals, such as Mumgaard, chief technology officer Dan Brunner, and chief science officer Brandon Sorbom, are graduates of the school. And the early renderings of Commonwealth Fusion’s proposed reactor look like scale models of international tokamak fusion experiments to which MIT physicists have contributed.
The scale is the key, though. Mumgaard explained that Commonwealth’s fusion device will take advantage of new types of powerful magnets that will enable it to contain its plasma in a smaller, tighter torus than has been previously possible. That, in turn, will allow other parts of the power plant to become smaller and less expensive.
“We now have technology—basic engineering technology, not moonshot technology—that can produce much higher magnetic fields because of new superconductors,” Mumgaard said. “You can make plasma systems smaller with the same performance. And if we can make them smaller, we can make them more power dense, more economical, and easier to build.”
Rather than pursuing a new avenue that might create a shortcut to a commercial reactor, as TAE and General Fusion are, Commonwealth is using the expertise built up over decades of mainline fusion research and working to turn it into a commercial product as quickly as possible.
Mumgaard projects the confidence of someone who sees the object of a long quest peeking over the horizon. Indeed, he lays out a fairly short time frame—about three more years of R&D, then four years of building—to reach the first prototype reactor. By the time ITER is up and running, Mumgaard believes Commonwealth Fusion may have the capability to begin producing commercial reactors.
“One of the advantages of the approach that we’re taking is that we don’t need a lot of plasma physics and fusion expertise—that’s embodied in the mainline approach,” Mumgaard said. “We’re adding in the engineering of making it manufacturable. That requires mechanical engineers and structural engineers and systems engineers, the type of high-end engineering you’d find on a Formula One team or a place like SpaceX.”
Princeton’s Prager believes Commonwealth Fusion’s approach of taking the existing state of plasma physics and turning that into a product is a sound one. “That effort is different from many other companies in the field because it is developing the mainstream fusion concept,” he said, “and adding the technological advance of high-field magnets.”
That’s not to say that other approaches won’t work. Prager suggests that we may eventually wind up with multiple fusion power concepts breaking into commercialization.
“There might be a first-generation fusion reactor,” Prager said, citing the doughnut-shape reactor as a potential winner, “but then another one of these concepts, such as the one TAE is developing, could become a second-generation reactor.”
Fusion will probably remain a futuristic-sounding technology for the time-being—a byword for something that would be world changing if we could only get it. But the momentum in the field seems to be building, and money and talent pouring seems to point to a breakthrough that will catch the cynics by surprise.
“We have come very far with fusion—that’s something not generally appreciated by the public,” Prager said. “We still have engineering and science challenges, but I think we can see our way through them. We might not have a commercial plant in 15 years, but it’s not 50 years off, either.”
Jeffrey Winters is a senior editor at Mechanical Engineering magazine.
Also read: Special Report on Clean Energy
Read the latest issue of theMechanical Engineering Magazine.