The Rolling Tires and the Beating Heart
The Rolling Tires and the Beating Heart
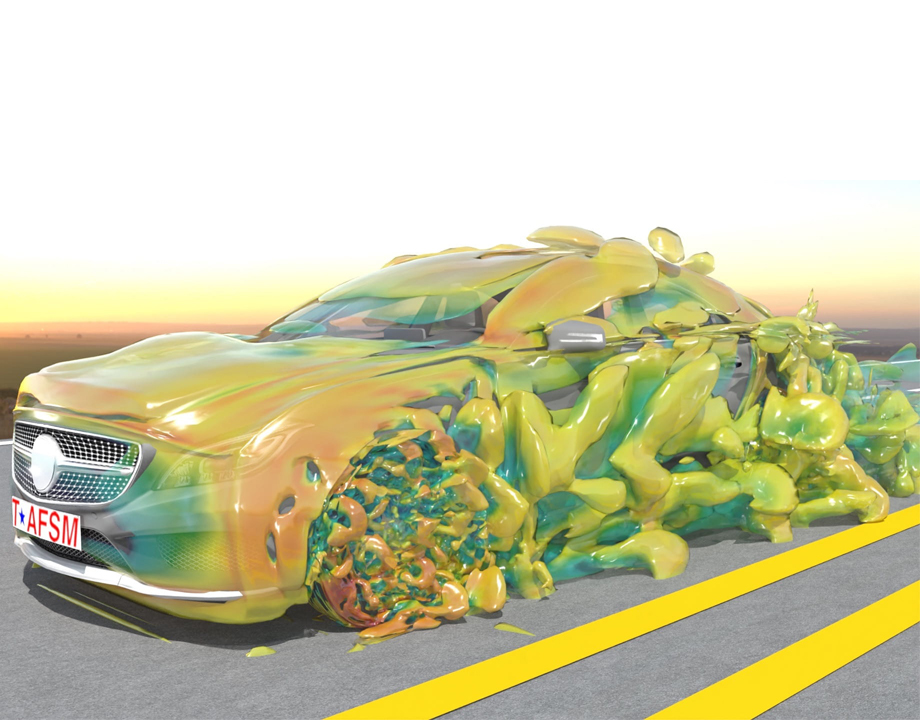
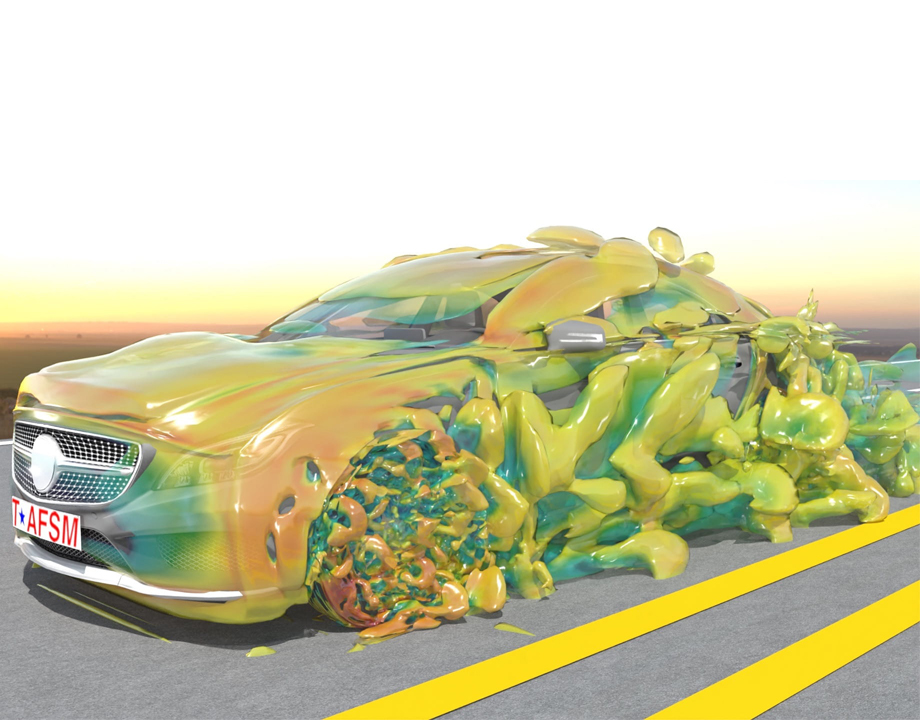
A depiction of how air flows around a moving vehicle, complete with tire deformation, from Rice University researchers. Credit: Rice University
A look at blood flowing through the human heart and air flowing around a car might not seem to have much in common. Actually, they’re part of a demonstration of a complex new method of fluid modeling.
The technique cuts computational time and costs while allowing for very complex computational fluid dynamic (CFD) models, according to researchers at Rice University in Houston and Waseda University in Tokyo who developed the method. They have modeled the flow around moving cars, right down to the air moving around rolling tires and the blood moving through a human heart as it beats.
Both projects have been led by researchers in the Rice laboratory of Tayfun Tezduyar, a Rice professor of mechanical engineering who has worked on sophisticated fluid-flow models of the human circulatory system as well as parachutes, wind turbines, and vehicles.
In February, just in time for Valentine’s Day 2022, the Team for Advanced Flow, Simulation, and Modeling at the Rice lab produced a video of fluid flow in a beating heart, a close-up view never before seen, due, of course, to the nature of the heart. To see it in action is impossible in a living person, Tezduyar said. There are medical devices that help depict individual looks at the human heart, but none provide this detailed view.
More for You: The Forefront of Electronics and Fluid Power
The researchers worked with colleagues at Waseda University to tackle what Tezduyar said is one of the toughest problems in biomechanics: a way to accurately characterize the flow of blood around and through the heart’s valves, taking into account the flow details near the surfaces of the valve’s three leaflets along the way.
The simulation can help clinicians understand the mechanisms that push blood through the body and learn how to aid the heart when blood flow is interrupted, Tezduyar said.
A visualization produced by the team depicts a top-view and a side-view of the heart’s ventricle-valve-aorta as it fills with blood. It shows the three-leaf valve quickly opens to relieve the pressure from the blood flow and the turbulent flow of blood as it pushes through.
“This is a computational technology that no one else in the world currently has with this level of accuracy near the leaflet surfaces,” Tezduyar said. “We’ve become aware recently that people at the Texas Medical Center are asking for CFD simulations of the cardiovascular system. I think perhaps they meant what happens just in the aorta, and that would have been a lot easier. But we went a little beyond.”
They could also have been said to go “a little beyond” in their more recent video that depicts airflow around a vehicle, including air moving around moving tires. Complicating the model is the fact that the tires are in contact with the road and deform as they roll, Tezduyar said.
Listen to Our Podcast: The Unknown Strengths of Fluid Power
The heart simulation shows how blood moves “through” the heart. The new simulation shows what happens as air flows around a moving object, he added.
The team calls the technique they developed to simulate these problems NURBS surface-to-volume guided mesh generation method. NURBS, which stands for non-uniform rational basis splines, is a mathematical technique to describe three-dimensional shapes and provide computational analysis of fluid and structural mechanics problems involving them.
NURBS’ use in computational analysis has grown in recent years, combining efficiency and accuracy by lowering the number of “mesh” points necessary to model a system.
In one model of a moving car the computational flow analysis with NURBS was achieved with about 1.1 million mesh points, a fraction of the number used in customary methods, while retaining its accuracy. That lowers the computational cost as well, Tezduyar said.
Recently, Takashi Kuraishi, a research associate in the Rice lab, produced a video that showed the airflow simulation in action.
“Knowing the airflow behavior around the car and its tires will lead to better understanding of their aerodynamic performance,” Kuraishi said. “Simulations this sophisticated are important to provide realistic solutions and reliable answers in design and performance evaluation.”
Jean Thilmany is a science and technology writer in Saint Paul, Minn.
The technique cuts computational time and costs while allowing for very complex computational fluid dynamic (CFD) models, according to researchers at Rice University in Houston and Waseda University in Tokyo who developed the method. They have modeled the flow around moving cars, right down to the air moving around rolling tires and the blood moving through a human heart as it beats.
Both projects have been led by researchers in the Rice laboratory of Tayfun Tezduyar, a Rice professor of mechanical engineering who has worked on sophisticated fluid-flow models of the human circulatory system as well as parachutes, wind turbines, and vehicles.
In February, just in time for Valentine’s Day 2022, the Team for Advanced Flow, Simulation, and Modeling at the Rice lab produced a video of fluid flow in a beating heart, a close-up view never before seen, due, of course, to the nature of the heart. To see it in action is impossible in a living person, Tezduyar said. There are medical devices that help depict individual looks at the human heart, but none provide this detailed view.
More for You: The Forefront of Electronics and Fluid Power
The researchers worked with colleagues at Waseda University to tackle what Tezduyar said is one of the toughest problems in biomechanics: a way to accurately characterize the flow of blood around and through the heart’s valves, taking into account the flow details near the surfaces of the valve’s three leaflets along the way.
The simulation can help clinicians understand the mechanisms that push blood through the body and learn how to aid the heart when blood flow is interrupted, Tezduyar said.
A visualization produced by the team depicts a top-view and a side-view of the heart’s ventricle-valve-aorta as it fills with blood. It shows the three-leaf valve quickly opens to relieve the pressure from the blood flow and the turbulent flow of blood as it pushes through.
“This is a computational technology that no one else in the world currently has with this level of accuracy near the leaflet surfaces,” Tezduyar said. “We’ve become aware recently that people at the Texas Medical Center are asking for CFD simulations of the cardiovascular system. I think perhaps they meant what happens just in the aorta, and that would have been a lot easier. But we went a little beyond.”
They could also have been said to go “a little beyond” in their more recent video that depicts airflow around a vehicle, including air moving around moving tires. Complicating the model is the fact that the tires are in contact with the road and deform as they roll, Tezduyar said.
Listen to Our Podcast: The Unknown Strengths of Fluid Power
The heart simulation shows how blood moves “through” the heart. The new simulation shows what happens as air flows around a moving object, he added.
The team calls the technique they developed to simulate these problems NURBS surface-to-volume guided mesh generation method. NURBS, which stands for non-uniform rational basis splines, is a mathematical technique to describe three-dimensional shapes and provide computational analysis of fluid and structural mechanics problems involving them.
NURBS’ use in computational analysis has grown in recent years, combining efficiency and accuracy by lowering the number of “mesh” points necessary to model a system.
In one model of a moving car the computational flow analysis with NURBS was achieved with about 1.1 million mesh points, a fraction of the number used in customary methods, while retaining its accuracy. That lowers the computational cost as well, Tezduyar said.
Recently, Takashi Kuraishi, a research associate in the Rice lab, produced a video that showed the airflow simulation in action.
“Knowing the airflow behavior around the car and its tires will lead to better understanding of their aerodynamic performance,” Kuraishi said. “Simulations this sophisticated are important to provide realistic solutions and reliable answers in design and performance evaluation.”
Jean Thilmany is a science and technology writer in Saint Paul, Minn.