Understanding the Limits of Machine Learning
Understanding the Limits of Machine Learning
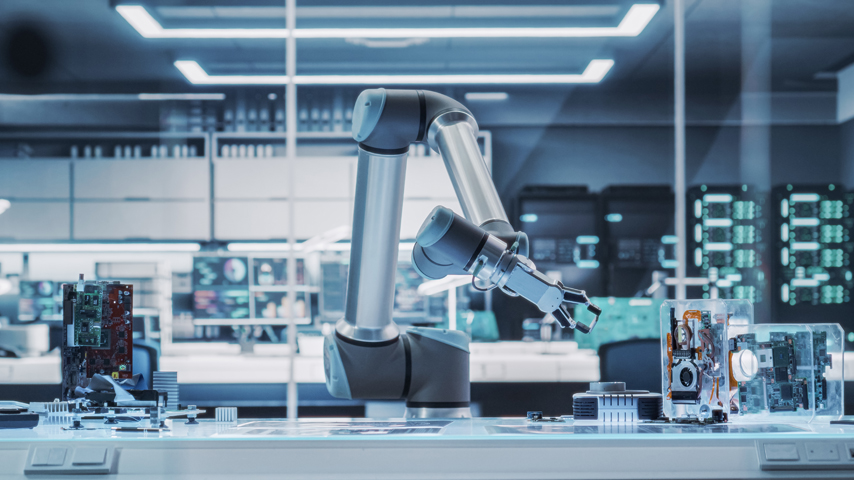
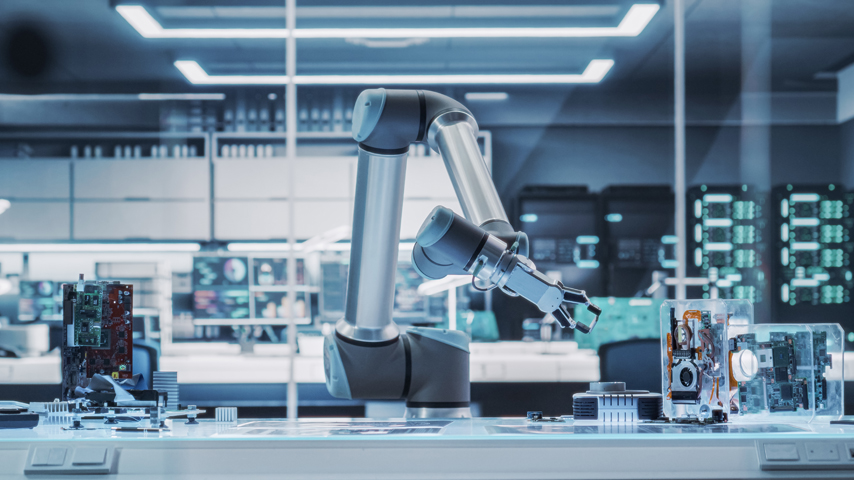
The proper application of machine learning to robotic control systems starts with understanding what they can’t do.
In the popular 1980’s movie, The Terminator, Skynet, a powerful artificial intelligence system, learns to become self-aware and, as a result, teaches its robot counterparts to wipe out the very human beings that created it. But Bruce Lee, a graduate student at the University of Pennsylvania’s Department of Electrical and Systems Engineering, said that machine learning algorithms aren’t quite as adept as learning from complex situations as popular culture may have led us to believe. They have limits to what they can learn and, to move the field of dynamic control systems forward, particularly in robotics and autonomous vehicle applications, it’s important to understand what those limits are.
“We see all these impressive applications of learning for robotics where a robotic pilot can outperform a human in autonomous drone racing and there are also general-purpose robots from Google where you can give a general language command, and they’ll execute some household task. They are all very impressive,” said Lee. “But they you try a lot of these methods in simple benchmark systems, and you can’t get the algorithm to work. You’re left with the question: Why?”
To answer that question, Lee, under the guidance of his advisor, Nikolai Matni, assistant professor of Electrical and Systems Engineering and a member of the Penn Research in Embedded Computing and Integrated Systems Engineering (PRECISE) Center, has been making a rigorous study of where you can expect these machine algorithms to work and in which systems the problems just may be too complex for them to function correctly. The idea is to provide appropriate guidance to roboticists and programmers so they can better understand where, when, and how these control algorithms will work not just in theory—but in practice.
In a recent project, Lee focused on a common control system called a linear quadratic regulator. Such algorithms are designed to operate a dynamic system in an optimized way and are often used in automobile and energy applications.
“From a control perspective, linear systems are the simplest models of a robotic system. If it doesn’t work well on a linear system, you shouldn’t expect it to work well on something more complex,” Lee said. “And if you are trying to understand the fundamental limits of a system, looking at the simplest system can often give you the best insights.”
Lee discovered that these systems, as they try to learn new, more complex tasks can require immense amounts of data to work reliably.
“It was surprising to see that linear systems could require so much data,” Matni said. “Typically, people associate difficulty in learning with some notion of bad measurements—they are somehow not getting the whole picture, not getting clear information or there’s some kind of noise. But our results showed this wasn’t the case at all. You can know everything about the system and every measurement point and still end up getting into trouble because there’s not enough data, especially in mechanical systems.”
Lee said that he helps roboticists and engineers, after looking at his work, will understand that, despite the fact that machine learning algorithms are showing up in all kinds of systems nowadays, they aren’t suited to solve every problem. But understanding the fundamental limits of machine learning can help not only identify and design the best algorithms to use for control systems for different applications, but how to troubleshoot problems when developers do encounter failures.
“Rather than asking, ‘Do I have the right algorithm?’ You should first ask yourself whether or not you have the right system,” Lee said. “Sometimes it’s just not possible for a robot to learn efficiently using a particular system.”
More For You: Energy Blog: Is AI Too Power-Hungry for Our Own Good?
He added that engineers can retool and restructure different applications to make them more amenable to learning—an additional sensor here, a new actuator there. But it’s important to consider which algorithm is optimal for a particular system given the problem you are trying to solve.
“There are different ways of collecting data for a system that will enable it to learn more effectively,” Lee said. “By understanding these lower bounds or fundamental limits of what an algorithm can learn, you get a better idea of the approach you should take—the type of data collection and the types of machine learning algorithms to apply to achieve them.”
Discover the Benefits of ASME Membership
Matni agreed and added that roboticists need only look at the simpler systems in the greater whole to better understand where their control systems may be falling short.
“Think of them as chains of systems connected together with sparse actuation and sensing,” Matni said. “Bad controller systems for even the best controller leads to bad performance. Those are going to have a really hard time learning the task you care about. It’s going to take a ton of data to find the best controller for your system and the best controller is still going to give you poor performance. So, if you find yourself in a scenario where you are getting a lot of data, you’re running these learning algorithms, and you are not getting the performance you want, it’s a signal that it’s a hard system and something needs to change.”
Kayt Sukel is a technology writer and author in Houston, Tex.
“We see all these impressive applications of learning for robotics where a robotic pilot can outperform a human in autonomous drone racing and there are also general-purpose robots from Google where you can give a general language command, and they’ll execute some household task. They are all very impressive,” said Lee. “But they you try a lot of these methods in simple benchmark systems, and you can’t get the algorithm to work. You’re left with the question: Why?”
Algorithms in practice
To answer that question, Lee, under the guidance of his advisor, Nikolai Matni, assistant professor of Electrical and Systems Engineering and a member of the Penn Research in Embedded Computing and Integrated Systems Engineering (PRECISE) Center, has been making a rigorous study of where you can expect these machine algorithms to work and in which systems the problems just may be too complex for them to function correctly. The idea is to provide appropriate guidance to roboticists and programmers so they can better understand where, when, and how these control algorithms will work not just in theory—but in practice. In a recent project, Lee focused on a common control system called a linear quadratic regulator. Such algorithms are designed to operate a dynamic system in an optimized way and are often used in automobile and energy applications.
“From a control perspective, linear systems are the simplest models of a robotic system. If it doesn’t work well on a linear system, you shouldn’t expect it to work well on something more complex,” Lee said. “And if you are trying to understand the fundamental limits of a system, looking at the simplest system can often give you the best insights.”
Lee discovered that these systems, as they try to learn new, more complex tasks can require immense amounts of data to work reliably.
“It was surprising to see that linear systems could require so much data,” Matni said. “Typically, people associate difficulty in learning with some notion of bad measurements—they are somehow not getting the whole picture, not getting clear information or there’s some kind of noise. But our results showed this wasn’t the case at all. You can know everything about the system and every measurement point and still end up getting into trouble because there’s not enough data, especially in mechanical systems.”
Understand limits
Lee said that he helps roboticists and engineers, after looking at his work, will understand that, despite the fact that machine learning algorithms are showing up in all kinds of systems nowadays, they aren’t suited to solve every problem. But understanding the fundamental limits of machine learning can help not only identify and design the best algorithms to use for control systems for different applications, but how to troubleshoot problems when developers do encounter failures.“Rather than asking, ‘Do I have the right algorithm?’ You should first ask yourself whether or not you have the right system,” Lee said. “Sometimes it’s just not possible for a robot to learn efficiently using a particular system.”
More For You: Energy Blog: Is AI Too Power-Hungry for Our Own Good?
He added that engineers can retool and restructure different applications to make them more amenable to learning—an additional sensor here, a new actuator there. But it’s important to consider which algorithm is optimal for a particular system given the problem you are trying to solve.
“There are different ways of collecting data for a system that will enable it to learn more effectively,” Lee said. “By understanding these lower bounds or fundamental limits of what an algorithm can learn, you get a better idea of the approach you should take—the type of data collection and the types of machine learning algorithms to apply to achieve them.”
Discover the Benefits of ASME Membership
Matni agreed and added that roboticists need only look at the simpler systems in the greater whole to better understand where their control systems may be falling short.
“Think of them as chains of systems connected together with sparse actuation and sensing,” Matni said. “Bad controller systems for even the best controller leads to bad performance. Those are going to have a really hard time learning the task you care about. It’s going to take a ton of data to find the best controller for your system and the best controller is still going to give you poor performance. So, if you find yourself in a scenario where you are getting a lot of data, you’re running these learning algorithms, and you are not getting the performance you want, it’s a signal that it’s a hard system and something needs to change.”
Kayt Sukel is a technology writer and author in Houston, Tex.
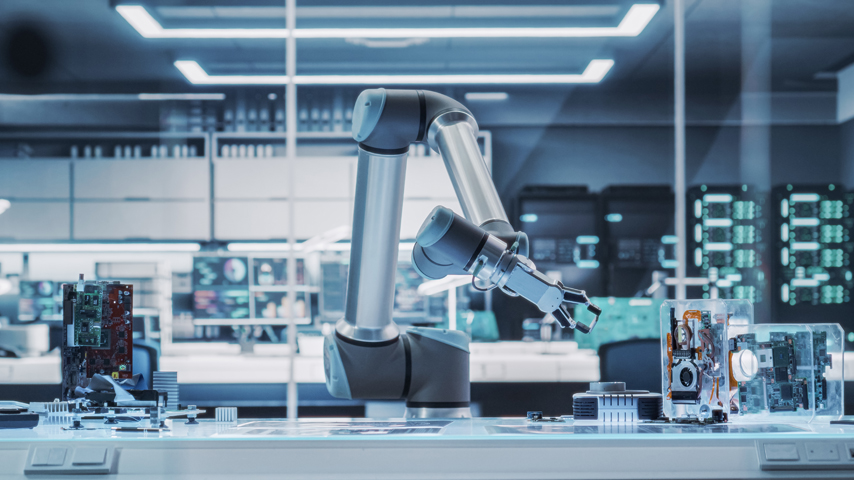
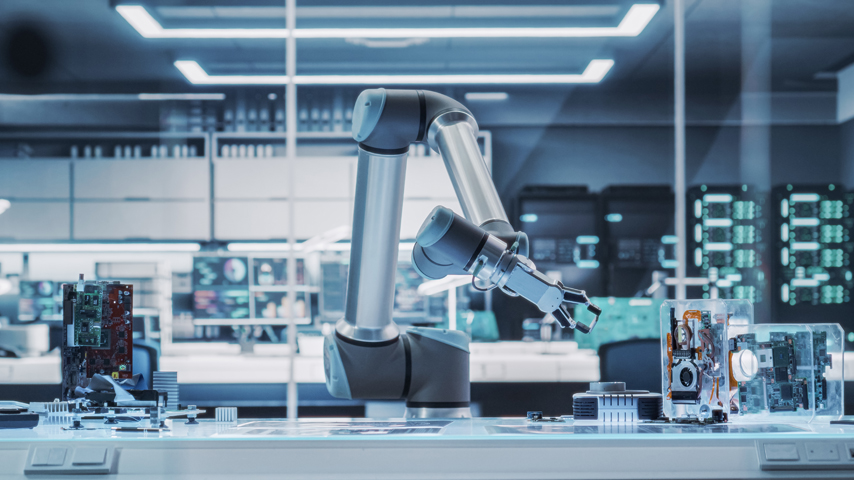