Using Concrete to Carry a Charge
Using Concrete to Carry a Charge
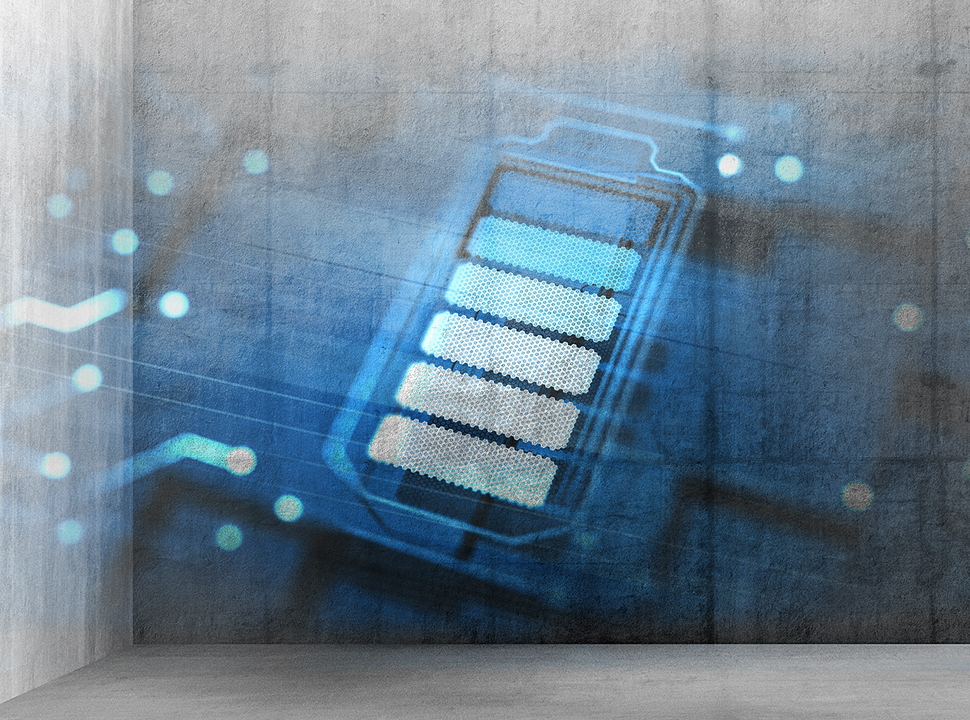
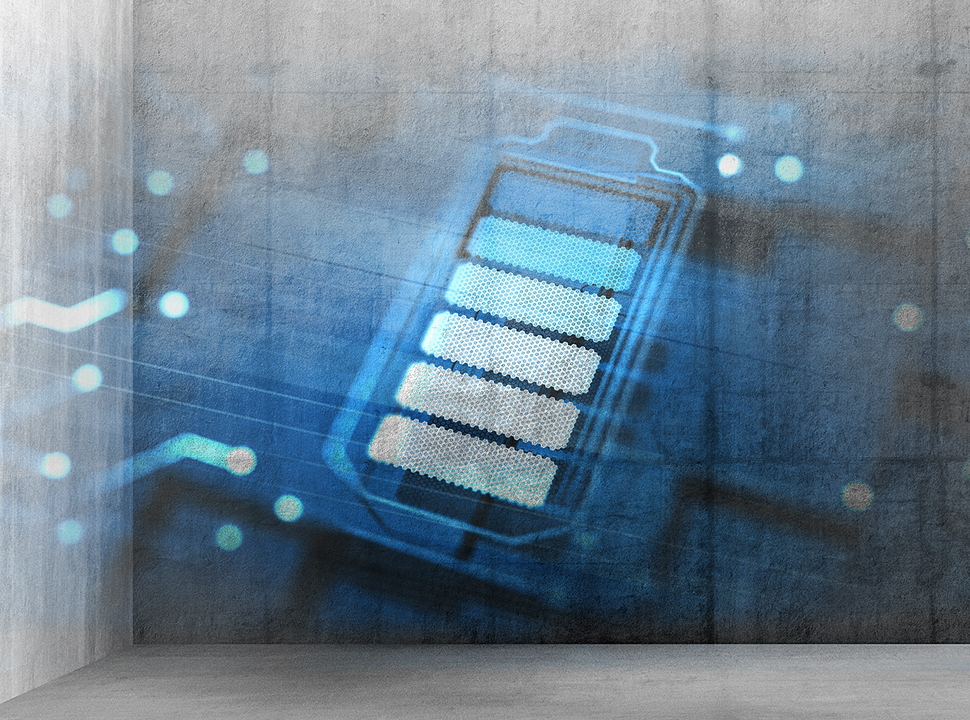
Rechargable concrete might store energy from renewable sources
If our homes and offices are to be powered someday by interruptable streams of renewable energy batteries will probably be needed to keep electricity flowing when the sun is down and the wind isn’t blowing. But batteries have their own nongreen downsides, chief among them the environmental cost of producing and shipping them. Those qualms would evaporate if the very walls of our homes and offices could store energy.
Thanks to the work of a Emma Zhang, a recent postdoctoral researcher at Sweden’s Chalmers University of Technology, and Luping Tang, a professor of building materials at the university’s Division of Building Technology, the structure of our homes may soon power our homes.
Zhang, now a senior development scientist for product development at Delta of Sweden, created a 9-x-9-centimeter, one-centimeter-thick slab of rechargeable concrete with an energy density of 7 Watt-hours per square meter. “If we have a 100-square-meter house that has 200 square meters of wall or panels or floors made of concrete, that is 200 square meters of a potential concrete battery that could store about two kilowatts hour energy per day,” she said.
Zhang’s attempt at creating a concrete battery is not the first. Ten years ago, materials scientist Deborah Chung, of SUNY Buffalo, first tried the concept. But her battery produced a fraction of the energy (1.42 micro-watts a square centimeter) as it used only the water in concrete as an electrolyte. And it wasn’t rechargeable. Zhang decided to add something conductive to the mix. She turned to a product that could also be used to reinforce the concrete: carbon fiber. She used short chopped up carbon fibers added directly to the concrete.
More for You: Advancing Battery Technology for Modern Innovations
“We were measuring the conductivity and the malleability of the mortar,” she said. “As you increase the conductivity, you lose the malleability.” The optimal concentration of carbon fiber turned out to be between 0.8 and 0.9 percent.
The battery is essentially a three-layered sandwich of concrete. The outside layers are reinforced with a mesh of coated carbon fiber acting as electrodes; iron on the anode side, and nickel for the cathode. “Exactly the same principle as the Thomas Edison battery,” said Zhang. “It’s a very robust system and can tolerate over-charging and over-discharging and have a very long service life. At the same time, the battery capacity is low, but since we have a really huge volume of concrete that could be used, it’s not a disadvantage for concrete batteries.”
Corrosion is not an issued because of its low current and voltage. In a worst-case scenario, corrosion of the carbon fiber in either the electrodes or the conducting mortar would not be even noticeable for at least a hundred years, she said. Nor is excess heat likely to turn away any users. The walls would likely only be a few degrees hotter than ambient temperature and very little of that would warm the air.
Editor’s Pick: Video: What Are Electrofuels?
A bigger challenge is how to recycle it when the building or battery is ready to retire. Composite materials are notoriously hard to recycle. “One possible solution for recycling is to crush the old concrete batteries to make new concrete batteries,” said Zhang. Another possibility is to simply use the rubble as aggregate for roads.
The next step is to build a meter-by-meter version and build a pilot project. “We have to see how it performs in real life,” said Zhang. “In my perfect world, in my dreams, it could happen in a few years. If other researchers have an interest in working on this topic it would evolve much faster.”
Michael Abrams is an engineering and technology based in Westfield, N.J.
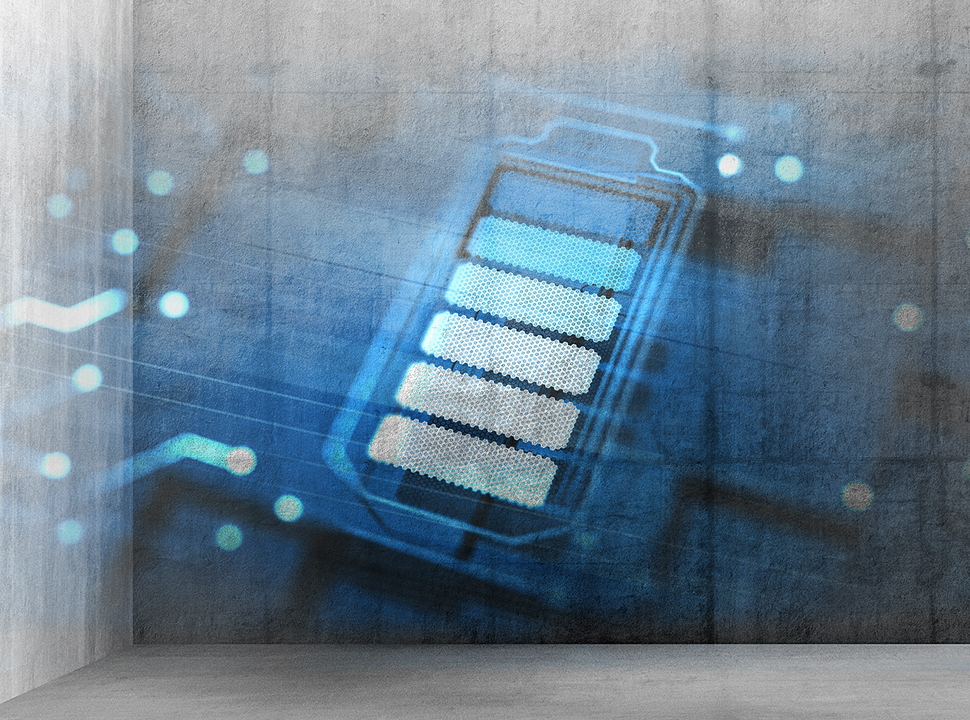
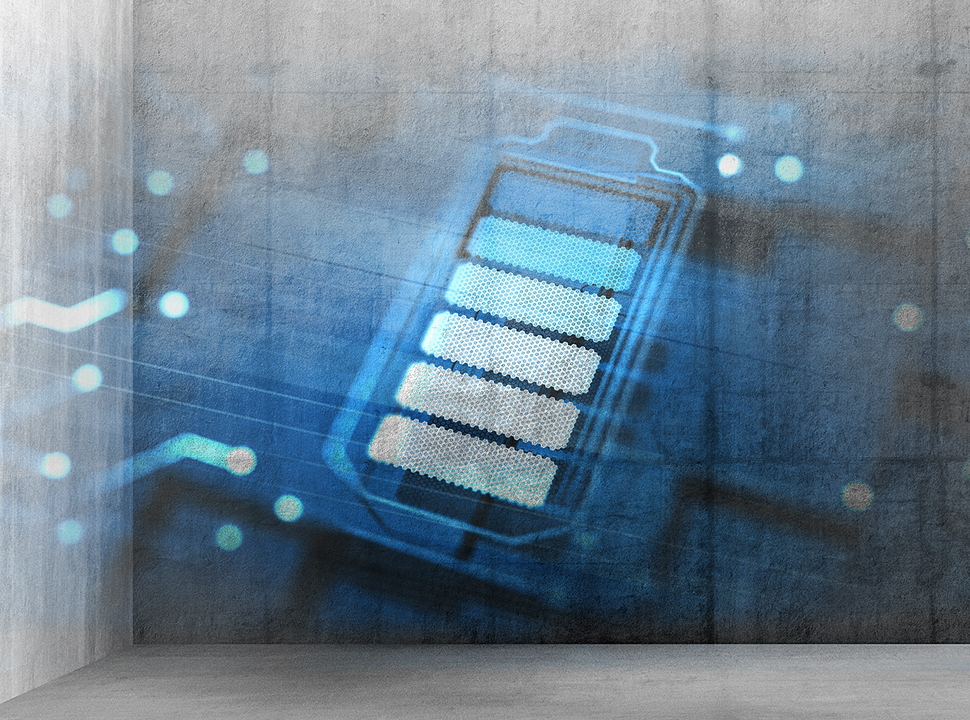