Virtual Prototypes Are Getting So Good They Can Eliminate Physical Ones
Virtual Prototypes Are Getting So Good They Can Eliminate Physical Ones
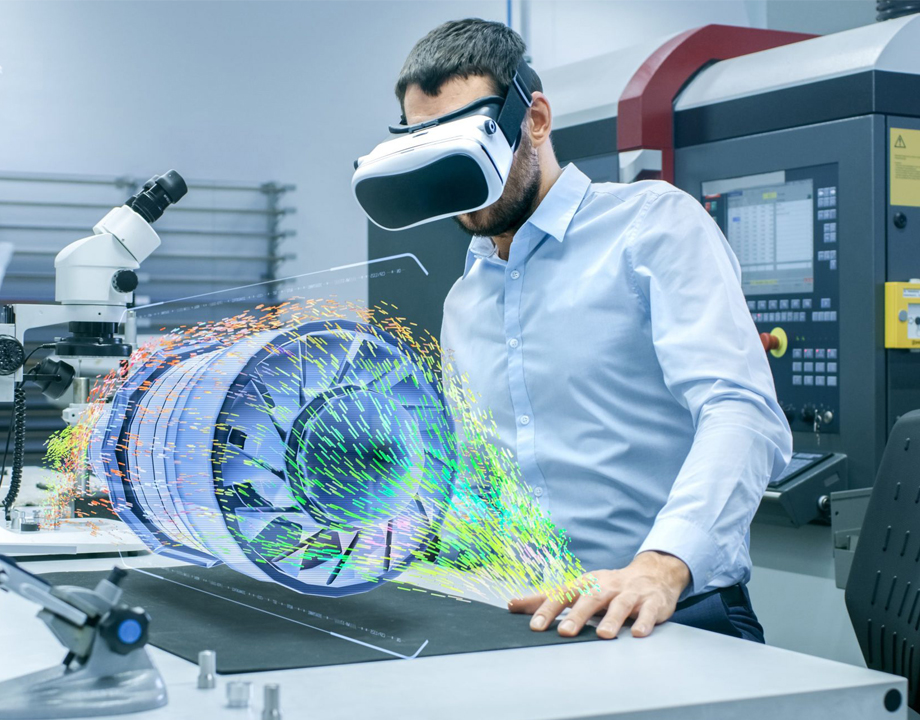
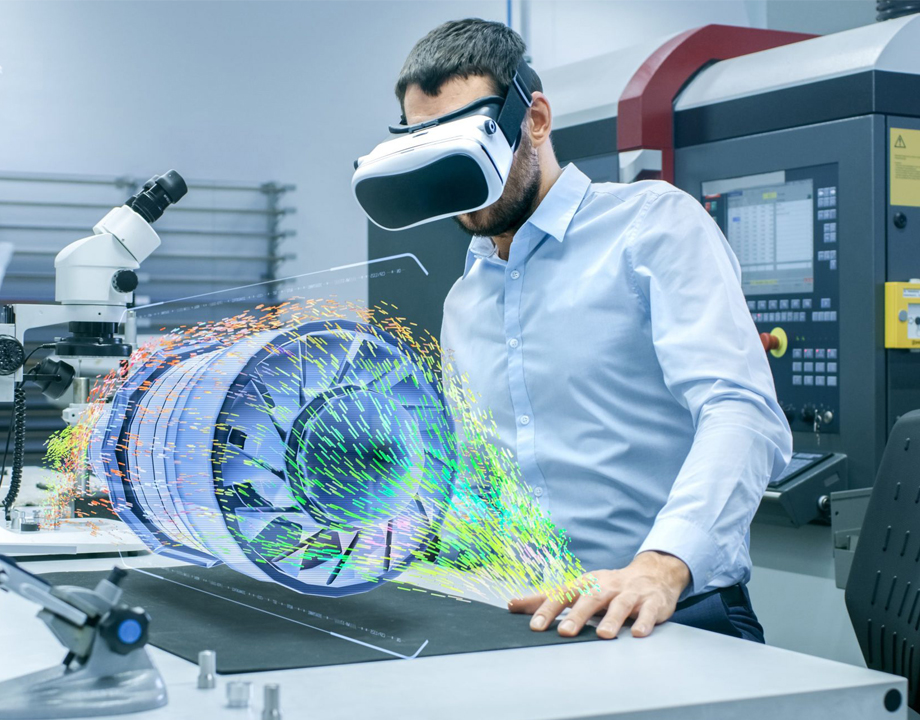
Manufacturers use computers to manipulate virtual prototypes and create highly detailed virtual models of components or products to finally produce a production-ready physical prototype.
Besides high quality and performance, the number-one goal for many manufacturers is reducing time to market (TTM). VP is being used on an increasing number of product designs to predict performance and speed up production, before building physical prototypes. Engineers can quickly explore thousands of design options to evaluate performance before investing the time and capital needed to build physical prototypes. System performance can be tested and refined in almost unlimited ways until the best model has been created, which greatly reduces the time of new product development and speeds up TTM.
Advantages of VP
Once a virtual product model has been designed, it can be tested in various ways to optimize performance, without building a physical model first. This allows designers and engineers to measure the response of tiny components that ordinarily would be highly difficult to measure with instruments.
Become a Member: How to Join ASME
Advantages of VP compared to standard prototyping are:
-
Tests all mechanical systems before building the actual system
-
Takes less time for testing
-
Explores multiple design options quickly
-
Optimizes product quality, performance, and longevity
-
Reduces operational costs
-
Improves communication and decision making among all stakeholders
-
Speeds up TTM
Key VP tools for engineers include:
-
Computer-aided engineering (CAE) simulates and optimizes product design and manufacturing processes and evaluates key variables such as strength, temperature, pressure, corrosion resistance, and flexibility.
-
Finite element analysis (FEA) relies on powerful software to evaluate the structural details of a design before prototyping starts. It is ideal for identifying weak points in a design that could lead to failure or poor performance. FEA includes both linear and non-linear testing.
-
Computational fluid dynamics (CFD) analyzes potential fluid-flow dynamics by altering variables that reflect real-world operating conditions. CFD simulates the action of thermo-fluids in response to changing variables within the product or system being tested, especially virtual experiments and prototyping.
-
Computer-aided machining (CAM) allows design engineers to create simulations that reflect different machining methods, workflows, quality analysis, and testing set-ups. It can use Internet of Things (IoT) technologies and artificial intelligence in the VP environment to identify the best machining process for a particular product.
-
Hardware-in-the loop (HIL) testing is especially popular in the automotive industry, where real signals from a controller are connected to a test system that simulates driving conditions. Rapid testing and design iteration can evaluate thousands of possible scenarios that fully test the controller, without having to do actual physical tests.
- Digital twins are exact (or very close) digital replicas of a real-world device or system. Digital twins exist only in the virtual domain and are manipulated virtually to test thousands of “what if” scenarios, ultimately defining the best design for a particular application, before any expensive manufacturing investments are made. Digital twins may soon be a viable alternative to HIL in the near future.
Future of VP
Parts, assemblies, and finished products continue to get smaller and more complex. Manufacturers want to use Industry 4.0 technologies, especially high-performance computing, IoT, artificial intelligence (AI), and machine learning to test and validate designs, which greatly accelerate speed to market. VP has the potential to ultimately eliminate actual prototyping. In fact, VI-Grade, a German simulation and driving simulator company, is keen on moving toward zero prototypes and even hosts an annual Zero Prototypes Summit.
Try Taking a Quiz: How Augmented and Virtual Reality Is Enhancing Manufacturing
Virtual prototypes have already been created that are accurate enough to be taken to production—without the need for a physical prototype for engineers to hold, examine, test, and revise. This is, of course, depends on the complexity of the product.
“Generally speaking, the more simplistic the product design is, with a small number of components, the easier it will be to produce from a virtual prototype,” said Jackson Hedden, president of Jackson Hedden Inc., a Birmingham, Ala.-based industrial design firm. “In contrast, a product with multiple components—in the range of dozens or hundreds—would be incredibly risky to produce without making a physical prototype first.”
The next advancements in VP will most likely be AI-driven, moving toward improving the ability to perfectly define an object or product in virtual space, thereby greatly reducing the number of prototypes needed to take it to production. “Some companies create hundreds of prototypes before making the product a reality,” Hedden said. “We have found that virtual prototyping can reduce those high numbers to a total of one to three prototypes on average. VP allows designers to make changes on the fly and truly visualize an item in its entirety, so that any shortcomings are noticed almost immediately.”
Mark Crawford is technology writer based in Corrales, N.M.
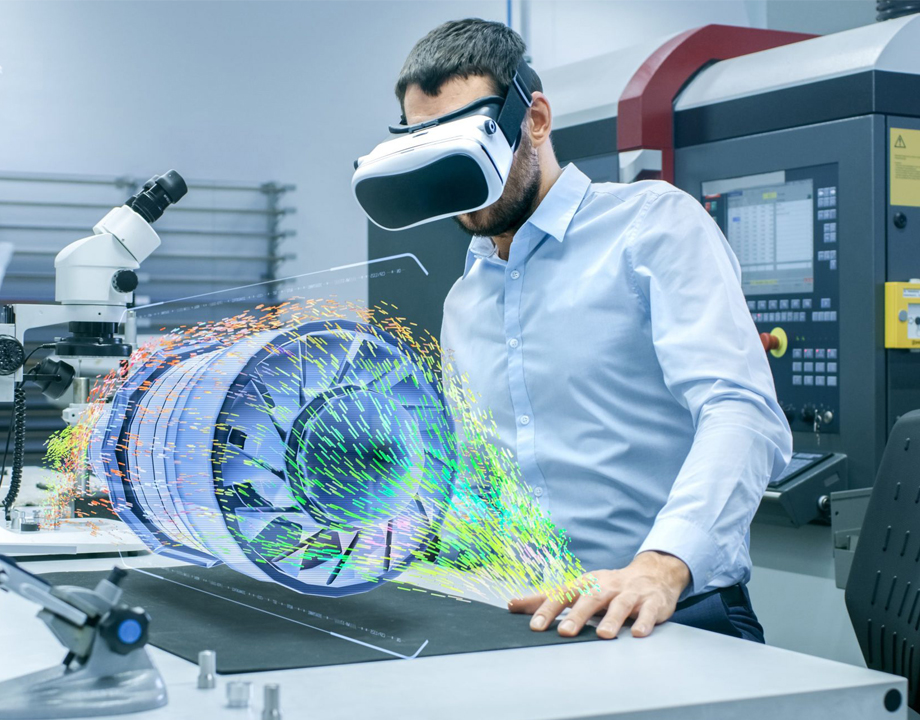
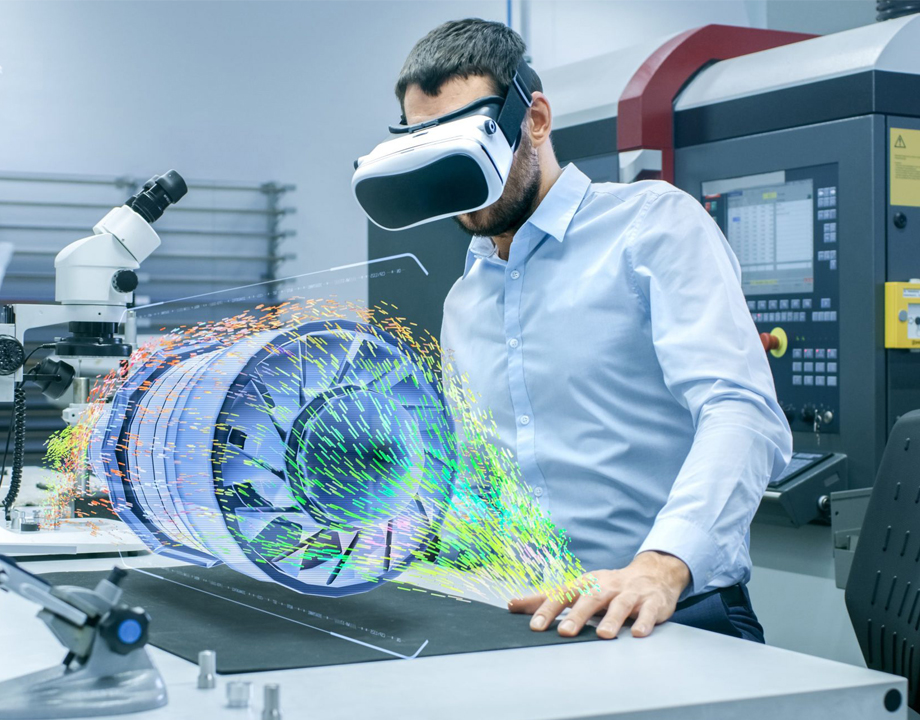