Finding Subsurface Damage on Aircraft
Finding Subsurface Damage on Aircraft
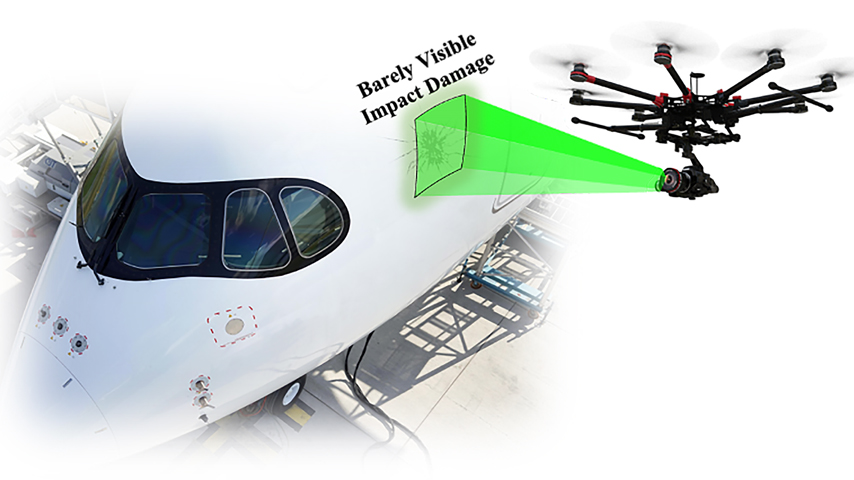
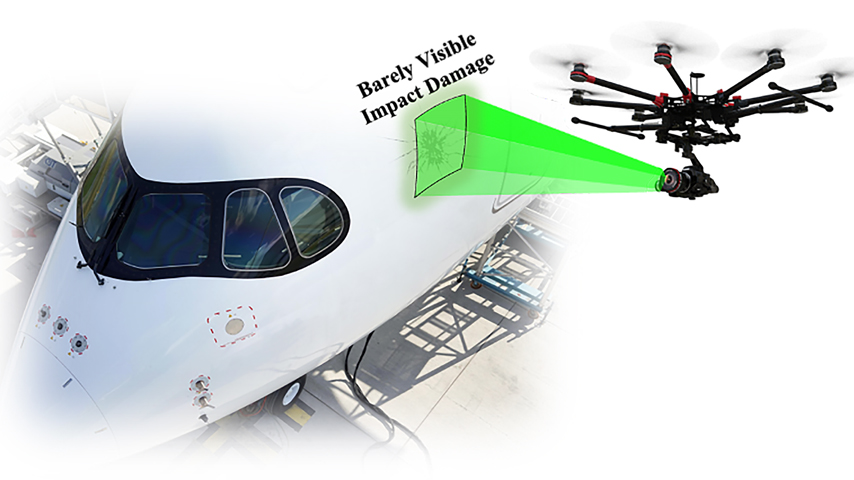
Traditional inspection methods fall short when used on planes made of fiber-reinforced polymers. A new method using wave propagation may find subsurface damage.
If you fall and scrape your knee, evidence of the injury is usually pretty visible. But there’s a reason that medical professionals use ultrasound and X-ray machines: Serious problems often play out underneath the surface and can go undetected.
A similar situation is unfolding with respect to the inspection of aircraft. When planes are constructed with lightweight metals such as aluminum, any damage causes surface dents that are easy to detect using visual inspection. But a greater number of aircraft today are made with fiber-reinforced polymers (FRP), which demonstrate very different responses to external damage. They don’t dent visibly but the damage plays out beneath the surface, which means traditional visual inspection methods don’t catch the full extent of potential problems.
Researchers at North Carolina State University have developed a solution: a noninvasive method to evaluate subsurface damage to composite aircraft bodies so safety will not be compromised. The procedure involves applying a Lamb wave to the surface and recording a 3-second video of the wave propagation. Applying signal processing techniques to the result reveals subsurface damage.
Carbon fiber-reinforced polymers (CFRPs) are lightweight and strong composites that help planes consume less fuel, thereby decreasing carbon emissions. As a result, they are becoming the construction material of choice for aircraft.
Become a Member: How to Join ASME
CFRPs are made up of layers of fibers bonded in a resin matrix. Their brittleness does not allow surface impact energy to dissipate neatly through. Instead, the layers delaminate under the surface, said Bryce Abbott, a fifth-year doctoral student of aerospace engineering at North Carolina State University, working with Professor Fuh-Gwo Yuan. So traditional visual inspection methods break down because there’s no visible damage.
The structural health monitoring (SHM) solution for CFRP-built planes that Abbott and Yuan propose helps detect subsurface damage using a Lamb wave from an active sensor. The solution builds on the premise that such a wave will propagate uniformly through a medium until it reaches an irregularity or defect. So studying the movement of the wave through the body of the aircraft should help spot problems.
In the solution, an active sensor attached to the surface of the aircraft via suction emits a sweep of frequencies that propagate across the structure. A camera captures the entire wave field for three seconds.
"If you’re able to fully reconstruct the wave as it propagates across the structure, you can look for interactions of the wave with any subsurface damage,” Abbott said. If there is subsurface damage, the wave is trapped within the damage boundaries and constructively interferes to create a higher amplitude at that location, which will show up in the recording.
More for You: Air Force Sees Promise in Blended Wing aircraft
To better observe the movement of a deforming wave, it helps to have a feature of interest on which to focus. Abbott achieved this by applying a speckle pattern on the surface. “Once they move, they show up in the video and we can use image processing algorithms to quantify the motion pretty much at each pixel location,” Abbott said.
The process applies two filters to the video recording to eliminate any external noise. The first gets rid of any vibrations that are outside of the frequency being applied and the second separates out propagating waves from standing ones to zero in on the damage.
Other methods to detect such subsurface defects depend on fully reconstructing the wave as it propagates. Laser doppler vibrometry is very accurate but expensive and limited to point-by-point sensing so it takes a long time. Finally, traditional ultrasound techniques use waves that propagate through only one location and attenuate quickly. Abbott uses guided or Lamb waves that can propagate in thin structures like aircraft skins with very little attenuation. So even with one active sensor, you can excite the wave field and detect problems over a large distance, which in turn saves time.
Editor's Pick: Quick Fixes to Aviation's Emissions Problem
Today the camera has a limited field of vision—100 mm × 100 mm—but Abbott hopes that improving technology will increase sensitivity to where the technique can inspect larger areas. “With the combination of our Lamb wave and wider-field-of-view cameras we can potentially scan the surface of the aircraft and stitch together the images that we get [for accurate, comprehensive, and fast inspection],” Abbott said.
Another improvement to work on for the future: a method that might help avoid the application of speckles. Projecting them onto the inspection surface is a good alternative that Abbott is exploring.
Future implementations might involve an inspection system with a projector, actuator, and camera mounted on a drone, traveling around an aircraft to inspect critical areas, like the fuselage, wing, or engine. “We envision the system to be fully autonomous and objective so you don’t need anyone to be trained and looking for very small damage or listening to taps on the surface,” Abbott said. “Our system will perform inspections with very little human intervention.”
Poornima Apte is an engineer and writer in Walpole, Mass.