Nanofiber Reinforces Carbon Composites
Nanofiber Reinforces Carbon Composites
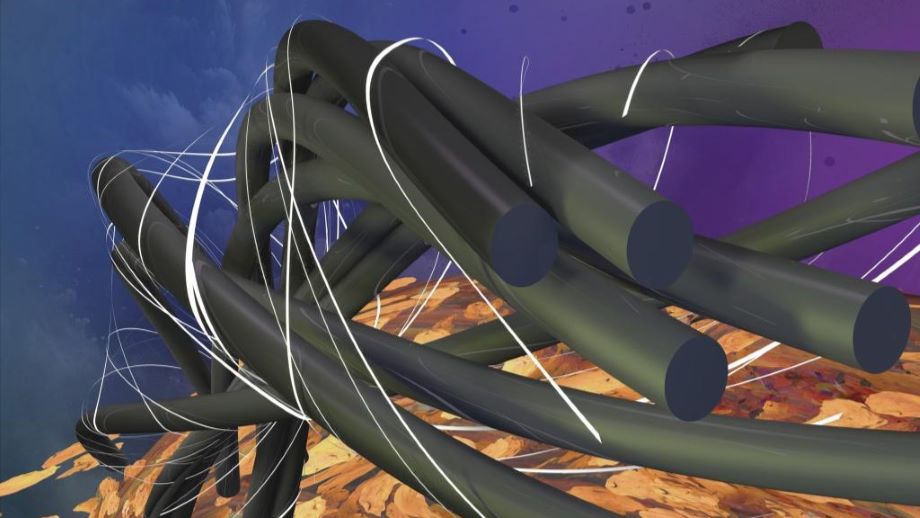
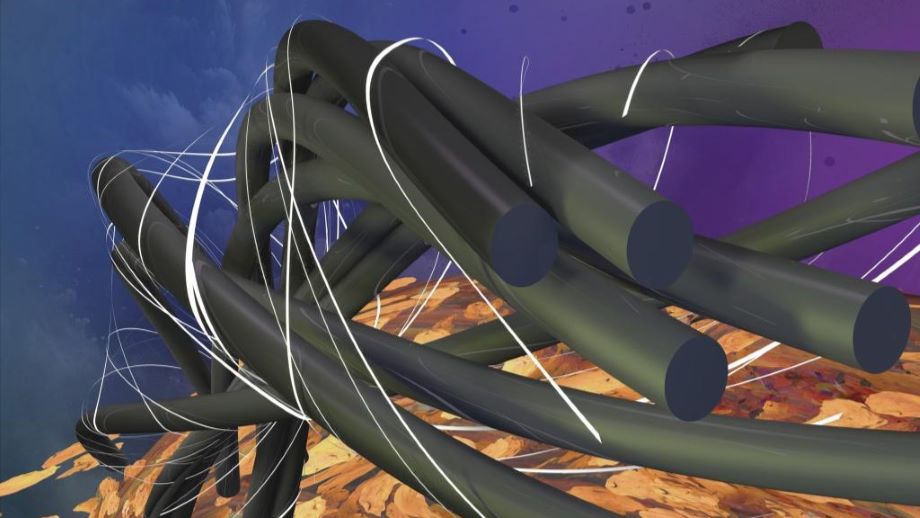
New technique bonds fibers without chemicals or heat, making it suitable for industrial applications.
Engineers make fiber-reinforced polymer composites by combining a polymer matrix with reinforcing fibers such as glass, carbon, or aramid. These composites possess high stiffness and durability and are widely used in the aerospace and automotive industries due to their high specific strength. However, the fiber-matrix interface in these composites is weak and prone to damage, which limits their overall mechanical performance.
Current methods to strengthen this interface involve growing nanomaterials on the fiber surface, chemically bonding them with the fibers, or dispersing them within the polymer matrix. Although these methods work, they are chemically intensive and challenging to scale for industrial use.
To improve on this approach, a research team at Oak Ridge National Laboratory, led by R&D associate Sumit Gupta, developed a straightforward technique to integrate chemically transformable thermoplastic nanofibers at the fiber-matrix interface. These nanofibers form covalent bonds with the matrix when heated, without the need for harsh chemicals or extreme temperatures, making this method suitable for industrial applications.
“Creating fiber-reinforced composites with both high strength and ductility poses a significant challenge due to the intrinsic trade-off between these two mechanical properties,” Gupta said. “Strength and ductility are often inversely related in materials, meaning that as one property increases, the other tends to decrease.”
This trade-off is a consequence of the mechanisms governing material behavior under stress.
High strength, typically associated with materials that resist deformation and fracture under load, is achieved by reinforcing the polymer matrix with strong fibers, such as carbon or glass, which carry a substantial portion of the applied load.
“However, these reinforcing fibers can be brittle, leading to a reduction in the composite’s overall ductility,” Gupta said. “On the other hand, ductile materials can sustain deformation without immediate failure, providing warning signs of impending failure and allowing for some degree of damage tolerance. Achieving high ductility often involves sacrificing some strength.”
Advanced Materials: Making Building Materials from Mycelium
Balancing this trade-off is crucial for optimizing the performance of fiber-reinforced composites in various applications. Previous researchers have tried, with limited success, to achieve a better compromise between strength and ductility by altering the composition of the polymer matrix, modifying the orientation and type of reinforcing fibers and incorporating hybrid materials.
Gupta and his research team developed an innovative technique using thermoplastic nanofibers to build a supportive network at the fiber-matrix interface in carbon fiber-reinforced polymer composites. When heated, these nanofiber scaffolds undergo a chemical transformation that creates a multiscale linkage between the fiber and the matrix, significantly enhancing the strength of the interface.
Nanofibers and the matrix material were carefully selected to create high-surface-area scaffolding or bridging as a load transfer pathway, a mechanism through which stress is passed between the reinforcing fibers and the surrounding matrix material. The team used polyacrylonitrile (PAN) nanofibers as the nanofiber scaffold and acrylonitrile butadiene styrene (ABS) as the polymer matrix. PAN can be spun into very fine fibers with high molecular alignment, offering unique properties for various applications. ABS is a cost-effective, strong, and durable thermoplastic that is easily molded when heated. The compatible nitrile groups in PAN and ABS can form covalent bonds when appropriately heated.
For You: Induction Welding Can Bond Composite Metal Foam
“Although we didn’t establish chemical bonding directly between the carbon fiber and the matrix molecules, we achieved a major breakthrough by chemically modifying the interphase material,” Gupta said. “This modification involved nanofiber-matrix crosslinking, creating an interphase with intermediate stiffness. The new chemical structure improved the interaction with the carbon fiber, resulting in superior interfacial properties for the composites.”
The modification led to some impressive results. “By simply altering the chemical structure at the fiber-matrix interface, the in-plane shear strength was improved by 60 percent and the toughness of the composites improved by 100 percent—without the need for complex chemical treatments,” Gupta said. “This breakthrough reveals a viable and scalable way to enhance composite materials.”
Non-Destructive Evaluation: Finding Subsurface Damage on Aircraft
Creating high-strength, lightweight materials is a top priority in the mechanical and aerospace industries. An enhanced fiber-matrix interface could significantly reduce the risk of catastrophic failure in composite materials, even under severe loading conditions. Gupta’s approach would allow mechanical and aerospace engineers to design structures using these advanced composites, thereby achieving their goal of lightweighting while maintaining safety and reliability.
This breakthrough can be applied to other fiber-reinforced composite systems, provided the nanofibers and the matrix have compatible chemical groups. This approach could also be extended to cementitious composites where steel is used as the primary reinforcement.
“By introducing a co-continuous interphase between the cement matrix and the steel reinforcement, we aim to create a tougher interphase, leading to high-performance cementitious composite applications,” Gupta said.
Mark Crawford is a technology writer in Corrales, N.M.
Current methods to strengthen this interface involve growing nanomaterials on the fiber surface, chemically bonding them with the fibers, or dispersing them within the polymer matrix. Although these methods work, they are chemically intensive and challenging to scale for industrial use.
To improve on this approach, a research team at Oak Ridge National Laboratory, led by R&D associate Sumit Gupta, developed a straightforward technique to integrate chemically transformable thermoplastic nanofibers at the fiber-matrix interface. These nanofibers form covalent bonds with the matrix when heated, without the need for harsh chemicals or extreme temperatures, making this method suitable for industrial applications.
“Creating fiber-reinforced composites with both high strength and ductility poses a significant challenge due to the intrinsic trade-off between these two mechanical properties,” Gupta said. “Strength and ductility are often inversely related in materials, meaning that as one property increases, the other tends to decrease.”
This trade-off is a consequence of the mechanisms governing material behavior under stress.
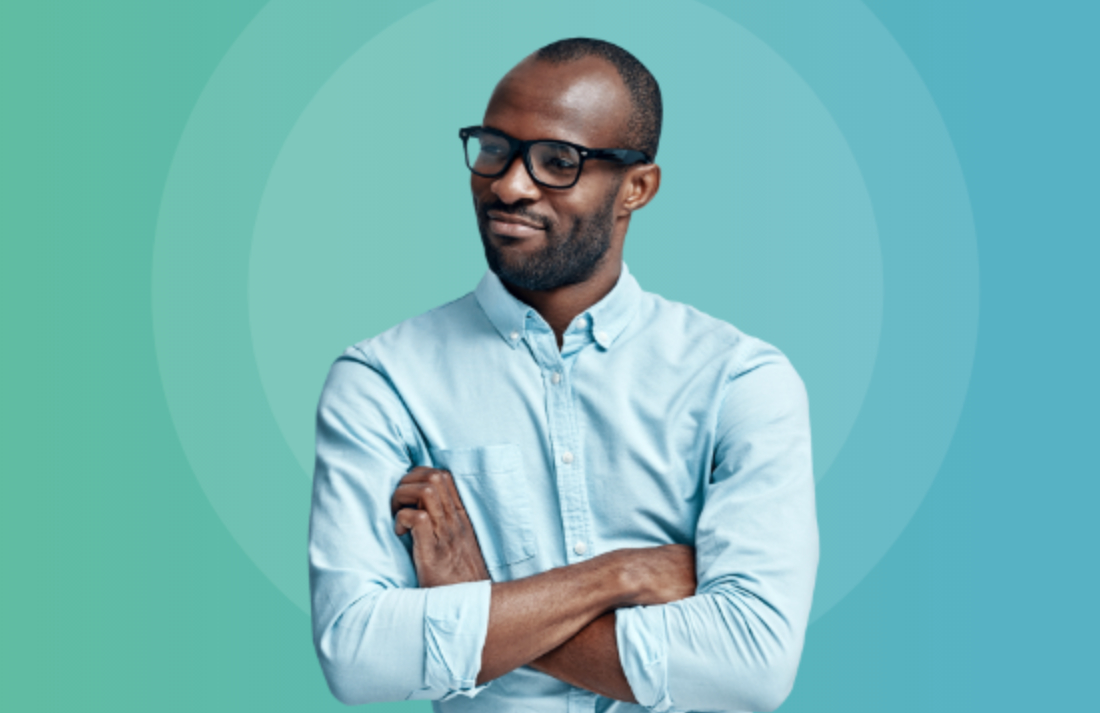
It's Time to Renew
Some benefits of ASME membership can be enjoyed for only a limited time, so don't wait to renew.
“However, these reinforcing fibers can be brittle, leading to a reduction in the composite’s overall ductility,” Gupta said. “On the other hand, ductile materials can sustain deformation without immediate failure, providing warning signs of impending failure and allowing for some degree of damage tolerance. Achieving high ductility often involves sacrificing some strength.”
Advanced Materials: Making Building Materials from Mycelium
Balancing this trade-off is crucial for optimizing the performance of fiber-reinforced composites in various applications. Previous researchers have tried, with limited success, to achieve a better compromise between strength and ductility by altering the composition of the polymer matrix, modifying the orientation and type of reinforcing fibers and incorporating hybrid materials.
Gupta and his research team developed an innovative technique using thermoplastic nanofibers to build a supportive network at the fiber-matrix interface in carbon fiber-reinforced polymer composites. When heated, these nanofiber scaffolds undergo a chemical transformation that creates a multiscale linkage between the fiber and the matrix, significantly enhancing the strength of the interface.
Nanofibers and the matrix material were carefully selected to create high-surface-area scaffolding or bridging as a load transfer pathway, a mechanism through which stress is passed between the reinforcing fibers and the surrounding matrix material. The team used polyacrylonitrile (PAN) nanofibers as the nanofiber scaffold and acrylonitrile butadiene styrene (ABS) as the polymer matrix. PAN can be spun into very fine fibers with high molecular alignment, offering unique properties for various applications. ABS is a cost-effective, strong, and durable thermoplastic that is easily molded when heated. The compatible nitrile groups in PAN and ABS can form covalent bonds when appropriately heated.
For You: Induction Welding Can Bond Composite Metal Foam
“Although we didn’t establish chemical bonding directly between the carbon fiber and the matrix molecules, we achieved a major breakthrough by chemically modifying the interphase material,” Gupta said. “This modification involved nanofiber-matrix crosslinking, creating an interphase with intermediate stiffness. The new chemical structure improved the interaction with the carbon fiber, resulting in superior interfacial properties for the composites.”
The modification led to some impressive results. “By simply altering the chemical structure at the fiber-matrix interface, the in-plane shear strength was improved by 60 percent and the toughness of the composites improved by 100 percent—without the need for complex chemical treatments,” Gupta said. “This breakthrough reveals a viable and scalable way to enhance composite materials.”
Non-Destructive Evaluation: Finding Subsurface Damage on Aircraft
Creating high-strength, lightweight materials is a top priority in the mechanical and aerospace industries. An enhanced fiber-matrix interface could significantly reduce the risk of catastrophic failure in composite materials, even under severe loading conditions. Gupta’s approach would allow mechanical and aerospace engineers to design structures using these advanced composites, thereby achieving their goal of lightweighting while maintaining safety and reliability.
This breakthrough can be applied to other fiber-reinforced composite systems, provided the nanofibers and the matrix have compatible chemical groups. This approach could also be extended to cementitious composites where steel is used as the primary reinforcement.
“By introducing a co-continuous interphase between the cement matrix and the steel reinforcement, we aim to create a tougher interphase, leading to high-performance cementitious composite applications,” Gupta said.
Mark Crawford is a technology writer in Corrales, N.M.