New Approach Cuts Manufacturing Time for 3D Parts
New Approach Cuts Manufacturing Time for 3D Parts
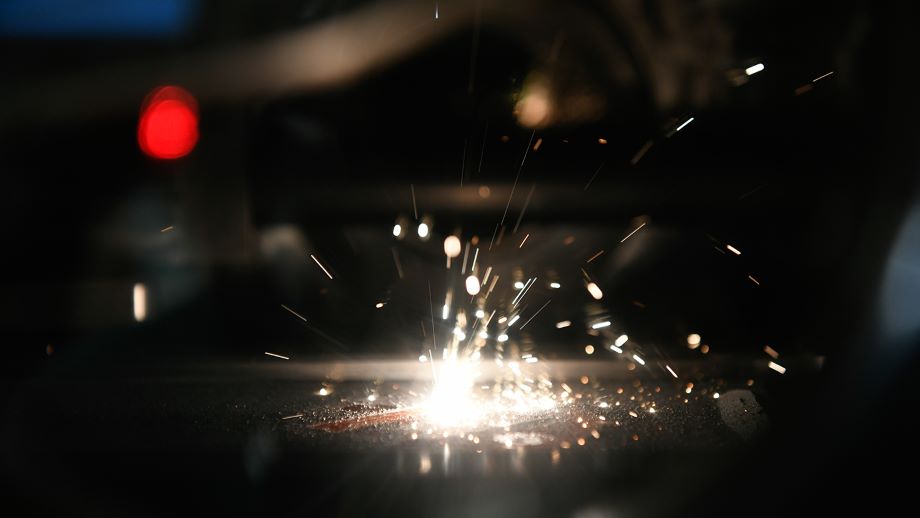
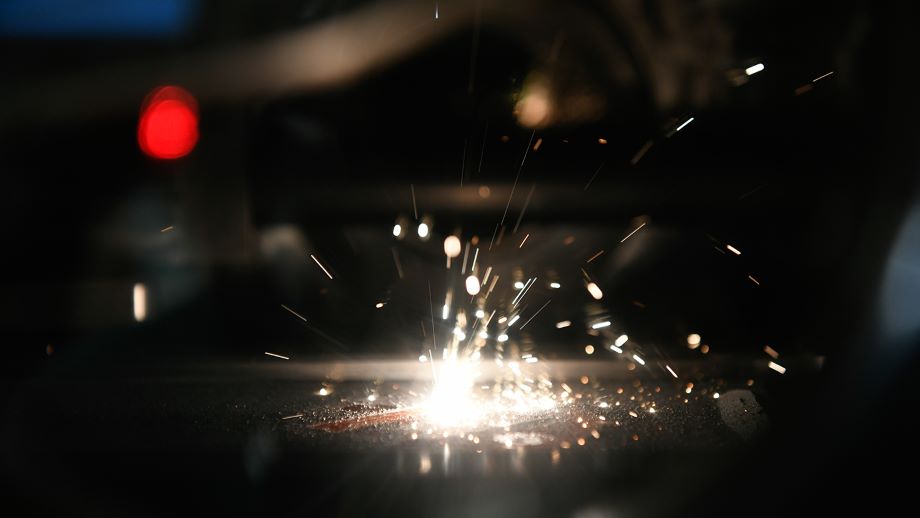
Researchers at North Carolina State University have developed a process that speeds up the additive manufacturing of metal machine parts by 33 percent.
Speed is high on the wish list of every manufacturer. They are interested in any process improvement that makes production faster, without sacrificing quality. One reason additive manufacturing (AM) technologies are so popular is that they allow companies to quickly replace critical machine components that are needed within the manufacturing plant, without having to endure costly supply chain delays.
Most AM-printed metal machine parts require detailed measurements to ensure they meet critical tolerances. This involves taking the part out of the manufacturing equipment, measuring it, and then putting it back into the equipment to make any needed adjustments. To ensure accuracy, the process is often repeated multiple times, which slows down production.
Looking to grant manufacturers their wishes, researchers at North Carolina State University in Raleigh have developed a process that speeds up the additive manufacturing of metal machine parts by 33 percent.
Have You Renewed Your ASME Membership?
The idea got rolling when Christopher Kelly, an engineering student, approached assistant research professor Brandon McConnell for help regarding the mathematical details of how to quickly take on-machine measurements to determine whether a part is in-tolerance or not.
“Once we understood the technical challenge for this automatic on-line inspection, we realized we didn’t need to code up some fancy math and instead could use a simple ‘walk the dog’ approach to arrive at the same answer,” McConnell said. “This simplified the project for Chris, who was balancing the data collection and math development components of the research with the manufacturing aspects of the project.”
At first, they focused their research efforts on geometric models and specifications using ISO tolerance standards, but this proved to be too broad for a small research project. Instead, they decided to look at a few basic geometric shapes that typically define the functionality of a product, such as holes, slots, and pockets. The idea was to integrate 3D printing, automated machining, laser scanning (for part location on a CNC machine), and touch-probe measurement technologies with related software to create a largely automated system that produces metal machine components. A key objective for this system was being able to conduct in-line quality inspection of the parts during the finishing process, without having to remove the parts from the manufacturing equipment for measurement, thereby saving considerable time.
The laser scans the part to establish basic shape and location on the CNC machine. A software program then uses these geometric features and locations, coupled with the desired critical tolerances to qualify the part’s accuracy, to make sure that the part’s dimensions are within the required specifications.
More Advanced Manufacturing: Porous Structures Give Metamaterial Key Properties
To test their new system, the team manufactured several parts using powder-metal 3D printing systems to produce near net-shape parts. These parts were then fixtured onto five-axis CNC machines where the machining and inspection instructions were automatically generated and executed.
“We were able to finish one of the test parts in 200 minutes using the automatic system and then inspecting the parts manually,” McConnell said. “We were able to inspect and finish the same part in 133 minutes using our new on-machine inspection technique. Time is money in most professional settings. Depending on the situation, saving 67 minutes could be incredibly important.”
Kelly and McConnell, along with NCSU engineers Richard A. Wysk, Ola A. Harrysson, and Russell E. King, published their results in the May 2024 issue of the International Journal of Manufacturing Technology and Management.
“Even though we reduced the scope of the research to what seemed to be easy geometric features to inspect, the interpretation and scope of things like maximum material specifications, datum relationships, and creating an inspection plan were not trivial issues to be resolved,” Wysk said.
For You: Better Flaw Detection During Powder Bed Fusion
This initial work focused on printing and finish machining parts that include holes and/or cylinders, such as pistons. However, the approach could be adapted for machine parts with other features.
“All of the hardware we used in this technique is commercially available, so we feel that this new approach could be adopted and put into use almost immediately,” McConnell said.
McConnell is open to working with partners who are interested in making use of this technique in their own operations. “The ideas are simple, but the impact is significant,” he said. “As we think about automation and leveraging additive manufacturing in commercial ventures, the reduction of one hour of production time per part demonstrates we have a ways to go before these technologies are fully integrated in the most efficient/effective manner. More research is needed to help companies realize the full potential of these methods.”
Mark Crawford is a technology writer in Corrales, N.M.
Most AM-printed metal machine parts require detailed measurements to ensure they meet critical tolerances. This involves taking the part out of the manufacturing equipment, measuring it, and then putting it back into the equipment to make any needed adjustments. To ensure accuracy, the process is often repeated multiple times, which slows down production.
Looking to grant manufacturers their wishes, researchers at North Carolina State University in Raleigh have developed a process that speeds up the additive manufacturing of metal machine parts by 33 percent.
Have You Renewed Your ASME Membership?
The idea got rolling when Christopher Kelly, an engineering student, approached assistant research professor Brandon McConnell for help regarding the mathematical details of how to quickly take on-machine measurements to determine whether a part is in-tolerance or not.
“Once we understood the technical challenge for this automatic on-line inspection, we realized we didn’t need to code up some fancy math and instead could use a simple ‘walk the dog’ approach to arrive at the same answer,” McConnell said. “This simplified the project for Chris, who was balancing the data collection and math development components of the research with the manufacturing aspects of the project.”
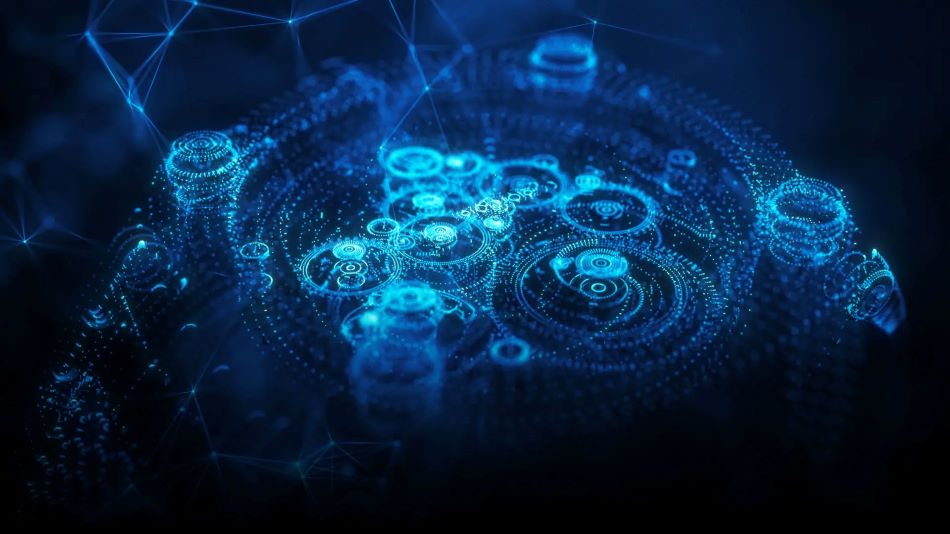
Engineering Research Highlights
R&D Pulse puts the spotlight on the best of ASME's journals.
The laser scans the part to establish basic shape and location on the CNC machine. A software program then uses these geometric features and locations, coupled with the desired critical tolerances to qualify the part’s accuracy, to make sure that the part’s dimensions are within the required specifications.
More Advanced Manufacturing: Porous Structures Give Metamaterial Key Properties
To test their new system, the team manufactured several parts using powder-metal 3D printing systems to produce near net-shape parts. These parts were then fixtured onto five-axis CNC machines where the machining and inspection instructions were automatically generated and executed.
“We were able to finish one of the test parts in 200 minutes using the automatic system and then inspecting the parts manually,” McConnell said. “We were able to inspect and finish the same part in 133 minutes using our new on-machine inspection technique. Time is money in most professional settings. Depending on the situation, saving 67 minutes could be incredibly important.”
Kelly and McConnell, along with NCSU engineers Richard A. Wysk, Ola A. Harrysson, and Russell E. King, published their results in the May 2024 issue of the International Journal of Manufacturing Technology and Management.
“Even though we reduced the scope of the research to what seemed to be easy geometric features to inspect, the interpretation and scope of things like maximum material specifications, datum relationships, and creating an inspection plan were not trivial issues to be resolved,” Wysk said.
For You: Better Flaw Detection During Powder Bed Fusion
This initial work focused on printing and finish machining parts that include holes and/or cylinders, such as pistons. However, the approach could be adapted for machine parts with other features.
“All of the hardware we used in this technique is commercially available, so we feel that this new approach could be adopted and put into use almost immediately,” McConnell said.
McConnell is open to working with partners who are interested in making use of this technique in their own operations. “The ideas are simple, but the impact is significant,” he said. “As we think about automation and leveraging additive manufacturing in commercial ventures, the reduction of one hour of production time per part demonstrates we have a ways to go before these technologies are fully integrated in the most efficient/effective manner. More research is needed to help companies realize the full potential of these methods.”
Mark Crawford is a technology writer in Corrales, N.M.
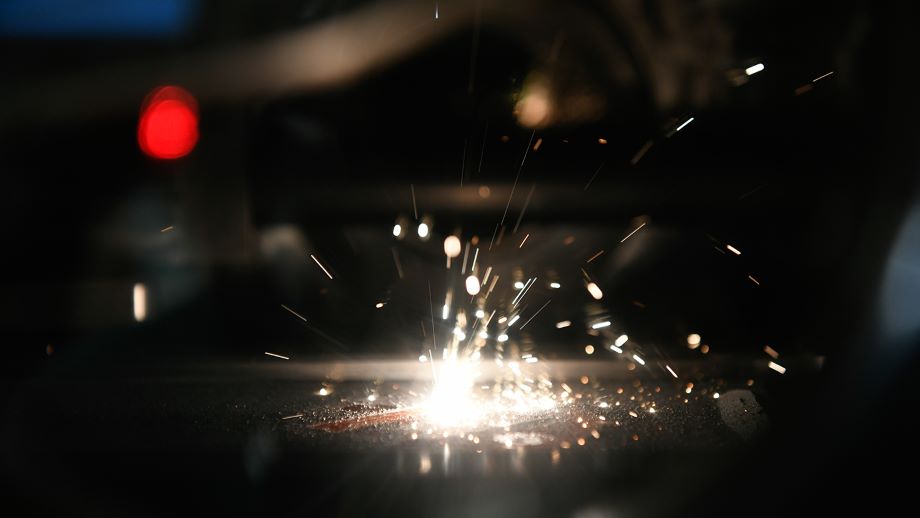
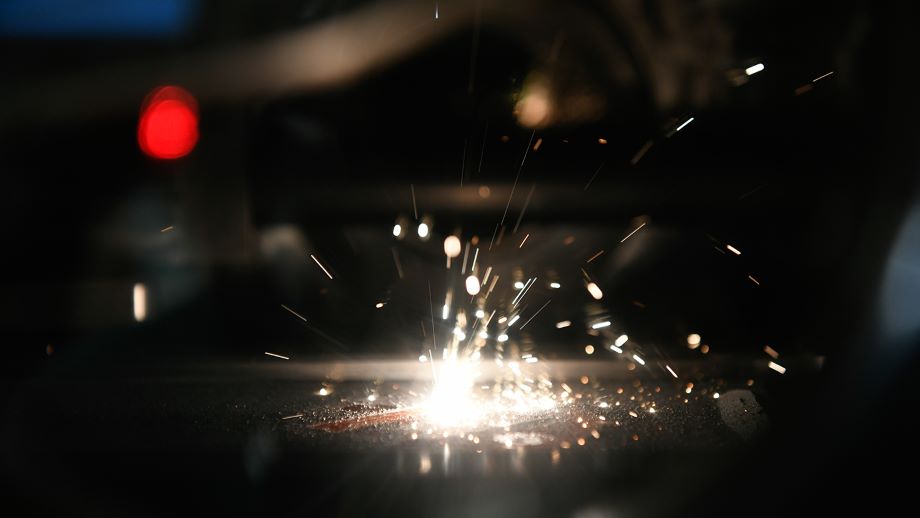