The Prototyping Technology that Disrupted the World
The Prototyping Technology that Disrupted the World
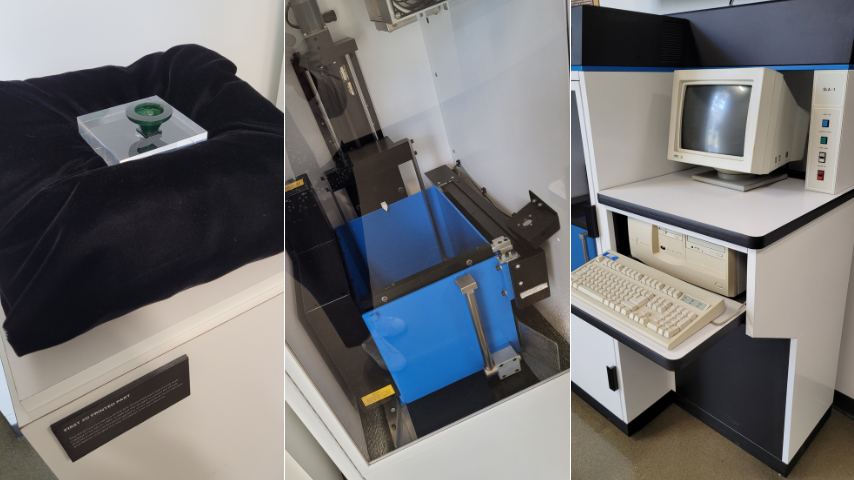
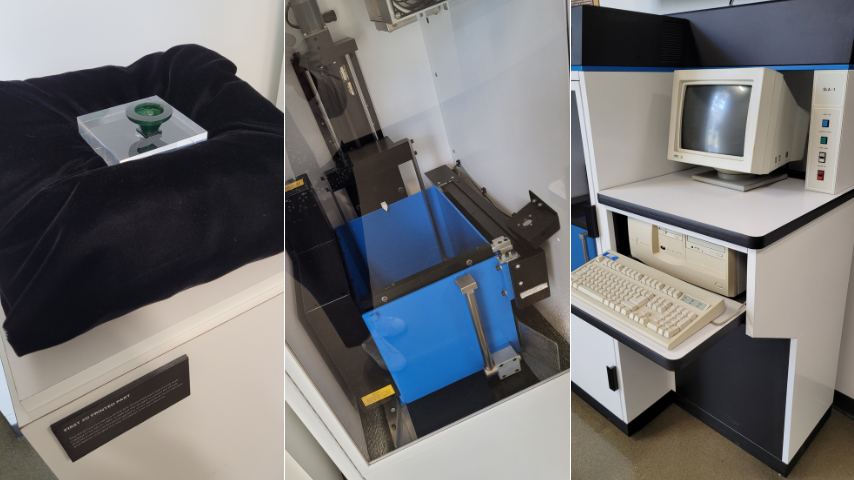
Chuck Hull’s stereolithography apparatus produced its first 3D-printed part in 1983. Adoption of advanced hardware, software, and materials has allowed innovation to continue for four decades.
The machine that transformed prototyping for manufacturing and then proceeded to change how the world designs, formulates, and “prints” production parts, sits unobtrusively in the lobby of a nondescript manufacturing building in Rock Hill, S.C. Yet, the device, SLA-1, taking up a small 10 by 12 foot spot against the wall in the headquarters of 3D Systems, has transformed multiple industries across numerous countries.
“The original idea was to prototype plastic parts,” explained Charles “Chuck” Hull, co-founder and chief technology officer of 3D Systems. “So, if you're designing a part, you want to see what it looks like, use it, and test it.” The inventor of stereolithography (SLA) described the innovative technology as a godsend that took the tedious process of tooling and offered a way to produce a prototype quickly.
Designated in 2016, SLA is an ASME Landmark. The machine includes a container filled with photopolymer, a UV light source, scanning mirrors, a movable elevator platform, and a computer to design the 3D object and translate the design into commands. SLA-1 sits below its ASME bronze plague and reminds those who visit how 3D printing began—with the 3D printer becoming available for commercial sale and use in 1988.
Hull—a named inventor on more than 85 U.S. patents in the field of optics and 3D printing—co-founded 3D Systems in 1986 to market his new invention that used a process that sounds straightforward now. But when he introduced stereolithography, the method of curing layers of photopolymers with ultraviolet rays to form solid objects, was almost unimaginable.
“There’s been a jillion applications developed using 3D printing,” Hull explained. An early one was casting patterns for investment casting. This has been “very successful” and one that is still a major application, he said. Today, rapid prototyping has become a leading technology for manufacturing new products and parts, explained Marty Johnson, vice president, product and technical fellow, of 3D Systems. Multiple offerings have influenced the medical, automotive, and aerospace industries among many others, he said.
Inducted into the National Inventors Hall of Fame in 2014, Hull stressed that what led to the invention of stereolithography was the challenge of the significant time it took to go from a design to a finished product—about six weeks. And if there were any problems found along the way, you had to start again. He noted that when he first saw UV-curable coatings he wondered if there was a way to “do some kind of imaging” and manipulate the coatings to prototype plastic parts.
Indeed, while subtractive manufacturing—traditional methods—that remove materials to reveal a finished part include such techniques as drilling, cutting, and milling, additive manufacturing builds objects layer upon layer from a digital 3D model, Johnson explained. Now the machine that started it all sits among new, precise 3D printers and the products that have been produced using the technology, such as engine part prototypes, flight-ready aerospace parts, running shoes, eyewear, hearing aids, and dental aligners.
Hull, who holds a bachelor’s degree in engineering physics, admitted that while he envisioned that 3D printing would be embraced by manufacturing, he could not have imagined what “customers” would do with the technology. Beyond obvious manufactured parts, healthcare is only one category that has become personalized with precision parts helping people live longer—everything from custom implants to prosthetics.
While the variety of products that can be 3D printed seems endless, there have been challenges to the adoption of 3D printing technology. “With every new technology there are stumbling blocks,” Hull conceded. But the free adoption of something new may have been the biggest challenge. There are always detractors, he said. But there are always “forward looking” individuals as well who step up to try “and this is the promise.”
Hull offered a simple example of hearing aids. When 3D Systems first worked with this application, years ago, hearing aids were all hand crafted. Then they designed the application using CAD, kept the data, and the process got much easier. “But it was probably five years or more before it was generally accepted,” he said. Now all hearing aid shells are made this way. This period of “adjustment” is also true of dental applications, like aligners, as well. Invisalign was the idea dreamed up by two Stanford graduate students who reached out to 3D Systems and “It took a long time before it was an accepted product,” Hull said.
What has amazed Hull the most throughout the years is the medical applications that 3D printing has made possible. “It was really a surprise to me,” he said.
“A very pleasant surprise. I mean, there's just been miraculous cures for various conditions that have come about because of this that I had not anticipated.”
More recently, Hull has been mainly working in bioprinting and regenerative medicine applications. And he finds different business models and the work they do remarkable. “Entrepreneurship may be his biggest journey,” he explained. “Learning how to grow a startup business is a real accomplishment.”
Cathy Cecere is membership content program manager.
“The original idea was to prototype plastic parts,” explained Charles “Chuck” Hull, co-founder and chief technology officer of 3D Systems. “So, if you're designing a part, you want to see what it looks like, use it, and test it.” The inventor of stereolithography (SLA) described the innovative technology as a godsend that took the tedious process of tooling and offered a way to produce a prototype quickly.
Designated in 2016, SLA is an ASME Landmark. The machine includes a container filled with photopolymer, a UV light source, scanning mirrors, a movable elevator platform, and a computer to design the 3D object and translate the design into commands. SLA-1 sits below its ASME bronze plague and reminds those who visit how 3D printing began—with the 3D printer becoming available for commercial sale and use in 1988.
Multiple applications
Hull—a named inventor on more than 85 U.S. patents in the field of optics and 3D printing—co-founded 3D Systems in 1986 to market his new invention that used a process that sounds straightforward now. But when he introduced stereolithography, the method of curing layers of photopolymers with ultraviolet rays to form solid objects, was almost unimaginable.
“There’s been a jillion applications developed using 3D printing,” Hull explained. An early one was casting patterns for investment casting. This has been “very successful” and one that is still a major application, he said. Today, rapid prototyping has become a leading technology for manufacturing new products and parts, explained Marty Johnson, vice president, product and technical fellow, of 3D Systems. Multiple offerings have influenced the medical, automotive, and aerospace industries among many others, he said.
Inducted into the National Inventors Hall of Fame in 2014, Hull stressed that what led to the invention of stereolithography was the challenge of the significant time it took to go from a design to a finished product—about six weeks. And if there were any problems found along the way, you had to start again. He noted that when he first saw UV-curable coatings he wondered if there was a way to “do some kind of imaging” and manipulate the coatings to prototype plastic parts.
Indeed, while subtractive manufacturing—traditional methods—that remove materials to reveal a finished part include such techniques as drilling, cutting, and milling, additive manufacturing builds objects layer upon layer from a digital 3D model, Johnson explained. Now the machine that started it all sits among new, precise 3D printers and the products that have been produced using the technology, such as engine part prototypes, flight-ready aerospace parts, running shoes, eyewear, hearing aids, and dental aligners.
Hull, who holds a bachelor’s degree in engineering physics, admitted that while he envisioned that 3D printing would be embraced by manufacturing, he could not have imagined what “customers” would do with the technology. Beyond obvious manufactured parts, healthcare is only one category that has become personalized with precision parts helping people live longer—everything from custom implants to prosthetics.
What’s next?
While the variety of products that can be 3D printed seems endless, there have been challenges to the adoption of 3D printing technology. “With every new technology there are stumbling blocks,” Hull conceded. But the free adoption of something new may have been the biggest challenge. There are always detractors, he said. But there are always “forward looking” individuals as well who step up to try “and this is the promise.”
Hull offered a simple example of hearing aids. When 3D Systems first worked with this application, years ago, hearing aids were all hand crafted. Then they designed the application using CAD, kept the data, and the process got much easier. “But it was probably five years or more before it was generally accepted,” he said. Now all hearing aid shells are made this way. This period of “adjustment” is also true of dental applications, like aligners, as well. Invisalign was the idea dreamed up by two Stanford graduate students who reached out to 3D Systems and “It took a long time before it was an accepted product,” Hull said.
What has amazed Hull the most throughout the years is the medical applications that 3D printing has made possible. “It was really a surprise to me,” he said.
“A very pleasant surprise. I mean, there's just been miraculous cures for various conditions that have come about because of this that I had not anticipated.”
More recently, Hull has been mainly working in bioprinting and regenerative medicine applications. And he finds different business models and the work they do remarkable. “Entrepreneurship may be his biggest journey,” he explained. “Learning how to grow a startup business is a real accomplishment.”
Cathy Cecere is membership content program manager.